(note: all quotes are from Nemet’s How Solar Energy Became Cheap unless otherwise noted.)
Welcome to Part II of “How did Solar Power Get Cheap?” To recap Part I, the modern solar photovoltaic (PV) cell was invented at Bell Labs in 1954. Early markets were almost entirely satellites, followed by other remote power uses such as navigation buoys and offshore platforms. The US led the world in solar cell R&D until the mid-1980s, when a fall in energy prices caused interest in PV to wane and funding to be slashed. After this, the locus of solar PV development moved elsewhere - first to Japan, then Germany, then China.
Japan
Japan started manufacturing silicon PV cells very early. By 1961, seven years after Bell Labs had announced their “Solar Battery”, Japanese manufacturers Sharp, NEC, Sanyo, and Mitsubishi were all producing silicon PV cells. As in the US, early Japanese markets for solar PV were largely satellites and power for remote, inaccessible locations. Sharp began installing PV systems on navigational buoys and lighthouses as early as 1961, and by 1972 had installed more than 200 of them, including the largest solar PV system in the world for a lighthouse on Ogami Island in 1966. In 1976 the Japanese space program launched a satellite with solar cells made by Sharp, who would later become the sole supplier of PV cells for Japanese satellites.
As in the US, in Japan the 1970s energy crisis accelerated solar PV development. An island with few natural resources, Japan was (and is) highly vulnerable to disruptions in oil supply. Following the 1973 oil embargo, in 1974 Japan’s powerful Ministry of International Trade and Industry (MITI) [0] launched its “Sunshine Project”, with a goal of developing clean, local sources of energy by the year 2000. But whereas in the US solar PV had been comparatively minor, in Japan solar took center stage, with other sources such as geothermal and hydrogen being used as a hedge in case solar development didn’t pan out. More than 25% of Project Sunshine’s funding went to solar between 1974 and 1981, more than any other energy source except geothermal. The goal was for half of Japan’s electricity to be generated by solar PV by 1990, and two thirds by 1995. Unlike most MITI projects, which typically had to show a positive return in five years, solar development was given much more time - “If it took 25 years to develop inexpensive PV, that was acceptable since the issue of energy dependence was so important to the country.”
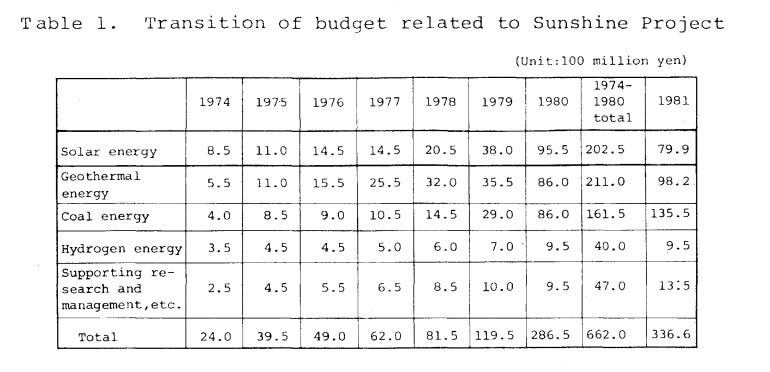
Beyond the funding provided by Project Sunshine, its high targets for PV electricity generation gave manufacturers confidence that large markets for PV would exist in the future, incentivizing them to make their own R&D investments.
Because solar PV was still too expensive to compete with grid power, Japan’s PV development in the 70s and 80s was largely focused on adapting the technology to consumer electronics. Sharp came out with its first solar PV calculator in the late 1970s, and by 1982 80% of Japanese PV production was going towards consumer electronics such as calculators and watches. By the early 1990s, consumer electronics had become the largest market segment for solar PV. MITI wasn’t thrilled by this, as their goal was for PV to provide utility scale power, but it was tolerated under the assumption that progress in consumer electronics PV would eventually spill over into utility-scale uses.
Solar PV for electronics was largely based on a different type of solar cell - amorphous silicon, a type of thin-film PV. Whereas traditionally solar cells were made from wafers of crystalline silicon, amorphous silicon used flexible sheets of unstructured silicon that were up to 100 times thinner than traditional wafers. Amorphous silicon PV cells were less efficient than crystalline PV cells, but required much less silicon, and eliminated several expensive manufacturing steps such as growing silicon crystals and slicing them into wafers. Because of this, it seemed likely that amorphous silicon PV would ultimately be cheaper than crystalline silicon PV on a cost per watt basis, and many Japanese manufacturers bet heavily on it. In the 1980s, 80% of Japan’s solar PV research was focused on amorphous silicon.
