Tunneling is an important technology for modern civilization, as a tunnel is often the only reasonable way to create a direct path between two points. When the Hoosac tunnel was completed in 1875, it turned a difficult, 20-mile railroad route along “precipitous grades” into a direct 5 mile route, connecting Boston with the Upper Hudson Valley. Large infrastructure projects such as hydroelectric dams often require tunnels to function. The Hoover Dam required more than 3 miles of tunnels 56 feet in diameter to divert the Colorado River around the construction site. And a tunnel can be used to create new land beneath dense urban areas, making it possible to build large-scale horizontal infrastructure like sewers or mass transit that wouldn’t be feasible to build above ground.
A common way of building a tunnel today is with a tunnel boring machine (TBM), particularly in urban areas where other construction methods such as drill-and-blast or cut-and-cover would be too disruptive. Of the 89 transit projects around the world that required tunneling in a dataset compiled by Britain Remade, 80 of them used TBMs. But tunnel boring machines are a comparatively modern construction technology. The first successful rock tunneling machines weren’t invented until the 1950s, and into the late 1960s most tunneling was done using other construction methods. But as TBMs have improved, they have increasingly been the method of choice for tunneling through a wider variety of ground conditions. And while many construction tasks have resisted automation and mechanization, tunneling machinery has steadily gotten more automated, to the point where a modern TBM is akin to a mobile factory that burrows through the earth and constructs a tunnel behind it.
What is a tunnel boring machine?
There are a variety of different types of machinery used to excavate tunnels. “Tunnel boring machines” use a rotating cutting head that engages with the entire face of the tunnel at once. This contrasts with something like a roadheader, which uses a much smaller cutter that moves back and forth over the face of the tunnel.
(The terminology around TBMs is somewhat non-standard. In some cases, any sort of mechanized tunnel shield gets referred to as a TBM. Other times TBM is used strictly for rock tunneling machines, and don’t include machines that tunnel through soil.)
All TBMs share several basic features. At the front, a rotating cutting head excavates the face of the tunnel. Excavated material, known as “muck," passes through openings in the cutting head and is removed by some sort of conveying system. To advance, a TBM uses large hydraulic cylinders to push off against either the excavated sides of the tunnel (in “gripper” TBMs) or against a prefabricated tunnel lining that has been installed around the inside of the excavated tunnel. Gripper TBMs are limited to use in rock, whereas TBMs that push against a segmented tunnel lining can also be used in soft ground. In soft ground, all this equipment is encased in a cylindrical structure known as a “shield," which supports the sides of the tunnel while it's being excavated. In rock, this shield may or may not be used.
TBMs can be further divided by whether some kind of support for the face of the tunnel is required. “Closed” TBMs use a fluid or other material behind the rotating cutting head of the TBM to prevent the face of the tunnel from collapsing, or from water intruding as the tunnel is bored. “Open” TBMs, on the other hand, don’t have this support, and can be used where the tunnel face is strong enough to support itself during excavation and where groundwater intrusion isn’t a problem. The chart below shows this breakdown:
TBMs have evolved along two parallel paths of technological development. The first is the development of machines for tunneling through soil and soft ground, and the second is machines for tunneling through rock. Today, machines of both types get categorized as tunnel boring machines, and the lines between them are sometimes blurry. But they evolved separately to solve different sorts of problems. In soft ground, excavation was comparatively easy, and the primary problem was to prevent the tunnel from collapsing or flooding as it was dug. In rock, by contrast, the tunnel could often support itself temporarily while it was being excavated, and the primary problem was building a machine that was strong enough to cut through the rock.
