On October 1st, 47,000 members of the International Longshoremen's Association (ILA), primarily dockworkers on East and Gulf Coast ports, went on strike after failing to agree contract terms with USMX, an alliance of port operators and employers. (West Coast ports, which are worked by a different union, the International Longshore and Warehouse Union, remained open.) Along with higher pay, the main point of disagreement was automation; the ILA demanded a complete ban on introducing new port automation. The strike ended on October 3rd with a tentative agreement on wage increases, but negotiations over automation will continue until January 15th.
The strike sparked a discussion about the quality of U.S. ports, and the degree they need to be automated to improve their performance. Most folks have (reasonably) assumed that the union is holding back port automation that would improve productivity. In the 1960s, dockworkers unions vehemently protested against introducing the productivity-enhancing shipping container, and current ILA president Harold Daggett has complained about EZ passes for highway tolls eliminating union jobs. The ILA’s case has not been helped by the extremely high wages of longshoremen (and of Daggett), the video of Daggett threatening to “cripple” the entire economy, or the fact that Daggett is alleged to have connections to organized crime.
But despite Daggett and the ILA doing everything in their power to turn people against their cause, the case for port automation isn’t straightforward. It is true that U.S. ports perform poorly compared to ports around the world, but it’s hard to blame this entirely on a lack of automation. Few ports around the world are automated, and the most heavily automated ports (including in the U.S.) don’t necessarily perform the best. Lack of automation may be partly behind poor American port performance, but there are many other factors as well.
U.S. container ports perform poorly
Since 2020, the World Bank has released a Container Port Performance Index, which ranks ports around the world based on how long vessels stay in port. Since a ship waiting in port isn’t making money by transporting cargo, shipowners want them in and out of ports as quickly as possible. Major American ports routinely rank near the bottom of this list. Los Angeles, the largest port in the U.S. by container volume, ranked #375 in 2023, and Long Beach (the second-largest) ranked #373. Savannah ranked #395, and Seattle ranked #360. Of the five largest American container ports, only New York-New Jersey cracked the top 100 (at #92). On average, per this index the U.S. has the worst-performing ports of any country in the world.
Other measures of port performance show the same thing. It takes roughly two to three times as long to move a container in a U.S. port as a Chinese port, and U.S. ports are slower than ports in most other major shipping countries.
The U.S. does better on bulk cargo and tanker handling, but only manages to be average or somewhat below average in cargo loading/unloading rates and ship waiting times.
This situation is not new. Since at least the 2010s, American container ports have been substantially less productive than ports in Southeast Asia.
However, it’s not clear how much this can be blamed on automation.
The basics of port automation
When we talk about port automation, we’re really talking about a collection of different tasks, which can be automated to different degrees. We can broadly break container handling automation into three different groups: ship- or quay-side tasks, yard tasks, and land-side tasks. The first are tasks required to move containers from the ship onto the shore, the second are tasks required to move containers around the storage yard, and the third are tasks required to move containers out of the port via land-based transport.
When containers are placed on a ship, they’re attached together with twistlocks to keep them from moving around. These locks must be connected after the containers are loaded and disconnected before they can be unloaded, part of a process known as lashing (which also includes installing tie-rods and turnbuckles). Lashing is a difficult process to automate (though automated twistlocks do exist), and it is mostly done manually, even in highly automated ports.
Containers are moved on and off ships using large ship-to-shore cranes. While some parts of this process can be automated, skilled workers are still required to align the cranes with the container, in part because the ship is moving slightly as containers are being picked. Traditionally these cranes were operated from cabs attached to the crane itself, though some ports are installing systems that allow for remote operation.

Unloaded containers will typically be moved to a storage yard, using a range of types of vehicles. Some, like regular trucks, move horizontally, while others, like straddle carriers, can both move it horizontally and lift the container to stack it. These operations can be automated using automated guided vehicles (AGVs) and automated lifting vehicles (ALVs).