As in the US, in Japan interest in solar PV for large-scale electricity generation waned when energy prices collapsed in the mid-1980s. By 1990, just 0.008% of Japan’s electricity was provided by solar PV, nowhere close to the Project Sunshine goal of 50%. Oil consumption had fallen, but it had almost entirely been replaced by natural gas and nuclear power.
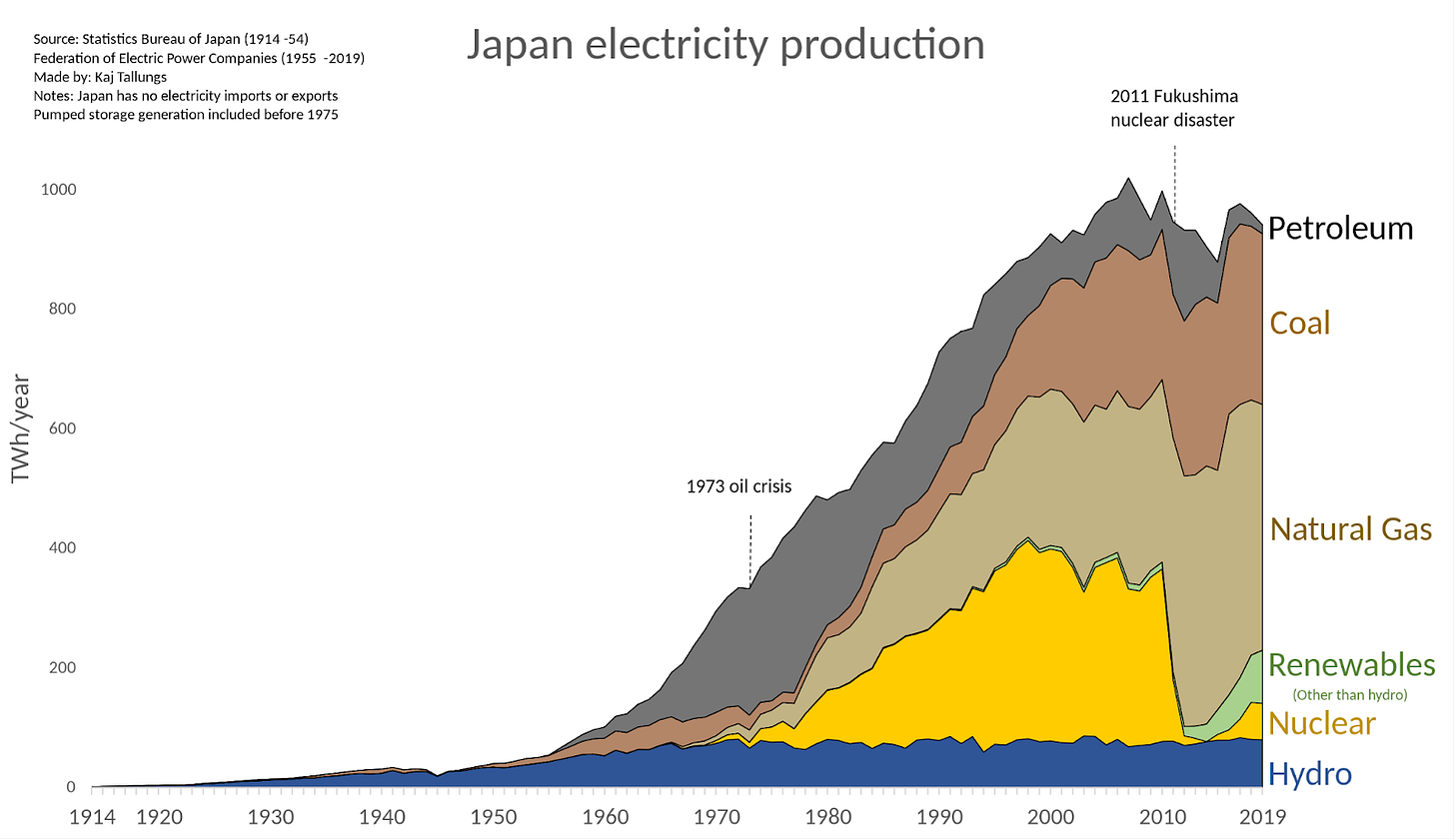
This began to change with a series of subsidy programs for rooftop solar. In 1993, MITI created a “700 roofs” program, where homeowners who installed solar PV systems on their roof would receive a rebate for 50% of the cost of the system (a percentage which fell over time) [1]. The program also simplified solar PV permitting, provided technical guidelines for connecting PV systems to the grid, and instituted a net metering policy which credited PV owners for the electricity they provided on their utility bills.