Soft ground tunneling
Soft ground TBMs evolved from unmechanized tunnel shields. The first tunnel shield was designed by Marc Brunel, father of famous engineer Isambard Kingdom Brunel and an accomplished engineer in his own right1, and built by Henry Maudslay for tunneling under the Thames in 18252. Brunel’s shield, which was inspired by the action of shipworms boring through the wood hulls of ships, consisted of a large cast-iron structure, 38 feet wide by 22 feet tall, which was broken into 12 separate “frames,” each consisting of three individual compartments stacked on top of another. Within each compartment was a series of horizontal boards, called “poling boards," that were placed against the face of the tunnel. A worker in the compartment would remove a board, dig out the earth behind it to a depth of around 6 inches, and then proceed to the next board. Once all the soil behind the boards in a frame had been dug out, that section of the shield would be advanced forward using screw jacks, and the process would repeat. Behind the shield, masons would construct the brick lining around the sides of the tunnel, which prevented the tunnel from collapsing and provided a structure for the shield to push off against.
When the Thames Tunnel was completed, it was the first tunnel under a body of water in the world. But the project proved to be incredibly difficult, encountering “almost overwhelming problems” (West p115). Excavation was slow, advancing at around 8 feet per week on average, and the tunnel flooded repeatedly. Gas occasionally filled the tunnel, which caused “collapse and blindness of the workmen” (West p109), and at one point the entire shield needed to be replaced. The tunnel wasn’t completed until 1843, 18 years after it was started, and it was never a commercial success, though it is still in use today. Tunneling via shield wasn’t tried again for over 25 years.
The next major attempts at tunneling with shields took place in 1869. That year, Alfred Beach in the US used a cylindrical tunnel shield to surreptitiously dig an 8-foot diameter tunnel for a pneumatic railway in New York (leading to use of the term “Beach Shields” in the US). The same year, Peter Barlow, who had patented his own design for a cylindrical tunnel shield, began construction on another tunnel under the Thames for the Tower Subway. Because so many builders remembered the difficulties of Brunel’s tunnel, none were willing to attempt another one, and James Greathead, an engineering apprentice to Peter Barlow, opted to undertake it.
Greathead designed a shield for the project based on Barlow’s ideas, and introduced a number of other innovations to the tunnel construction process. Instead of a brick tunnel lining, Greathead used cast-iron segments bolted together. Not only could these be installed much faster than brick, but could immediately support the tunnel sides and withstand the reaction from the shield jacks once in place, whereas a brick lining required waiting until the mortar had set. Cast iron segments also greatly reduced subsistence of the ground above the tunnel, which often damaged buildings above tunnels constructed with brick linings. (Setting the prefabricated cast-iron segments became even faster on subsequent tunnels when Greathead developed a mechanical system for lifting the segments into place.) To fill the gaps between the lining and the sides of the tunnel, Greathead injected grout into the space. On later tunnels, Greathead would invent a special “grout pan” that made this injection easier by using compressed air.
Greathead’s Thames tunnel proved to be much more successful than Brunel’s, taking just 1 year to complete compared to Brunel’s 18 (though Greathead’s tunnel was much smaller). Whereas Brunel’s shield advanced at around 8 feet per week, Greathead’s advanced at 8 feet per day. Greathead went on to build several other subway tunnels beneath London, and ‘Greathead’-style tunneling shields became popular around the world. A cylindrical tunnel shield, a prefabricated segmental tunnel lining erected mechanically, and grout injection between the prefab lining and the sides of the tunnel all remain standard practice on tunnel construction today.
Mechanization
Until this point, the actual excavation work of tunnel construction was done manually, by laborers using picks and shovels. Shields with mechanical excavation equipment were first patented in 1876, but the first successful machine was designed by John Price in 1896, and steadily improved over the next several years3. Price’s improved machine consisted of a rotating disc with 6 bucket-shaped cutters mounted around the edge attached to a cylindrical shield 3.86 meters in diameter. As the disc rotated, the cutters would scrape away the soil, feeding it into a conveyor for removal.
Price’s initial machine was not particularly successful, but the improved version became “an immediate success” (West p279), achieving excavation rates up to 180 feet per week. Price Shields were not only faster than non-mechanized Greathead shields, but also required less labor (10 workers vs 13), and were found to be “exceptionally reliable." Price machines became the standard for soft-ground tunnel excavation for the next 50 years, and are the ancestors of modern soft-ground tunnel boring machines4.
