Reinforced concrete is, by a large margin, the most widely used building material on earth - by mass, we use as much reinforced concrete as every other material combined. One reason for this volume of use is concrete’s versatility - because concrete is placed as a liquid, it can be used to form structures of virtually any size and shape. Placing concrete thus requires some way of forcing the liquid concrete into the shape that you want it to take. This is traditionally done with concrete molds called forms or formwork [1]. Liquid concrete gets poured into the formwork, it solidifies [2], and the formwork is removed, leaving behind solid concrete in the shape of your structure.
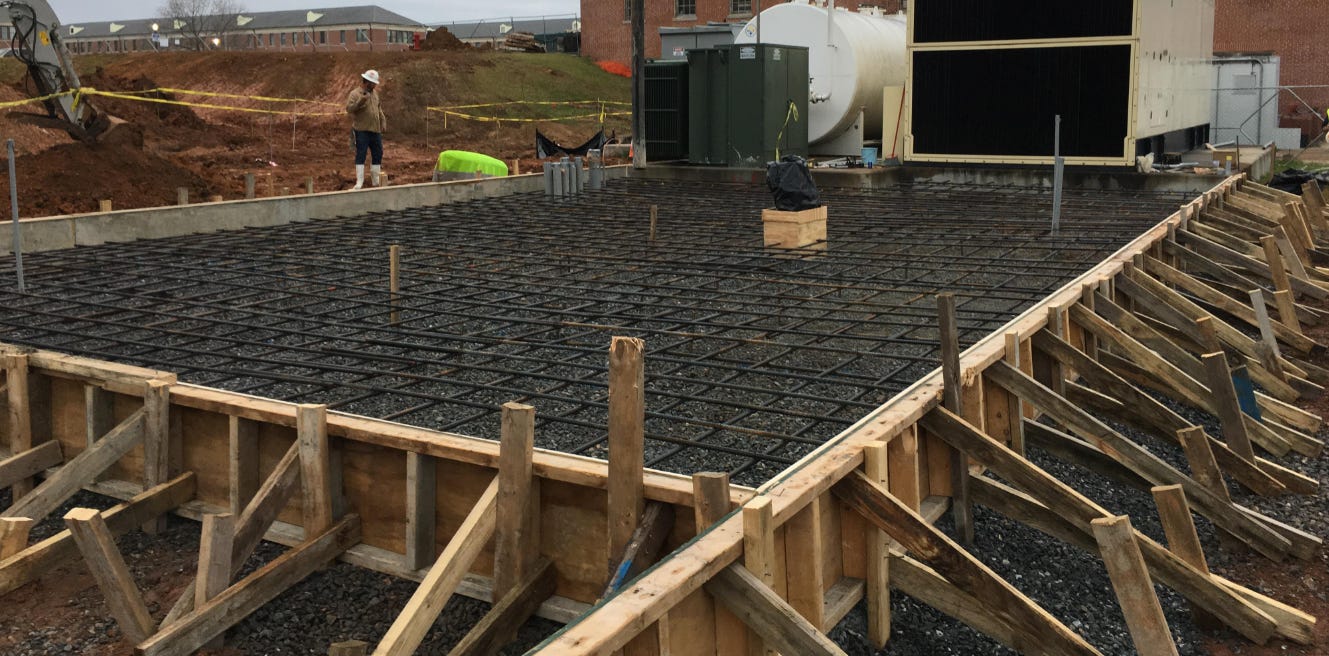
The simplest way of using formwork is to just build what amounts to a liquid-tight box in the shape of your structure, then fill it full of concrete. This method for forming concrete dates back thousands of years - Roman builders would use timber forms to build foundations, walls, arches, and other structures from concrete (in some cases, the imprint of the formwork can still be seen in the concrete).
Similar methods of formwork construction are still used today - builders use a variety of materials (wood, steel, aluminum, plastic) to construct their forms. In some cases (such as with wood forms), the formwork gets built on-site, while with others the forms are prebuilt, and delivered to the jobsite and arranged in the proper position.
