When trying to think of how construction might be improved, I’ve often reached for a car manufacturing analogy. Cars are large, complex objects that improvements in production methods made vastly cheaper, and most folks start with a lot of preexisting knowledge about them, making them a useful point of comparison. (It’s not just me who does this - car analogies were a basic talking point at Katerra, for instance.) I’ve occasionally used other manufacturing analogies, but car manufacturing has generally been the default.
In general I think this has been a useful tool [0]. But lately I’ve been wondering whether shipbuilding isn’t a more apt comparison - they’re similar to buildings along a number of different axes:
Ships are similar in size to buildings, and contain many of the same elements that buildings do (they often contain large amounts of floor space designed for occupancy, for instance.)
Ships are produced in small enough numbers[1] that they typically can’t be built using mass production methods. Traditionally ships were custom-built based on the needs of a specific client, much like many buildings.
They have a relatively long lifespan (20+ years) [2], and repair work to keep ships operational has often been a significant fraction of overall ship spending.
They exist in a highly cyclical industry, which shapes how shipbuilders structure their operations, and how the industry evolves.
Like buildings, civilization has been building ships for thousands of years, with the technology used to produce them gradually changing over time.
There’s also a few other benefits to using ships as a comparison. Unlike cars (where most production information is locked up with the producer), there’s a lot of publicly available data on ships and shipping cost. Because they’ve been produced for so long, and because ships can be built basically anywhere with water access, we’ve also seen a lot of cycles of shipbuilding moving to somewhere cheaper - America to Britain, Britain to Japan, Japan to Korea and China. And because shipbuilding is often considered a matter of national importance (for its connection to navies if for no other reason), these shifts tend to produce a lot of speculation on how x nation has lost their shipbuilding advantage, and how they might recover it, which is useful if you’re trying to understand the moving parts of the industry.
Another benefit of studying shipbuilding is that in modern history it has seen substantial improvements in productivity. And because shipbuilding consists of producing very small numbers of very large objects, these productivity improvements took a different shape than they did in other manufacturing industries. So let’s take a look at how productivity improved in shipbuilding, and figure out if it has any relevance to construction.
Pre-WWII Shipbuilding
Up until around WWII, with a few deviations, ships were built in a way that resembles modern building construction [3]. Ships were built to spec for particular clients, and assembled in place (on a shipway or drydock) in a system-by-system fashion. Workers would first lay down the keel, then build and attach the frames, then attach the hull piece by piece, then build out the various systems - piping, ventilation, electrical, etc. This work was typically done by skilled craftsmen (often members of unions) trained in some particular system or task - shipfitters, boilermakers, etc. The work was often done with comparatively lightly specified drawings, leaving it up to the expertise of the workers assembling the ship to fill in the blanks [4]. It was a time consuming and labor intensive process.
Like with building prefabrication, there were many early examples of attempts at a more industrialized production process, that often stretch back surprisingly far - the Venetian shipbuilding arsenal, for instance, was able to produce galleys using something resembling an assemblyline process, with partially-built ships moving along canals from station to station. And during WWI highly prefabricated ships were built in sections all over the country, and transported to Hog Island for final assembly. But it was the onset of WWII that would spur a widespread change in shipbuilding techniques.
Liberty Ships and the productivity revolution
During the war, it quickly became obvious that huge numbers of cargo ships would be needed to ferry goods from the US to Europe, and to make up the losses being incurred by German submarine warfare. Early on the US was prevented by the Neutrality Act of 1939 from aiding Britain directly, but Roosevelt sought ways of aiding them by other means. The result was the Emergency Shipbuilding Program, where the US would build merchant ships for Britain in several newly-built shipyards. In 1940 the US was contracted to build 60 ships (totalling 600,000 tons) for Britain, a bit less than the total volume of merchant ships built by the US in 1939. But the ship volume (as well as the number of shipyards) quickly ratcheted up - in January of 1941 it was expanded to over 3 million tons, then to 5 million, then to 6 million. And after the US officially entered the war after the attack on Pearl Harbor in December 1941, it was raised even more - a staggering 9 million tons in 1942 and 15 million in 1943.
