Welcome to Construction Physics, a newsletter about the forces shaping the construction industry.
“There are hundreds of shop-fabricated house building schemes, all technically more promising than the hand-to-mouth methods now current on the building sites. Why do these technical ideas, in the United States, for instance, seem largely to stay in the scheming stage instead of giving us a splendid show of contest in the broad field? Although the grandstands are crowded to the point of collapse, the track is not yet open.” - Richard Neutra, 1950
The book Car chronicles the development of the 1996 Ford Taurus. In the book, once the design of the car is complete but before manufacturing has begun, Ford builds 99 prototype cars for testing. The final version of the Taurus will cost around $20,000, and take around 10 hours for the factory to assemble, which will allow Ford to sell over 300,000 Tauruses a year. But those first 99 prototypes (which use the same parts as the final version), are assembled by hand over the course of 4 weeks, and cost 400,000 dollars each. Efficient manufacturing brings the cost and the time to build a car down by a factor of 20.
For over 100 years, people have been waiting for the same sort of efficiencies to happen with buildings.
The relative inefficiency of the construction industry is no secret. Unlike other industries, where advances in technology have continuously increased what a single worker can accomplish, construction remains as labor intensive as ever. Since 1945 in the US, productivity in manufacturing has increased 8.6 times. In the early 1800s, agriculture employed over 80% of us workers - today, it employs less than 2%. But construction productivity has only increased by 10% since 1945 - and construction productivity in the US has actually decreased since the 1960s.
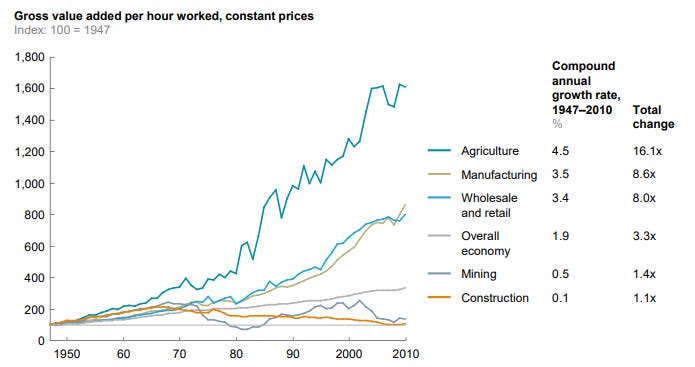
Buildings are built no faster today than in the past. The Empire State Building, completed in 1931, famously took merely 410 days to build. The Chrysler Building, completed in 1930, took 563 days. But 432 Park Avenue, completed in 2015, took over 1500 days. Average time to build a single family house has gone from 4.8 months in 1971 (the earliest year data is available), to 7 months in 2019. Even scaling this by average house size (around 1600 feet in the early 70s, compared to over 2600 square feet today), we're still slower today.
Look at an old set of construction documents, and you'll find construction details and structural systems nearly identical to the ones used today. Open up a design manual from the 1920s or the 1930s, and you'll find it depressingly applicable to today's buildings. Dimensional lumber, plywood, reinforced concrete, hot-rolled and cold-formed steel sections, metal roof deck, pre- and post-tensioning - almost every building framing system currently in use has been in use since the 1950s, and in many cases far earlier.
Materials remain similar as well. Modern construction steels are only slightly stronger than those of the early 1900s. Higher strength concretes are available, but any given project will likely use a 3000 psi mix no stronger or more durable than was used 100 years ago. Woods have actually gotten weaker over time in many cases, as lumber from old growth forests has been replaced with younger, farmed trees.