The popularity of the program caused MITI to continue and expand it. Rooftop PV installations under the program steadily grew, from 539 per year in 1994 to 54,475 per year in 2004. Between 1995 and 2005, solar PV generated electricity in Japan went from 106 gigawatt-hours to 1421 gigawatt-hours. Altogether, MITI spent the equivalent of $1.1 billion financing more than 200,000 rooftop PV installations. By 2000, rooftop PV systems were 50% of the solar PV market globally, and Japan had become the largest solar PV market in the world.
The explosion in the Japanese market also caused an explosion in Japanese solar PV manufacturing. Between 1994 and 2005, Sharp increased its solar PV production by a factor of 200. By 2003, Sharp was the largest solar PV manufacturer in the world, and had captured 30% of the market.
As output increased, PV cells, and the techniques for manufacturing them, continued to advance. Solar PV factories grew larger (average factory output increased by more than 100x between 1980 and 2001) enabling greater economies of scale. Modules got more efficient, going from 8% to 13% efficiency on average. Manufacturers switched from using round wafers cut from a single silicon crystal (monocrystalline panels) to square wafers made from many different crystals (polycrystalline panels), as well as using less pure silicon. Between 1980 and 2001, the cost of silicon for PV cells fell by over 80%. Manufacturers also found ways to use less of it. Silicon wafers also got larger during this period, resulting in larger cells and thus less assembly effort to make a module. Technologies such as wire saws for cutting the wafers (a technology adapted from the radial tire industry) and screen printing the metal contacts were introduced. As a result of these and other advances, between 1980 and 2005, the cost per watt of a solar PV panel fell by nearly 90%.
But Japan’s status as the world leader in solar PV would be short-lived. The rooftop subsidy program ended in 2005. Once dominant Japanese manufacturers increasingly had trouble competing with low-cost producers that were beginning to emerge in China. By 2007 Sharp’s share of the PV market had fallen to 10% and would continue to decline. And while thin-film PV continued to improve, and to be used for consumer electronics, crystalline PV improved faster, and remained (and remains today) the technology used for large-scale electricity generation. The Japanese manufacturers that had bet on amorphous silicon for utility-scale use had bet wrong.
But just as the Japanese PV market was cooling off, the German market was exploding.
From Japan to Germany
The clean energy movement in Germany began with the anti-nuclear movement of the 1960s and 1970s, and was catalyzed by the 1970s energy crisis and the 1986 Chernobyl nuclear accident. There was increasing advocacy for Germany to transition away both from nuclear energy and from fossil fuels. In the 1990s, German cities began to pass generous feed-in-tariffs for rooftop solar PV systems, which would compensate the owners for the amount of electricity they contributed to the grid, often at very generous rates. In 1992 for instance, the city of Aachen passed a PV feed-in-tariff equivalent to $1.30 per kilowatt-hour, roughly 20 times the retail electricity price at the time. Germany’s federal government also passed a feed-in law in 1991 which required utilities to purchase electricity from renewable sources at a rate that varied depending on the average price of electricity and the source of electricity. For wind and solar PV, it was 90% of the average electricity price for all customers [2].
These feed-in tariffs were largely based on the US’s experience with PURPA and California’s ISO4 standard contract, which together required utilities in California to purchase renewable-generated electricity from suppliers at what turned out to be very generous rates. The enormous explosion in wind power in California that followed gave German policymakers confidence that a similar policy would incentivize renewable energy projects in Germany.
These developments set the stage for an even more transformative German energy policy which today is known as Energiewende, a strategy aimed at transitioning Germany away from fossil fuels and nuclear energy. In 2000, a renewable energy law (known as EEG) was passed, which included feed-in-tariffs that varied based on the technology - for solar PV, they were roughly double the retail rate of electricity. Like the Japanese rooftop program, rates would decline over time as the cost of clean energy technologies fell. In 2004, the renewable energy laws were strengthened further - feed-in rates were raised, caps were removed, and a goal of 20% renewable energy by 2020 was set.