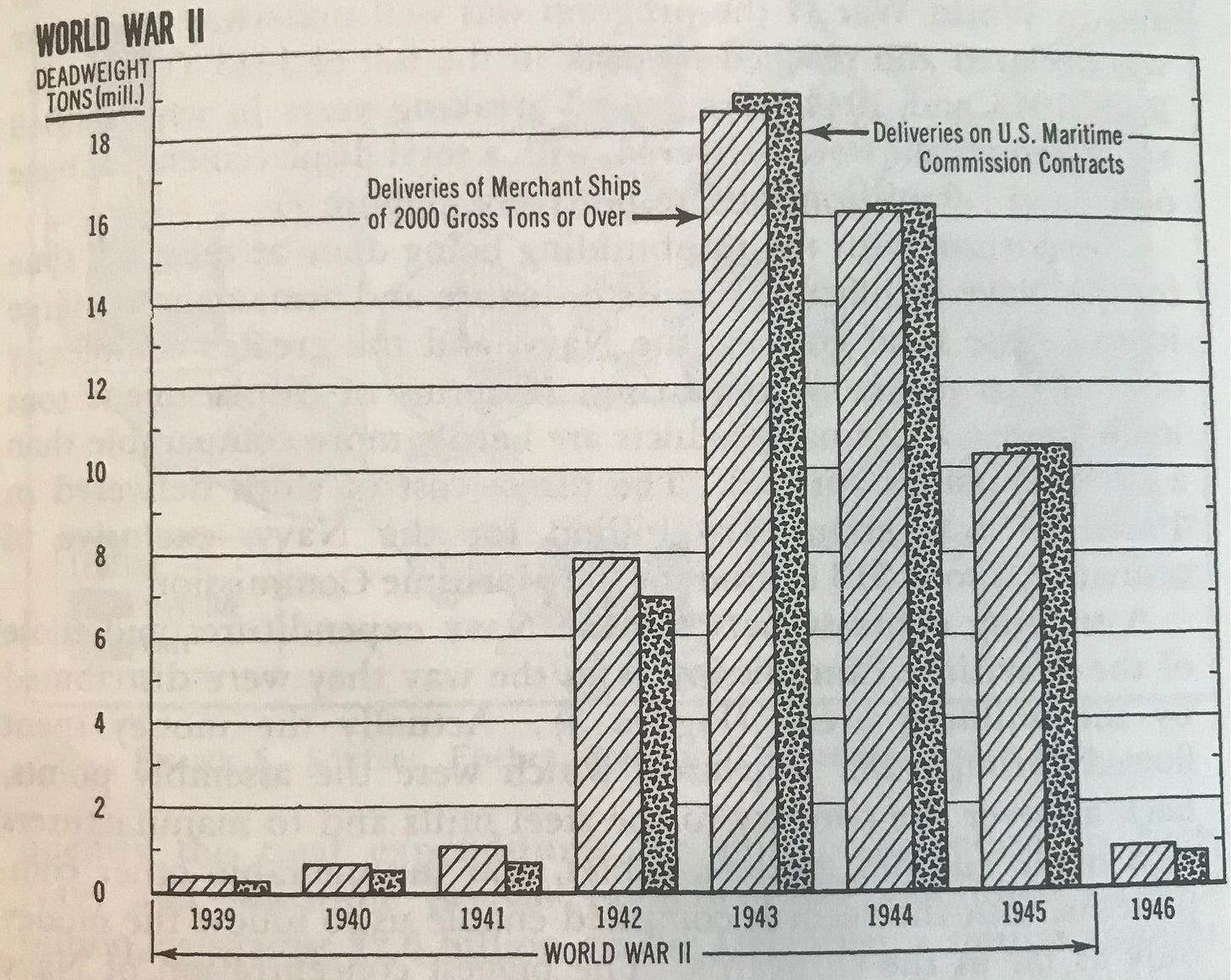
This volume of ships vastly exceeded current US production capabilities. And the new ships were needed fast - they didn’t have time to wait the months the traditional shipbuilding process took.
