The big question about Artificial Intelligence, other than whether it will destroy human civilization, is the effect it will have on employment. Large language models already seem poised to automate large fractions of the work in certain industries, and the technology is only getting more capable.
There are, broadly, two schools of thought about this issue, what we might call the optimists and the pessimists. The optimists note that we’ve been automating work for hundreds of years, and it has yet to result in sustained, large-scale unemployment. Certain jobs, like telephone switchboard operators or dockworkers, get automated away or see drastically reduced employment as technology improves, but on an economy-wide basis workers get reallocated to other jobs that still require human labor. In this view, AI will simply be a repeat of this historical pattern.
The pessimists, on the other hand, think that this time will be different. If an AI can do everything, or nearly everything, that a human can do, and do it for cheaper, there’s no longer any economic reason to hire a human. In this view, AI will structurally reduce the demand for all human labor, the same way that cars structurally reduced the demand for all horse labor.
As the saying goes, it's hard to make predictions, especially about the future. It's not yet clear what the ultimate impact of modern AI technology will be. But one thing we can do to try and understand the problem is take a closer look at the mechanics of how automation has happened historically. Understanding the specifics of how automation has happened in the past might give us clues as to how it will proceed in the future.
A good job for drilling down into the specifics of automation is welding. Welding today exists right on the “automation frontier” — some industries, like car manufacturing, have automated nearly all their welding, while others, like construction, have automated very little of it. Welding also encompasses a fairly narrow set of tasks that have changed comparatively little over a long period of time. This makes it easy to understand what, specifically, is being automated, how automation capabilities have advanced, and how advancing automation has affected welding employment.
How welding works
There are two main types of welding to consider when talking about welding automation.
The first is resistance welding. With resistance welding, the parts to be welded are pressed between two electrodes. Current then runs across the electrodes, and the electrical resistance of the metal between them causes the parts to heat up, melt, and weld together. Resistance welding can be done as “spot welding” (where just a single point is welded), or as “seam welding” (where a continuous seam is welded). Resistance welding is generally used to join thin materials, such as sheet steel.
The second type of welding is arc welding. With arc welding, an electric arc is created between a metal electrode and the metal to be welded, and the heat of the arc melts the metal. The arc is then moved along the joint to be welded. There are several different types of arc welding, such as MIG, TIG, and SMAW, which differ in things like the material of the electrode, whether the electrode is consumed in the process, and how the weld is shielded from the air.

In addition to these, there are other types of welding such as forge welding, laser welding, friction welding, and oxyacetylene welding. But for the last 100 years most welding, and most welding automation, has been done with either resistance or arc welding.
A brief history of welding automation
Machines to automate the welding process were built very early. Resistance and arc welding were both developed in the late 19th century, and by the early 20th century automatic machines had been built to do both. Resistance-welding machines were particularly simple to build, as all the machine had to do was position the welding electrodes correctly with respect to the parts to be welded, press them together, and run the current.

Automating arc welding was more complex. Unlike resistance welding, arc welding had a variety of parameters that needed to be controlled such as the feed rate of the welding electrode, the traveling speed of the machine, the current and voltage, the distance and angle the electrode was held from the base metal, and so on. Many of these parameters affected each other, and they were also affected by things like variation in current from the electrical generating equipment. Arc welding parameters also needed to be tailored to the specifics of the metal being welded and the configuration of the joint. A butt weld on inch-thick steel plate demanded different welding parameters than a fillet weld on quarter-inch aluminum. But these problems were solved, and by the 1920s automatic and semi-automatic arc welding machines were in use.
