The earth contains a lot of titanium - it’s the ninth most abundant element in the earth’s crust. By mass, there’s more titanium in the earth’s crust than carbon by a factor of nearly 30, and more titanium than copper by a factor of nearly 100.
But despite its abundance, it's only recently that civilization has been able to use titanium as a metal (titanium dioxide has been in use somewhat longer as a paint pigment). Because titanium so readily bonds with oxygen and other elements, it doesn’t occur at all in metallic form in nature. One engineer described titanium as a “streetwalker," because it will pick up anything and everything. While copper has been used by civilization since 7000 BC, and iron since around 3000 BC, titanium wasn’t discovered until the late 1700s, and wasn’t produced in metallic form until the late 19th century. As late as 1945, there was no commercial production of titanium, and the metal only existed in tiny amounts in labs. But less than 10 years later, thousands of tons of it were being made a year. And 10 years after that, it formed the literal backbone of the most advanced aerospace technology on the planet.
As a report to the National Research Council notes, “the birth of a tonnage structural metal industry is an unusual event. Only three such births have occurred in the past 100 years [now closer to 150] – aluminum, magnesium, and titanium – and no new one is in prospect.” How did titanium go from totally unused to a critical aerospace technology? What does it tell us about technological development? Let’s take a look.
Origins of titanium
Titanium was first discovered in 1790 by William Gregor, an English clergyman and chemist who realized he couldn’t identify a metal contained in a white oxide mixed in with the black sands of Cornwall. In 1795, Martin Klaproth, a Prussian chemist, was able to extract titanium from the mineral rutile. Because of the strong bond it formed with oxygen, Klaproth named the metal “titanium” after the Greek Titans.
Because titanium bonds so readily with other elements and contaminates so easily, it's extremely difficult to obtain in a pure state, and for the next hundred years titanium was mostly regarded as a laboratory curiosity. In the 1880s, two Swedish scientists successfully produced 94% pure titanium metal, and in 1910 Matthew Hunter, a scientist at General Electric, developed a variant of their process to produce metallic titanium while searching for a material for improved lightbulb filaments.
But a commercially viable process for producing titanium wasn’t developed until the 1930s. In 1930 William Kroll, a scientist from Luxembourg, began experimenting with titanium in his home lab, and developed a process to produce titanium by reacting titanium chloride (TiCl4) with magnesium under a vacuum. By 1938, he had successfully produced 50 pounds of titanium metal, and successfully formed it into wires, rods, sheets, and plating. Kroll came to the US in 1938 to attempt to sell his process, but was unsuccessful.
That same year, the US Bureau of Mines began to investigate titanium, in response to promising studies of its properties performed by the Philips Corporation (which had developed its own process for producing titanium). The Bureau of Mines concluded the Kroll process had the most potential as a commercial process and began to develop it. Its work was delayed by the war, but as early as 1944 the Bureau of Mines was making 15-pound batches of titanium in a plant that could make 100 pounds of titanium a week.
After the war, the Bureau’s work on titanium accelerated. By 1947 it had successfully scaled up Kroll’s process, and had produced two tons of titanium “sponge,” a porous, spongy metal created by the process, which is melted down to produce bars, sheets, wires, etc. A 1948 report on titanium’s properties commissioned by the Bureau concluded that titanium and its alloys had great potential engineering applications. Titanium was nearly as strong as stainless steel, but weighed 40% less. It was also incredibly corrosion-resistant, and maintained much more strength at elevated temperatures compared to aluminum. This made it potentially very useful for aerospace applications, where weight was at a premium and materials were often exposed to high temperatures.
The military had followed the progress of the Bureau’s development work, and interest in the metal was high after samples began to be investigated by Army, Navy, and Air Force labs. Titanium began to be called a “wonder metal”:
The metal gained numerous advocates within the military and industry. Early promoters visualized the use of titanium in naval vessels, armor plate, tanks, trucks, landing craft, aircraft structures, and airborne equipment. It was thought that it could possibly replace both aluminum and steel in the design of many defense applications. - Simcoe 2018
In 1948, titanium first began to be produced commercially, at a small DuPont plant that could produce 100 pounds of titanium a day. The first batches of titanium went to experimental use on military jets, such as the F-84 and the F-86. To try to kickstart the industry, the Air Force encouraged manufacturers to substitute steel with titanium, and the Army Ordnance Corporation placed an order for $1 million worth of titanium metal.