The 2000 and 2004 renewable energy laws created a gold rush in the German PV market. Between 2003 and 2004 solar PV installations in Germany quadrupled, and in 2004 Germany made up 60% of the worldwide solar PV market. By 2012 Germany was installing 7 gigawatts of solar PV a year, over 8 times what had been installed during the entire 11 years of the Japanese rooftop program, and by 2014 renewables were providing 27% of Germany electricity. Of the 66 gigawatts of solar PV installed globally between 2004 and 2011 (increasing worldwide capacity by a factor of 20), more than a third of it was installed in Germany. Between 2004 and 2012, Germany would spend over 200 billion euros subsidizing solar PV.
As in Japan, this resulted in an explosion of German PV manufacturers. In 2008, German PV output surpassed Japan’s, and German manufacturer Q-Cells was the largest PV manufacturer in the world.
Costs of solar PV continued to decline (though it plateaued for several years in 2005 due to a price spike in polysilicon), mostly via the same mechanisms as they had previously. Plants continued to get larger enabling greater economies of scale, cells continued to get more efficient, silicon wafers got larger and cheaper, and manufacturers found ways to use less silicon. Between 2001 and 2012, the cost per watt of solar PV fell another 75%.
Up through the 1990s, solar PV manufacturing largely used repurposed equipment from the semiconductor industry, and many steps in the process were done manually. But by the early 2000s, equipment manufacturers began to produce highly automated manufacturing equipment designed specifically for the PV industry, in some cases offering entire “turnkey” integrated PV fabrication lines. Because the requirements for solar PV were much less stringent than for semiconductors, the PV-specific equipment could often be made much larger, and produce panels much more cheaply than repurposed semiconductor equipment. Similarly, in the early 2000s lower quality polysilicon especially for the solar PV industry began to be manufactured. Before 2000, most polysilicon was used by the semiconductor industry. By 2012, 90% of it went to solar PV.
As with other countries, German leadership in solar PV wasn’t sustained. In 2012 the Feed-In-Tariff was phased out, and German solar PV installations collapsed. Q-Cells declared bankruptcy the same year [3]. But by then, China was already emerging as the world leader in solar PV production.
From Germany to China
China began to manufacture solar PV cells in the 1970s, for use on satellites and for remote military communications. By the 1990s, it was exporting a very small number of solar PV cells to Europe, but its share of the PV market was small. As late as 2003, less than 2% of solar PV cells worldwide were produced in China.
But the German market grew far faster than German, Japanese and US manufacturers could respond, and Chinese manufacturers stepped in to fill the gap. An early leader was Suntech, a solar PV firm started by Shi Zhengrong. Shi was a scientist who had researched solar PV at University of New South Wales, which at the time was setting records for solar PV cell efficiency. Shi was able to cobble together financing for a solar PV company, and in 2002 set up a 10 megawatt production line, adding a 30 megawatt production line the next year. When the German market exploded in 2004, so did Suntech’s sales. It IPOd on the New York Stock Exchange in 2005 (the first private company in China to do so), raising $400 million in funding). By 2009, Suntech had an annual production capacity of 1000 megawatts, and had become the largest PV manufacturer in the world.
Suntech’s success inspired followers. Whereas only a handful of firms were producing solar PV in China in 2000, by 2011 there were over 500 (Hopkins & Li 2016). Between 2008 and 2012 Chinese companies bought $30 billion worth of PV manufacturing equipment from European suppliers (they have since started producing their own PV manufacturing equipment). By 2008, China produced more solar PV than any other country, and by 2012 it was producing nearly 60% of the world's PV.
Initially, most of China’s solar PV was exported. As late as 2008, 98% of PV cells produced in China were sent overseas. But in response to increasing tariffs and the economic conditions of the Great Recession, China instituted measures to support its solar industry. A rooftop subsidy was created in 2009, and a 50% upfront subsidy for grid scale PV systems was in place between 2009 and 2013. In 2011, China launched its own Feed in tariff. China PV installations grew from 140 MW in 2008 to 3500 MW in 2012. By 2013, China had become the world's largest consumer of PV as well as the largest producer, a title it has held since.
As Chinese production capacity increased, the cost of solar PV continued to drop. Between 2009 and 2019 the cost of solar PV fell by 89%. By 2014, utility-scale installations became the primary market for solar PV.