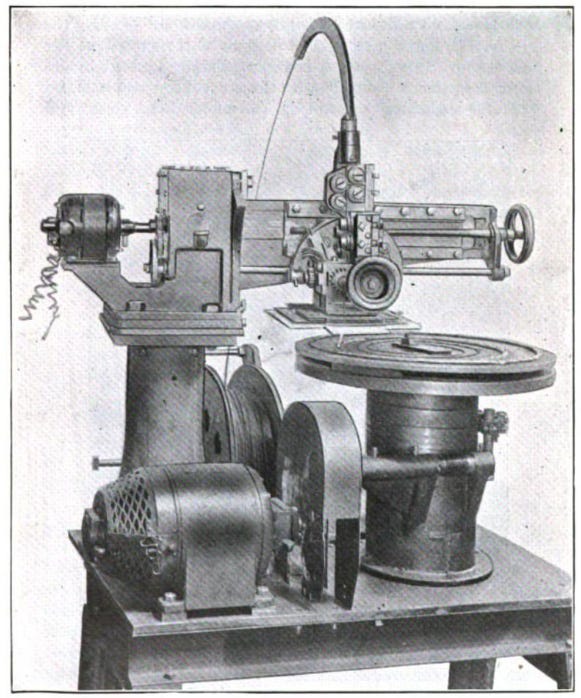
Early welding machines were what today we’d consider “hard automation.” They were built to repetitively perform some specific series of motions, and had little flexibility. An automatic welding machine could be adjusted to accommodate things like differently sized parts of the same type, but variation beyond that, such as different weld geometry, would require a different machine to be built. Because of this, these machines were most useful for producing large volumes of very similar parts.
These types of welding machines became popular, and by the late 1950s there were automatic or semi automatic machines for nearly every type of welding process. Car manufacturers developed special machines for performing multiple spot welds at once, and manufacturers ranging from boiler makers to locomotive builders used automatic arc welding machines for things like steel tanks, pistons, and pipes. By the late 1950s, welding machine operators (who probably mostly operated resistance welding machines) made up more than half of all welders.1
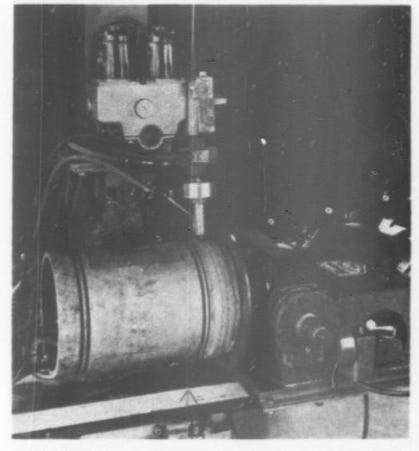
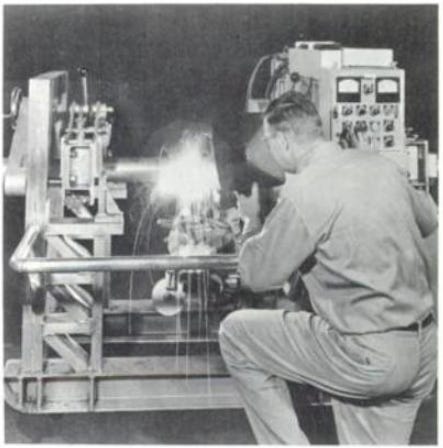
The next stage of welding automation was with robots. The first industrial robot in the world, the Unimate, was used to unload die-casting machines at a General Motors plant in 1961, and three years later GM decided to install 66 Unimates for spot welding at its Lordstown, Ohio plant. By 1980 there were several thousand robots working in the car industry around the world, and 65% of them were being used for welding.
Unlike previous “hard” automation, which only did one thing, a robot could be adapted to different types of tasks by reprogramming it.2 This was especially important for the car industry, which had historically retooled or scrapped a significant amount of machinery whenever a new car model was introduced.3 But with robots, retooling could be done just by feeding them a new program, greatly reducing capital costs. The car industry quickly became the largest consumer of industrial robots.
As with the early 20th century welding machines, spot welding, being simpler than arc welding, was automated with robots first.4 By the early 1980s, spot welding robots were common in the automobile industry, while arc welding robots were still somewhat experimental. With spot welding, the robot just had to move the spot-welding gun into the correct position — it (mostly) didn’t matter how it got there or how smooth the motion was. With arc welding, however, the robot needed to move smoothly over a specific path, something that was beyond the capabilities of the early point-to-point, hydraulic-powered robots.5 And the robot had to control not only the motion of the welding gun, but also its orientation, taking into account how both affected the heating rate of the piece being welded.
Part alignment was also a more complex problem with arc welding robots. With spot welding, the force of pressing the electrodes together eliminated any gaps between the metal sheets being welded. But with arc welding, which was done on thicker, heavier parts, there wasn’t any way to squeeze them together to eliminate gaps, and variation in part thickness or part fixturing could slightly change the joint geometry. A human welder could naturally compensate for this sort of variation by making adjustments on the fly, but a robot programmed to follow a specific path with specific welding parameters could not.
