3D Printed Buildings and Technology S-Curves

Developments in the construction industry tend to stay below most folks’ radar. Despite being responsible for the entire built environment (as well as a huge fraction of GDP), it’s rare for news in the sector to spread beyond industry trade publications [0]. Even giant, well-funded startups tend to shoot below replacement in terms of press coverage and general interest if they’re in the construction world.
3D printed buildings are an exception to this. The idea of “printing” a building is fascinating to folks, perhaps because 3D printers still feel like futuristic technology (and are easy to project a lot of inflated expectations on). Almost any 3D printed building effort is guaranteed a lot of press, to the point where stories about 3D printed buildings vastly exceed the number of 3D printed buildings themselves:
This enthusiasm has percolated throughout the entire technology development ecosystem. Everyone from investors, to startup founders, to researchers, to governments thinks that 3D printed buildings might be the future. Eric Schmidt described it as an important ‘moonshot’ initiative (though it doesn’t appear that Alphabet is developing the technology). Dubai plans for 25% of its buildings to be 3D printed by 2030, as part of a bid to be a world hub of 3D printing expertise. NASA, the DoD, and Oakridge National Lab are all investigating the technology. And while it’s normally rare for anyone to fund developments of new building systems outside of universities, there are dozens of commercial efforts to develop 3D printed building technology. This is despite the fact that there are perhaps a few hundred 3D printed buildings in the world, and few enough people living in them that you still regularly get “first resident of a 3D printed home” stories.
All this suggests the technology is rapidly ascending the peak of the technology hype cycle. Given the amount of attention the sector receives, I thought it’d be useful to take a look under the good, and get a sense of its capabilities.
3D Printing Overview
3D printing (aka additive manufacturing) is a manufacturing method that involves building an object by laying down thin layers of material one on top of the other. By precisely controlling where material is placed, a 3D printer can produce objects of any shape and configuration, the same way a normal printer can produce any sort of 2D image. This flexibility makes them extremely useful for creating custom, one-off items where setting up a conventional fabrication process would be too expensive or time consuming.
Abstractly, this makes 3D printing seem like the perfect technology for producing buildings. One of the main criticisms of the conventional construction process is that everything is one off and custom, and that its inefficiency stems from its lack of repeatability or economies of scale. It’s often assumed (implicitly or explicitly) that changing the industry will require introducing more repetitive designs. 3D printing seems like it offers a potential way out - just like a normal printer isn’t slowed down by the complexity of the document it's printing, a building 3D printer could quickly and easily fabricate buildings of any size or shape, allowing for true mass customization.
And because 3D printing can precisely control where material is placed, it allows for more efficient, optimized structures that only have material where it’s needed, and that would be impossible to achieve with a conventional construction process. A typical steel beam, for instance, has the exact same section profile along its entire length, due to production constraints and being an off the shelf product that needs to accommodate a wide variety of potential uses. This results in a lot of “extra” material - the web usually is thicker than it needs to be at the center of the beam, and the flanges are bigger than the need to be at the ends.
A 3D printed beam, on the other hand, could omit all the extra material, without any adjustments to the production process. Placing material only where it’s required also means that 3D printed buildings wouldn’t have the waste resulting from cutting materials down to the size needed that conventional construction has. The result is that a 3D printed building would use much less material than a conventionally built one.
3D printing also allows you to connect your fabrication system directly to your design software, cutting out the manual process of translation that slows down conventional construction.
That’s the theory, anyway. In practice, the field is in its infancy, and getting even a simple wall printed is a huge technical challenge. Because the technology is so new, and can’t be straightforwardly adapted from “traditional” 3D printing [1], we actually see a lot of variation in how the technology is implemented, as folks try to figure out what works and what doesn’t. It’s not unlike the late 1800s, when it wasn’t quite clear what it took to make a heavier-than-air flying machine. So it’s interesting to take a high level look at the territory different players are exploring.
Printing Material
One of the trickiest parts of 3D printing is getting the material right. Placing a series of thin layers one on top of the other requires a material that is flowable enough to be placed where it needs to be, but can still hold it’s shape once it’s been placed.
Traditional 3D printers accomplish this in a variety of ways. Some systems, like FFF/FDM, extrude material (usually some type of plastic) through a heated nozzle that is then quickly cooled. Others, like stereolithography (SLA), use lasers to rapidly cure thin layers of liquid resin.
The majority of building 3D printers today use a special concrete mix as their material. Companies like COBOD, Icon, Winsun, and Apis-Cor all use some type of concrete in their printers, though they often use it in different ways. Most are using it to print entire structures on-site. Others, like WinSun, print concrete formwork that is then infilled with a traditional poured concrete mix. And some, like Bruil, print concrete components that are then shipped to the jobsite and installed.