The “build a box” method is probably the most common method of forming concrete. But from an efficiency standpoint, it’s far from ideal, as it requires a lot of time, labor, and expense to set up and tear down the formwork - you're essentially constructing, then tearing down, a second building in the shape of your building (yo dawg I heard you like buildings). Thomas Edison noted this problem in 1903, stating that concrete construction required “erecting two wooden walls to get one concrete wall”. Using formwork means either wasting the material used to construct it (for single use formwork) or cleaning, maintaining, transporting and storing the large, bulky equipment required (for multi-use formwork).
And the more complicated your concrete structure, the more time and effort it takes to build the formwork for it. In practice, this makes it difficult to take advantage of some of reinforced concrete’s versatility. It's possible, for instance, to create large structures out of extremely thin “shells” of concrete. But a thin concrete shell requires a somewhat complex shape (the material needs to be arranged to minimize the amount of tension in it), which means complex formwork:
Similarly, one way of spanning large spaces efficiently with concrete is by using rib or waffle slab construction, which uses additional formwork to create voids in the slab, reducing its weight.
A similar building method to this is the voided biaxial slab system, which involves placing large plastic spheres in the concrete to create voids:
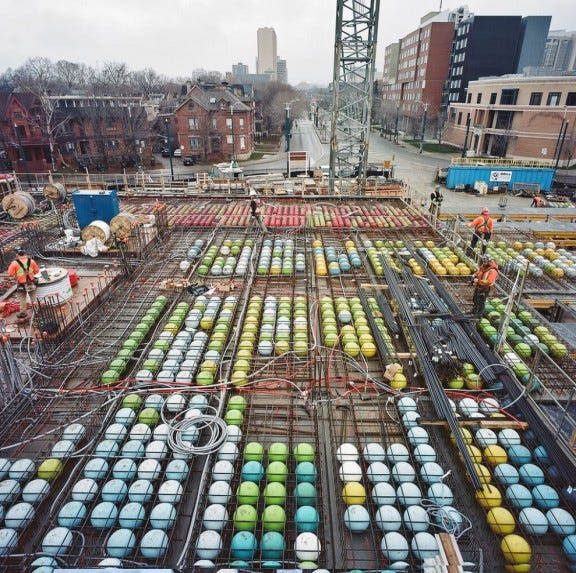
These methods all are essentially trading off additional labor (required to build the more complex formwork) for reduced material use. As labor got comparatively more expensive, this tradeoff made less sense, and most modern concrete structures that use on-site formwork are generally designed to be as simple as possible to form (ie: lots of flat surfaces).
Similarly, Edison’s method of constructing concrete houses in a single pour was derailed in part due to the complexity and expense of the formwork required.
Because of the difficulties associated with concrete formwork, folks have developed a variety of different building methods to try to improve it - much of the last century of concrete technology development can be thought of as a way of solving the formwork problem.
Don’t move the formwork
One simple way to avoid setting up and tearing down your formwork is to just leave the formwork in one place, and instead move the concrete. This is the method precast concrete construction uses - a precast concrete plant is constructed that has several more or less permanent [3] concrete forms. Concrete is cast in the form, removed, and transported to the jobsite where it’s lifted into place by crane. Precast has been used in the US since the early 20th century, and became popular in the 1950s and 1960s.
This method of building has some advantages, and is popular for certain kinds of structures (notably parking garages and bridges in the US), but in a sense this just trades the difficulties of setting up and tearing down formwork for the difficulties of moving large pieces of concrete around.
A variant of this idea is, rather than moving the concrete, you move the entire precast factory - set up a precast plant at your jobsite, and have it make concrete components which are then lifted into place. This method is seen occasionally (several attempts at mobile precast factories appeared in the 1960s, and today Weckenmann will sell you a mobile precasting plant) but is not especially popular (it's not obvious to me what sort of project this would make sense on - it seems like it would require a relatively large volume of relatively small pieces).
Make the formwork easier to move
Instead of not moving the formwork, we can also try making the formwork easier to move. This is the concept behind slipforming. With slipform construction, a special form is used which is supported by a partially complete concrete structure below. As concrete is added to the form and it solidifies, the slipform slowly “climbs” up the structure. Using this method, a tall concrete structure can be built using a comparatively small section of formwork. Slipforming was first developed in the early 20th century for the construction of grain silos, and is a common method of construction for building bridge piers, elevator cores, storage tanks, silos, and cooling towers.