Tunnel support
Another important development in soft-ground tunneling machines was in the methods used to support the face of the tunnel as it was being excavated. As we’ve noted, Brunel used manually positioned wood boards to support the tunnel face. On Greathead shields, these were replaced by a steel wall with doors in it called a diaphragm. Workers would open the doors to get access to the tunnel face and excavate the soil.
Neither of these solutions prevented the intrusion of water from the tunnel face, which made tunneling through permeable soil below the water table difficult. To deal with the problem of water intrusion, tunnelers turned to compressed air. By installing an air lock at the tunnel exit, and pressurizing the air in the tunnel up to several times atmospheric pressure, water would be kept out. Compressed air was first used on a drainage tunnel built in Antwerp in 1879, and was first used in conjunction with a tunnel shield in 1888 for a railroad tunnel under the St. Clair River. By the 1890s, tunnel shields and compressed air were standard practice for below-river tunneling.
Compressed air continued to be used throughout the 20th century. Construction of the LA Metro in the 1980s, for instance, used compressed air in conjunction with digger shields to excavate some of its tunnels. And compressed air is still used in some circumstances today, such as when workers need to access the cutting head of a closed TBM to replace worn out cutting tools. But there are drawbacks. For one, there are health risks to working in compressed air. Decompression sickness/”the bends” is a serious and potentially fatal condition when dissolved gasses bubble out from the body during decompression. Today, the risk of this has been greatly reduced by using proper decompression procedures, but decompression sickness was incredibly deadly before they were discovered. During construction of the Hudson River Tunnel in 1889, 25% of the workers died from decompression sickness. Long-term exposure to compressed air can also result in bone necrosis.
The health problems of working in compressed air were partially addressed with the development of shields that used it just behind the cutting face (rather than the entire tunnel). A shield of this type was first used to excavate a section of underground Paris railway in 1962 (West p180). But this didn’t address another problem. To prevent the tunnel face from collapsing and water intruding, the force of the air pressure needs to balance the force pressing inward from the face of the tunnel. This pressure is due to the weight of material pressing down from above, and so it gets larger the further down you go. Thus at the top of the tunnel the pressure is less than at the bottom. Air pressure, on the other hand, is essentially uniform at both the top and bottom of the tunnel. The air pressure is thus higher than the pressure from the tunnel face at the top of the tunnel, and lower than the pressure at the bottom.
This means that, at the bottom of the tunnel, water would constantly want to leak in, and at the top, air would want to leak out. If the ground is permeable enough for the air to reach the surface, this could create a “blowout," a dangerous condition where air suddenly escapes, and water suddenly rushes in. In one blowout while tunneling under the East River in New York City in 1905, a worker was “blown into the hole, through the silt of the river bed, and upwards through a further 15 feet of water to the river surface," where he miraculously emerged unscathed. (West p145)
To address this, tunneling machine builders developed other ways of supporting the face of the tunnel during excavation. One option was to use bentonite slurry, a heavy liquid clay which had long been used to support the sides of oil wells while they were being drilled5. Because it was a heavy liquid, the pressure from the bentonite would vary with height in the same way as the pressure from the tunnel face it was resisting, and thus avoided the pressure differential problems of compressed air. The first bentonite slurry TBM was invented in 1964 by John Bartlett. Behind the cutting head was a pressurized chamber that could be filled with slurry. Excavated soil would mix with the slurry, and then be pumped out of the tunnel to the surface. The soil would then be filtered out and disposed of, and the bentonite would be stored for reuse. To prevent the slurry from leaking into the TBM from the sides of the shield, a “tail seal” was added around the edge of the shield. By disconnecting the bentonite pump and other equipment, and replacing it with a normal conveyor, Bartlett’s machine could also operate without fluid support, which let it operate in different sorts of ground. Similar slurry machines were developed in the late 1960s in Japan by Mitsubishi, and in the 1970s in Germany by Wayss and Freytag. By the end of the 1970s, slurry TBMs were in common use.