Unlike traditional 3D printing, which usually hardens its material as soon as it's printed, 3D printed concrete stays soft after it's been printed (though it hardens much faster than conventional concrete). To accommodate this, it uses mixes that are carefully formulated to have just the right viscosity. Too little, and the concrete won’t flow through the print head. Too much, and it won’t maintain its shape once it’s been laid down, and as increasing load is placed on it as more layers get added.
Concrete seems like natural material for a building printer - it’s a strong, low cost, flowable material, whose raw components are trivial to obtain, and that building codes and code officials already understand. But it has some drawbacks.
For one, freshly placed concrete has limited ability to support itself, meaning it generally needs to be placed on top of a solid surface. Conventional 3D printers usually have some ability to print overhangs and bridges, but currently most concrete 3D printing is limited to purely vertical elements (though you’ll also sometimes see structures that are printed horizontally and then tilted on their side, to get a 3D printed roof). Openings such as doors and windows are usually handled by someone manually placing premade lintels at the top of the opening. This problem is being worked on by folks like Apis Cor and Twente, and progress is being made.

Another drawback is the design of the mix itself. 3D printable mixes differ from traditional concrete in that they have no large aggregate, only sand (making them more like grout than concrete). They also have very large fractions of cement or cementitious materials - they seem to hover around a ratio of 1:2 between cement and aggregate, compared to a 1:7 ratio for more traditional concrete. Since cement is by far the most expensive material in concrete, 3D printable mixes are much more costly than traditional ones, as well as more carbon intensive (though a 3D printed concrete element will likely use less material than a traditional built one). They’re also much more sensitive to mixing conditions - a slight variance in slump or spread that would be acceptable in a traditional concrete application might mean that your wall collapses under its own weight in a 3D printed mix.

The timing of the layer placement is also critical with 3D printed concrete. Concrete placed at different times will form what’s known as “cold joints” - planes of weakness between layers of concrete that haven’t properly bonded to each other. Preventing cold joints limits how much time can pass between layers being set, and thus places an upper bound on how big a structure a single printer can print at one time. The potential for cold joints, combined with 3D printed mixes’ rapid cure time, also makes concrete 3D printing much more sensitive to any sort of interruption in the placing process.
Another issue is reinforcement. Conventional concrete is almost always reinforced with steel to give it tensile strength, and to prevent sudden, brittle failures. Adding reinforcing is a challenge for 3D printed concrete - you can’t fit rebar through a print head. Current solutions mostly seem to be either a) leave the concrete unreinforced, or b) have someone place reinforcing manually as the wall is printed, neither of which is especially compelling. More speculative ideas are to include steel fibers in the concrete mix (which creates difficulties with pumping the concrete through the print head, and doesn’t have the same performance as steel reinforcing), replace the manual rebar placement with robotic placement (apparently Hyperion is working on this), or have some extruder that can feed wire alongside the concrete print head (limited to horizontal reinforcing placement).
But the biggest issue is that using concrete as a material limits you to printing just the structure itself - it doesn’t give a way to print the wiring, plumbing, finishes, or anything else in the remaining 80% of the building.
Concrete printers seem to make up about 75% of 3D printing developments, but a few folks are working with different materials. MX3D uses “wire arc additive manufacturing” to print structures out of steel, essentially by extruding wire through an off-the-shelf welding machine attached to a robot arm (one can imagine combining this technique with a concrete printer, to print rebar cages inside the concrete as it takes shape). WASP is focused on 3D printing buildings using local materials, and uses a mix of clay, sand, and straw. Batiprint actually prints in foam, creating a void that is then filled with traditional concrete (sort of a 3D printed ICF).
But the most interesting of the bunch might be Mighty Buildings. They use a proprietary material known as “light stone material” (LSM), which according to patent filings is some sort of polymer. LSM is lighter and less thermally conductive than concrete, and is water and fire resistant. Instead of simply waiting for the material to harden like with concrete, LSM is cured as it prints, using a UV light attached to the print head. This gives it a much greater ability to overhang/support itself than printed concrete does - their ADU product includes an overhanging curved wall, and at least some videos show them printing unsupported horizontal spans (though others show them using supports).
Mighty Buildings also seems capable of printing at a higher resolution/thinner layer than concrete-based printers (which seems to always yield thick, noticeable layers), though it’s still rough enough that they grind it down as part of the finishing process.