Slipforming can also be used horizontally. Hollowcore plank, for instance, is a precast concrete product used for building floors and roofs that is produced using a slipforming machine [4]. A special concrete mix is fed into the machine, and as it travels it slowly extrudes a hollowcore slab. Like vertical slipforming, hollowcore plank was first developed in the early 20th century. A similar building method is used for road construction.
Use part of the building as the formwork
Rather than using temporary formwork that you need to set up and tear down, in some cases the formwork can be designed to become part of the building itself. One popular method is with composite construction, where a layer of concrete is bonded to another structural element. Composite deck construction, for instance, starts with a thin sheet of profiled steel. The steel deck acts as the formwork for a layer of concrete that gets added on-site, and the combined concrete-steel element acts as the building’s flooring system. This system has the advantage of compensating for concrete's weaknesses - concrete is strong in compression and weak in tension, so this building method places steel exactly where it's most needed. Composite deck construction started to appear in the 1920s, and had become popular by the 1950s. Today, composite deck construction is an extremely popular method of building for commercial buildings.
Another type of composite construction is Diversakore, which uses a similar principle as composite deck (a thin steel element acting as temporary concrete formwork), but is used to form heavy structural members like beams and columns.
We can also use concrete as the form - it's not uncommon, for instance, for precast concrete members to get an additional layer of concrete topping once they’ve been placed in the building.
Another “use another building element as the formwork” method is to use insulation as the formwork material. This is the method behind Insulated Concrete Forms (ICF). ICF consists of modular ‘blocks’, which consist of two layers of insulating foam separated by plastic spacers. Walls are built up block-by-block, and then concrete is poured in the void, leaving a solid concrete wall with a layer of insulation on each side. One downside of this method of building is that only the exterior walls have any insulating value, so interior walls built using ICF essentially wastes the insulation. ICF block construction was first developed in the 1960s, and you sometimes see more modern variants of it such as the Hercuwall system.
Another way of using a building element as part of the formwork is to use the ground floor concrete slab of the building as the bottom of your formwork. This is the method that tilt-up concrete uses, which casts concrete panels flat against the slab of the building, and then tilts them up into place as the building’s walls. Tilt-up concrete was developed in the early 20th century, and is extremely popular for distribution centers and industrial buildings, as well as for smaller commercial buildings.
A variant of this method is to cast all the floors of a building on the ground, one on top of the other, and then lift each one into place. This was the method behind the “lift slab” method of construction, somewhat popular in the US in the mid 20th century but largely unused today (partly due to at least one high profile construction failure).
For foundation elements, it’s often possible to avoid using formwork by casting directly against the earth. Shallow foundations, for instance, can sometimes avoid formwork by just casting against the sides of the excavated trench (if the soil is stiff enough to allow this).
Similarly, auger cast piles are a deep foundation system where a deep hole is drilled and then filled full of concrete as the auger is withdrawn. Auger cast piles were first developed in the mid 20th century.
Use a concrete that requires less formwork
Formwork is required for building concrete structures because concrete starts out as a liquid. But “liquid” is something of a sliding scale - if the concrete mix has the necessary properties (viscosity, “stickiness”, etc) to be self-supporting, it may be possible to avoid using formwork, or at least use substantially less of it.
One example of this sort of method is shotcrete, which is concrete that’s applied pneumatically with a spray nozzle. Shotcrete requires a surface to spray against, but is viscous and sticky enough to hold its shape without any additional formwork.
Shotcrete was first developed in the early 20th century, and is commonly used where it can be sprayed against an excavated surface (such as in pools, tunnels, and mines), but it can also be used for other structures. The Emmedue building system, for instance, uses layers of insulation as a surface to receive shotcrete (a sort of reverse ICF).
Another version of this type of building method is with concrete 3D printing, which uses a print head to extrude a thin layer of concrete viscous enough to be self-supporting. Like with conventional 3D printing, a large structure can be built up layer-by-layer. Concrete 3D printing is a relatively recent development, and only a few hundred buildings worldwide have been built with the technology. (I’ve previously looked at concrete 3D printing here).
You can also use 3D printing to print the formwork directly. Batiprint, for instance, 3D prints a foam formwork that then gets filled with concrete (akin to ICF).