The result was the Liberty Ship: a simple 10,000 ton tramp steamer based on a British design that was in many ways old fashioned (it used, for instance, an outdated compound steam engine instead of a more modern steam turbine) that could be quickly produced in huge numbers [5]. To produce the number of ships needed, several new shipyards would be built, many of which would be operated by groups who had no previous experience shipbuilding, notably Kaiser and Bechtel, heavy construction companies. The entire effort was coordinated by the US Maritime Commision.
To build the ships at the speeds and quantities required, new production methods were needed. Traditionally, ships had been built using riveting, a method of joining steel plates by forcing a headed steel pin through them, then hammering down the opposite end. The Liberty Ships, on the other hand, would be welded. Not only could welding be done faster, but unskilled workers could be trained to do it far quicker than they could be trained to rivet - it took just 10 days to train a welder to perform basic production work [6]. In addition, welded ships were more efficient - they required significantly less steel than riveted ones, since they didn’t have overlapping metal plates, and they didn’t have the drag induced by rivetheads projecting into the water [7].
Arc welding was first developed in the 1880s, and had been gradually improved and adopted by other industries over the following decades, but was still treated as suspect by the shipbuilding industry, and was used only in limited applications [8]. (This reluctance would prove somewhat well-founded, as a nontrivial fraction of Liberty Ships failed due to cracks caused by stresses incurred from welding.)
Using welded construction as a starting point, several US shipyards (notably Kaisers) set about creating a revamped method of ship production that would allow for rapid construction. Rather than being built from the ground up system-by-system, ships would be constructed from large, prefabricated blocks that were built in various workshops and assembly stations in the yard, and then attached together on the shipway. This allowed most of the work to take place off the shipway, in large fabrication yards where huge blocks of the ship were fabricated then lifted into place. Once assembly was complete, the ship would be moved out of the shipway, and work would start on assembling a new ship.
Tassava 2003 describes some of these assemblies being fabricated. Here’s a description of the forepeak, the front of the ship, being built:
Another typical skid-built subassembly was the massive forepeak section which, when installed on the hull, became the ship’s prow. As complicated as the inner bottom was simple, the prow was simply too big to build indoors, and so Kaiser-Richmond and Marinship both fabricated them on special skids which merged scaffolding with a kind of massive jig. Aided by cranes, workers assembled numerous curved plates (which had been gently but precisely bent along all three dimensions in the plate shop) into a massive V-shaped structure which only remotely resembled a ship’s prow. Clambering onto the scaffolds, workers then affixed reinforced deck plating and steel braces to gird the prow in case of collision and carefully cut out holes for anchor chains, piping and wiring, and sundry mechanical equipment. Forty feet in height and fifty tons in weight, a completed forepeak resembled a slumping pyramid as it stood awaiting the teamed-up cranes that would turn it ninety degrees and install it at the front of a building hull.
And here’s the deckhouse [9]:
The manufacture of Liberty ship deckhouses in the Richmond Prefab plant highlights these differences. On skids at the intake end of the Prefab building, workers turned plate steel into deck plates, compartments, and other discrete pieces of larger components. This partially-fabricated steel flowed steadily into the Prefab building, where overhead cranes laid them on massive rolling platforms and teams of shipfitters and welders began assembling them into individual deckhouses. Beginning with the square surface of the main deck, these teams added the bulkheads of that deck’s compartments, the second deck and its compartments, and finally the third deck and its compartments. At the egress end of the plant, a worker could see a long line of increasingly complete deckhouses extending towards her.
