Reading List 04/19/25
Astro Mechanica’s fundraising, BYD’s semiconductor division, drone deliveries in Texas, Starlink in Nigeria, an Alaskan volcano that might erupt, and more.
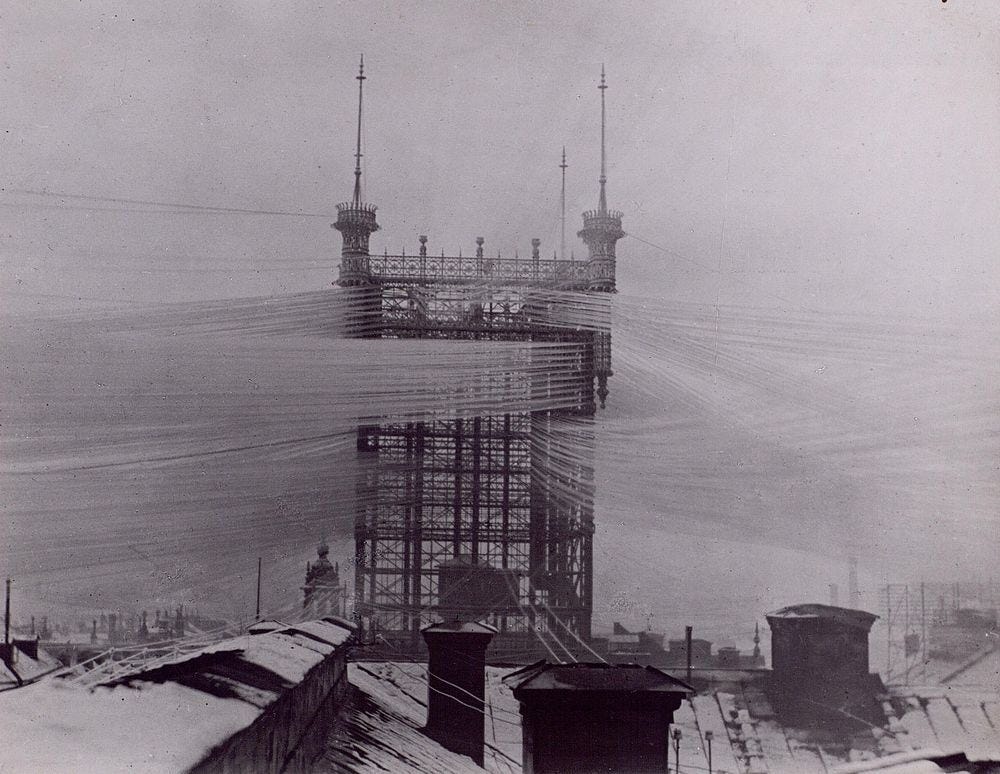
Welcome to the reading list, a weekly roundup of news and links related to buildings, infrastructure, and industrial technology. This week we look at Astro Mechanica’s fundraising, BYD’s semiconductor division, drone deliveries in Texas, Starlink in Nigeria, an Alaskan volcano that might erupt, and more. Roughly 2/3rds of the reading list is paywalled, so for full access become a paid subscriber.
Astro Mechanica raises $27 million
I’ve talked previously about the difficulties of building a new jet engine, and a new commercial airliner, and that I’m not particularly bullish on the odds of Boom Supersonic successfully delivering a supersonic airliner. But I’m not universally pessimistic about the chances of new aerospace companies succeeding. One company I’m more optimistic about (as a non-aerospace expert) is Astro Mechanica, which is developing an interesting variation of the jet engine. Rather than have the compressor driven directly by a turbine, in Astro Mechanica’s engine the turbine drives an electric motor, which in turn drives the compressor. This lets the engine run efficiently at a much wider variety of speeds than a conventional jet engine. (Partly I’m optimistic because this seems like a genuinely novel technology, and partly because their plan to pursue government contracts seems more realistic than going directly for the commercial market.) The company recently raised $27 million. Via Techtonic Defense:
Astro Mechanica CEO Ian Brooke told Tectonic in an exclusive interview that the funding will be used to build out the company’s software team, further develop and test its efficient supersonic jet engine, and stand up a team to start building air frames.
“We really want to get to the world’s first supersonic trans-Pacific demonstrator flight in the range of two to three years,” he said. Within ten years, they’re aiming for supersonic commercial flight at a price point similar to traditional air travel.
BYD semiconductor division
Nomad Semi has an interesting piece about Chinese car manufacturer BYD’s in-house semiconductor division, and how it’s enabled various BYD innovations:
BYD Semiconductor was first established in 2002 as a fabless design company to research on battery protection IC. This was a year before it decided to went into the automotive sector in 2003. Subsequently, it also went into microelectronics, optics and LED.
In 2004, TSMC made the decision to shut down Fab 1. This was the company’s very first fab, originally located inside the Industrial Technology Research Institute (ITRI) where TSMC was founded in 1987. In 2005, all the equipment from TSMC’s Fab 1 was sold off as a complete line to establish a 6-inch fab at Ningbo SinoMOS Semiconductor (宁波中纬). Ningbo SinoMOS’s patents were mainly licensed from TSMC. Many of their engineers were also former TSMC employees, so there were some similarities in process technology and management.