Another way to support the face of the tunnel is with the excavated earth itself. By letting the earth accumulate in a chamber behind the cutting head, it can be used to balance the pressure from the tunnel face. These are known as Earth Pressure Balance Machines, or EPB machines/EPBMs, and were first developed in Japan in the 1960s, in an attempt to find an easier way to cope with environmental regulations. Slurry machines, which treated the excavated soil chemically to separate the bentonite for reuse, had difficulty complying with these laws. EPBMS did not require this chemical treatment (and thus were environmentally friendlier than slurry machines), and eliminated the slurry treatment and pumping system. EPBMs are also significantly faster than slurry machines. EPBMs do, however, often inject foam or polymer into the soil ahead of the cutting face to modify the soil properties to make it easier to excavate. The first EPBM was used in 1974, and today EPBMs are the most common type of TBM for soft-ground tunneling.
Another important development in soft-ground tunneling was precast concrete tunnel linings, which first were used widely in Europe after WWII (since their iron industry had been destroyed during the war), and by the 1970s and 80s had spread to the US (US tunnels book). Initial precast linings used identical segments, but the development of “wedge blocks," where one segment of a ring was tapered and jacked into place last, greatly increased how fast tunnel linings could be installed, and allowed “outstanding rates of tunnel progress to be achieved” (West p169). Today, wedge-shaped key segments are still widely used for tunnel linings, but there are a variety of different shapes of lining segments in use.
Rock tunneling
Tunneling through rock proved more difficult than tunneling through soil. And while the only alternative to mechanized soil tunneling was laborious hand excavation, rock tunneling had a successful technology in the form of the drill and blast excavation, which was first developed in the 1850s (West p31). Workers would drill holes into the face of the tunnel, fill them with explosives, blast apart the rock, and repeat. As the technology for drill and blast improved (from nitroglycerine explosives to dynamite, and from hand drills to compressed air drills)6, there was comparatively less incentive to develop mechanical rock tunneling machines, and successful ones didn’t appear until the 1950s.
The first attempt at a rock tunneling machine was by Henri-Joseph Maus in 1845. Maus’s machine consisted of 118 chisels arranged in several rows, driven by a series of cables connected to a water turbine outside the tunnel. The chisels would deliver 150 blows per minute to the rock, while water jets would clear out the debris and keep the chisels cool. A prototype of Maus’ machine was built in 1847, which Maus estimated could excavate at a rate of 18 to 24 feet per day. But the tunnel project it was built for – a railway through the Alps – was canceled, and the machine was never used.
Another early attempt at a rock tunneling machine was by Charles Wilson for the Hoosac tunnel in 1851. Wilson’s machine consisted of a rotating 24-foot cylinder powered by steam, with a series of rolling cutters mounted to it. The machine would cut a groove around the outside of the tunnel, and a 2-foot circle in the middle. Once the inner and outer grooves were cut, the rock between would be removed via drill and blast. Wilson’s machine was built, but only managed to excavate 10 feet before it was abandoned and sold for scrap (Stack p146, West p230). The Hoosac tunnel was ultimately excavated by the drill and blast method.
Over the next 70 years, “a great many tunneling machines were designed and patented” (West p231), but few were built, and the ones that were built weren’t successful. By the 1930s, “after the repeated failures which had attended the introduction of most rock tunneling machines, interest in their development tended to wane” (Stack p230), and no machines were built until the 1950s.
The first successful rock tunneling machine was built in 1954 by James Robbins for the Oahe Dam project in South Dakota. The key innovation on Robbins’ machine was the disc cutter. Previously, most attempts at rock tunneling machines used drag picks, which are sharp steel tools that cut the rock by being dragged across it. The disc cutter, on the other hand, works by being pressed against the face of the rock, freely rolling over its surface as the head of the boring machine rotates and crushing a narrow channel of rock beneath it. A disc cutter does not work like a saw, spinning rapidly to cut a channel through the rock. It merely gets pressed against the rock until the rock beneath it is crushed, forming a channel beneath the cutter. When this channel gets deep enough, the force from the cutter causes fractures to occur between adjacent troughs, spalling off the remaining rock.