Because the shipyards were building hundreds of identical ships, there were ample opportunities for streamlining and improving the operations. Over time, for instance, it was found to be more efficient to rearrange production to have certain areas of the yards focus on one particular type of assembly (such as forepeaks, or double-bottoms), and to have all the necessary equipment in place that the work required. And once there were specific assembly stations that did specific tasks, the layout of the yards could be rearranged to allow material to smoothly flow from one assembly station to another, until it was ready to be attached to the ship [10].
Another example is the effort spent on reducing the amount of work required after the ship left the shipway. Once the hull was complete, there were still hundreds of tasks needed to get it in seaworthy condition - carpentry work in the quarters, final electrical work, installation of insulation, installing cargo booms and lifting equipment, final engine installation, and so on. Early on, most of this outfitting work was done when the ship had moved off the shipway. This was time consuming and difficult, and the rapid pace of work meant that ships often had defects that were known at the time of fabrication, but couldn’t be addressed without disrupting the steady flow of material through the yard. (In “Ships for Victory”, Lane mentions that some ships were built with doors in locations that were known to be incorrect, that were simply built and then repaired later.) Over time production was reorganized to push more of this work back up the production line where it was faster and easier to do - things like ladders, fans and ventilation units, gratings, and insulation were installed on the subassemblies in workshops, rather than when the hull was complete (and working conditions were far more cramped.)
Many of these improvements were based on suggestions from the workers themselves, a process that the shipyards encouraged and incentivized. Workers would write up their suggestions and place them in suggestion boxes, which would then be reviewed by a labor management committee. If approved, the worker would receive a bonus, and would be tasked with implementing it. By 1945, the Maritime Commision had collected more than 3000 suggestions, which collectively saved $45 million and 31 million manhours, and the suggestions were compiled into books and distributed throughout the shipbuilding industry. A few examples of improvements:
One worker invented a special clamp to allow a chalkline to be held by just one person.
Plate shop workers installed cams to allow 3-dimensional adjustments to their flame planers.
Workers created a mini-prefab plant to assemble parts of the steam engine, which reduced installation time by 90 percent.
Welding machines were moved into large racks to allow them to be easily lifted by crane onto the building hull.
Creation of a “mock engine room”, for laying out and fitting the engine room floor plating before installing it on the ship, which saved thousands of hours of labor.
Creating posters detailing the different welds to be used throughout the ship.
The result of this continuous improvement was a steep drop in the time it took to produce a Liberty Ship - from over 200 days in 1941 to under 50 days in 1943 (in one publicity stunt, a Liberty Ship was built in just under 5 days.) Labor requirements fell as well, from over a million hours per ship on average in 1941 to under 600,000 in 1943.
In large part, the Kaiser shipyards led the way in the development of improved assembly techniques. Kaiser’s California and Oregon yards were some of the most productive shipyards producing Liberty Ships - ships built at Oregon and Richmond plant 2 achieved costs that were 5% lower than the national average, despite the west coast having higher labor costs. Altogether Kaiser Yards produced 1480 ships during the war, including 862 Liberty Ships (33% of the total) and 306 Victory Ships (60% of the total.) Staff from other shipyards frequently visited the Kaiser shipyards to learn their production techniques.
However, though the Liberty Ship production achievements were impressive, they were still in many ways unrefined. Though they often touted their “mass production methods”, assembling the ships still required a great deal of manual fitting to get everything to align - parts weren’t produced at sufficient tolerance to be interchangeable, and skilled workers were needed to fill in the gaps (figuratively and literally.) And there were difficulties in adapting the processes developed to things other than Liberty Ships - when a new type of ship came along (such as when the yards switched to producing Victory ships), productivity tended to decline, as their learning curves reset.
And while the new assembly methods resulted in improved productivity, productivity levels remained below what the British could achieve. The British, using their more traditional methods (riveted construction and lightly specified drawings), were able to produce Liberty-type ships at lower cost and fewer labor hours than the US was able to - at best, the most efficient US yards may have been able to match British yards [11]. Part of this was likely due to optimizing for speed at the expense of efficiency - the British ships were produced much slower than the US ones, and the US emphasized speed of production above all else. But it would take further development for the new shipbuilding methods to be unquestionably superior. Those developments would take place in Japan.