In the press, titanium began to be called “the wonder metal," “the miracle metal," and the “Cinderella metal” (because it had been overlooked for so long). An executive for a company producing titanium noted that “Sensational magazine articles predicted that titanium would become the miracle metal-for spacecraft, ‘atomic furnaces,’ airplanes of all kinds, submarines, railroad tracks, truck bodies, portable bridges” (Rowley 1972). Between 1950 and 1952, more than two dozen companies announced plans to produce titanium.
But the nascent titanium industry struggled. In 1951, the materials advisory board projected the need for 30,000 tons of titanium products, but actual shipments were just 75 tons, barely enough for research applications. Producers had assumed that the same equipment for melting, rolling, and shaping stainless steel could be used for titanium, but this turned out to be very difficult: titanium didn’t behave like steel, or like any other metal. Titanium was found “not to forge like any other material,” (DTIC 1952) and stamping it in presses damaged the stamping dies. A company that studied grinding titanium noted that “titanium grinds unlike steel. Anything you have learned concerning the effective grinding of steel does not apply in the case of titanium”. The first attempts to use titanium on commercial aircraft resulted in a sheet of metal so brittle it could be torn in half like a sheet of paper. Mills found that they often “produced more scrap than useful metal" (Simcoe 2018).
To support the budding industry, the US government stepped in. It funded the construction of several titanium sponge plants, and agreed to purchase any surplus titanium sponge production for the national stockpile. It offered rapid amortization of titanium production equipment for tax purposes, and demonstrated production techniques at the Bureau of Mines’ pilot plant. The Army funded projects to develop better alloys, including one of 6% aluminum and 4% vanadium (Ti-6Al-4V) that remains the most popular alloy of titanium today, and is credited with saving the titanium industry. When it was found that rolling titanium into sheets consistently was difficult, in 1956 the Department of Defense initiated a program to develop sheet rolling of titanium, “one of the most comprehensive technical programs ever undertaken in metallurgy” (Simcoe 2018). Production problems were overcome, and titanium was increasingly used for aerospace applications. By 1958, Pratt and Whitney had produced 5000 jet engines with titanium components, and the US industry was producing thousands of tons of titanium products a year.
The A-12
In the late 1950s, Lockheed won a contract to develop a high-speed, high altitude reconnaissance plane for the CIA. Because it was the 12th iteration of a design codenamed “Archangel," it became known as the A-12. To meet the unprecedented performance requirements (a cruising speed of Mach 3 and a cruising altitude of nearly 90,000 feet), Lockheed needed a metal that would retain its strength at the hundreds of degrees the exterior of the plane would reach. This ruled out aluminum, leaving either stainless steel or titanium. Ultimately, titanium alloy was selected for the A-12, as it would cut the gross weight of the plane nearly in half.
Titanium had never been used to such an extent on an aircraft, or anywhere else. Lockheed had worked with titanium on a small scale since 1949 but prior to the A-12 titanium had mostly been used for small components on jet engines. For several years, for instance, 50% of all titanium was used in the J-57 jet engine. But on the A-12, titanium would be used for nearly every part of the airplane – 93% of the gross weight of the A-12’s structure was titanium.
Building a plane out of titanium proved difficult. Initially Lockheed “had no idea how to extrude it, push it through into various shapes, or weld or rivet or drill it” (Rich 1994), and every production problem solved seemed to reveal two or three more. Titanium was found to be “totally incompatible” with chemicals like chlorine, fluorine, and cadmium. In one case, an engineer who marked a sheet of titanium using a pen with chlorine-based ink was shocked to see the ink etch away the metal like acid. Titanium bolts that were heated had their heads pop off, a problem that was eventually traced to cadmium-coated wrenches used to tighten them. Titanium welds made in the summer unexpectedly failed, due to (it was eventually realized) chlorine that the local utility added to the water during the summer to prevent algae growth.
When Lockheed tried to fabricate a portion of the forward fuselage, which had to be made from a novel “beta” titanium alloy, it found that the titanium was so brittle after heat treating that it would shatter if dropped on the floor. This was eventually resolved by replacing an acid-pickling process with one identical to that of Lockheed’s supplier, but not before scrapping thousands of titanium components. Of the first 6000 pieces fabricated from the beta titanium alloy, 95% were lost.