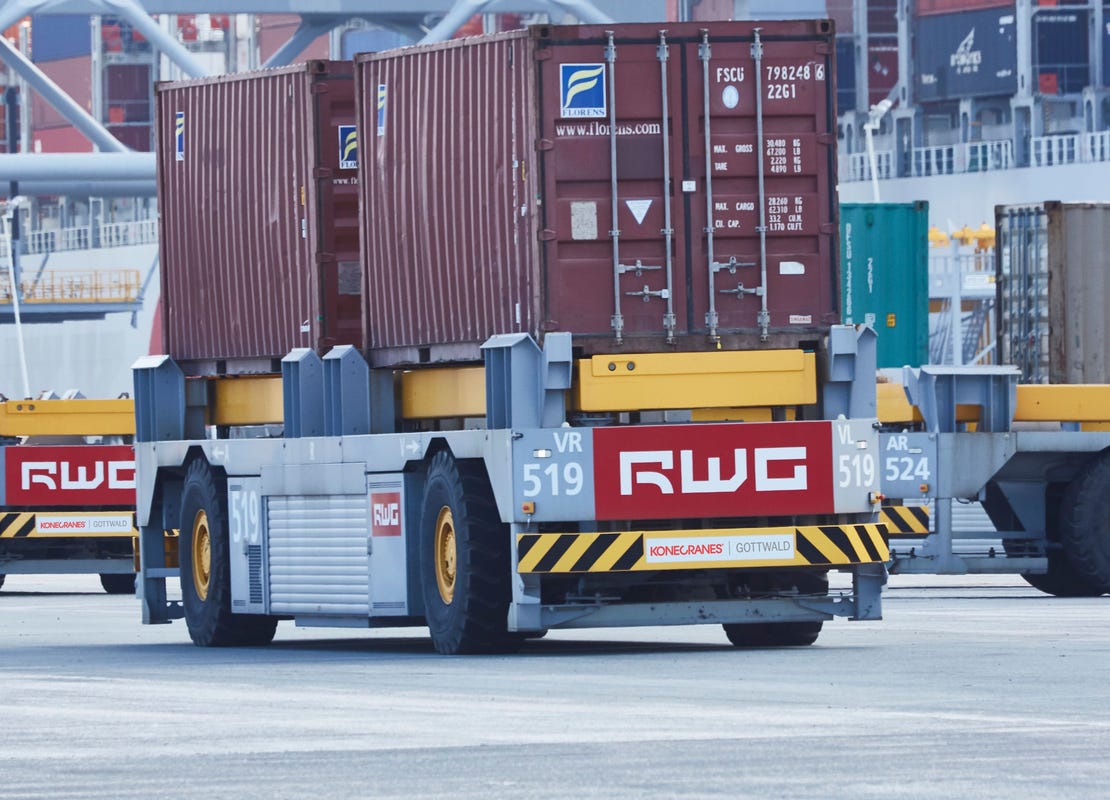
Containers in the storage yard will be moved around either via lifting vehicles or by large gantry cranes. Gantry cranes come in two types: either rail mounted (called RMGs) or equipped with large rubber tires that allow them to move without needing rails (called RTGs). Both types of cranes can also be automated.
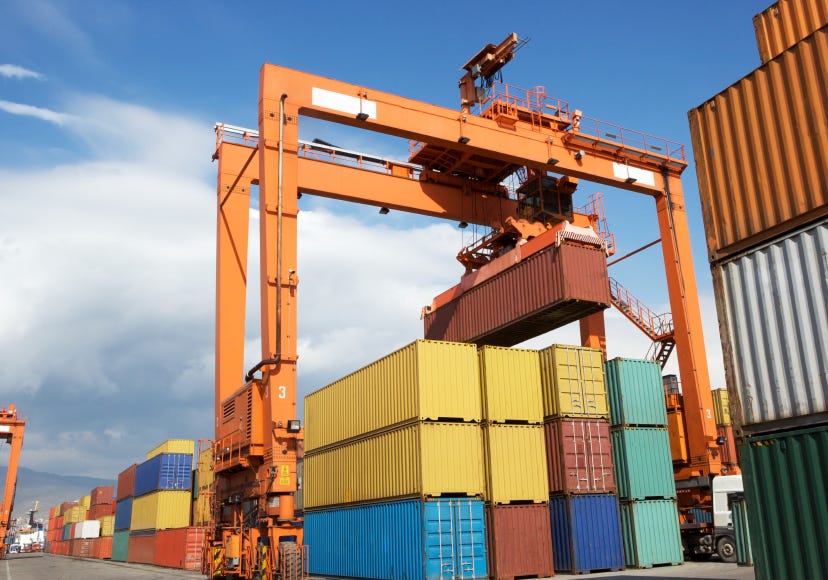
From the yard, containers are moved out of the port onto land via trucks or rail. Containers must be checked at the port gate, and parts of these gate-checking operations can also be automated using things like radiofrequency ID (RFID) and optical character recognition (OCR) systems to automatically track and update container movements.
