The construction industry is (slowly) beginning to see increased focus on the environmental impacts of buildings and construction. One area that seems to be getting a lot of attention recently is the carbon emissions due to cement and concrete. This seems at least partly due to Bill Gates’ book “How to Avoid a Climate Disaster”, which talks about emissions from cement (and I’ve been told everyone in Silicon Valley read.) Cement production is a huge industry, and is responsible for somewhere around 5-10% of global CO2 emissions [0]. Because concrete is such a fundamental part of the built environment, it’s worth taking a look at this problem in the context of how, as a civilization, we use concrete.
First, a bit of background - concrete is formed by mixing together cement, aggregates (such as sand and gravel), and water. The cement (which mostly consists of calcium silicates), reacts with the water in a process known as hydration, and binds the entire mixture together into a single solid mass. Beyond its strength and its low-cost, it’s the property of starting out liquid that makes concrete so useful - it can easily be formed into any shape, and can be leveled with the help of gravity to form a flat walking or bearing surface. Essentially all modern concrete is reinforced with steel bars, which provide tensile strength and arrest cracks.
The CO2 emissions from concrete are mostly due to the production of cement [1]. This is partly due to the energy intensive production process, where limestone and clay are heated in a kiln to ~2500 degrees F. And it’s partly due to the chemical reaction that produces cement (calcinization), which releases CO2 as a byproduct. Roughly 50-60% of emissions of cement’s carbon emissions are due to calcinization [2], and thus wouldn’t be addressed by moving to less carbon intensive electricity sources.
The scale of concrete production
The most important thing to understand about concrete is the scale of its production. The world produces somewhere around 4.25 billion metric tons of cement annually [3], which works out to about 30 billion tons of concrete produced each year [4].
How much is 30 billion tons?
It’s not easy to get a sense of scale once you start to deal with numbers this big (billion doesn’t feel 1000 times bigger than million). One way of looking at it is we produce around 4 metric tons, or just under 60 cubic feet, of concrete for each person on the planet every year (this is a cube just under 4 feet on a side).
Another way of looking at it is to consider the total amount mass that gets input to civilization each year. Estimates here vary quite a bit, but it seems to be in the neighborhood of 100 billion tons [5]. So of the total volume of material that gets extracted and used each year (including all oil, all agriculture and tree harvesting, and all mining), around 30% of it by mass goes toward making concrete. The amount of concrete produced each year exceeds the weight of all the biomass we use annually, and all the fossil fuels we use annually.

Another way of looking at it is that the total mass of all plants on earth is around 900 billion metric tons. So at current rates of production, it would take about 30 years to produce enough concrete to exceed all the Earth’s plant (dry) biomass.
And because a) we’ve been producing concrete for a while, and b) concrete tends to last a long time, we seem to be on the cusp of this happening. Elhacham et al 2020 estimates that total human-created mass (roughly half of which is concrete) reached the total weight of all earth’s biomass sometime in 2020. Eyeballing their graph, concrete alone will exceed total biomass weight sometime around 2040.
In a pure mass-flow sense, human civilization is basically a machine for producing concrete and gravel (and to a lesser extent bricks and asphalt), with everything else as just a byproduct.
Where concrete goes
So civilization uses a lot of concrete. Where is it all going?
Geographically, everyone probably knows the punchline here - most of this concrete is being used in China. In recent history, China has been responsible for roughly half the world’s cement production and consumption (and by implication, concrete use) [6].

Here’s another view from around 2010, showing what this has looked like over time (data after 2010 is a projection).

This gets summarized in the oft-repeated statistic that China used more cement in 3 years than the US did in the entire 20th century.
But since China has such a large population, we can get a more intuitive understanding of this by looking at cement consumption per-capita. Here’s per capita consumption sometime around 2015 (via Globbulk):
We see that the official numbers from China make it a huge outlier in cement consumption, using around 8x the amount per capita as the US (though some Middle Eastern countries exceed it. Saudi Arabia is higher, and Qatar, which is somewhere over 2000 kg/capita, doesn’t even show up on the graph).
The official Chinese numbers are so huge, in fact, that some analysts suspect that they’re inflated, either by manipulating the data, or by producing construction projects that don’t have actual demand (or both). The graph above also includes a more “realistic” estimate (which is still 3x as high as US per-capita use).
What does all this concrete construction mean in practical terms? Well, China has somewhere around 50%-60% of the floorspace per capita as the US does, or roughly as much living space per capita as most European countries [7]. This is the result of a massive trend towards urbanization over the last quarter century. In under 20 years China quintupled its urban residential floor space, and urbanization rates went from around 25% in 1990 to 60% in 2017, during which it also increased its population by 250 million (roughly the size of the 1990 US). China is what you get if you double your total floorspace in 20 years in a country of over a billion people, and use concrete construction as the way to do it.