Another example of this sort of building method is the no-fines concrete mixes (such as the Wimpey No-Fines system), which are concrete mixes without fine aggregate (ie: sand). The lack of fine aggregate yields in a concrete that’s much less fluid, which results in less pressure on the formwork, allowing for the use of lighter, less rigid forms. No-fines concrete structures were first built in the early 20th century in Europe, and the Wimpey No-Fines system was briefly popular in post-war Britain for home construction, but no-fines concrete never gained significant traction in the US (though you do sometimes see it used in drainage applications).
Use a fabric formwork
One potential way of reducing the cost of formwork is by using a lightweight fabric instead of a heavy, rigid material like steel, wood or plastic. Fabric is lighter and easier to manipulate, but is much more limited in how it can be used to resist load - fabric can only carry tension, so the formwork needs to be arranged accordingly. One way of doing this is to have the fabric be stitched to a more rigid surface. The Ctesiphon system, for instance, consisted of fabric draped over a series of steel catenary arches, which was then covered in concrete. It was used to build approximately 50 concrete shell structures during WWII.
A similar method was used to build catenary structures in the 1960s. Today, the Fastfoot system uses fabric attached to a lightweight wood frame to create foundation formwork, and architect Kenzo Unno uses fabric formwork to build single family homes in Japan.
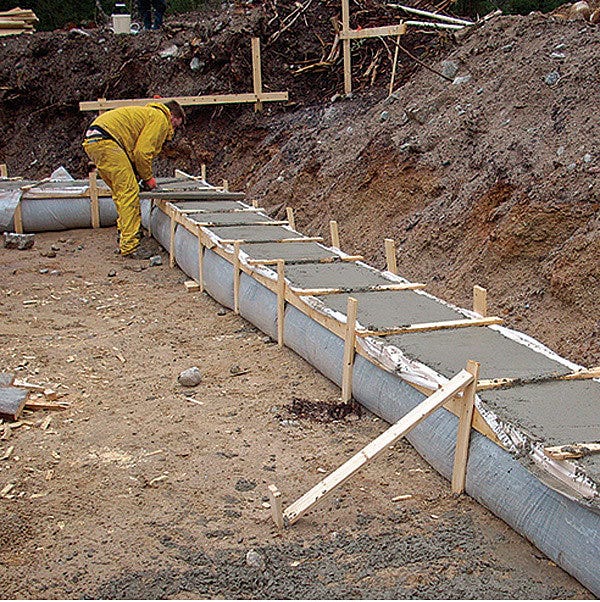
Use an inflatable formwork
But needing to have a rigid structural element on your fabric forms limits its usefulness. One way around this is to keep your fabric in tension by pressurizing it. With pressurized fabric formwork, you don’t need any large, bulky elements at all - all you need is a pump. And as a bonus, you don’t need to spend time laying out your formwork at the jobsite. You simply stitch the fabric together in the shape of your building, and when it inflates the formwork will take the proper shape.
This method of concrete forming was first developed in the 1940s by Wallace Neff, and saw some minor success in the 1960s and 70s. Typically, these structures would be built by inflating the formwork and then applying a layer of shotcrete to either the inside or outside. Builders like David South and Dante Bini used this method to build hundreds of structures.
One drawback of this method of construction is that you’re limited in what shapes you have available. The fabric needs to be inflated to a high pressure to provide enough support to act as a formwork, and anything you inflate will want to take the shape of a sphere or cylinder (and indeed, most existing pneumatically formed structures in the world are sphere-shaped). To truly be a solution to the problem of constructing formwork, we’d need our inflatable forms to take any possible shape.
A new company, Automatic Construction, is developing the technology to do this. (Disclosure: I’m an advisor to this company, but I have no financial interest in it). They’ve developed a novel formwork system that uses drop-stitch fabric as the formwork material.
Drop stitch fabric (also known as double wall fabric) consists of two layers of fabric joined by tens of thousands of cross stitches. The cross stitches allow drop stitch fabric elements to be pressurized enough that they can support significant weight while still forming flat, rigid surfaces. It was developed in the 1950s by the US military, who used it to build an inflatable, lightweight airplane (the Goodyear Inflatoplane weighed just 225 pounds, and was capable of flying with an additional 365 pounds of pilot and fuel). Today, drop stitch is used to make inflatable boats, paddleboards, docks, and gym mats.
