Here’s an idea you see spreading across the internet every so often: that all semiconductor and solar PV manufacturing depends on extremely pure quartz from the town of Spruce Pine, North Carolina. This quartz is used to make the crucibles which hold the molten silicon as it gets turned into silicon ingots, which are then cut into wafers and made into chips. The quartz needs to be very pure to prevent impurities from seeping into the silicon, and Spruce Pine is where this very pure quartz comes from.
Spruce Pine quartz started to get major attention after it was mentioned in Ed Conway’s 2023 book Material World, though it was also mentioned in Vince Beiser’s 2018 book The World in a Grain. Interest spiked following Hurricane Helene amidst concerns that flood damage to the Spruce Pine mines might shut down supply: articles showed up in places like NPR, Forbes, and Axios.
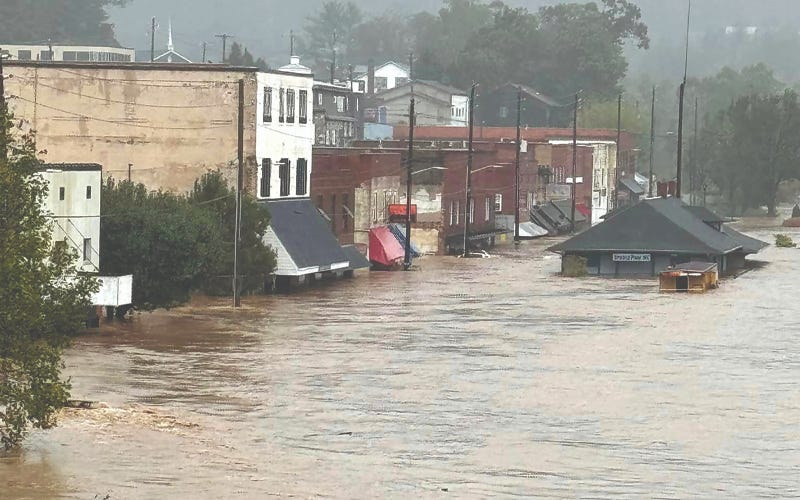
Spruce Pine quartz is often discussed in apocalyptic terms. The implication is that if something happened to the mine, semiconductor manufacturing (and possibly the world economy) would grind to a halt while we scrambled to find a substitute. In his tweet above, Mollick says that “The modern economy rests on a single road in Spruce Pine, North Carolina.” In Material World, Conway quotes an industry expert who says that sufficient damage to the mines “could end the world’s production of semiconductors and solar panels within six months.”
Is this true? Sort of. Quartz crucibles are indeed necessary for most semiconductor manufacturing, and Spruce Pine is where most of this quartz comes from. Spruce Pine quartz isn’t quite an irreplaceable linchpin in semiconductor manufacturing. But alternatives are all some combination of not yet developed, not quite as good, and not quite as cheap. Cutting off the supply of Spruce Pine quartz probably wouldn’t choke off the supply of semiconductors completely, but it would mean yields going down and costs going up. The industry is aware of the bottleneck: new sources of quartz are being developed, and new crucible materials are being investigated. A new crucible material, if found, would have a particularly large impact: not just because it would eliminate the Spruce Pine bottleneck, but because quartz is a major limiting factor in silicon ingot manufacturing, and a new, better material could potentially increase production efficiencies dramatically.
Semiconductors and high-purity quartz

Most modern semiconductors are made from very high-purity silicon: 99.9999999% (known as 9N) pure for microchips, and somewhat less pure (6N-8N) for solar cells. Getting silicon to this level of purity requires multiple refining steps. The process starts with quartz (silicon dioxide), which is reacted with carbon in a submerged arc furnace to produce metallurgical grade silicon (around 98–99% pure). Metallurgical silicon is then run through the Siemens process: silicon is reacted with hydrogen chloride to produce gaseous trichlorosilane (SiHCl3), which then gets liquified, evaporated back to gas, and exposed to heated silicon filaments in the presence of hydrogen gas. The silicon condenses on the filaments via chemical vapor deposition, creating rods of very pure polysilicon, silicon made up of multiple crystals with intersecting boundaries.

