It’s no secret that the Allies won World War II on the back of the U.S.’s enormous industrial output. Even before the U.S. entered the war, the Americans provided hundreds of millions of dollars’ worth of equipment to the Allies, and between 1938 and 1943 U.S. manufacturing output tripled as production of munitions ramped up. Over the course of the war the U.S. produced around 5,600 cargo ships, 80,000 landing craft, 2.4 million trucks, 2.6 million machine guns, and 41 billion rounds of ammunition.
One of the most important elements in the “Arsenal of Democracy” was aircraft. Over the course of the war the U.S. produced around 325,000 airplanes valued at roughly $46 billion ($800 billion in 2024 dollars). Not only is this more aircraft than what Germany, Japan, and Italy combined produced during the war — it’s also more aircraft than have been built for commercial transport in the entire history of aviation.1
Creating an aircraft industry capable of producing planes by the hundreds of thousands didn’t happen overnight, and on the eve of the war the industry was a tiny fraction of what it would grow into. In 1937 the U.S. produced around 3,100 aircraft, most of which were small private planes. Prior to the war the value of aircraft made in the U.S. was about one-fourth the value of cans produced, and just 3.5% of the value of cars produced. Despite the continuing escalation of the war in Europe, the U.S. was reluctant to prepare for large-scale mobilization. Existing mobilization plans assumed that any future war would be smaller in scale than World War I had been, and that only half of the already-small existing aircraft manufacturing capacity would be devoted to war production. As late as 1940 the U.S. military had just 2,665 aircraft, around a tenth of what Germany’s Luftwaffe fielded. And the aircraft the U.S. did have were out of date: Though the airplane was invented in the U.S. in 1903, by the late 1930s the most advanced aircraft were being produced in other countries, and there was little urgency to close this gap. Military orders for Boeing’s advanced B-17, of which more than 12,000 would ultimately be built, were canceled in 1937 after a crash during testing in favor of the cheaper and less capable B-18, nearly driving Boeing into bankruptcy.
Producing the aircraft needed to win the war required a complete transformation of the aircraft industry. Between 1939 and 1944, the value of aircraft produced annually in the U.S. increased by a factor of 70, and the total weight of aircraft produced (a common measure of aircraft industry output) increased by a factor of 64. In 1940, the airframe industry employed just 59,000 people; three years later that reached 939,000, with another 339,000 building aircraft engines. Factories of unprecedented size, enclosing millions of square feet were built; by the end of the war aircraft engine factory floor space had increased from 1.7 million square feet to 75 million, and a single large engine factory encompassed more space than had been used by the entire pre-war engine industry.
Not only did the aircraft industry grow in size, but it also adopted entirely novel methods of production, modifying mass-production methods used in cars and other products for the needs of aircraft manufacturing. And while it seems rapid in hindsight, in fact the process took years. In part because the U.S. government and the aircraft industry were unprepared for the requirements of large-volume production, and in part because developing new aircraft and scaling up manufacturing were difficult and time-consuming activities that could only be accelerated so much, even in an emergency. Had conditions been slightly different — if Britain and France hadn’t kickstarted the industry with enormous aircraft orders, or if people like GM President Bill Knudsen hadn’t pushed for early industrial mobilization — the outcome might have been very different.
Takeoff
The first push to grow the U.S. aircraft industry came well before the U.S. entered the war. Desperate for more planes to counter Hitler’s territorial ambitions, both Britain and France placed large orders with U.S. aircraft manufacturers in 1938 and 1939. In 1938 Britain placed an order for up to 250 of Lockheed’s Hudson bombers, worth $25 million.2 The order, then the largest order ever received by a U.S. aircraft manufacturer, was several times Lockheed’s annual revenues of $2-3 million, and Lockheed quickly doubled its workforce to fulfill it. Engine manufacturer Pratt & Whitney was rescued from the brink of bankruptcy by a French order for engines worth $2 million in 1938, followed by an even larger order worth $85 million in 1939. North American Aviation grew from 150 employees in 1935 to 3,400 employees in 1939, partly due to British orders for its AT-6 “Texan” training aircraft.