Non-module costs
Today, roughly half the cost of utility scale solar PV electricity is from the costs other than the actual solar PV cell (in residential PV, it’s closer to 80%). This includes things like other hardware (support racks, inverters, wiring), the labor to install and maintain it, and so-called “soft costs” - permitting, land acquisition, overhead, etc. As the industry has grown, these non-module costs have fallen precipitously as well.
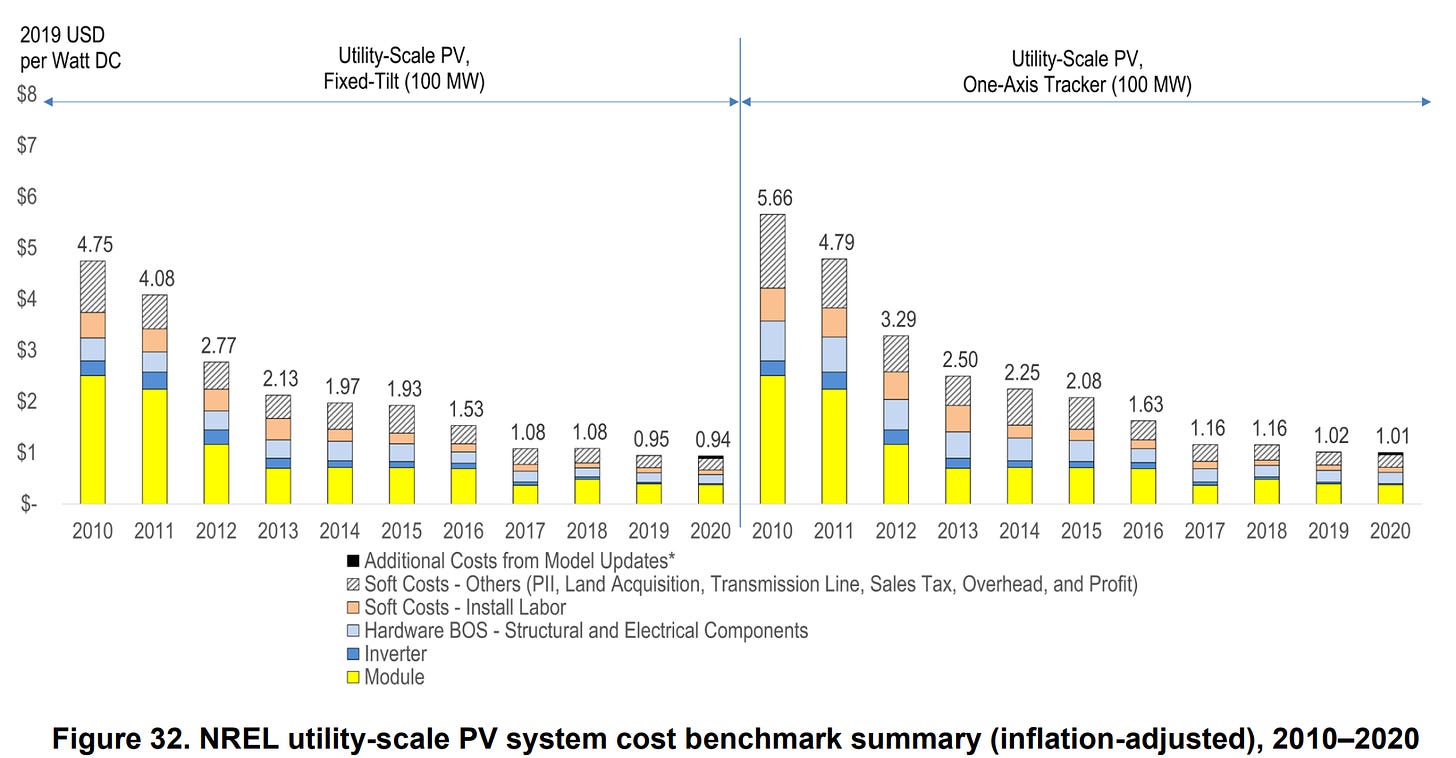
Inverters have gotten cheaper, smaller, and easier to replace. Installers have gotten more adept at installing modules and managing solar PV projects, and designing overall systems to be as cost effective as possible. PV systems have also gotten bigger over time, enabling economies of scale at the level of installation. Permitting bodies have gotten more familiar with solar PV projects. Financing costs have fallen as payback periods decline and as solar PV projects become more predictable and “bankable”.
Conclusion
The history of solar PV is a complicated story.