These grain boundaries create undesirable defects in the crystal structure, so for microchips and high-efficiency solar panels, we need monocrystalline silicon: ingots of silicon that are one single crystal.1 Monocrystalline silicon is almost entirely made by the Czochralski (or CZ) Process. In the CZ process, polysilicon is melted in a quartz crucible, reaching temperatures of more than 1400 degrees Celsius, and a small silicon seed crystal is dipped into the melt. As the crystal is slowly withdrawn, the molten silicon solidifies around it, aligning with the existing crystal structure and creating a large ingot that’s one single crystal. This ingot will then be sliced into wafers, which are then made into microchips or solar cells.
The high temperature of the process causes impurities in the quartz to migrate into the molten silicon, even through the protective coatings that the crucibles have. Because semiconductors are extremely sensitive to impurities — even a few parts per million of the wrong sorts of atoms can have disastrous effects — the quartz for the crucibles needs to be as pure as reasonably possible.2 Because high-purity quartz is expensive, crucibles are made with a layer of high-purity quartz surrounded by a layer of cheaper, lower-purity quartz.
The quartz crucible not only has a major impact on the quality of the silicon ingot, it’s a major determinant of the cost of ingot manufacturing. High-purity quartz costs on the order $10,000 a ton, and the crucibles themselves cost several thousand dollars apiece. What’s more, crucibles have short lifespans. Over time, the crucible degrades, and chemical changes caused by the high heat cause it to crack after it cools down. Manufacturers can stretch crucible life by pulling multiple ingots from them without cooling down the furnace, but a crucible is still limited to around 400 hours of operation. A CZ furnace will consume on the order of 20–25 crucibles a year, and a large ingot manufacturing operation might have dozens of CZ furnaces. One paper estimated that 30% of the manufacturing cost of monocrystalline silicon ingots was from the crucibles.
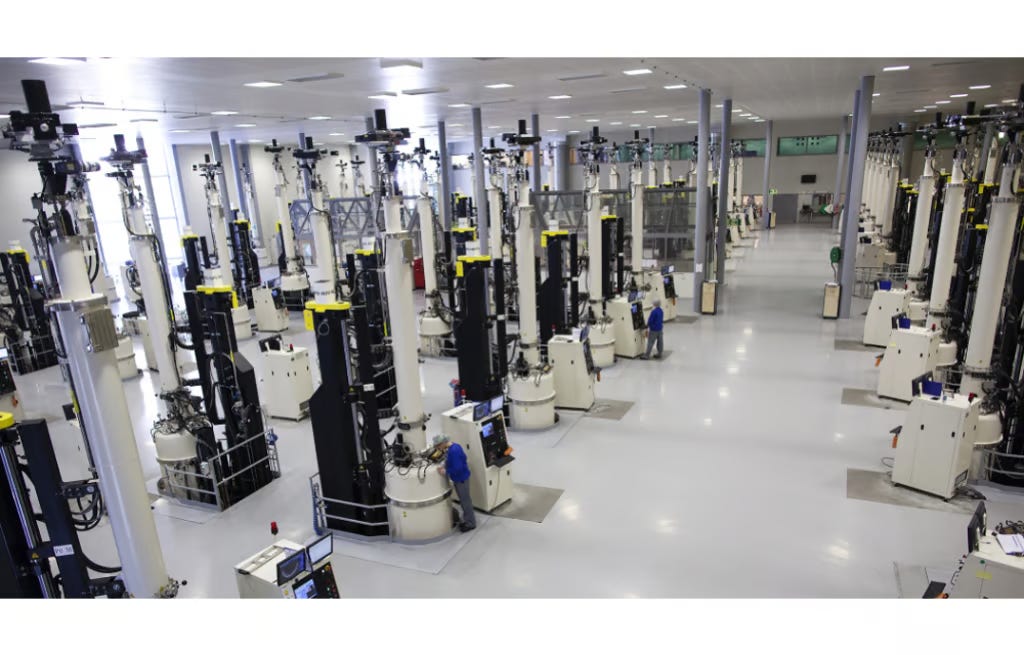
Most of the high-purity quartz for these crucibles comes from Spruce Pine, from two companies that mine there: Covia (formerly Unimin), a subsidiary of Belgian mining company Sibelco, and the Quartz Corp, a Norwegian mining company. Specific numbers are hard to come by (the high-purity quartz industry is extremely secretive), but Spruce Pine is estimated to produce 180–200,000 tons of high-purity quartz per year. If this number is correct, it’s risen substantially over time (not surprising, given rising solar PV volumes and the transition from polysilicon to monosilicon for the cells). In 2013, worldwide quartz shipments were only 80,000 tons (including medium, high, and ultra-pure quartz), and in 2015 total high-purity quartz annual output was estimated to be around 30,000 tons. 200,000 tons isn’t that much material (for comparison, the largest coal mine in the US produced 62 million tons last year), and the Quartz Corp estimates that it has decades of reserves in its existing mines, with even more available in planned future mines.