By 1940 Britain and France had together ordered more than 6,000 planes from U.S. manufacturers for roughly $573 million ($12.8B in 2024 dollars), or around seven times what the U.S. aircraft industry produced in 1936 by dollar value. This allowed U.S. aircraft manufacturers to greatly expand their workforces, and industry employment tripled between 1938 and 1940. The orders also enabled manufacturers to build new, larger factories. French upfront payments allowed Pratt & Whitney to build a new facility at its Connecticut factory (dubbed “the French Wing”) which doubled its floor space, and a similar French investment allowed Wright to triple its factory space. Altogether, by 1940 the British and French had invested $72 million ($1.6B in 2024 dollars) in U.S. aircraft factories, estimated to have sped up the process of scaling up aircraft production by a year.
The next great push for aircraft production came in 1940, after Germany invaded western Europe. On April 9th Germany invaded Norway and Denmark, and on May 10th Germany invaded Belgium, Luxembourg, the Netherlands, and France. On May 16th Roosevelt asked Congress for $1.2 billion in additional defense funding ($26.8B in 2024 dollars) and called for the U.S. to build 50,000 aircraft a year, roughly as many aircraft as the U.S. industry had produced in the entire history of aviation to that point. This was 25 times what had been built in 1939, and more than eight times existing aircraft expansion plans. By July Congress had authorized funds to build 24,000 aircraft, and over the next year Congress appropriated $12 billion in total defense spending, roughly 10 times what the U.S. had spent annually in the 1930s. By 1941, while not planning on building 50,000 aircraft a year (a number Roosevelt had seemingly selected out of thin air), plans were in motion to expand U.S. air forces to more than 63,000 aircraft by 1944, as well as to continue supplying Allied nations with aircraft. A 1934 law, which prevented the U.S. from extending credit to countries that had defaulted on their WWI debt, threatened to derail further foreign sales. But in 1941 the U.S. passed the Lend-Lease Act, which authorized $7 billion ($149 billion in 2024 dollars) to supply Allied nations with supplies and military equipment, including aircraft.
After Japan attacked Pearl Harbor in December 1941 and the U.S. formally entered the war, Roosevelt raised aircraft production targets again, to 60,000 aircraft in 1942 and 125,000 aircraft in 1943. Though many doubted these production levels could be achieved, (and indeed, they weren’t), they nevertheless became the targets the U.S. aimed to hit.
Building the factories
Initially it was hoped that aircraft manufacturers would be able to build the factories needed themselves, and several measures were taken to try to reduce the burdens of plant construction. The Vinson-Trammell Act limited profits on government contracts to just 12% (later reduced to 8%), and required an extensive audit of the contract to ensure the profits were correct prior to production beginning. This Act was suspended, and nearly every aircraft contract during the war was structured as cost plus fixed fee (ultimately resulting in low, single-digit profits for the aircraft manufacturers). And the allowable tax amortization period for new factories was reduced from 20 years to 5 years to reduce the financial burden of new, large factories that might only be needed briefly. While these measures were being debated in Congress, aircraft procurement slowed to a standstill: 100 days after Roosevelt’s demand for 50,000 airplanes and congressional funding of $400 million worth of aircraft, just 343 aircraft had been ordered.
It was soon realized that the scale of expansion required was far too much for the existing industry to finance (in part because banks were reluctant to provide loans), and ultimately most new aircraft factories were built by the government as GOCO (government-owned, contractor-operated) facilities. While some factories were built by the War and Navy Departments directly, much of the expansion was financed by the Defense Plant Corporation (DPC), the brainchild of Bill Knudsen, who had left his job as president of General Motors at the request of President Roosevelt to work for free helping U.S. industrial mobilization. North American Aviation, for instance, used DPC financing to construct a new factory in Dallas, and DPC leased the company machine tools to expand its Los Angeles factory. Thanks in part to DPC financing, by the time of the attack on Pearl Harbor, North American had expanded from 3,400 to 23,000 employees, and had enlarged its factory space by a factor of six.
The DPC was a subsidiary of the Reconstruction Finance Corporation, a government-owned corporation formed during the Great Depression to provide emergency lending for businesses, and in the years since had become the government’s “biggest bailout machine, infrastructure bank, and multipurpose source of credit and finance.” As a result of government funding the industry’s expansion, by the end of the war the federal government owned roughly 90% of the aircraft manufacturing capacity in the U.S.