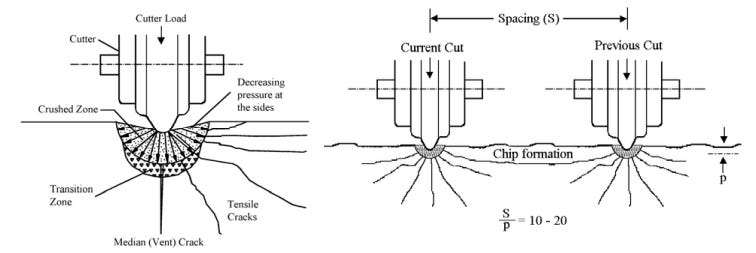
Robbins first rock boring machine for Oahe used both drag picks and disc cutters, but the machine worked poorly, due in part to the frequent breakage of drag picks. After the machine was redesigned, it was found that the machine actually worked better with disc cutters alone. Robbins’ redesigned boring machine was able to achieve excavation rates of almost 200 meters per week on the Oahe project, five times as fast as drill and blast, and Robbins remains a leading manufacturer of TBMs of all types today.
Robbins’ first TBM was only capable of boring through relatively soft rock. Early attempts to tunnel through harder rock, such as on the Alkirk Tunnel in 19627, weren’t successful, and harder rocks remained the domain of drill and blast. But over time, the machines improved, partially due to the development of larger, stronger cutters capable of handling more force (and lasted longer before needing to be replaced, increasing machine efficiency). The cutters on early TBMs were 11 inches in diameter, but by the late 1980s, 19-inch diameter cutters made of a specially designed tool steel had been developed. Disc cutters remain the standard cutting tool for rock TBMs, and are also used on soft-ground TBMs8.
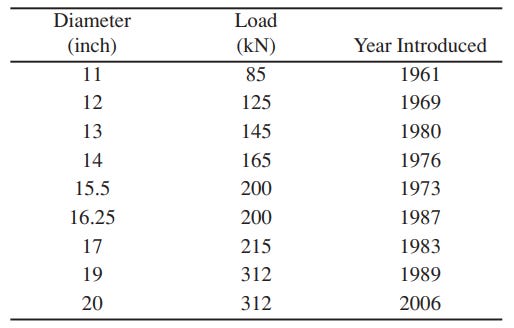
Flexibility
Historically, most tunnel boring machines were designed to tackle the ground on a particular project, and many early tunneling successes bored ground that was particularly easy to tunnel through. Greathead’s Thames tunnel was bored through a stratum of London Clay that was “an almost perfect medium for shield tunneling” (West p117), and later London Tube segments were set at a level specifically chosen to allow as much tunneling as possible in London Clay. Robbins early rock TBM successes were likewise only possible because of how soft the rock being tunneled through was9. Using a TBM required knowing much more about the ground to be drilled through than something like drill and blast, and many machines couldn’t cope with highly variable ground conditions (say, needing to tunnel through both soft soil and hard rock).
But over time, TBMs have become increasingly capable at tunneling through a broad array of ground conditions. Often this has resulted in blurred lines between soft ground TBMs and rock TBMs. In 1972, for instance, Robbins developed the double shield rock TBM, which can tunnel through fractured rock by using a shield to protect the TBM machinery from rock collapse. During this period, TBMs also began to be used to install segmented tunnel liners on rock tunnels. In 1985, Herrenknecht developed the mixshield, which can change from open (no face support) to either slurry or EPB modes. Manufacturers such as Robbins have also developed machines that can convert between soil/EPB and rock tunneling. Today, there are almost no ground conditions that can’t be handled by some type of TBM.
TBMs have also been developed to handle a wider variety of tunnel sizes. The maximum size of tunnel shields and TBMs have steadily increased over time (though Brunel’s shield had a very large equivalent diameter). In 1888, the St. Clair River was an unusually large tunnel shield, at over 6 meters in diameter. Today, the largest TBMs have a diameter almost 3 times this size.