Spruce Pine quartz is desirable not just because it’s naturally high-purity, but because it’s amenable to further purification, allowing it to reach 99.999% purity or more.3 From The World in a Grain:
Spruce Pine quartz is highly pure to begin with, and purer still after being put through several rounds of froth flotation. But some of the grains may still have what Glover calls interstitial crystalline contamination — molecules of other minerals attached to the quartz molecules. That’s frustratingly common. ‘I’ve evaluated thousands of quartz samples from all over the world,’ said John Schlanz, chief minerals processing engineer at the Minerals Research Laboratory in Asheville, about an hour from Spruce Pine. ‘Near all of them have contaminate locked in the quartz grains that you can’t get out.’
…The very best Spruce Pine quartz, however, has an open crystalline structure, which means that hydrofluoric acid can be injected right into the crystal molecules to dissolve any lingering traces of feldspar or iron, taking the purity up another notch. Technicians take it one step further by reacting the quartz with chlorine or hydrochloric acid at high temperatures, then putting it through one or two more trade-secret steps of physical and chemical processing.
Spruce Pine isn’t the only source of natural high-purity quartz. China produces around 5,000 tons annually, and is hoping to scale up its operations to 20,000 tons or more. Norway and Russia both produce a small amount, and historically Brazil was a major supplier. And there are other potential sources around the world being investigated in Canada, South Carolina, Sri Lanka, and Australia. But for now, Spruce Pine is the source of 70–90% of the world’s supply. Damage from Hurricane Helene doesn’t yet seem to have disrupted semiconductor manufacturing (and the mines seem to have at least partially resumed operations), possibly because manufacturers keep a buffer of crucibles in stock.4
Alternatives to Spruce Pine quartz
But Spruce Pine being the primary source of high-purity quartz doesn’t make it irreplaceable. In addition to efforts to find new sources elsewhere, there are a variety of ways that it could be substituted, though they’re not without difficulties.
One option would be to use synthetic quartz rather than naturally mined quartz. Synthetic quartz can in fact be made far purer than natural quartz. The downside is that synthetic quartz is much more expensive, perhaps on the order of 5–10 times the cost of natural high-purity quartz. Chip manufacturers could probably absorb this cost, given that the silicon ingot is a relatively small fraction of the cost of a microchip, and as I understand it some chip manufacturers already use synthetic quartz crucibles, sold by companies like Japan Super Quartz. For solar PV, however, this cost increase would be a huge burden.
Similarly, manufacturers could use alternative, lower-purity quartz sources and refine them more to achieve the necessary levels of purity. This would also be more expensive, and the resulting quartz might still have more impurities than Spruce Pine quartz, causing lower yields and thus even higher costs, but it’s also probably doable. A post from SemiAnalysis argues that worries about Spruce Pine quartz are overblown specifically because of the availability of synthetic quartz and the possibility of refining lower-purity sources.
Longer term, there’s the possibility of finding alternative crucible materials. Quartz’s ability to withstand high heat, its low coefficient of thermal expansion, and its relative unreactivity with molten silicon are difficult to substitute, and quartz crucibles are currently the only option for silicon semiconductor manufacturing (though if you use other materials like germanium or gallium nitride, there are more options).5 But researchers are exploring alternative crucible materials like silicon nitride and silicon carbide. Because quartz is a major bottleneck limiting crucible lifetimes, a novel, higher-performing material that would allow CZ furnaces to operate for longer would be a major advance in ingot manufacturing.
It’s also technically possible to manufacture high-purity silicon ingots without crucibles at all, via the Float Zone process. In this process, an ingot of polysilicon is slowly remelted by a ring-shaped radiofrequency heater that travels along the length of the ingot. As the silicon melts and resolidifies around a seed crystal, impurities migrate out, and an ingot of monocrystalline silicon is produced.