This will continue next week with Part II!
These posts will always remain free, but if you find this work valuable, I encourage you to become a paid subscriber. As a paid subscriber, you’ll help support this work and also gain access to a members-only slack channel.
Construction Physics is produced in partnership with the Institute for Progress, a Washington, DC-based think tank. You can learn more about their work by visiting their website.
You can also contact me on Twitter, LinkedIn, or by email: briancpotter@gmail.com
[0] - For instance, one defense I’ve heard of needing many separate building permitting jurisdictions is that it’s necessary to deal with regional variation in building conditions. But cars clearly operate in lots of different environmental conditions without needing separate approval bodies.
[1] - In 2020, there were fewer than 100,000 ships over 100 gross tons in the world. New ship construction was a bit over 3% of total gross tonnage of the existing world fleet.
[2] - If you look at fleet statistics from Lloyds register, the average age at disposal is well above 20 years up until 1998. UNCTAD gives an average ship age of 20 years for 2020, though if you scale that by ship size the average age drops to just over 10 years, due to containerships continuing to get larger over time. By comparison, the average age of cars on the road is just over 12 years, though it has been rising over time.
[3] - For instance, from Tassava 2003:
the assumptions and routines which governed ship construction remained strikingly constant through the transitions from sails to steam and wood to metal. A similar process turned out ships as diverse as galleys, clippers, steamships, and dreadnoughts. A shipowner still contracted with a yard for a precisely-specified vessel. A small crew of craftsmen still erected the ship on an assembly berth which comprised, along with nearby shops (and a body of water), a strikingly compact industrial facility. Whether working with wooden planks and timbers or metal plates and shapes, the assembly crew built the vessel one piece at a time.
And from Weirs 1984:
The traditional organization of shipbuilding, dating from the days of wooden ships, was to construct the ship in place, working on each functional system of the ship in turn. First, the feel was laid, then the frame erected, and so on. When the hull was nearly complete, outfitting of the ship began. Outfitting was planned and carried out by system, as ventilation, piping, electrical and machinery systems were installed. The traditional organization of work presented several obstacles to high productivity. Managing and controlling the construction of a large ship on which literally hundreds might work was a very difficult task using traditional methods.
...The failure of one work crew to finish work needed by another would frequently result in overtime for one crew and idleness for another. Poor timing in providing material often slowed progress as well. Worker specialization was difficult because of the sequence of radically different activities; the task of erecting the frame was very different from outfitting. Consequently, workers specialized by skill or craft rather than by task, becoming master welders, pipefitters, etc. instead of master outfitters or master hull builders. Since all the building activity was done at the shipway, use of any but temporary manufacturing equipment was difficult. Outfitting the ship after completion of the hull placed a number of handicaps on efforts to increase productivity. First, and most importantly, the cramped quarters inside a ship severely limited the number of workers who could work in an area at any one time. The size of available openings made moving machinery and equipment inside the ship awkward, and the provision of temporary services such as welding cables, staging, compressed air, etc., could be difficult, costly, and even dangerous. Moreover, workers often performed tasks overhead or with compromised access to their work, and frequently worked exposed to the weather.
Regarding compromised access, the effects of this can’t be understated. From Stott 2018:
The British Shipbuilders extensive productivity improvement program of the 1980s, conceived in conjunction with Louis D. Chirillo and IHI of Japan, estimated that the cost of a piece of work doubles once the block has left the workshops and that the same piece of work takes 8 times as many man-hours if undertaken at the final assembly site compared to at the early stage of the steel fabrication process and 12 times if undertaking postlaunch.