TBMs that can excavate smaller tunnels have also been developed. In the 1970s, mini rock TBMs 2 meters in diameter first appeared (stack), and today manufacturers produce rock boring machines as small as 0.6 meters.
Speed
Technological advances have allowed tunnel boring machines to get faster over time. Brunel’s tunnel shield in its best week managed to tunnel around 14 feet, or just over 4 meters. 40 years later, Greathead achieved a weekly tunneling rate that was nearly 4 times that with his tunnel shield, which more than doubled again with the introduction of Price’s mechanized shield at the end of the 19th century. Today, rock tunneling machines have achieved tunneling rates of over 700 meters per week, and soil tunneling machines have achieved rates of over 200 meters per week, though this is dependent on the size of the TBM10.
Of course, it's hard to talk about tunnel boring machine speeds without referencing The Boring Company, the Elon Musk company founded in 2016 with the goal of greatly increasing tunneling boring speed. Though it initially used a TBM (“Godot”) built by Lovat, their current TBM, an EBP named “Prufrock," was designed in-house, and has been used to dig tunnels for the Las Vegas Loop.
The Boring Company has announced several different tunnel speed goals. One of the most publicized is to beat a snail, or around 140 meters per day/980 meters per week. Its Prufrock TBM is apparently designed to achieve speeds of a mile/1609 meters per week. And its “medium term goal” is to achieve tunneling rates of 7 miles per day, or nearly 80,000 meters per week (100 times faster than the fastest TBMs). The Boring Company aims at achieving these with a variety of methods, including more powerful machines, continuous tunneling rather than stopping for maintenance and to set the lining (which current TBMs often must do), launching directly from the surface (avoiding a time-consuming excavation and machine setup process), and eliminating the rails used to deliver tunneling lining segments.
(There seems to be some inconsistency in how these speeds are described. Metaculus describes “snail speed” as 140 meters per day, or 980 meters per week assuming 24/7 operation. But The Boring Company describes 1 mile/1609 meters per week, as “4-5 times slower than a snail”. They also describe Prufrock’s 1-mile per week goal as “6 times faster than their previous generation TBM (Godot+)”, which would be at least 268 meters per week for Godot+. This, I believe, would be a world-record speed for a soft-earth machine if it had actually been achieved, but I haven’t found any indication that it has.)
These goals are not that far off the historical trajectory of speed advancement in TBMs. Between 1825 (the first use of Brunel’s shield) and 1966, maximum weekly TBM speed increased by about 3.5% per year on average. Extending that same rate out to 2030 would yield a speed of around 5000 meters per week, somewhere between the Boring Company’s medium-term goals and design speed for Prufrock, and about 7 times faster than current maximum weekly TBM speeds.
But the company is currently nowhere close to achieving it. The recently-excavated Las Vegas loop took 10 weeks to tunnel 716 meters. Assuming 2-3 weeks were needed to prep the site and deploy the machine (remember that it is designed for quick deployment), that's a tunneling rate of about 90 meters per week, which TBMs have been achieving for more than 50 years, and is less than 1/10th the speed of their lowest goal of beating the snail. And this rate was achieved with a relatively small machine, in comparatively easy ground to tunnel through.
It's also unclear whether the Boring Company’s proposed improvements will work. Most of these suggestions, such as eliminating rail and continuous operation, are either already done by TBM operators or are being actively pursued by them. Being able to tunnel directly from the surface without needing a long and involved excavation is likewise a capability that TBMs have had for many years. And it’s unclear whether or how the Boring Company will address issues that limit how fast soft-earth tunneling machines can excavate, like settlement and ground heave.
A possible bigger benefit of the Boring Company is the structure of the company. Unlike other companies, which are in the business of selling TBMs, the Boring Company is in the business of selling tunnels, and happens to use its own tunnel boring machines. This vertically integrated structure changes the incentives at work – while most tunnel contractors are rationally risk averse and are reluctant to adopt new technology, the Boring Company will be incentivized to use its own machines, and have the opportunity to rapidly iterate and improve on their design in a way that machine manufacturers selling to risk-averse contractors don’t have. Similarly, SpaceX had the option to learn by blowing up rockets, in a way that risk-averse programs like NASA would never be able to.