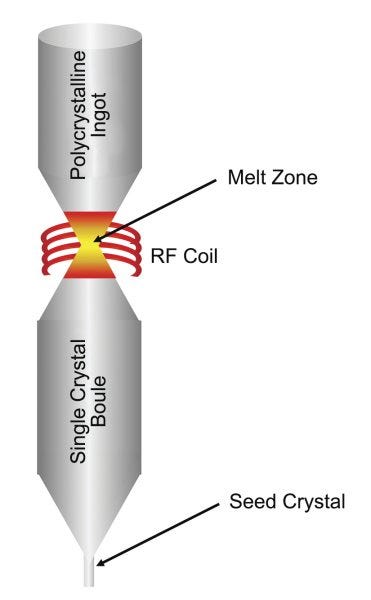
Because the float zone process doesn’t require the silicon to touch a crucible at all, it can achieve even higher purities than the CZ process. It’s used for things like power electronics where such purity is required. The float zone process, however, is more expensive than the CZ process, partly because it requires large polysilicon ingots rather than smaller chunks of polysilicon: this website from a semiconductor manufacturer indicates that a float zone wafer is about twice the cost of a similar CZ wafer.
More critically, the float zone process is limited in how large an ingot (and thus wafer) it can produce. It maxes out around six inches in diameter, while since the early 2000s leading edge semiconductor nodes have used 12-inch wafers. Size limitations would mean even higher costs, both because smaller wafers means fewer chips processed at a time, and because all existing semiconductor manufacturing equipment would have to be modified or replaced to handle smaller wafers. Realistically, a large-scale transition to the float zone process probably isn’t feasible outside the most dire of circumstances.
Conclusion
Spruce Pine is indeed a key choke point in the modern semiconductor manufacturing landscape, but it’s not quite an irreplaceable, load-bearing column supporting all of the modern economy. It’s closer to occupying a relatively unique niche in a price-performance landscape: there are alternatives, but they’re all some combination of not as good, not as cheap, and not yet developed. Conway more or less confirms this in a recent Substack post:
After all, as I wrote in the book, it’s not as if there’s no high-purity quartz elsewhere. It’s more that Spruce Pine has a near unique combination of purity, availability and price. There are mines in Russia and Brazil, not to mention China, which already produce lots of high-purity quartz. There are some companies which are able to make high purity quartz synthetically.
So yes, in the long run, this will not be the end of the world. This will not ‘end’ semiconductor or solar cell manufacture. Then again, as someone once said, in the long run we’re all dead. In the short run, actually ramping up that alternative production will take some time and, just as importantly, some cost.
Most interesting to me isn’t the Spruce Pine bottleneck, but the limits that quartz crucibles place on silicon ingot manufacturing more generally. Finding an alternative crucible material would be a major win in helping solar PV costs continue to fall, and I’ll be interested to see if any progress gets made on new materials as solar PV adoption continues to rise.
Historically, solar panels were often made directly from polysilicon, but today they’re almost all made from monocrystalline silicon.
Quartz is silicon dioxide, or silica, a molecule consisting of two oxygen atoms bonded to a silicon atom. The molten silicon is hot enough that the crucible itself will slowly dissolve and transfer oxygen into the melt, and dealing with oxygen impurities is another major challenge of the CZ process.
Spruce Pine quartz that doesn’t quite make the purity cut gets used for sandtraps in high-end golf courses.)
There are claims that a 2008 fire at Spruce Pine, which “all but shut down” high-purity quartz supplies, are responsible for a spike in polysilicon prices. It’s not clear to me that this is actually true, given that the CZ process produces monocrystalline silicon, not polysilicon (unless there was also a shortage of crucibles for directional solidification furnaces).
One paper laments that high-temperature silicon “reacts with almost everything.”
Fascinating article. I found it especially noteworthy that while the mines are in the US, they're run by foreign companies. Supply webs are complicated, something I think people talking about onshoring critical production don't fully appreciate.
Next, I want to know more about how quartz underground gets turned into crucibles. I was envisioning chunks of quartz getting turned on a lathe. I can't see how that would work. What's the actual process? If it involves casting the quartz, what do you melt _that_ in? A superquartz crucible? Is it quartz elephants all the way down?
The image of a cross-section of a double-layer crucible is actually illustrating a combination of mechanical properties, not relative purity. See https://www.sciencedirect.com/science/article/pii/S2666539522001043. This paper also answers Pete Smoot's question rather exhaustively.