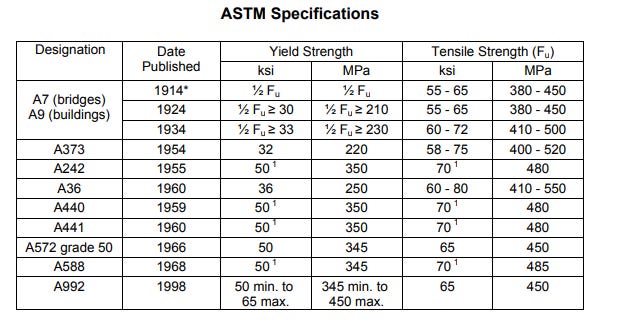
The construction industry doesn't look like other mature industries, which tend to consolidate down to a few large players as efficient businesses grow and inefficient ones shrink and die. In 1909, shortly after Ford introduced the Model T, there were 272 auto manufacturers in the US. By 1965, just 3 manufacturers (GM, Ford, and Chrysler) controlled 91% of the market. Boeing and Airbus combined have 91% of the commercial aircraft market. Hard drives were once built by 85 different manufacturers - today it's just 3.
But construction still looks like an industry that's finding its footing. The market remains highly fragmented, with no player capturing more than a small percentage of it. The US has over 700,000 construction companies. In Europe, 94% of the 3.3 million construction firms have less than 10 employees, with an average of 4 each. Even narrowing our focus to one facet of the construction industry, single family homes in the US (not even worldwide!), we find that no company has more than 20% of the market, and 73% of the market is split between 15 builders. This is despite the fact that the single family home is a product that has been in existence for hundreds of years, and continues to use a framing system invented in the 1800s.
It is of course always possible that some miraculous invention may open the gates which have so long resisted all attack, but this seems very unlikely. It has seemed to some that enormous investments of capital might offer the key, but that this in itself is not enough seems witnessed by some recent events. Some of us have hoped that a thriving, if small and unspectacular, manufacturer of fairly conventional houses, might, step by step, year by year, introduce the improvements in structure and materials and the efficiencies in design and production which would gradually drive down the cost and increase the market. But none of these things has yet come about. - The Prefabrication of Houses, 1951
The blame for this is often placed on a lack of prefabrication. That buildings need to be built offsite, in factories, like all other consumer goods. Many companies have attacked the problem from the angle of using manufacturing best practices, trying to do for construction what Henry Ford did for automaking.
But offsite construction has existed in one form or another since the 1800s. During the San Francisco gold rush, houses were shipped to the west coast from as far away as New York. After World War I, over 10,000 prefab 'Dorlonco' houses were built in the UK for returning veterans (and hundreds of thousands more prefabs would be built after WWII). From the early 1900s up until the 1980s, thousands of homeowners purchased pre-cut homes sold out of catalogs from Sears, Aladdin Homes, and others.
Yet these efforts never manage to reshape the industry. The companies always seem to either give up, go out of business, or eke out a small share of the construction market. The modular construction market has captured around 5% of the construction market. Modular projects are lucky if they're even able to deliver buildings more cheaply than standard, site built construction, much less show a 20x improvement in efficiency.
History is littered with the carcasses of massive, well-capitalized companies that tried and failed to bring advanced manufacturing techniques and new technologies to the construction industry. Governments around the world spent millions of dollars and built thousands of houses in an attempt to kickstart innovation in the industry. Dozens of new framing systems have been tried in earnest. A thousand flowers have bloomed and wilted.
Worldwide, construction makes up 13% of global GDP, and employs 7% of the workforce. In the US alone, over 900,000 single family homes were built in 2019. The potential rewards for whoever can displace incumbents, and build buildings more efficiently, is massive. But despite this, construction continues to move along seemingly unchanged.
The goal of this newsletter is to try to understand why these things are true - why buildings are built the way they are, and why the construction industry looks the way it does. The hope is that over time, we can identify the fundamental mechanics that govern construction.
This is hugely informative and interesting. Thank you for putting it all together.
Awesome intro, thanks, especially re nearly identical building framing systems for so long.
Do you think many of those 3.3m construction companies in Europe (incl Russia) were defunct at time of writing? (Today that estimate is 3.7m.) That number simply feels too off for Europe's population.