Many of the new plants were built in the Midwest, both because it would be easier to find workers and to keep the factories out of reach of enemy attack. To build the plants quickly and minimize the use of critical materials, novel construction methods were often used. A factory for Chrysler was redesigned to use reinforced concrete instead of steel, and constructed using movable rolling forms known as “Trojan Horses,” where concrete would be poured, set, and then the forms rolled into the next position. Some factories were built in as little as 30 days.
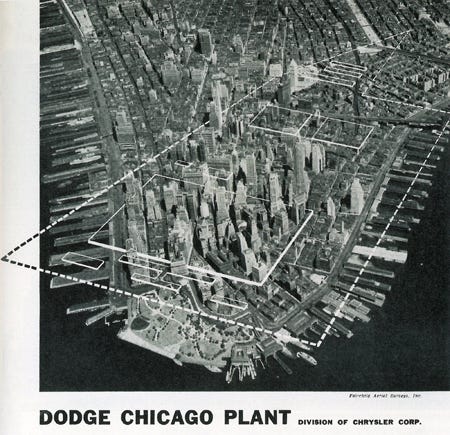
Many of these factories were designed by Albert Kahn, the famous industrial architect responsible for the design of Ford’s enormous Rouge Facility. Over the course of the war Kahn’s firm designed nearly 100 million square feet of factory space. Kahn favored large, single-story factory buildings with wide bays to maximize the flow of material through the factories and minimize interruptions. To accommodate the thousands of factory workers while still allowing material to flow smoothly, many of Kahn’s factories were designed to have locker rooms, cafeterias, and other worker services in the basement of the factory below the production floor. Workers would enter the factory from below and then climb stairs to their work area, minimizing the need to cross the production floor and interrupt material travel paths.
Roosevelt’s production targets were far greater than what the existing aircraft industry could handle, even after they greatly expanded their workforces, and manufacturers in a variety of different industries ultimately contributed to wartime aircraft manufacturing. Final assembly of aircraft themselves mostly remained the purview of existing aircraft manufacturers scaling up their operations, though several different manufacturers produced the same aircraft (Boeing’s B-17, for instance, was also made by Douglas and Lockheed). Ford was the only non-aircraft manufacturer that delivered fully assembled aircraft in any appreciable quantity, building roughly 6,800 aircraft during the war.
But for aircraft parts and subassemblies, manufacturers outside the aircraft industry were used heavily as subcontractors and licensees. Car manufacturers like Studebaker built aircraft engines, and appliance manufacturers Nash-Kelvinator and Frigidaire built airplane propellers. Chrysler built a variety of aircraft components including engines, nose sections, and wing edges for the B-29 and cockpit enclosures for the B-17. Roughly half of the weight of aircraft produced during the war was produced by subcontractors and licensees, compared to about 10% in 1940. The car industry alone produced about 56% of the more than 800,000 aircraft engines built during the war.
Expanding aircraft manufacturing also required scaling up manufacturing in related industries. Thousands of aircraft required millions of tons of aluminum (e.g., a single B-17 used about 10 tons of aluminum), and between 1940 and 1943 aluminum manufacturing capacity more than quadrupled thanks to DPC financing. The aircraft also created an enormous demand for aviation gasoline, and refiners spent nearly a billion dollars of their own money (roughly half of what was spent on the Manhattan Project) to expand aviation gas refining capacity. And the aircraft industry was just one of many industries demanding huge quantities of machine tools, and during the war annual production of machine tools increased by a factor of 50.
Challenges of production
Prior to the war, aircraft were produced using small scale, job-shop type manufacturing methods: Individual aircraft were assembled in place piece by piece, largely by hand, not unlike the way cars had been built prior to Ford’s Model T. It was a slow, expensive, and labor-intensive process: On a per-pound basis, it cost about 30 to 40 times as much to build an aircraft than it did a car. And while the auto industry produced 1,500 times the number of cars as the aircraft industry did planes, it did so with just eight times as many workers. In other words, it took almost 200 times as many workers to build an aircraft as it did a car.