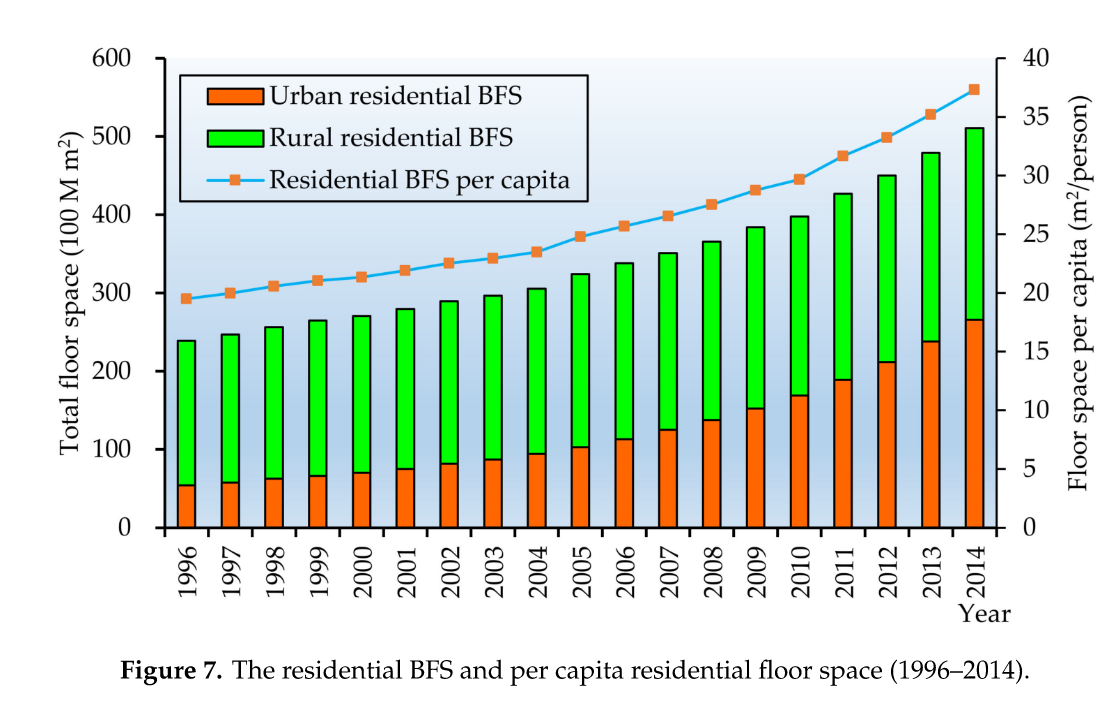
Beyond China, we see high rates of cement use in the rest of Southeast Asia, as well as the Middle East [8].
One reason you see this volume of concrete use in lower income, urbanizing countries is that concrete construction is comparatively labor intensive. The materials for concrete are extremely cheap, and much of the cost (especially in high-cost labor countries, such as the US) is due to the labor to produce it - building and setting up the formwork, laying out the reinforcing, placing the embeds, etc. If you’re a country with a lot of low-cost labor, this is a pretty good tradeoff.
In addition to the current largest users, one trend to keep an eye on long-term is India’s concrete use. If it ever proceeds on a path of mass-urbanization similar to China, (as some folks speculate it will), we could see a massive uptick in global concrete output - India’s current urbanization rate of 34% is around where China was in the late 90s. A shift in India towards a per-capita cement consumption more consistent with the rest of southeast Asia (say, around 600 kg/capita) would increase worldwide cement consumption by about 13%, and it does seem as if India’s cement use is trending upward.
By contrast, one thing clear from this data is that the US actually uses an unusually low amount of concrete - per capita, it uses as little as any other western country, and far, far less than some (who knew that Belgium was such a prolific user of concrete?) To some extent, it seems like the greatest concern about concrete use comes from places that use the least of it.
Concrete use by application
So we’ve seen where it gets used in the world. Can we go deeper, and look at specifically what concrete is being used for?
This will vary significantly depending on the region, and the local construction tradition. In the US, we have roughly the following breakdown (via PCA):
Overall, roughly half of our concrete gets used in buildings, and half gets used for infrastructure (streets and highways, water conveyance and treatment tanks, etc.) About 26% goes into residential buildings, and 16% into commercial buildings. And because most construction in the US is just 1 or 2 story buildings (which will mostly be wood for residential buildings, and steel for commercial ones), this concrete is probably mostly going into foundations, slabs on grade, and concrete over metal deck (though there’s probably a substantial amount going into concrete masonry units as well).