There were basically two strategies for addressing this. The first was to reduce variation and increase the precision of the arc welding process and the processes upstream of it, so a preprogrammed, repetitive process would work reliably. The second was to use sensors and feedback mechanisms to give welding robots the ability to compensate for variation that did occur.
Getting robots to arc weld successfully seems to have required both. On the variability reduction side, electric-drive robots were introduced in the 1980s, which were more precise and could more easily trace smooth, continuous paths than hydraulic-powered robots. More powerful computers and higher-capacity computer memories made it possible to calculate and store the proper continuous paths — prior to this, arc welding systems would “cheat” and use point-to-point movement with closely-spaced points. Manufacturers adjusted their upstream processes to produce more uniform parts with less variability. Part tolerances were reduced in things like metal stamping, jigs and fixturing were made more precise, new handling methods were introduced to prevent parts from being damaged moving between stations, and parts were thoroughly cleaned before welding.
To compensate for variation, a variety of weld-sensing technologies were developed that would allow the robot to maintain the proper position with respect to the weld. These technologies basically fell into three categories.
The first were basic touch sensors: the robot would move until the welding wire touched the part, which completed an electrical circuit and indicated that the robot was touching the part to be welded. By moving along different axes, a simple ‘map’ of where the part was with respect to the robot was created. Touch sensing was simple and reliable, but it was slow, and couldn’t do much more than help the robot find the part. (Touch sensors could also be used to ensure a welding gun was following a groove to be welded, but this was more common in hard automation welding.)
The second type of weld sensing technology was through-arc sensing. With through-arc, the robot would be programmed to weave back and forth as it welded. This would cause the length of the arc to change as it got nearer and farther from the base metal, which would change the current and voltage in the arc. This allowed the robot to stay centered on the weld seam, compensating for things like part misplacement or heat distortion.

The third type of weld sensing was vision based. By measuring the reflection of laser light, a robot could calculate the location of the piece to be welded, similar to touch sensing but without having to actually touch the workpiece. Lasers could also be used for seam tracking: by measuring the reflection of laser light in front of the weld location, the seam could be located and the robot could follow it exactly. Laser seam tracking could also compensate for variation in the gap between the parts to be welded. The laser could measure the thickness of the gap, and then automatically compensate by changing weld parameters.
Other types of weld-sensing technology were developed, such as acoustic seam finding, but touch, through-arc, and laser-based became the most dominant. By the late 1980s these technologies were well established, and they remain the most common type of weld-sensing technology today.
Robotic welding also benefited from more general advances in robotics technology. Lifting capacity increased which enabled larger welding guns. More degrees of freedom were added, which gave robots more flexibility and enabled them to reach previously inaccessible places. Computer power continued to increase, which enabled faster seam tracking calculations and allowed the robot to move faster.
Over time, robot manufacturers and automation integrators developed ways to make it easier to integrate robotic welders into manufacturing environments. Manufacturers learned how to design parts that were easy for a robot to weld. Programming the robot was simplified. Historically, programming a welding robot was a slow, tedious process that required entering commands into a teach pendant, but modern welding robots can be programmed quickly with user-friendly software, or by physically moving the robot through the proper motions. In some welding machines, the welding program can be created automatically by feeding it a CAD file of the part to be welded.
Robot manufacturers also introduced collaborative robots, or ‘cobots’. A conventional industrial robot isn’t safe to work near, just like any other piece of rapidly moving industrial equipment. But a cobot is designed to limit the amount of inertia it exerts, and has feedback sensors that can stop it if it impacts something, making it safe for humans to work near. This makes a cobot somewhat easier to integrate into an existing shop. Today, automation integrators sell ‘turnkey’ robot welders that consist of a collaborative robot and welding equipment mounted to a movable cart. The robot can be moved into position, programmed, and start welding in a matter of minutes.