In part this was due to the comparatively small volumes of aircraft being built, which precluded the use of capital-intensive manufacturing methods with high upfront costs but low unit costs. But it was also due to the unique challenges of aircraft themselves, which made adopting efficient mass production methods difficult. For one, aircraft were far more complex than other mass-produced goods. While a car had around 5,000 parts, a B-25 bomber had around 165,000, not including the tens of thousands of parts in the engines, instruments, and other equipment, or the 150,000 rivets needed to stitch the plane together. And the performance requirements for aircraft were much higher: An aircraft piston engine, for instance, was much more powerful, much lighter per horsepower, and was pushed much harder than a car engine. A 1930s-era Ford V8 could generate about 85 horsepower, while aircraft engines generated 1,000 to 2,000 horsepower, and a car engine weighed about 6.9 pounds for every horsepower it generated, compared to 1 to 2 pounds for an aircraft engine. And while a car engine rarely exceeded 22% of its maximum power, an aircraft engine regularly ran at maximum power, or even above maximum power.
This meant that aircraft manufacturing had much tighter production tolerances than car manufacturing, and much more machining was required to make parts as light as possible. It also meant using lightweight materials like aluminum sheets and magnesium castings that other manufacturers had limited experience using. Meeting these strict tolerances required greater control over the production environment: Aircraft engine factories were air conditioned to minimize heat fluctuations and kept at constant 50% humidity to minimize surface rust.
Ensuring aircraft would meet their demanding performance standards also required much more inspection than other types of manufacturing. An aircraft engine and its constituent parts might undergo 70,000 inspections during the manufacturing process. When Ford engineers visited a Pratt & Whitney factory to learn about aircraft engine manufacturing, they initially thought the job “looked easy” and that the quality and precision requirements were excessive, but as they studied the engines, their performance requirements, and the need for reliability, they changed their minds. At a Ford aircraft engine plant that eventually employed around 15,500 workers, 3,000 of them were inspectors.
Aircraft were also designed and built differently than other mass-produced goods. With most products, parts are heavy and rigid enough that assembly can be done by simply holding them together and fastening them. But aircraft were built from thin sheets of aluminum bent into complex curves, and “mating surfaces,” areas where parts overlap and can be attached, were much smaller. Defining these curves couldn't be done with normal dimensioned drawings, and an elaborate process called “lofting” was used where contours were defined by taking a section of the airplane at uniform spacing, using those contours to build a steel skeleton, and using that skeleton to create a plaster mockup that could be used to create tooling. And during assembly, aircraft required large, elaborate workholding devices to keep the sheets of aluminum aligned in their proper shape as they were fastened together.
The unique characteristics of aircraft manufacturing meant that new tooling was required not only for existing aircraft manufacturers (to speed up and mechanize their processes), but it was also needed for manufacturers outside the industry already using mass-production methods. When Ford built a facility to manufacture Pratt & Whitney engines at its Rouge plant, its existing tools were only suitable for 10% of the tools needed; the other 90% had to be built new.
In addition to the new tooling required, existing aircraft drawings were completely unsuitable for large-volume production. Small-volume, job-shop type manufacturing meant that aircraft drawings and production control systems — the system for telling the factory what it should build and when — could be somewhat informal, with much of the critical information kept in factory foremen’s heads. Aircraft designs were often updated by changing factory tooling and templates, without updating the actual drawings, and drawings were often found to be inconsistent. Drawings were also often missing critical information, such as manufacturing tolerances, on the assumption that skilled workers would be able to fill in the blanks.
Even the seemingly simple task of assembling a complete set of drawings and parts list for an aircraft to be built proved monumentally difficult. When Ford first began work to produce the B-24, it found that drawings only existed for about 80% of the aircraft, and the ones that did exist had numerous inconsistencies. Ford ultimately redid the entire set of drawings, turning the original 7,500 drawings into more than 20,000 that could be more easily understood by workers inexperienced in aircraft manufacturing. Similar efforts were required by nearly every airframe manufacturer as they scaled up operations and transferred their designs to other companies.
One of the reasons for this poor state of production control, and another difference between aircraft manufacturing and other types of manufacturing, was that aircraft designs were constantly changing. With conventional manufacturing, design of the factory took place once designs were “frozen” and no more major changes to the design would take place. Mass-production factories achieved their high efficiencies by having carefully arranged and timed flows of material, which would be disrupted by major design changes that might require new tools, different parts, and changed material routing.
But while attempts were made to “freeze” aircraft designs to make manufacturing easier, ultimately this proved infeasible. Designs had to be constantly improved to address deficiencies, improve performance, and deliver aircraft that were capable of overcoming the enemy. Engines were upgraded to be more powerful, parts that were found to fail frequently were redesigned, and new guns and other equipment was installed.