[4] - In particular, Britain was known for having a much different drafting tradition than America, and required much fewer drawings to specify a ship than America did. From “Liberty’s Provenance”:
In Britain, a skilled shipbuilding workforce, used to repetitive practices, did not require the number of working drawings illustrating what was to be done and how it was to be done. With regard to the engines alone, eighty drawings became 350. British practice was to build up machinery from scratch - in effect under the one roof. It was seldom innovative. It was repetitive, following long accepted and well-proven procedures and practices. Tradesmen learnt their skills over many years of apprenticeships to the point where technical drawings were minimal and tended to be indicative rather than prescriptive. For the Americans, tolerances, clearances and other details normally taken for granted in Britain had to be specified in infinite detail.
[5] - The Liberties were often described as “5 year ships” because they only needed to be useful for a very short amount of time. From the House Committee on appropriating the money for them in 1941:
It is slow and seaworthy and has the longevity of a modern steel ship, but for the demands of normal commerce in foreign trade it could not compete in speed, equipment, and general serviceability with up-to-date cargo vessels. The design is the best that can be devised for an emergency product to be quickly, cheaply, and simply built. They will be constructed for the emergency and whether they have any utility afterward will have to be determined then.
[6] - This was aided by the fact that both Kaiser and Bechtel had significant experience with welding, having used it for hundreds of miles of pipeline construction. From Tassava 2003:
By 1940, Kaiser and Bechtel had accumulated more than a decade of experience [welding] laying hundreds of miles of pipelines all over the Middle and Far West.
[7] - Drag problems would eventually be solved by the development of flush riveting for the construction of aircraft.
[8] - Welding had been adopted to a limited extent in shipbuilding to help get around the London Naval Treaty, which placed limits on ship weight. The Germans, for instance, used welding on their pocket battleships to reduce their weight, allowing them to mount larger armaments.
[9] - A longer description of figuring out how to prefabricate the deckhouses, from “Freedom’s Forge”:
“Under the traditional methods of shipbuilding, when a ship’s hull was nearing completion and the deckhouses were being added, swarms of welders, electricians, cutters, pipe fitters, burners, and joiners moved in, out, and around the action to do their job—but also getting in each other’s way. This meant the process of building a ship actually slowed down the closer it got to completion, as Kaiser’s men were finding out.
Edgar and Clay tried various ways to speed up the process. But they couldn’t avoid the fact that the shipbuilding process required doing large numbers of tasks at once, rather than in sequence like Knudsen’s auto assembly line.
Bedford decided there had to be a better way—and the place to start was the Liberty ship’s mid and after deckhouses.
He talked his idea over with Norman Gindrat. Each deckhouse was made up of separate slabs of steel averaging twenty feet long each—the heaviest weighing 72 tons and the lightest 45 tons. Clay told him to create a prefabricating shop where workmen could weld these sections together and build the deckhouses off-site. Then he and Clay would find a way to move those assembled deckhouses and install them complete, onto the hull—like snapping the lid onto a box.
What Gindrat came up with was a mammoth 480-foot-long steel-frame shed, with two 90-foot bays with three bridge cranes in each bay, and a 150-foot run out beyond the building where the slabs of steel would be set out—and a vertical clearance below the cranes of 40 feet. Work spaces for the various crafts for outfitting the deckhouses, from joining and pipe fitting to electrical and sheet metal shops, ran along the long sides of each bay.
Once it was built, Bedford put Elmer Hann, a veteran shipbuilder Kaiser had recruited from Consolidated Steel in San Francisco, in charge and stood by to watch. Plates and structural shapes went from the various suppliers direct to the warehouse, and then to the prefab center by flatcar or trailer. There three conveyor belts in each bay were set up to handle three deckhouses at a time. The belt was not a belt at all, but a three-foot-high concrete platform, on which were mounted trolley wheels at two-foot intervals—and on the wheels were the enormous mounted jigs carrying the deckhouse and pulled by a two-drum 10-horsepower hoist at the opposite end.