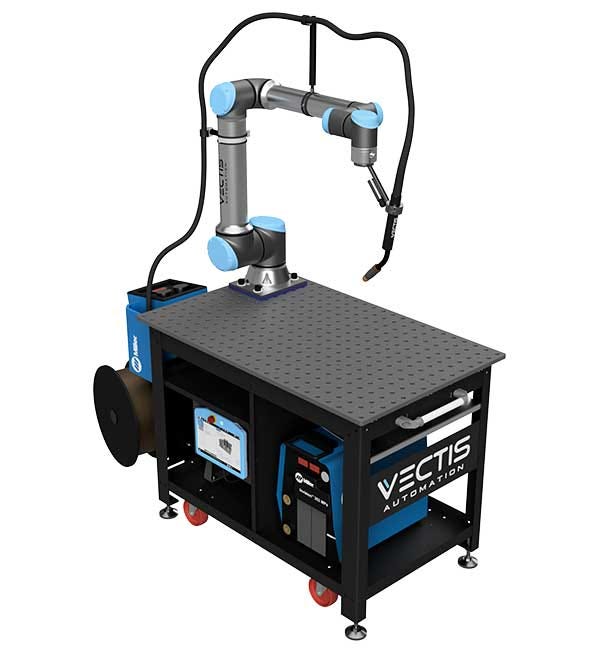
There are also efforts to apply AI and computer vision technology to welding automation. Startups like Path Robotics and companies like Abagy, for instance, have robotic welding systems that don’t require programming at all. These systems look at the part to be welded using a 3D camera, and compare what they see to a CAD file of the part or parts to be welded. They then work out where the welds are, and the path that the robot needs to take to create the weld. This lets the robot compensate for things like changes in part position, variation in part dimensions or gaps, and clamps or fixtures that might interrupt the path of the welding robot. It's currently something of an open question whether this technology will be competitive with manual programming, which continues to get easier.
So, welding automation started with specialized machines that repetitively performed some specific welding motion. These early machines had no ability to sense or respond to feedback from their environment, had limited ability to handle different sorts of tasks, and required humans to operate. They could often only be justified for producing large volumes of very similar parts.
With the advent of robots, welding automation gained more flexibility. Instead of scrapping or rebuilding machinery when the welding task needed to be changed, you could simply reprogram the robot. Because robots were still expensive capital equipment that required large production volumes to justify, they were initially most widely adopted by automotive manufacturing, which had both very large production volumes and frequent retooling requirements for every new model change.
The first robots could only move from point to point in jerky, uncontrolled motion, which only made them suitable for spot welding, but as the technology advanced robots were able to successfully arc weld as well. Over time welding robots gained slightly more ability to sense their environment and compensate for things like mislocated parts and variable gaps in weld joints, but these capabilities were specific and narrow. They couldn’t compensate for things like a clamp that impeded that path of a robot, or a part that was too dirty to weld properly, or a part that was oriented vertically instead of horizontally, or any of the other thousand things that a manual welder could automatically adjust for. Today, this sensing ability is still fairly limited. Companies like Path Robots and Abagy are trying to push back this automation frontier somewhat, but their options are still limited in what sort of environmental variation they can handle (such as cleaning dirty parts).
Automation and the welding job market
How have advances in welding automation affected the welding job market?
If we look at welding employment over time, we see a peak in 1980 at just under 800,000 welders, declining to around 430,000 welders today (though welding employment has actually risen since 2010).
Interestingly, we see the largest decline not in manual welders but in welding machine operators. In 1959 there were an estimated 200,000 welding machine operators in the US, compared to just over 30,000 today.
Of course, this is confounded by other changes in US industries over time. If output has decreased in welding-intensive industries like shipbuilding, or products have changed such that they require less welding, this would reduce welding employment irrespective of the level of automation.
One way to address this is to look at an industry that has had somewhat static welding demand. The car industry is a good candidate: car bodies are mostly made by welding together pieces of steel, and this has been true since the early 20th century.6
If we look at welding in the car industry, we see the same basic trend. Welding employment peaked in 1973, right around when robotic welding was introduced, and has steadily declined since then. But while manual welding employment has fallen by about 50%, welding machine operator employment has fallen by close to 90%. This would be even more stark if we adjusted for vehicle output, which increased from about 9.6 million in 1973 to about 12 million today.

Advancing welding automation technology, then, seems to have mostly taken tasks that were already automated to some degree, and made them more efficient. Better welding robots and weld sensors reduced the need for expensive machine retooling, and reduced the number of machine operators. It’s had comparatively less effect on skilled welder employment: better sensors, cobots, and portable welding rigs have changed the calculus somewhat, but a robotic welding system is still far less capable than a manual welder in terms of the sort of variation that it can cope with and the sorts of problems it can solve.