The P-47 Thunderbolt, for instance, of which more than 15,000 were made, went through five major design revisions (the P-47B, C, D, G, M, and N) and numerous smaller updates. The P-47C had, among other things, a redesigned rudder to prevent failures, the P-47D added more cockpit armor, the M added a new, more powerful engine, and the N had longer wings which held more fuel. Making these improvements required numerous individual changes. Flight testing of the B-29 resulted in 900 design changes before it even began large-scale production. When Chrysler manufactured the Cyclone engine for Pratt & Whitney it had to incorporate more than 6,000 changes over the course of the war, resulting in nearly 50,000 separate change orders. North American’s B-25 first flew in 1940, but over the next five years the company spent roughly two million engineering hours redesigning the aircraft and incorporating changes.
To balance the need for high-volume production with the need for constant aircraft improvements, the industry adopted an awkward, stopgap measure: the modification center. After leaving the factory, aircraft were flown to another facility that would make the necessary changes.; recent design changes would be incorporated, and any mission-specific customizations would be added. Modification centers were first used in Britain to modify arriving U.S.-built aircraft for British needs, but eventually became widely used in the U.S. to cope with the flood of aircraft changes. Ultimately there were 20 modification centers built in the U.S., and anywhere from 25 to 50% of the labor spent building military aircraft during the war was spent at the modification centers. In part this figure is so high because the work done at modification centers was incredibly inefficient. Not only was it difficult to do work on a completed aircraft, but the modification centers were also often just open, outdoor spaces with tarps covering the cockpit to provide a makeshift working area. A part installation that could be done in minutes in a factory might take hundreds of hours at a modification center. In one case, 8,000 man-hours were spent modifying an aircraft that had only taken 9,000 hours to build in the first place.
As manufacturing scaled up, aircraft builders had to constantly address bottlenecks that were slowing down production, and as time went on these bottlenecks shifted. Early on the main problem was simply the lack of factories and machine tools to produce the necessary aircraft. As more factories came online, the problem became one of finding sufficient material: The huge increase in output and the fact that manufacturers were incentivized to hoard materials created constant shortages. And finally, the primary bottleneck became finding enough labor to fill the factories. Not only did the aircraft industry need to hire a huge number of workers, but so did every other major war industry, made worse by the fact that the workers they did have were constantly being drafted or volunteering for service.
The biggest source of untapped labor proved to be women. Though aircraft manufacturers were initially reluctant to hire women, women eventually made up roughly 40% of the aircraft labor force, and in some plants were as high as 90%. But using large numbers of female workers required completely redesigning the production process. Not only were women typically inexperienced in aircraft factory work (as were most male new workers recruited), but they also weren’t as physically strong as men.
To accommodate inexperienced female factory workers, a variety of changes were implemented. Processes were broken down into simple steps that unskilled workers could do. Part tolerances were relaxed where possible. Tasks were rearranged to be less physically taxing, and aids like trunnion jigs, which parts could be mounted to and freely rotated, were more widely adopted. Tools were redesigned to make them easier to use. Rivet guns, for instance, were redesigned to have counterbalances, which not only reduced the strength required to use them but made it possible to rivet with a single worker where it had previously required two. These redesigns not only made it possible to use women and other unskilled laborers, but also simplified and streamlined the production process — factory managers realized that if a women could do a job swiftly and easily, a man could too, and “practically every job in the catalog was revolutionized.”
More generally, though the complexities of aircraft manufacturing meant that mass production methods couldn’t be adopted directly, high-volume production did require a transition from job-shop methods to “line” or flow production, where material moved along a production line, smoothly and steadily being transformed into a finished aircraft. Not only was this more efficient at high production volumes, but previous job-shop methods required a highly-skilled labor force that wasn’t available. The pool of labor available — unskilled workers with no experience in aircraft manufacturing — in a very real sense “chose” the production system.
In addition to changes in shop floor work, expansion forced aircraft industry management to change. In 1935, the five largest aircraft manufacturers employed an average of 1,400 employees each. By 1943, that had ballooned to 100,000 each. Accommodating this required adding many new layers of management, and executives who had previously spent much of their time on the factory floor now found themselves spending most of their time in meetings, or dealing with the endless amounts of paperwork that the government required. Many managers failed to make the transition.