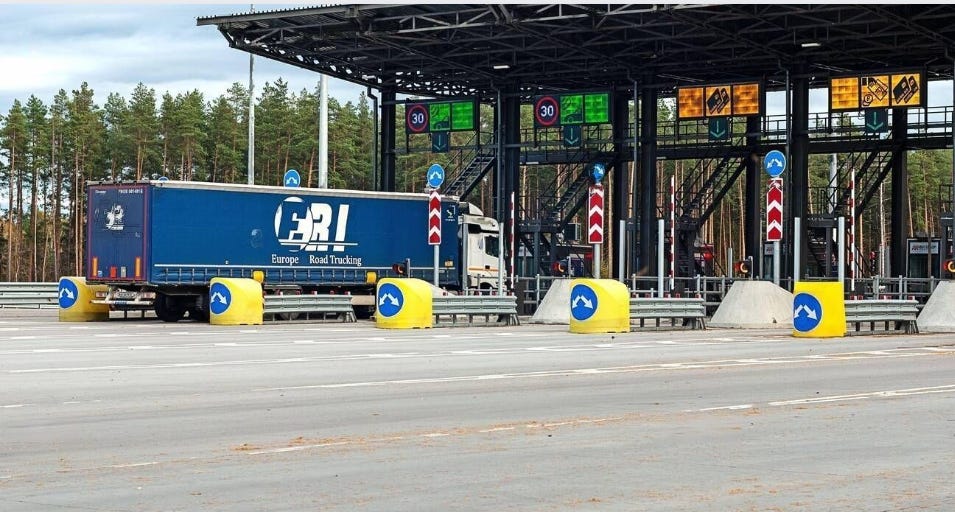
When a container port is referred to as “automated,” it typically means it has adopted container-moving technologies like automated guided vehicles and straddle carriers, automated gantry cranes, and remotely operated ship-to-shore cranes. Lashing is still mostly done manually even in automated ports, and even “un-automated” ports (including most large ports in the U.S.) have adopted gate automation systems.
Port automation and productivity
Does automating container handling improve port productivity? It’s not clear that it does, or that the lack of it is why U.S. ports perform so poorly. For one thing, few ports around the world have adopted this sort of automation. As of 2021 there were around 63 automated or semi-automated container terminals in the world out of more than 1,300 container terminals total, accounting for only about 4% of global container capacity. Where automation has been adopted, it’s often limited to a single container terminal out of many in a given port, each operated by different companies.
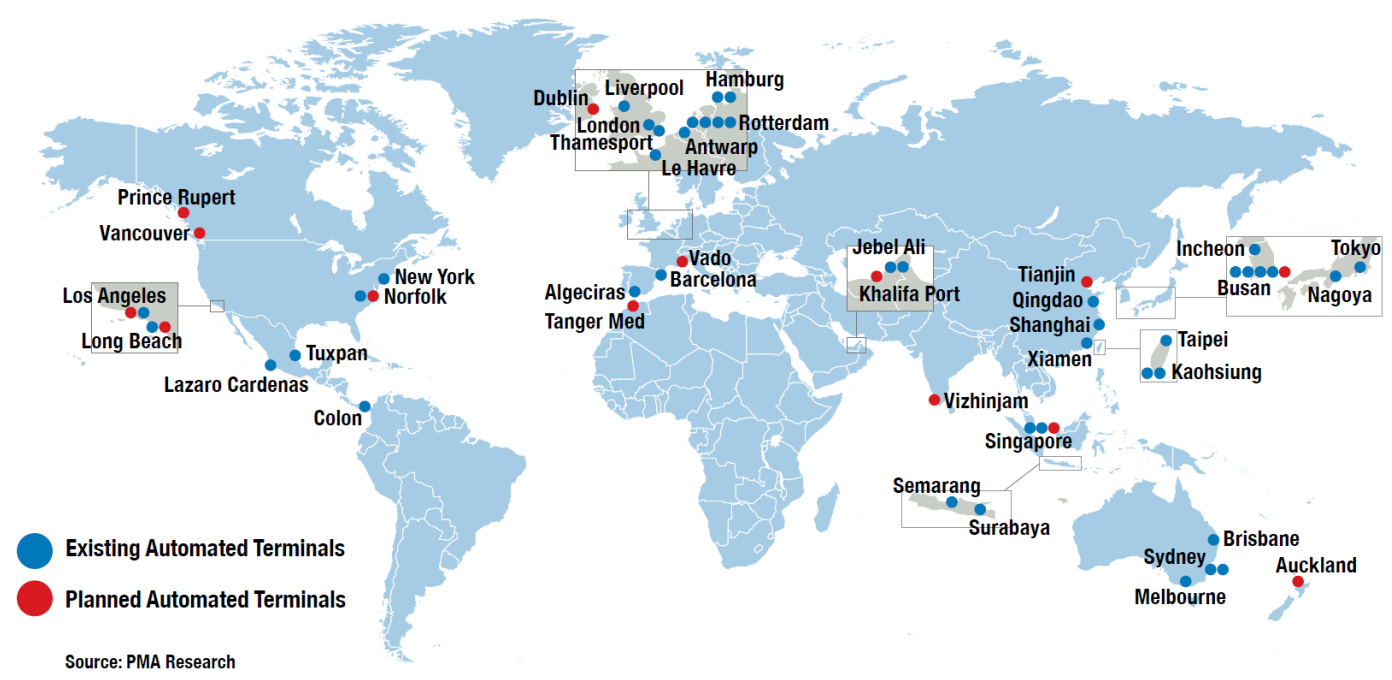
Several of these automated terminals are in the U.S. Los Angeles, for instance, has two automated terminals, and its sister port of Long Beach has another. On a country-by-country basis, in fact, the U.S. is towards the higher end in the number of automated or semi-automated container terminals it operates.
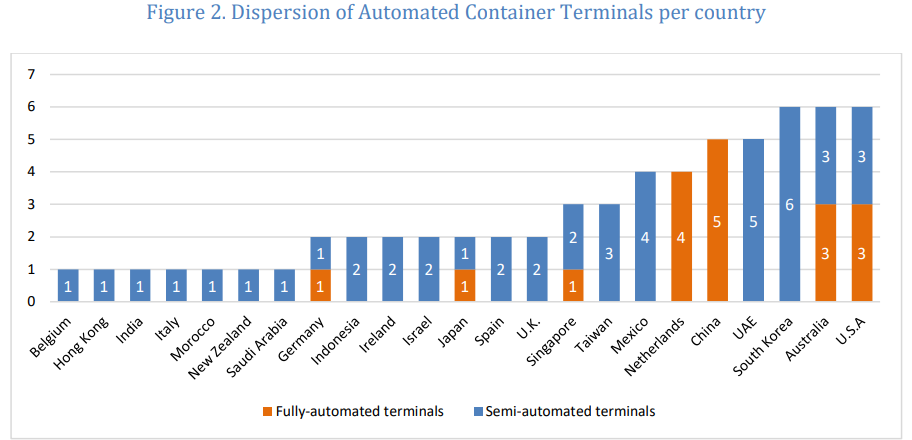