Automatic Construction is aiming to use drop stitch fabric forms to rapidly and inexpensively build concrete structures. With their system, drop-stitch fabric forms are created in the factory in the shape of the structure to be built - one “form” will consist of the floor, walls, and roof of the structure, complete with windows and other openings. The form gets delivered to the jobsite, inflated, and then pumped full of concrete to form the structure. Right now, Automatic’s forms are about 300 square feet, with larger structures formed by splicing together multiple forms (reinforcing extends out from one form into the adjacent form), though Automatic is exploring using forms up to several thousand square feet. Once the concrete is cured, the formwork can be left in place as the structure’s waterproofing, or be removed.
Right now, reinforcing is added manually (the formwork is pressurized enough that rebar can simply be poked through the drop stitch and they form stays inflated), though in the future it will be added in the factory. To support the overhead slab, it uses a second set of forms, which inflate beneath the slab to provide temporary shoring - once the slab is cured, these forms are removed and reused.
Automatic is still in the early stages - they’ve built a few test structures, and are planning on next constructing a pair of ADUS and a single family home. Right now they’re focused on single-story construction, though they ultimately foresee targeting all aspects of the concrete market as the system gets developed. They hope to ultimately drop the cost of cast-in-place concrete construction by 80%, which is refreshingly bold.
Concrete formwork and construction innovation
We’ve previously noted that adopting new construction systems can be difficult from a risk point of view, and that successful innovations tend to be things that require limited changes to the overall process. What can we learn about construction innovation from the development of concrete forming systems (which largely require significant process changes)?
It's something of a mixed bag. On the one hand, almost every way you could think of for forming concrete seems to have been tried at some point, and many of them became incredibly popular construction systems. Precast concrete, composite deck, shotcrete, and tilt-up concrete are all popular building methods in the US for certain kinds of structures.
On the other hand, the most successful systems seem to have largely been developed in the early 20th century, when reinforced concrete technology was relatively new, and the overall building technology landscape was in flux. Beyond the development of reinforced concrete, the steel-framed building (built on the back of cheap Bessemer steel), electrification, indoor plumbing, widespread availability of dimensional lumber, and (somewhat later) air conditioning completely changed the requirements and means for constructing buildings over a relatively short period of time in the late 19th and early 20th century. Concrete innovations that came later (such as ICF, Lift-Slab construction, and Diversakore) into a more static construction environment seem to have had much less success in the US. (Auger cast piles are an exception, perhaps explained by the fact that the “interface” between a deep foundation and the rest of the building is smaller than for other sorts of building systems).
What does this suggest for new concrete forming technology like 3D printing or inflatable drop stitch formwork? To me, it seems to suggest that this technology would be best served by finding some particular building type their system handles particularly well, that’s less well-served by existing solutions (this is the basic Christensen disruption / Paul Graham playbook, with the added complication that the new technology may not ever displace the incumbent). But it also suggests that the barrier to adoption is quite high, and a system has to be a really significant improvement over the status quo to be adopted
[1] - This is sometimes called “falsework” or “shuttering”, depending on the country.
[2] - “curing” is the process of cement reacting with the water, known as hydration.
[3] - The forms will actually be moved in and out of storage depending on whether they’re needed or not, but they can be thought of as “effectively” permanent.
[4] - There are actually multiple sorts of hollowcore machines, some of which are called slipformers, some of which are called extruders, but for our purposes this distinction isn’t important.
Structural concrete work is especially resistant to change because of the consequences if your new innovation fails, and no one wants to be the guinea pig for it.
A somewhat related personal example - We were building a very typical 5 story concrete office building. Since the first floor had higher ceilings for retail than the office floors above, the concrete contractor built his formwork to the typical 2-5 floor height and then slipformed the columns coming off the ground floor so they were usable on all floors, which his drawings did not show.
Our structural engineer absolutely blew a gasket when he learned there would be cold joints in the columns. It became a huge ordeal that nearly ended with us tearing out and re-pouring the columns and required extra testing and I believe we had to drill and epoxy extra bar for the engineer to accept it. The concrete sub claimed means and methods, they do it all the time, it saves cost and time, etc etc - which was true! - but this relatively minor deviation got them absolutely drug through the ringer, so its no surprise that innovation isn't growing by leaps and bounds in the concrete trade.
Very thorough and interesting.