But over time, Lockheed overcame its production problems. In machining, for instance, drill bits initially needed to be replaced every ten holes, ten times as often as when drilling aluminum. In other machining operations, the rate of metal removal was just 5% of the rate when machining aluminum. To improve its machining, Lockheed developed new drill bits, cutting fluids, and cutting machinery, and learned the proper “feeds and speeds” for machining titanium (it was found, for instance, that small changes in cutting speed had a large effect on tool life). Over the course of the program, the rate of metal removal in machining was increased to “3 to 10 times the industry average” (Johnson 1970), and drill life was increased by more than a factor of 10.
The A-12 “practically spawned its own industrial base” (CIA 2012), and over the course of the program thousands of machinists, mechanics, fabricators, and other personnel were trained in how to work with titanium efficiently. As Lockheed gained production experience with titanium, it issued reports to the Air Force and to its vendors on production methods, and “set up training classes for machinists, a complete research facility for developing tools and procedures, and issued research contracts to competent outside vendors to develop improved equipment" (Johnson 1970).
The A-12 first flew in 1962. 14 years later, its successor, the better-known SR-71, set an airspeed record of nearly 2200 miles per hour, which remains unbroken today.
Titanium medical implants
While titanium manufacturing for aerospace was ramping up, a very different use of the metal was being discovered. In 1952, Swedish medical researcher Per-Ingvar Brånemark was studying blood flow in healing bones. In one experiment studying the bone marrow of rabbits, Brånemark’s team implanted a tiny camera into rabbits legs, to watch the wound heal from the inside. When they later went to remove the camera, they found that the titanium camera casing had bonded with the bone.
At the time, it was thought that the body would eventually reject any foreign object implanted in it. Dr. Brånemark’s discovery that bone would bond directly with titanium (which he dubbed “osseointegration”) was radical, and had huge potential implications for medical implants. Brånemark quickly pivoted his research to study osseointegration, eventually receiving a grant from the US National Institutes of Health. Research on his own students (where he implanted a small piece of titanium in their arms) showed that titanium could be safely implanted in the body with no ill-effects.
Interestingly, during the course of this research, it was noticed that bone could conduct sound – a deaf patient was able to “hear” the ultrasonic vibrations used to check that the titanium had been implanted correctly. One of Brånemark’s students followed up on this discovery, and developed the first bone conduction implants to restore hearing in deaf people.
Brånemark’s team went on to develop titanium dental implants (which were often made from surplus aircraft-grade titanium) that lasted much longer than implants of other metals. Today, the Brånemark system of dental implants is still sold, and titanium is the most popular material for dental implants, as well as being used for other medical implants such as artificial hips.
Titanium comes of age
You can get a sense of the development of the titanium industry by reading reports on industrial symposiums held in the 1940s, 50s, and 60s.
The first symposium on titanium was held in 1948, and was organized by the Navy to provide “a comprehensive review of the titanium research effort”. Several military organizations discussed their research programs, but most of the presentations were on topics such as physical properties of titanium and its various alloys, the crystal structure that resulted from different methods of fabrication, and methods of melting titanium sponge. The pages are full of pictures of laboratory setups, graphs of data on stress-strain relationships, phase diagrams, and magnified pictures of titanium microstructure. Nearly all the presentations are from either research labs or from companies trying to produce raw titanium “sponge” from ore.
In 1952, another titanium symposium was held, this one sponsored by the Army’s Watertown Arsenal. By then, titanium was being manufactured in large quantities, and while the prior symposium had been focused on laboratory studies of titanium’s physical and chemical properties, the 1952 symposium was a “practical discussion of the properties, processing, machinability, and similar characteristics of titanium". While physical characteristics of titanium still took center stage, there was a practical slant to the discussions – how wide a sheet of titanium can be produced, how large an ingot of it can be made, how can it be forged, or pressed, or welded, and so on. Presentations were by titanium fabricators, but also by metalworking companies that had been experimenting with the metal.
Though by 1952 many of these companies had been working with titanium for years, there’s an air of uncertainty in many of the presentations, a distinct sense of “this is what we’ve learned so far, but there’s still much we don’t know.” A company that studied the effects of different working fluids when grinding titanium admitted that not enough was known about the chemistry at work to understand why different fluids had different effects. A company that studied surface treatments and polishing methods noted that “materials and methods for polishing titanium have not been definitively established," and that while “the most commonly used abrasives are not completely satisfactory," manufacturers were working on the problem, and “more efficient methods will no doubt be developed”. A company that studied cold-forming of titanium sheets described its own methods as “crude and undeveloped”.