The ports that have adopted automation aren’t necessarily particularly efficient. Rotterdam was one of the first ports to automate (its first automated terminal opened in 1993), and today it’s one of the most heavily automated ports in the world, but its port performance ranking is just #91, one point above the comparatively less automated New York, and far below the un-automated ports of Charleston and Philadelphia (#53 and #55 respectively). Likewise, the U.S.’s most automated port, Los Angeles, comes in very close to the bottom of the worldwide rankings, while the top two ports on the list (Yangshan in China and Salalah in Oman) have just one and zero automated terminals, respectively.
Other analyses likewise point to a complex relationship between automation and efficient port operations. A McKinsey survey from 2017 found that while port automation reduced labor costs, it actually reduced port productivity between 7 and 15%, and the labor savings weren’t necessarily enough to justify the investment. A 2021 OECD report similarly found that “automated ports are generally not more productive than their conventional counterparts,” and a 2024 GAO report also noted that both U.S. and international ports found “mixed effects” on performance when adopting automation. APM Terminals, a global container terminal operator, stated in 2021 that its fully automated terminal in Rotterdam (Maasvlakte 2) had lower performance than its older, non-automated terminal (Maasvlakte 1). A 2021 survey of automated port operators found that while port operators did generally receive benefits they expected from automation, they were somewhat prone to overestimating the reduction in container handling costs (though they also underestimated the benefits to things like truck turn time).