But the US has a somewhat unusual construction tradition, where the vast majority of our residential construction (both single family and multifamily) used light framed wood. In other places, it's much more common to use concrete as the primary structural system. Here’s a breakdown in concrete use from the UK:

The UK uses closer to 80% of its concrete for buildings, with most of that going towards the superstructure. China (which has urbanized on the back of huge numbers of concrete residential highrises) probably devotes an even larger share to residential construction.
A world with less concrete
Understanding how much concrete the world uses, and where it uses it, is important if you want to use less of it.
The scale of the industry is particularly important to keep in mind. For instance, you often see enthusiasm for the idea of replacing concrete buildings with mass timber ones. But assuming you could substitute all the world’s concrete for an equal volume of wood [9], you’d need to more than triple the total annual volume of global wood harvested [10], which puts a somewhat different spin on the issue.
And many other materials would have emissions as bad or worse than concrete if they were used on the same scale.
Consider, for instance, railway ties. In the US, these are still largely made out of wood, but in many places have been replaced with concrete ones. And some places are considering changing from concrete to plastic composite rail ties instead. It’s hard to know the exact embodied emissions without a lot of specific details about the materials and supply chains used, but can we ballpark how much plastic uses compared to concrete?
Per the Inventory of Carbon and Energy database, concrete varies between 150 and 400 kg of embodied CO2 per cubic meter, depending on the properties of the mix, with an “average” value of about 250. Plastics mostly have embodied emissions of about 3-4 kg of CO2 per kg of plastic, or about 3500 kg per m3 (assuming a density of about 1000 kg per cubic meter). So per unit volume, plastic embodies somewhere around 10x as much carbon as concrete does.
We can also do a more direct comparison. Consider a beam spanning around 20 feet, and supporting a 2.1 kip per foot vertical load. The lightest US standard steel section that will span this distance is a W16x26, which weighs about 236 kg and will have embodied carbon emissions (based on the ICE database) of around 354 kg.
A concrete beam of the same depth, supporting the same load and spanning the same distance, will be 10.5 inches by 16 inches, with (3) #10 bars running along the bottom. This beam will have about 190 kg of embodied emissions from the concrete, and about another 230 kg of embodied emissions from the steel. This is about 20% more than the steel beam, but in the same ballpark - and over half the “concrete” emissions are actually due to the embedded steel.
This is arguably a non-representative example (most concrete, such as in columns or slabs, will have a much lower ratio of steel), but the basic logic holds: concrete is unusual in its total volume of use, not how emissions heavy it is as a material. Most substitutes that aren’t wood, recycled materials, or byproducts that can be had for ‘free’ won’t necessarily be much better when used at the same scale. In some ways, it’s surprising that the carbon emissions from concrete are as low as they are.
Lower carbon cement
Of course, this calculus is likely to change over time - as electricity sources are replaced with lower carbon ones, you’re likely to see the embodied emissions of materials drop along with it. But since cement releases CO2 as part of the chemical process of producing it, concrete will get comparatively worse over time.
One potential option here is to find ways of changing the concrete or cement production process to be less carbon intensive. The easiest option is to just replace manufactured Portland Cement with some other less carbon-intensive cementitious material. These are often industrial byproducts such blast furnace slag, silica fume, and fly ash, and thus don’t have a ‘carbon penalty’ (since they’d be produced regardless.) These can potentially eliminate large volumes of cement in a concrete mix, and they’re a key part of current low-carbon concrete strategies (and even ‘normal’ concrete mixes tend to utilize these to some degree.) But the total volume of these materials is limited by the extent of various industrial processes (and for things like fly ash, which are a byproduct from coal plants, we can expect production to decline over time.)
Another option is to take advantage of the fact that concrete will naturally absorb CO2, a process known as carbonation (even normal concrete will absorb roughly 30% of the CO2 emitted during the production process over the course of its life.) Companies like Carbicrete, Carboncure, Carbonbuilt and Solida all offer methods of concrete production that allow the concrete to absorb CO2 during the production process, substantially reducing embodied emissions. Interestingly, these producers mostly claim that their concrete is actually cheaper than conventional concretes, which would obviously be a massive tailwind for the technology’s adoption.
It’s not obvious what the best path forward is for addressing concrete carbon emissions (like with most things, I suspect it’ll end up being a mix of different solutions), but understanding the parameters of the problem is necessary for solving it.
These posts will always remain free, but if you find this work valuable, I encourage you to become a paid subscriber. As a paid subscriber, you’ll help support this work.
Construction Physics is produced in partnership with the Institute for Progress, a Washington, DC-based think tank. You can learn more about their work by visiting their website.