Making these changes inevitably took time: Nearly every aircraft produced during the war took more than a year to go from the 5th aircraft produced to the 500th aircraft produced. Even manufacturers familiar with mass production methods took time to ramp up. Despite the enormous amount of attention given to Ford’s Willow Run factory that mass-produced B-24 bombers, its performance was mediocre at best. For the first two years the plant produced virtually nothing as it struggled with the difficulties of aircraft production, and the time it took to reach volume production was slower than many existing aircraft manufacturers. At one point operations were going so poorly that the government considered taking over the factory). And while the factory eventually worked out its issues and produced aircraft in large volumes with impressively low labor inputs, by the time it did so it was too late: The army no longer needed B-24s — what it needed were the larger, longer-range B-29s.
And ramping up volume manufacturing for new aircraft models could only take place after a long period of testing and development. Most aircraft the U.S. fielded during the war took two to three years between when design started and the 5th aircraft was produced. Nearly every aircraft the U.S. produced in large numbers during the war started design work before June 1940, more than a year before Japan attacked Pearl Harbor.
Figuring out a novel manufacturing system capable of producing aircraft in large volumes also meant that the first aircraft were built incredibly inefficiently. Though much attention is given to the incredible increase in production efficiency that occurred during the war for things like Liberty Ships, in large part the efficiency gains were so great because the starting point was so bad: manufacturers were producing things they had never built before, using production methods they didn’t understand. (Indeed, despite the improvements, U.S. manufacturing productivity was lower at the end of the war than it was in 1941).
But manufacturers quickly improved. The job-shop methods of aircraft manufacturing were replaced with line production: Manufacturers installed conveyors and monorails to quickly move material through the factory, and new factories were designed and built with line production in mind to maximize material flow. Work was more finely divided into individual subassemblies to allow increased subcontracting and to have many different people working on portions of the aircraft simultaneously. Manufacturers adopted new, improved high-accuracy machine tools that could automate work and be operated by unskilled labor. Some manufacturers adopted transfer machines, an innovation from the auto industry that combined many separate machines into one, automatically moving material to different steps in the production process. The aircraft themselves were redesigned to be easier to manufacture, and novel production processes (such as centrifugal casting, hydroforming, and the Guerin process) were developed or more widely adopted to speed up work. Novel inspection methods, such as radiographic inspection, were also developed. Better tools and workholding systems were developed, tasks were redesigned, and material routing along the factory floor was improved to reduce travel distances. Production and material control systems were improved, eventually making it possible to incorporate major design changes on the factory floor and eliminate the need for modification centers. Standardized procedures for things like quality control were developed, and best practices were shared between different manufacturers.
As a result of these improvements, the time it took to build an aircraft steadily fell as manufacturers advanced along the learning curve. In 1941 Boeing required more than 140,000 hours of labor to assemble a B-17. By 1944, that had fallen to less than 20,000. The cost to produce aircraft fell on average by 32% over the course of the war.
Production system winds down
As late as 1941, the U.K. was building more planes per year than the U.S. But by 1942, the U.S. was building roughly as many aircraft as Germany, Japan, the U.K. and Italy combined. And by 1944, U.S. aircraft production was so voluminous that the Army and Navy were having trouble dealing with them all. Not wanting to shut down the plants for fear of losing the expertise contained within them, the U.S. simply began to dispose of old planes to make way for new ones.
As a measure of the industrial might of the United States in 1944 and 1945, the subsequent whirl of destruction told a better story than a thousand pages of statistics. If a plane needed minor repairs, it was pulled off the flight line and junked, and a shiny new replacement unit flew in to take its place. Hundreds of airplanes were flown into remote Pacific island airstrips, parked in a vacant clearing, and abandoned. Many such aircraft “boneyards” were later used for target practice by U.S. bombers on training missions. Scrapped airplanes were bulldozed into pits, and the wreckage compacted by running tanks over them. Marginally damaged carrier planes were pushed off the flight decks into the sea, and new replacement units flown in from escort carriers. This mass-junking of perfectly serviceable warplanes occurred at the height of the war, when the Japanese were falling well short of aircraft production targets and struggling to keep their assembly lines in operation at all. - Twilight of the Gods
By the end of the war, some aircraft were being flown directly from the factory to junkyards for scrap.