The drawback with a material like LSM is likely cost, and the sensitivity of the production environment. Unlike concrete printers, which mostly print their product on-site, Mighty Buildings prints panels and modules in a controlled factory environment, and then ships them to the jobsite.
On-site vs In-factory
3D building printing efforts also need to decide where to do their actual printing. They can bring the printer to the jobsite, and print the building where it will stand. Or they can do the printing in a controlled, factory environment, and then ship the finished components to the jobsite
Printing on-site eliminates the logistics problem of shipping large finished components, and enables you to print structures larger than could be physically shipped. It also means you don’t have to design your buildings to survive being shipped, which is often the controlling load case in off-site construction. But setting up a printer on-site in some ways simply shifts where the logistics problems occur - instead of your building being collapsable and transportable, now your printer needs to be. And printing in an exposed jobsite environment rules out any sort of process that might be sensitive to environmental conditions, and makes it more difficult to achieve a high level of quality. In practice, it seems like even on-site printing efforts often take place under a tent or other protective structure to shield the freshly printed material.
Printing off-site has the same advantages as any sort of off-site production: it gives you a controlled environment to produce in, it gives you total control over the production process, and it makes it easy to produce at a higher volume (your printer can spit out buildings 24/7 instead of spending half its life being moved to and from jobsites).
The drawbacks for off-site printing are the same as conventional off-site construction, and are old hat at this point - the larger your components, the greater your transportation costs, and the smaller the market you can deliver to cost effectively.
Most concrete printers, such as Icon and Winsun, seem to opt for on-site printing, though Bruil seems to use both on and off-site. Batiprint also opts for on-site printing. Mighty Buildings’ process, on the other hand, seems to require a controlled factory environment - on their roadmap they talk about eventually having a network of local factories, but make no mention of on-site printing. MX3D also seems to do factory-based printing.
I think it’ll be particularly interesting to see how this trend will play out. The drawbacks of factory production are substantial, but abstractly it seems like it would be easier to implement a complex, multimaterial print in a controlled factory environment than on a jobsite. If the technology improves enough to where a substantial fraction of a building can be printed, and the costs drop enough, it could still have the potential to significantly reduce construction costs even with the added burden of shipping them from the factory.
On the other hand, while industrial and high-end conventional 3D printers usually print in an enclosed environment, open-air 3D printers are increasingly able to produce high quality prints. It may turn out that on-site printing is able to achieve a sufficient level of quality that the benefits of factory production don’t outweigh the costs.
Print Head Movement
Another axis of variance for building 3D printers is how they move their print head.
Conventional 3D printers mostly seem to use a gantry system (though some technologies, such as SLA, don’t require a moving print head at all), with the print head moving back and forth along a supporting beam, which in turn moves in the other axis on a pair of support rails.
Most building 3D printers seem to use a gantry system as well. In particular, the systems that have moved beyond the experimental stage and are in use for actual production seem to favor it:
ICON, the first 3D printed homes for sale in the US
COBOD, manufacturer of 3D concrete printers
WinSun, Chinese concrete 3D printing company
A gantry system can be implemented in a couple different ways - you can have an overhead gantry, with elevated rails that a boom then moves along. Or you can have a pair of rails mounted to the ground. Elevated rails require a larger support structure, but ground mounted rails require more extensive ground preparation to get a level rail surface. Construction 3D printers that use gantry systems seem roughly 50/50 split between them.
A gantry system is popular for a reason. It’s relatively inexpensive, it’s simple to implement, it’s fast and accurate. An elevated rail gantry also gives an easy way to provide a semi-protected environment to the print area (just hang some canvas from your gantry supports). But it has some weaknesses. It needs to be assembled before it can be used, which is burdensome for a printer that will constantly be changing location. For a large printer, this might mean pouring special foundation, or tying it down with large concrete dunnage blocks.
The building also needs to fit within the gantry extents - the taller or wider the building, the heavier your gantry framing has to be, and the more difficult this becomes. Icon’s current 3D printer is limited to printing 1 story buildings no more than 33’ wide.
A close cousin to the gantry printers are the center-pivot printers. These printers have a print head that runs along a centrally mounted, rotatable boom (essentially 2-axis movement operating in polar instead of cartesian coordinates). Apis-Cor, and at least some versions of the WASP printers operate on a central pivot system.