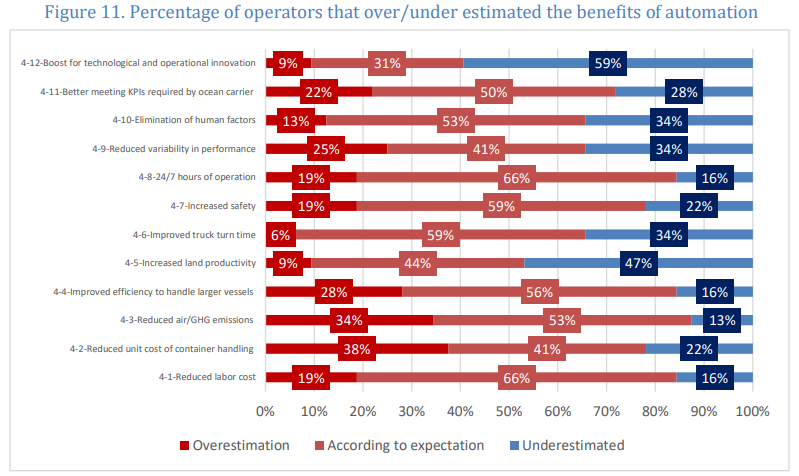
Why is port automation not a more obvious win? A variety of factors are at work. For one, automated container handling equipment is not always as capable as manual handling. The GAO survey of automated port operators found that while automated equipment had benefits like being able to stack containers closer and sometimes needing fewer container moves, it was sometimes slower and less capable than conventional equipment, even after several years of operation. Automated cranes might make fewer crane moves per hour due to inability to operate in adverse weather conditions, like rain or fog, that a human could handle. When the Port of Auckland tried to adopt automated handling equipment, automated straddle carriers were found to operate at just one third the speed of manual ones, and often behaved unsafely and unpredictably. Auckland ultimately abandoned its automation project after spending $400 million (and losing hundreds of millions more due to shipping delays), and is now converting its automated straddles to manual. The performance of remotely operated cranes has sometimes been disappointing for similar reasons.
Automated equipment is less flexible than a human operator, and it can’t respond to unusual or unexpected situations that a human could handle; AGVs, for instance, often follow fixed paths guided by transponders embedded in the concrete. And automation does best with a steady, predictable volume of containers. But as container ships have gotten larger, container volumes have often gotten less steady, with more peaks and troughs. Highly varying volumes might be more easily handled by a human labor force that can be scaled up and down as needed.
Relatedly, it’s typically easier to install automated equipment in a new, greenfield container terminal than to retrofit an existing terminal. Union work rules that limit labor flexibility might also make it hard to take maximum advantage of automated equipment. These last two factors are likely part of the reason why Chinese ports tend to see greater advantage from automation than U.S. ports.
Container unloading and transport is a long sequence of operations, of which only some can be addressed by automation. If your operations aren’t carefully synced, or they’re bottlenecked by some other factor unrelated to automation (such as the availability of truck chassis), then automation can’t do much to help. Conversely, carefully synchronizing operations to minimize waiting and waste doesn’t require automation to achieve. In 2013, the best-performing container terminal in the world was a non-automated APM terminal in the Japanese port of Yokohama. It achieved this via good old fashioned continuous improvement methods to cut out as much waiting as possible.
Automated equipment reduces unit costs of container handling, but this reduction can be offset by the high upfront costs needed to install the equipment. A survey of automated port operators found that payback periods were most often 6 years or more, and some U.S. operators expected payback periods of 10 to 20 years. This makes automation risky if the expected future container volumes don’t materialize, and automation tends to be easiest to justify in very large ports with large container volumes.
Large volumes might also be needed for the productivity benefits of automation to materialize. APM Terminals stated in 2021 that its Maasvlakte 2 Terminal was too small to fully achieve the benefits from automation:
“The high degree of automation only comes into its own when large volumes can be rotated, and these are insufficient at this time. Sometimes, processes are still carried out manually, which should actually be automated. If the terminal is expanded, with the same staffing, more volume is processed, and productivity goes to the intended level.”