In 1966, another titanium symposium was held, this one sponsored by the Northrup Corporation. By this time, titanium had been used successfully for many years, and the purpose of this symposium was to “provide technical personnel of diversified disciplines with a working knowledge of titanium technology.” This time, the lion’s share of the presentations are by aerospace companies experienced in working with the metal, and the uncertain air that existed in the 1952 symposium is gone. A presenter on titanium’s corrosion resistance noted that “the corrosion resistance of titanium, unlike that of most metals, can be defined within rather simple limits." A presentation on forging noted that “titanium alloys are quite forgeable…The evidence which substantiates this statement is the large number of jet engine and missile components plus the growing lists of structural parts that have been produced in the last 10 years.” And a presentation on machining noted that “Fifteen years ago, titanium was considered to be very difficult to machine. Subsequent research and experience, however, have progressively improved this situation," the result of “gradual refinements in tool materials, machine tools, tool geometries, and cutting fluids”.
Thus, by the mid-1960s, titanium had become a mature engineering material. While there was still much to learn about titanium, the practical aspects of working with it and using it to solve engineering problems were well-understood, and it increasingly found use in aerospace and other industry applications. Following the A-12, for instance, military aircraft began to make extensive use of titanium in their structural frames. From military aircraft, titanium made its way into commercial aircraft. By 1971, 46% of titanium was going towards commercial aircraft, compared to 37% to government aerospace projects.
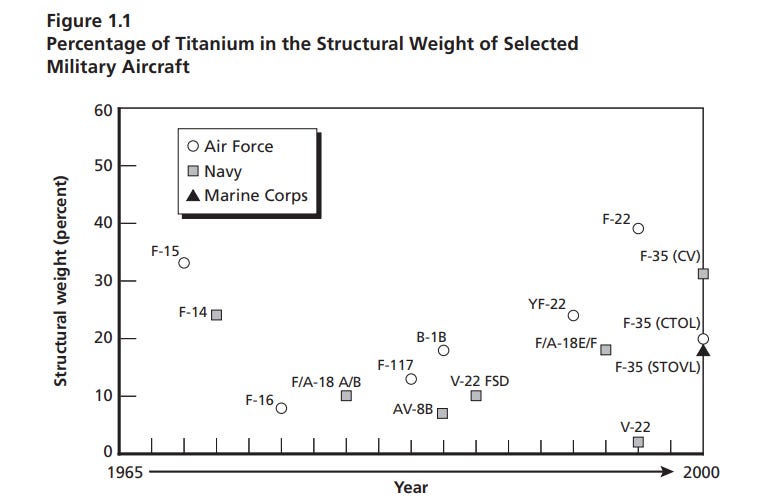
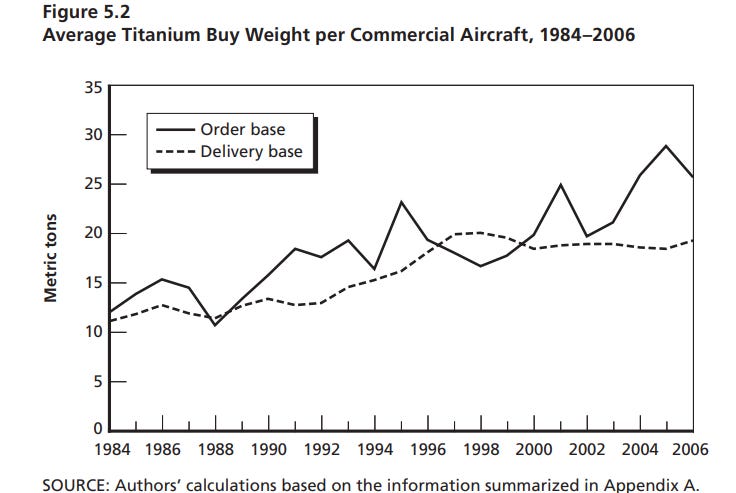
Lessons from titanium
What can we learn from the story of titanium?
For one, titanium is a government research success story. Titanium metal was essentially willed into existence by the US government, which searched for a promising production process, successfully scaled it up when it found one, and performed much of the initial research on titanium’s material properties, potential alloys, and manufacturing methods. Nearly all early demand for titanium was for government aerospace projects, and when the nascent industry struggled, the government stepped in to subsidize production. As a result, titanium achieved a level of production in 10 years that took aluminum and magnesium nearly 30.