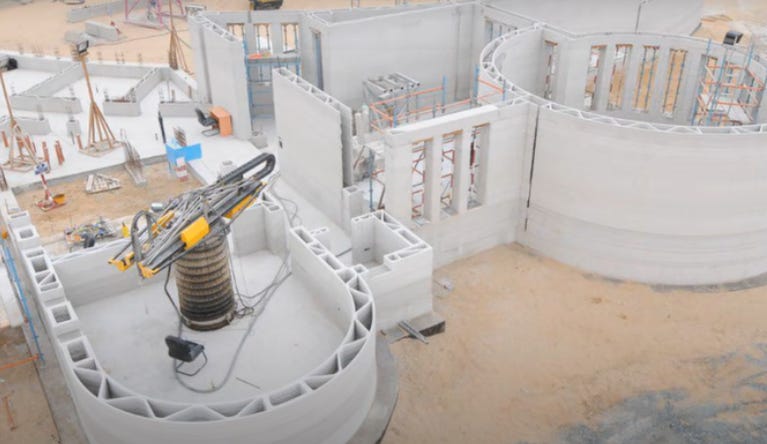
Center pivot systems have a lot of benefits. Since it only has one support, a center pivot system can set up quickly, while still reaching a relatively large area. A center pivot system can be a relatively self-contained piece of equipment in a way that’s difficult for a gantry system.
Empirically, in other domains we mostly see gantry systems in fixed environments - factories often use gantry cranes for moving material around within them. Center pivot systems, on the other hand, are more popular in temporary environments - conventional construction is largely done with center-pivot tower cranes.
Some companies implement a movement system by mounting a print-head to an off-the-shelf robotic arm, like an ABB or a Kuka. The benefit with this sort of system is that you get a highly accurate print head movement system without having to do the development work to create one. And because a robot arm has more movement degrees of freedom, you’re not limited to placing material in a 2D layer. Companies like Bruil and MX3D use robot-arm mounted print heads to produce free-form printed elements that aren’t merely a stack of 2D layers.

The drawbacks of a robot arm are price - heavy duty, 6-axis industrial robot arms are expensive. And on their own they have relatively limited reach compared to, say, a gantry system. To get around this, companies often mount their robot arm printers to some type of conveyance system. Bruil mounts theirs to a track inside their factory, and CyBe has stuck theirs onto a pair of treads.
We also see some even more out there ideas. Early versions of the WASP used a 3-armed support that seems to be designed for tall, skinny elements. Constructions-3D has what appears to be a large crane boom mounted to a sort of spider-like robot. Contour Crafting (as well as a few other folks) have floated the idea of avoiding support framework by having the printer climb the building as it grows (sort of like a 3D printer version of a slipformer). Overall, print head movement strategies show a lot of variation, which suggests no one has quite cracked it yet [2].

Inclusion of Non-Printable Items
Even under the most optimistic projections, it’s unlikely that a 3D printer will be able to print all the components of a building - non-printed items are likely to remain a substantial portion of the components.
One possible solution to this issue is to pair the 3D printer with a robot arm that sets components such as prebuilt doors, windows, and wiring into the printed elements [3]. As far as I know, the only company that has worked on this is XTreeE (though Icon did include manual placement of wiring in the walls of their recent Austin printed houses).
Industry Trajectory
Since there’s too many companies to describe individually, I’ve compiled them all together in this chart:
And a rough timeline of the fields development is here (click to embiggen):
For the most part, despite the hype, the current state of building 3D printing is fairly unimpressive. The resolution is poor, the process is sluggish (Icon’s printer can print a 10’ x 10’ room in little over 8 hours - not terrible but not setting the world on fire), the material options are extremely limited, the equipment is expensive and finicky, and the results are generally worse on multiple axes than what you could get from conventional construction. Sorry building 3D printing folks!
But the current state of building 3D printing is mostly immaterial. Building 3D printing is an entirely new construction paradigm, and a new paradigm always starts out looking worse than a mature, well-developed solution. The earliest jets performed worse than piston-driven planes, and it took decades before electric cars were anywhere near parity with internal combustion ones. A technology exists within an entire ecosystem of supporting and enabling technologies, and developing a new technology means redesigning or rebuilding a lot of existing “solution infrastructure” to take advantage of it.
Clay Christensen describes these mechanics in “The Innovator’s Dilemma”. Technology progress takes the form of an S-curve - new technology starts out inadequate and unimpressive compared to existing technologies. The initial rate of improvement is slow, and for a while it seems more like a toy than something capable of actually solving a problem. But as problems are worked out and experience curves kick in, its rate of improvement increases until it surpasses existing technology. Then, as the technology matures, the rate of improvement slows down, and progress consists of small, incremental improvements.
The important thing for building 3D printing isn’t the current state, but the shape of it’s S-curve, and where we currently are along it.