Facing financial difficulties, BYD came in to acquire Ningbo SinoMos in 2008 for $29 million. They knew that IGBT will be a key component for electric vehicle. This is how BYD Semiconductor went from a fabless company to an integrated device manufacturer (IDM) that oversees the entire production process from design to manufacturing. In fact, BYD is also a system company that incorporates the chip made from BYD Semiconductor in its EVs.
Semiconductors seem like they’re especially important for EVs, but electronics have long been a key component for internal combustion cars. Some sources claim that a modern ICE car has more than 1000 chips (though this seems implausibly high to me), and both Ford and GM formerly operated semiconductor divisions. Ford manufactured semiconductors under its Philco subsidiary that it acquired in 1961, and under Ford Microelectronics. GM manufactured them under its Delco subsidiary.
Large language models and physical tasks
Machine learning researcher Adam Karvonen has an interesting essay exploring how good various AI models are at physical tasks. While these models are often shockingly good at various information-processing tasks, like writing software, they often come up short when asked about manipulating objects in the real world:
Since the GPT-4 release, I’ve evaluated frontier models on a basic manufacturing task, which tests both visual perception and physical reasoning. While Gemini 2.5 Pro recently showed progress on the visual front, all models tested continue to fail significantly on physical reasoning. They still perform terribly overall…
My evaluation is simple - I ask for a detailed plan to machine this part using a 3-axis CNC mill and a 2-axis CNC lathe. Although not completely trivial, most machinists in a typical prototype or job shop setting would view executing this as a routine task, involving standard turning and milling techniques across multiple setups.
What are the model failures? Often they simply can’t produce an accurate description of the part at all. When they can, they give advice for machining it that is incorrect.
For two years, I’ve observed essentially zero improvement in visual capabilities among models from Anthropic and OpenAI. They always miss obvious features like the flats cut into the round surface, holes, or even hallucinate nonexistent features such as holes drilled along the part’s length. I have never seen Claude 3.5, Claude 3.7 (thinking and non-thinking), GPT-4.5, GPT-4o, or O1-Pro produce a reasonable description of the part….
My high level impression when reading the response is “someone who can parrot textbook knowledge but doesn’t know what they’re talking about”. The models are very eager to give textbook knowledge about e.g. recommended cutting speeds, but are completely incorrect on important practical details. This matches my conversations with friends and former colleagues in manufacturing and construction: current LLMs are seen as almost entirely useless for the core, hands-on aspects of their jobs.
NEPA reform misstep
A stated goal of the Trump administration is to accelerate the construction of major infrastructure and eliminate burdensome permitting requirements. One of the first actions taken by the administration was to remove the authority for the Council on Environmental Quality to make new regulations around the National Environmental Policy Act (NEPA). This week the administration has tried to further reduce NEPA burdens by directing all federal agencies to revoke NEPA rules, and instead issue nonbinding guidance.
Unfortunately, as my colleague Aidan Mackenzie points out, this is almost certainly going to backfire, and create much more permitting overhead and uncertainty:
Repealing CEQ reg authority was a fine step — it softens some regulatory requirements and gives agencies flexibility to redo & improve how they implement NEPA.
But it was always a down payment: The real upside is figuring out how agencies can redo NEPA regs and make them better…
Now CEQ is directing agencies to convert the actual agency NEPA regs into guidance. This is significantly different than getting rid of CEQ reg authority (and bad):
-NEPA is a law and it must be followed — agency regs explain how to do that by setting standards, CatExs, etc…
-Converting agency regs into "guidance" will only serve to confuse everyone including bureaucrats, project devs & courts.
-The process for converting current regs into guidance will get sued, requiring notice and comment and years of litigation... taking time away from reform
In (possibly) better permitting news, the White House also issued an executive order directing agencies to adopt technology to streamline the permitting process and reduce permitting times:
Executive departments and agencies (agencies) shall make maximum use of technology in environmental review and permitting processes for infrastructure projects of all kinds, such as roads, bridges, mines, factories, power plants, and others, to:
(a) eliminate the use of paper-based application and review processes;
(b) accelerate the processing time for projects, with little to no impact on quality of review;
(c) reduce the length and increase the accessibility of documents related to permit applications;
(d) reduce duplicative data submissions;
(e) increase the interagency use of existing analyses including analyses from other agencies relevant to different permit applications for the same projects;
(f) eliminate friction in coordination between agencies in the environmental review and permitting processes;
(g) improve the transparency and predictability of project permitting schedules;
(h) ensure agency legal departments have the support, funding, and technology to provide the most expeditious and best defense of challenged environmental documents and permit decisions;
(i) streamline the overall environmental review and permitting process at the Federal level, with the goal of speeding data gathering and decision-making that can improve timeliness for State, local and tribal decision-making as well; and
(j) maintain a readily available source of information that may be relevant to judicial review of any permits.