The government’s support of the early industry was successful: shortly after the program was initiated in 1951, the cost of titanium began to decline more steeply. Since then, titanium costs have fallen at an impressive 23% learning rate (ie: costs fall 23% every time cumulative production doubles), similar to the learning rate in solar PV production. When government subsidies were removed in the late 1950s, the industry struggled, but cost declines continued. And from the initial government projects in military aerospace, titanium has spread into commercial aircraft, medical implants, industrial equipment, and other uses. Titanium is thus a successful case of the government jumpstarting an industry.
But titanium is also a story about the limits of this sort of jumpstarting. Despite its impressive learning rate, titanium remains an expensive, niche material. A 2006 report noted that titanium is five times as expensive as aluminum to refine and ten times as expensive as aluminum to turn into finished products. Despite initial expectations, titanium hasn’t widely displaced either aluminum or stainless steel, and is only used where its unique properties make its high cost worth it. The aerospace industry remains the largest user of titanium.


It's interesting to compare progress in titanium production with progress in solar photovoltaics. In both cases, the basic phenomenon (metallic titanium and producing electricity from sunlight) had been explored in the late 1800s, but it wasn’t until mid-20th century technology breakthroughs (the Kroll process and the silicon PV cell) that they became practical. In both cases, the US government funded much of the initial development, and acted as the first customer (government satellites and government aerospace projects). Both have similar learning curve slopes, and both technologies gradually expanded outside of their initial markets as knowledge was gained and the costs of the technology fell. And in both cases, there were sky-high expectations for the “potentially world-changing technology” that neither initially lived up to.
But whereas titanium remains a relatively niche, expensive technology, solar PV is increasingly widely deployed, and seems poised to become the primary method of electric power production. In learning curve terms, while both titanium and solar PV have similar learning rates, the solar PV curve has stretched much farther. Between 1975 and today, cumulative titanium production has increased by perhaps a factor of 5-10 (cumulative US consumption of titanium sponge was about 250,000 tons in 1975, and about 1.3 million tons in 2019). Cumulative solar PV production, on the other hand, has increased by a factor of more than 300,000. Though they have the same learning rate, solar PV has had many more doublings in production volume, and its costs have thus fallen much further.
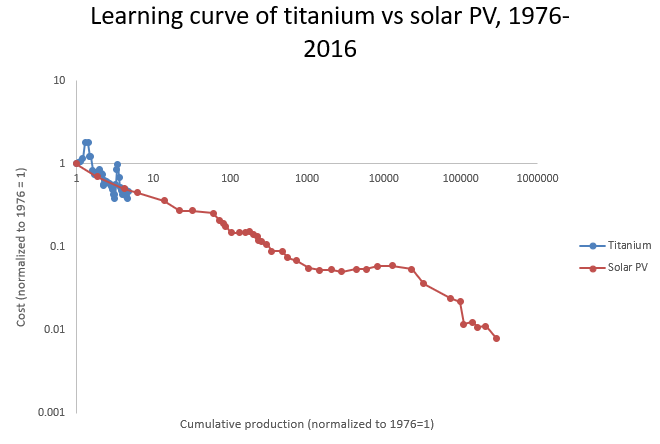
I can see at least two potential factors here. One is that solar PV production has seen a much greater level of government support than titanium production has. In addition to early government support in the 1950s, solar PV also saw US and Japanese government investment in the 1970s, and German government support in the 1990s (via a generous feed-in tariff). Today, governments around the world support solar PV via feed in tariffs, tax credits, and renewable portfolio standards. Continued government subsidies have incentivized increased production, which has resulted in the costs of solar PV continuing to fall. Without that government support, the level of production of solar PV would have been much lower, and its march down the learning curve would have happened much more slowly.
Titanium, on the other hand, has seen much less government support. After subsidies were withdrawn in the late 1950s, the titanium industry has been dependent on large government or commercial aerospace projects. If those fail to materialize (such as when Cold War strategy pivoted from bombers to missiles, or when supersonic commercial aircraft development was canceled), the industry has struggled. If government support of the industry had continued, perhaps it would be farther along on its learning curve.
The other potential factor is technical: while there are many potential process improvements to solar PV manufacturing, there may be substantially fewer potential improvements in titanium production. In the 1950s, it was hoped/assumed that a better process for producing titanium sponge would come along to replace the Kroll process, which is a laborious and energy-intensive batch process that must be done in an inert atmosphere. But such a process has never materialized, and the Kroll process remains the primary method of refining titanium ore. Likewise, turning titanium sponge into metal is an energy and capital-intensive process, often requiring multiple rounds of melting the metal to achieve sufficient purity. This process has also changed little since the 1950s.