Other U.S. port productivity factors
In addition to the factors of scale, greenfield vs. brownfield sites, and work rules that make it harder for U.S. ports to take maximum advantage of automation (and to generally operate efficiently), there are other factors that drag down American port performance.
One factor is the type of work ports are doing. Most U.S. ports are “gateway” ports, where imports enter the country and exports leave via land-based travel like rail and trucks. By contrast, some ports that act as hubs for global trade do much more transhipment, where containers arrive on one ship and depart on another. Singapore, for instance, has one of the largest ports in the world, but very little of the cargo is Singaporean imports and exports.
Transhipment cargo tends to take less time to move, and ports that have a large fraction of transhipment will naturally have higher performance as measured by vessel waiting time. On the Container Port Performance Index, many of the top-performing ports, like Salalah, Cartagena, and Tanger-Med, are primarily transhipment ports. (Of course, the Jones Act makes it hard for the U.S. to take advantage of transhipment for domestic cargoes.) High transhipment fractions may also make it easier to adopt automated equipment, though experts seem to disagree about this.1
Another major performance factor is hours of operation. Top-performing ports tend to operate 24 hours a day, 7 days a week, whereas U.S. ports don’t operate around the clock.
The limited hours of operation relate to another potential issue, that of lack of coordination. As we noted, effective container handling requires all operations to be coordinated and synchronized, and there’s some evidence that American ports don’t coordinate their operations especially well. In Los Angeles and Long Beach, for instance, individual terminals have separate rail systems for moving cargo, and the systems don’t work together. Lack of coordination between truckers, shipyards, and companies that move containers also seems to be behind the failure of a program designed to help farmers ship out crops through the Port of Oakland. Historically, U.S. ports have lacked appointment systems for trucks to arrive and pick up cargo; instead trucks would simply arrive randomly, often creating large amounts of congestion as they waited to load and unload. And while U.S. ports seem to be adopting truck appointment systems, they don’t yet appear to be universal or completely coordinated (as of last year the ports of Los Angeles and Long Beach had several different appointment systems in place). During the post-pandemic cargo congestion at major ports, things like lack of available warehouse space made temporary 24/7 port operations less than successful. There are often shortages of truck chassis or truck drivers needed to move containers out of ports, and customs processes are often slow and not coordinated.
Another possible issue is infrastructure investment not keeping up with port container volumes, an issue highlighted in a 2015 Federal Maritime Commission Study. One example of this is insufficient dredging to handle larger container ships (a problem made worse by the Foreign Dredge Act, which prevents the use of foreign-built dredges). Most American ports can’t handle the very largest container ships. In 2021 a 24,000-TEU container ship needed to unload its cargo to a smaller ship at the Port of Long Beach, which then transferred its cargo ashore, a time-consuming operation required because the Bay was not deep enough to allow the larger ship to access the port.
Conclusion
Automation, at best, seems like a partial explanation of American port productivity problems. The U.S. is not necessarily all that far behind in automated equipment adoption, and it’s not as clear a win as some people seem to think. Plenty of automated ports (including American ones!) don’t operate particularly efficiently, and plenty of non-automated ports do.
Of course, this doesn’t mean that the union is correct to ban all automation going forward. Right now, automation is the worst that it will ever be. It will only get better and more capable, and banning it will hamstring port efficiencies in the future even if it doesn’t necessarily do it now. It’s hard to imagine how much poorer the U.S. (and the world) would be if unions had successfully fought off the introduction of the shipping container in the 1960s. We shouldn’t stop the introduction of new, productivity-enhancing technology, but we should also be realistic about what benefits it will actually be expected to yield.
If you’re interested in learning more about port automation, a recommended reading list of the best and most useful sources I found is available here for paid subscribers.
The ITF report claims that transhipment is hard to do with automation, while the GAO report says the opposite, and this METRANS report somehow seems to say both.
Great article. One thing that I learned from studying military logistics in World War II is that the key to port efficiency is how quickly they can get shipments out of the port. People tend to focus on how much cargo a port can accept, but the true gating factor is how much it can get out or discharge. Otherwise, all the cargo piles up in the ports getting in the way of all the other cargo.
It may be that the real cause of lower inefficiency in American ports is with the trucking and rail system not being able to discharge fast enough.
when I visited a Toyota plant in Japan I was surprised by how much of the emphasis was on improving human productivity rather than automating it away. so they had all sorts of gadgets for making sure people had the right tools at the right moment.