Nevertheless, it's still far too early to determine whether the Boring Company will be able to achieve its goals. It's worth noting that around 40% of the betters on Metaculus are predicting that the Boring Company will not even achieve snail speed by 2027.
Conclusion
The arc of tunnel boring machinery looks much more like the progression we see in other industrial areas, and that we don’t often see in construction. Construction operations often remain craft-based and labor intensive, and have been performed in similar ways for decades (or centuries). With tunnel boring machines, we see gradual automation and “factoryization," where the work increasingly takes place in a highly mechanized, factory-like environment. New technology comes along and displaces the old technology, even in an environment of high risk aversion. And the process gradually converges on the “continuous flow," where the machine continuously transforms solid ground into a lined tunnel, and continuously removes excavated material with the use of conveyors, the same sort of development we see in things like Ford’s assembly line, chemical process industries, and the Toyota production system.
Thanks to Brad Grothen at Robbins TBM for helpful conversations on TBM technology. All errors are my own.
Sources
Books
Stack (1982) - Handbook of Mining and Tunneling Machinery
West (1988) - Innovation and the Rise of the Tunneling Industry
Roach et al (2017) - The History of Tunneling in the United States
Maidl et al (2012) - Mechanized Shield Tunneling
Maidl et al (2008) - Hardrock Tunnel Boring Machines
Wagner and Shulter (1996) - Trends in Design and Construction of Mechanized Tunneling
Bickel et al (1996) - Tunnel Engineering Handbook
Other
Rapid Excavation - Problems and progress; proceedings of the 1968 tunnel and shaft conference
Proceedings of the North American Tunneling Conference (2002)
Proceedings of the International Conference on Tunnels and Underground Structures (2000)
Underground construction in modern infrastructure conference proceedings 1998
Tunnelling '82 : papers presented at the third international symposium
FHWA (2009) - Technical Manual for Design and Construction of Road Tunnels - Civil Elements
Roby et al (2010) - The Current State of Disc Cutter Design and Development
Herreknecht (2019) - Innovations in Mechanized Tunneling Since 1970
Herreknecht (2012) - Newest Technology and Trends in Mechanized Tunneling
In addition to inventing the tunnel shield, Marc Brunel also designed and built a series of machines for mechanizing the manufacturing of pulley blocks for the British navy, an early example of mechanized manufacturing.
Though Brunel had originally designed it to tunnel under the Neva River in Russia.
Early improvements included a change from mounting the drive to the center shaft to having the drive mounted to the inside of the shield, and the addition of the conveyor.
Besides TBMs, there are also other styles of mechanized tunnel shield excavation. “Digger shields," for instance, consist of a digging boom (a backhoe-like device) mounted inside a shield. Though these are less commonly used today, historically they were much more popular. Much of the Los Angeles Metro, for instance, was excavated using digger shields.
Bentonite clay is actually thixotropic, which means it gets less viscous, and more liquid, when mechanically stressed.
By the 1960s, drill and blast could achieve excavation rates of over 30 meters per week.
In Japan, early use of rock TBMs also weren’t successful.
Any technology will consist of a nested hierarchy of sub-technologies, each of which will have its own progression. There have been a series of incremental developments in cutter technology, for instance - optimal cutter spacing, better bearings, different designs of the head, different attachment mechanisms, different seals, etc.
Prior to tunneling through the soft Oahe dam rock, Robbins successfully used a rotary-style TBM to tunnel through Pierre Shale that was 1/100th as strong, and thus not truly considered “rock” at all.
Great article! We also have different shapes of TBM these days like the "double O" and square designs!
https://en.wikipedia.org/wiki/Tunnelling_shield#/media/File:Shielded-machine.JPG
I recently came across a very nice exploration of modern tunnel construction here: https://www.youtube.com/watch?v=6AV2NcyX7pk