First the decks were laid out, made of thirty-six steel plates, and double-torched and match-marked to fit. Then the plates were set on an “upside down” jig on the conveyor belt, where they were welded together by two welding machines and a pack of Lincoln 300-amp welders.
Then came the beams, stiffeners, and other shapes that were welded in place, each cut and bent to shape in large numbers ahead of time and stored in the “angle orchard.” Then bridge cranes lifted each deckhouse and turned it right side up and onto a series of jigs, so that the bulkheads, boat decks, bridge decks, house tops—all cut, shaped, and machined ahead of time and stored in racks—as well as piping, plumbing, heating, and electrical wiring, could be installed, station by station, on the belt.
By the time the deckhouse reached the end of the conveyor belt, it was complete in every detail, including temporary stiffeners and rigging for hoisting each deckhouse into place in the shipway. Then a retractor conveyor picked it up and jacked it up for a trailer. Each trailer was a Trailermobile weighing eighty-five tons, with thirty-two 10×15 tires. Then a Caterpillar DW10 tractor moved it to the ways, where four high gantry cranes lifted the finished deckhouse and slid it into place. Easier said than done, since coordinating all four cranes to lift at the same time took some planning and skill. But like everything else in the Kaiser yards, practice made perfect.
Bedford soon expanded this technique to include the engine room. All the one hundred sections of piping were prefab, which the pipe fitters worked together in a mock-up of the Liberty engine room, complete with a wooden dummy engine. Welders fastened down the flange at one end of each pipe with a complete weld, but the other ends were only spot-welded so that they could be disassembled, then refitted and welded into place in the actual ship.
Assembly-line production had come to America’s shipyards. By August the prefab yard had 2,500 workers, with 42 women welders and burners—and ships were ready that were 95 percent preassembled.”
[10] - See “Ships for Victory” pg 224.
[11] - From “Britain’s War Machine:”
...while Liberty ship production was exceptionally fast, British output per man-hour was ‘appreciably higher’. In 1942 British yards needed an average of 336,000 person-hours to build a Liberty-type ship, while US-built Liberties at first needed 1.1 million person-hours, falling later to a minimum of 486,000. Only the most successful US yards ‘approached and occasionally overtook the British average after producing a hundred or more similar ships’.
An interesting precedent: The Monitors.
John Ericsson designed the Monitor so that Monitors could be built rapidly in any well equipped machine shop
The original Monitor was built in 100 days, despite being novel in almost every respect, from the freeboard so low (18 inches) that she made no target, to the never-before-attempted revolving turret, to the novel recoil mechanism on the guns.
A Monitor could be built in any well equipped machine shop, anywhere near water (including lakes and rivers). The turret of the original Monitor was built in a Manhattan iron works, the boiler and machinery in another Manhattan machine shop, then both were disassembled and reassembled on the hull in a Brooklyn yard.
Once the original Mionitor proved its worth, Ericsson turned them out like popcorn. Although they were not blue-water ships, they didn't need to be; they were for coastal defense and blockading.
What stood out, to me:
1. "But they couldn’t avoid the fact that the shipbuilding process required doing large numbers of tasks at once, rather than in sequence like Knudsen’s auto assembly line."
2. "There three conveyor belts in each bay were set up to handle three deckhouses at a time. The belt was not a belt at all, but a three-foot-high concrete platform, on which were mounted trolley wheels at two-foot intervals—and on the wheels were the enormous mounted jigs carrying the deckhouse and pulled by a two-drum 10-horsepower hoist at the opposite end."
Similar takeaways from modular construction factories. These can serve as indicators why spatial design of a modular construction factory floor following traditional auto assembly line rules might not be the right approach. We are already learning from an ongoing project that the traditional site construction sequencing should not be followed as is for factory build sequencing. Example, shifting solar PV install steps upstream closer to roof build station on the factory floor (vs a downstream activity, after the roof has been set). Makes sense for cost, time, collaborative work. There is even more room to get creative with the sequencing.