When the war ended, this enormous production machine was dismantled. Tens of thousands of excess aircraft were flown to boneyards and left to rot. The enormous aircraft plants built at government expense were far larger than the aircraft industry needed outside of wartime, and few manufacturers wanted them. Plants were sold off by the government, often at a tiny fraction of what it cost to build them, and repurposed for a variety of endeavors. Some became airports, like the Douglas factory that eventually became O’Hare. Others were used for car manufacturing: Ford’s Willow Run factory was sold to Henry Kaiser for his Kaiser-Frazer automobile company, and the failed Tucker and Playboy Motors also set up shop in former aircraft factories. What had been the largest factory in the world, the Dodge Chicago aircraft plant was used to briefly produce a factory-built house, the Lustron Home.3
A similar fate befell much of the tooling used to build the aircraft. The tools, jigs, and fixtures were often specific to certain aircraft and couldn’t be repurposed, and the machinery was often only useful for high-volume production. It too, was scrapped.
Conclusion
Looking back 70 years later, U.S. aircraft manufacturing during WWII looks like an unqualified success. The U.S. turned itself from a tiny producer of aircraft to manufacturing an unending, overwhelming stream of planes that proved critical to the war effort.
But this success was highly contingent. The U.S. was woefully unprepared to expand its aircraft industry. The U.S. didn’t have the proper aircraft developed going into the war, and the medium and heavy bombers that proved crucial to victory couldn’t be produced in large numbers until relatively late in the war. Neither the government nor the industry had the organizational infrastructure in place to handle the scale up, or plans for creating it: Most army mobilization plans implicitly assumed that industrial mobilization was like flipping a switch, and that on “M-Day” the industry would immediately switch to wartime production.
But scaling up an industry doesn’t work like that. It wasn’t until 1942, three years after Germany invaded Poland and France and Britain declared war on Germany in response, that U.S. aircraft production truly ramped up, and even this was only possible because of enormous early orders from Britain and France, and the work of far-sighted folks like Bill Knudsen who knew how long it took to scale up manufacturing operations. Had events occurred slightly differently, the outcome of the aircraft industry scale-up, and perhaps the war itself, might have looked very different.
World War II aircraft production shows that it's possible for a complex manufacturing industry to grow incredibly rapidly. But it also shows the limits of that scale up; that even in an emergency some things can only be accelerated so much, and success depends on what preparations have been taken beforehand.
For the last 25 years commercial jet deliveries have been on the order of 1,000 per year, which make up the majority of commercial aircraft. Deliveries in the second half of the 20th century were even lower, and while I couldn’t find data on earlier commercial aircraft production, prior to the invention of the jet passenger air travel was less popular, and most commercial aircraft like the DC-3 only had a few hundred built. Note that “commercial transport” does not include private planes (Cessnas, etc.)
There is some inconsistency in the numbers here. Destructive Creation says $17 million, Climb to Greatness says $25 million.
Similar efforts took place in Britain, where aircraft factories were used to produce the aluminum Airoh house.
Great piece with a very high signal / noise ratio.
Also very very glad Knudsen gets his dues. I would put him right up there as one of the most impactful US immigrants in history, at least as it relates to progress and industry.
I think the near monopoly US industry had on mass manufacturing before WW2 is worth calling out. Ford and GM (with Knudsen a key player) were the absolute titans of industry from the mid 1910s through the start of the war.
Could the US have ramped aircraft production (and engine assembly) as quickly if not for the knowledge, process (like transfer machines as mentioned) and talent spillovers from the auto industry?
Neither Japan or Germany had anywhere close to the volume of auto production prior to WW2 either.
This article is quite interesting and mostly (but not entirely) correct so far as I can tell, it is regrettable that it is so coy about sources in many cases. Many important assertions are entirely unsourced while for others the citations will be to cryptic for most readers.
One important cryptic source is, more fully, _Buying Aircraft: Matériel Procurement for the Army Air Forces_ by I. B. Holley (1964). As it is one of the U.S. Army's outstanding "Green Book" series of World War II histories it is not only still in print but available online in PDF at https://history.army.mil/html/books/011/11-2/CMH_Pub_11-2.pdf .
Much more difficult to find, unfortunately, is _Problems of Accelerating Aircraft Production During World War II_ by Tom Lilley, et al.