On the one hand, it shows the enormous potential of learning curve effects. Solar went from the most expensive source of electricity in the 1950s to the least expensive source of electricity in the 2020s. Solar PV had a learning rate (how much cost declines for every doubling of capacity) higher than any other energy technology. As costs fell, the potential uses for it grew. As uses grew, output increased, which caused prices to fall further, in a virtuous cycle that continues today. Without the enormous cost declines of solar PV, it’s hard to imagine getting anywhere near net zero electricity generation.
This virtuous cycle was aided by the fact that solar PV had a huge number of advantages.
PV works at any scale, from milliwatt cells on electronic watches to utility scale installations billions of times larger.
Likewise, it can successfully operate in a wide variety of environments - deserts, oceans, outer space, etc.
It has no moving parts, requires no fuel, and has no byproducts, making it inherently reliable and low maintenance.
Because generating solar PV electricity requires the repetitive construction of large numbers of nearly-identical modules, it has unusually strong learning curve effects.
It was for many years able to piggyback on developments in semiconductor manufacturing.
These gave solar PV huge tailwinds - its costs fell unusually quickly, and it had a wide variety of niche uses it could expand into before needing to compete with utility-scale generation.
But despite these benefits, getting solar PV competitive with grid-scale electricity took many decades, and required hundreds of billions of dollars of both public and private investment that no one firm, no one country could fund alone.
Solar PV shows the power of learning curve effects, but it's also an illustration of how difficult it can be to disrupt a mature, entrenched technology.
Sources
Gregory Nemet - How solar energy became cheap
Gregory Nemet - Beyond the learning curve: factors influencing cost reductions in photovoltaics
Gregory Nemet - Characteristics of low-priced solar PV systems in the U.S
Kavlak et al - Evaluating the causes of cost reduction in photovoltaic modules
Hopkins and Li - The Rise of the Chinese Solar Photovoltaic Industry (in “China as an Innovation Nation”)
Martin Green - Silicon Photovoltaic Modules: A Brief History of the First 50 Years
Footnotes
[0] - As an example of the power of MITI, prior to the late 1960s and early 1970s, “no technology entered the country without MITI’s approval; no joint venture was ever agreed to without MITI’s scrutiny and frequent alteration of the terms; no patent rights were ever bought without MITI’s pressurizing the seller to lower the royalties or to make other changes advantageous to Japanese industry as a whole; and no program for the importation of foreign technology was ever approved until MITI and its various advisory committees had agreed that the time was right and that the industry involved was scheduled or “nurturing” - MITI and the Japanese Miracle
[1] - Slowly decreasing rebate values was a policy innovation that would later be adopted by other countries, such as Germany.
[2] - This is described as a very generous policy for reasons which are unclear to me.
[3] - It has since been revived as a Korean company
There's a big issue with this analysis. Namely, it uses levelized cost of electricity, which bakes very aggressive assumptions about time preference into its calculation while glossing over quality issues related to solar power. When this is your standard, solar overperforms its actual performance in reality. After all, you can throw up a solar farm in a relatively short timespan, especially with regulators largely leaving solar projects alone. Compare this to, say, a nuclear plant which will take years to build even if it doesn't get tied up in regulations for decades. By LCOE, the nuclear plant will fare much worse. In some sense, it should. After all, nuclear plants have loans which accumulate interest while the plant is under construction/fighting red tape.
But... look, your background is in architecture, so imagine I started talking about a revolutionary new technology which, under my Levelized Cost Of Shelter framework was vastly cheaper than conventional construction. I take you out to a demonstration site where I... pitch a perfectly normal tent. This is a very tight analogy, you can pitch a tent in a few hours, rarely need to deal with regulation, etc. But anyone who's been on a bad camping trip will tell you that no, tents aren't actually relevantly analogous to houses. In the energy context, nuclear (and coal, and LNG, and...) have properties (constant flows of energy, supply scalability which is responsive to demand, no need for battery-based energy storage infrastructure) which are hidden by a simple LCOE comparison. If you look at another framework, like energy return on energy invested, solar is actually not very cost-competitive with fossil fuels and nuclear. That's why, virtually everywhere they're widely deployed, renewables energy systems need to be supplemented with fossil fuels on pain of brownouts and blackouts.
So, before we ask "how did solar power get so cheap?" we should ask "did solar power get so cheap?" By at least one measurement which is in many ways more reasonable than LCOE, it didn't.
Do you have any thoughts on the claims that LCOE measures substantially undercount the costs of solar (and wind) due to the direct and indirect (ie grid) effects of intermittency?