You can also contact me on Twitter, LinkedIn, or by email: briancpotter@gmail.com
[0] - This figure varies depending on the source - Chatham House provides a frequently-cited estimate of 8%. We can also ballpark it - roughly 0.93 pounds of CO2 gets emitted for each pound of cement produced, around 4.25 billion tons of cement are produced annually, which gets ~3.95 billion tons of CO2, and total annual CO2 emissions are in the neighborhood of 46 billion tons, getting us a bit less than 9%.
[1] - Per Circular Ecology, ~70-90% of emissions are from the cement production process, depending on the type of concrete and what the rest of the supply chain looks like.
[2] - This seems to vary depending on where the cement is being made - in Myanmar, for instance, it’s around 46%.
[3] - Another number where the sources often don’t agree with each other, see here, here and here for estimates on annual cement production.
[4] - Concrete is roughly 10-15% cement by weight, depending on the strength of the mix, what other cementitious materials are being used, etc. An average value of 12.5% yields 34 billion tons, which we’ll knock down to account for other uses of cement (masonry mortar, grout, gypsum overlay, etc.) This roughly tracks with estimates from PCA (“4 tons of concrete produced each year for every person on earth”), and from the now-defunct Cement Sustainability Initiative, which estimated 25 billion tons of concrete against 3.125 billion tons of cement in 2015.
[5] - See here, here and here for an estimate of total civilization mass flow. This doesn’t (I believe) include waste byproducts, which can be substantial - for instance, it doesn’t include the ~46 billion tons of CO2 emitted each year, or the 16 billion tons of mine tailings, or the 140 billion tons of agriculture byproducts (though this last number is difficult to verify and seems high).
[6] - We see something similar with cement as we do with other bulky, low-value materials, in that it's made in lots of distributed manufacturing facilities relatively close to where it’s used. See here for a map of cement plants in the US around 2001, for instance.
[7] - For China’s total floorspace, see here (most sources seem to agree with these numbers). For US floorspace, see my Every Building In America article. For per-capita living space in Europe, see here.
[8] - The often high-rates of cement use by middle-income countries have led some folks to develop a U-shaped cement consumption theory of industrial development - that countries start out using a small amount of cement, use more as they get richer and build up their physical infrastructure, and then eventually transition to using lower volumes of cement again. The Globbulk paper spends considerable time debunking this.
[9] - It’s not actually obvious to me what the substitution ratio would be. In strength-governed cases you’d need proportionally more timber than concrete, but in other cases (such as replacing concrete walls with light framed stud walls), you’d probably use less. Obviously you can’t substitute all concrete for wood, but you can probably switch out more than you think - there’s no reason you couldn’t use wood foundations instead of concrete ones in many cases, for instance.
[10] - 30 billion tons of concrete is roughly 12.5 billion cubic meters, and total annual wood products produced is currently around 5.5 billion cubic meters.
A couple of minor comments:
Most horizontal concrete (pavement, sidewalks, curbs etc.) is unreinforced - I would guess somewhere around 1/3 of all concrete placed in the US is unreinforced.
Concrete mix design is all about tradeoffs - strength, workability, set time, durability, cost, etc. Embodied CO2 is one of those tradeoffs. Each of these tradeoffs has a central value as well as risk. The easiest way to reduce CO2 is to reduce the cement content (i.e. more rock, less glue). This generally also increases durability, but also brings in risks on the strength and workability fronts. Mitigating this risk requires thought/engineering. In general cement is cheap and thought is expensive.
(As a note, when comparing concrete costs you need to be careful about where that cost is assessed - at the batch plant, or delivered to the site (including transport), or in place (including formwork, screeding, finishing, curing etc.).
With regards to carbonation, carbonation only applies to the lime component (calcium hydroxide aka CH). An excess of CH is generally necessary to get an acceptable set time, but is in general detrimental to durability. CH can get soaked up by supplementary cementitious materials (flyash, slag, natural pozz, CO2 injection (trivially in that case) etc), but then that CH is not available for future carbonation. In a geologic timeframe all of the available CH will get soaked up by something, but good quality concrete doesn't have a lot of excess CH, and the penetration of carbonic acid is very slow.
Before we start coming up with innovative solutions, we can start with:
1. actually designing structures that are efficient, instead of utilizing 75% of the capacity because 95% 'feels' too dangerous.
2. notifying the client that the architect's design could've been a lot more sustainable if it is not a 10m multistory cantilever that would require a transfer structure and a heavily reinforced core wall.
3. not giving in to seemingly sustainable design choices e.g. sky garden, which adds an insignificant amount of SDL.
In general... do you job well and less regulations