Beyond the lack of process improvements, titanium is just fundamentally difficult and expensive to deal with. Turning titanium ingots into bars and sheets is a challenge due to titanium’s reactivity: it readily absorbs impurities, requiring “frequent surface removal and trimming to eliminate surface defects” which are “costly and involve significant yield loss.” Machining titanium is likewise fundamentally expensive. As one report notes:
The hardness that makes titanium so desirable also makes it more difficult to machine than traditional aluminum. This presents a challenge akin to that of machining high-strength steel. However, the process is complicated by titanium’s high reactivity and low thermal conductivity. It is highly reactive and tends to wear tools very quickly, especially at higher temperatures. The low thermal conductivity means that high temperatures can be generated easily in the course of machining. Consequently, titanium must be machined at lower tool speeds, slowing production.
If there are simply fewer potential process improvements in titanium production compared to solar PV, due to the lack of better refining processes and the various physical constraints dictated by its chemistry, there’s less room for costs to fall. With less room for costs to fall, titanium remains an expensive, niche material, which in turn keeps production volumes low.
Titanium is also a story about the importance of serendipity in scientific discovery and technology advancement. Titanium’s biocompatibility, and its usefulness for medical implants, was discovered purely by chance. Studying biocompatibility led to another chance discovery, that of bone conduction of sound. Both of these discoveries led to the development of important medical technology, implants and hearing aids.
Finally, titanium is also a story about the critical role that manufacturing plays in technology development. The knowledge required to turn titanium into a practical technology came from the research lab, but it also came from the factory floor. Using titanium meant understanding its chemical properties, but it also meant figuring out how to forge it, weld it, press it, turn it into fasteners, design parts effectively with it, designing tools to machine it, and a million other shop floor discoveries that came from actually building things with the metal. As one producer noted, “you cannot ship a customer a carload full of tensile properties, nor a box full of Charpy tests. You have to make something out of the material in order to use these marvelous characteristics.” (DTIC 1952). It's only after the enormous effort to build the all-titanium A-12, and the training of thousands of machinists, fabricators, engineers, and other workers to work with titanium, that we begin to see titanium being used in large amounts in military and commercial aircraft. This sort of practical knowledge – the learning that comes from actual production – is critical for technological progress. Technology consists of materials and machines and ideas, but they’re all stitched together by a collection of people that know how to do things. It’s by way of those people doing those things, and understanding them better and better, that new and better technology becomes possible.
Sources
Report of Symposium on Titanium, 1948
Proceedings of the titanium symposium at Watertown Arsenal, 1952
Titanium 1966: Lectures given at Norair symposium
Johnson 1970 - Some Development Aspects of the YF-12A Interceptor
Johnson 1981 - Development of the Lockheed SR-71 Blackbird
Rich 1994 - Skunk Works: A personal memoir of my years at Lockheed
Donachie 1988 - Titanium: A technical guide
Titanium: Past, Present, and Future (1983)
Tylecote 1976 - History of metallurgy
Simcoe 2018 - The history of metals in America
Robarge 2012 - Archangel: CIA’s supersonic A-12 reconnaissance aircraft
Seong 2009 - Titanium: industrial base, price trends, and technology initiatives
Abkowitz - The emergence of the titanium industry
Kroll 1955 - How commercial titanium and zirconium were born
Titanium in aerospace applications (1961)
Great article! I was sorry you didn't mention the Soviet titanium programme, though - according to https://www.cia.gov/readingroom/docs/CIA-RDP86T00591R000200170005-0.pdf, by 1984 the Soviet Union was producing five times as much titanium as the USA, and was the only country to use titanium extensively in the production of submarines. They used titanium in ways that made no economic sense - after the fall of Communism, Western mountaineers sometimes funded expeditions to the former USSR by buying cheap titanium ice screws in-country and selling them at huge markups on their return.
“Titanium metal was essentially willed into existence by the US government”
The entire modern world was willed into existence by the US government, lol.
Telecommunications, semiconductors, nuclear power, metallurgy, petrochemistry, modern agriculture and ecology, genetics, fiber composites, plastics, , mass production and modern logistics.
Basically, after WWII, the Germans birthed modern machine tooling and CNC processes, the Japanese modern shipbuilding and manufacturing/logistics process integration, and the US basically everything else. And almost all of it was a spin-off from defense and government usage, just as the chronograph stemmed from British government prizes all the way back when.