Unfortunately, figuring this out is difficult. Gwern catalogs the vast number of companies and researchers that correctly predicted the rise of some new technology, but failed to predict when it would occur. Even with an insider’s knowledge, it’s not obvious when some critical component will be good enough, or when some parallel technology development will unlock something that was previously impossible. Jet engines were outperforming piston-driven engines 8 years after their invention, but Babbage’s computer would need to wait 100 years for the development of the reliable vacuum tube. If you’re unlucky, you might have to wait even longer - Hero’s Aeolipile would eventually be able to do useful work 1800 years after it was invented.
Can we hazard a guess as to what the development curve for building 3D printers looks like? There are plenty of marketresearchreports optimistically predicting a rapid takeoff of the technology, between 2024 and 2026. But these aren’t based on any sort of fundamental technological analysis. And they haven’t done a great job of predicting the development so far - they don’t seem to even agree on what the current size of the 3D construction printing market is [4].
One way to guess at the shape of the S-curve would be to assume building 3D printers will follow the same development trajectory as traditional ones. Traditional 3D printers were originally developed in the 1980s, and it took several decades (and some patent expirations) before the technology really began to take off. It now seems to be ascending the steep slope of the S-Curve, improving at a rate of around 30% per year.
Construction 3D printing first began to be developed in the mid 2000s, a roughly 20 year lag behind traditional 3D printers. Simple extrapolation would thus predict the technology would really start to take off in the early 2030s.
We can also try to extrapolate based on patent filings. As of 2018 there were around 40 construction 3D printing patents filed per year in the US [5]. This rate of patent filing roughly corresponds to the early 90s for traditional 3D printing, also suggesting a 20 year lag period.
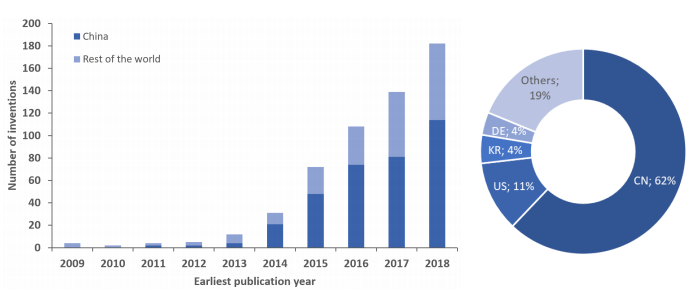
So perhaps we’ll see this technology dominate the construction landscape sometime in the next decade.
[0] - I suspect at least part of this is due to the structure of the industry - a fragmented, non-consumer facing industry means the built-in audience for any given story is low, and makes for an unattractive press target. Stories that do break through tend to piggyback on some element that people have already heard of.
[1] - Traditional 3D printing differs from construction 3D printing on a number of different axes:
Materials: Traditional 3D printing is mostly done with plastics and polymers such as ABS, PLA, or Nylon, which are mostly unsuitable for structural materials in buildings. Metal 3D printing is getting more common, however.
Techniques: Construction 3D printers don’t seem to currently make use of FDM/FFF, SLS, or SLM printing techniques. The one exception is the SLA technique, which involves using light to selectively harden a liquid resin - Mighty Buildings uses a similar technique in their printer.
Environment: Most printers above hobby level take place in an enclosed, controlled environment that’s part of the printer itself. This allows the environment to be adjusted as necessary (for example, heating up as part of the SLS process) and to protect the object being printed. But most construction printing takes place in the open air on the jobsite, exposed to the elements.
Scale: traditional 3D printing mostly works with relatively small objects. Construction 3D prints, on the other hand, work with buildings thousands of times larger.
[2] - Free construction startup idea: a Shaper Origin-like device that can mount a 3D printer to a telehandler or lift, and compensate for it’s imprecise, jerky movements. Accurate print head movement using low-cost, easily available field equipment.
Alternatively, take the same capability and mount the print head to a drone - trivially print a building of any size with no expensive support framework! They already make firefighting drones capable of lifting water-spraying equipment, no reason in principle it couldn’t be done for printing equipment.
[3] - Though this does raise the question of if you can use a robot arm to set your material, how much value does the actual printing add? Why not just use robots to build the building normally?
[4] - I suspect there’s a bias in these sorts of market reports to suggest trends that would validate their own existence. No one is going to pay $4500 for a report whose summary says “the building 3D printing market isn’t going to grow at all”.
[5] - According to this, the majority of construction 3D printing development is taking place in China, stemming from the government’s emphasis on developing 3D printing technology. Unclear if that’s true - in a crowded field, WinSun seems to be the only Chinese company that ever gets any press.