A robotic welder also remains an expensive piece of capital equipment, starting in the neighborhood of $50-100,000 even before you add in things like laser seam tracking (which might be another $50,000).7 This is a substantial investment, especially when you consider that the average wage for a human welder is about $47,000 per year, a robotic welder will still require someone to operate it, and there will be tasks that the robotic welder can’t do. A robotic welder is faster than a human and can work hour after hour, day after day without taking a break (typical estimates range from 3 to 6 times as productive as a human welder), but taking advantage of that requires a high enough volume of output to spread the costs over. A human welder is less productive, but remains more flexible than a robot, and evidently enough welding tasks require that sort of flexibility that much welding in the US is still done manually. Interestingly, the pitch for a lot of robotic welding systems is often more focused on the difficulty of finding skilled welders, rather than on the potential cost savings of a welding robot.
Thanks to Josh Nieman for conversations which informed this piece. All errors are my own.
It's a little difficult to be sure of the numbers here. This BLS publication gives about 200,000 welding machine operators in 1959. The 1960 Census lists about 390,000 people working as “welders and flamecutters” in 1960, and another BLS publication gives about 300,000 people working as welders in 1956. Its not clear if that includes welding machine operators, but current BLS data includes “welding machine operators” as a subset of welders, and per this publication it seems like “welders” in 1956 includes resistance welding machine operators.
The company that built Unimates, Unimation, was a concatenation of “universal automation,” and was formed with the goal of automating any sort of task.
In addition to being expensive, this retooling could be time consuming. When Ford changed from producing the Model T to the Model A, the Rouge plant had to shut down for 6 months to retool.
Spot welding was in fact simple enough that it could be done using “open loop” control, which didn’t provide any feedback information to the robot.
Early arc welding robots would apparently try to “cheat” this by defining a series of closely spaced points for the robot to travel to, with mixed results.
This article gives 4000 spot welds on a Renault Dauphine in 1960. This report gives around 2900 spot welds in a “recently launched new car” in 1982. This book gives 4000 welds for a Saturn in 1998. Various sources (such as this paper) indicate that the number of spot welds in a car today is around 3500-6000. In some ways, though, the car industry is not especially representative, as they’re an especially heavy user of automation, something we’ll have to keep in mind.
A cobot solution will be up to around twice as expensive as a normal robot.
Having spent the past nearly 50 years working in and with manufacturing automation, I am in the optimist camp.
I've been hearing since the early 50s "you can be replaced with a button" often as part of a screed about how automation was going to put us all out of work. It has not happened yet. Even without AI I do not believe it will ever happen.
Not only have we created new jobs (Like Changeover Wizard?) for all those people displaced by automation, we have generally created better better jobs.
Go read Henry Ford's 1923 autobio "My Life and Work" (Email me at johnhenry@changeover.com if you would like a copy) He describes how he invented what is now called the Toyota Production System..
He was also a fanatic on automation "NEVER put a man to do what a machine can do" He probably created more jobs, paying double or more the going wage, than anyoiine before or since.
Manufacturing output in the US, for all the doom and gloom we hear has increased steadily and dramatically year after year from WWII to today.
Manufacturing employment is down and that is a good thing. Most unskilled and semi-skilled (fully trained in a month or so of on the job training) are really crappy. They are probably not something to be desired, they are something to be eliminated.
So, let's go automation and let's go robotics. And to the extent that AI can improve automation and robotics, lets go AI.
Trying to figure out anything sane about AI (in its current form this AI cycle as LLMs) is massively overcomplicated by the boosterism of a marauding giant blob of money getting anxious that tech is about to turn into a dull industry. There's a hundred years of science fiction to coopt as marketing (even when it's apocalyptic; if your app could take over the world there's no question that it's competent), quasi-messianic cults inside of some of the largest developers high on their own supply, and astounding capital investments that, much like when we did this a few years ago with self-driving cars, aren't getting made back in a timely fashion.
I think comparing it to welding is instructive- because it suggests that the answer for what happens with any realistic automation technology is 'it's a mess and it depends.' AI investors and marketers are keen to present LLM capabilities as completely novel and transformative- and it's true, they do some neat things that were hard to do before- but they're also clearly part of a long chain of search technologies, text generators and linters, and inappropriate personification of simple programs, that stretches back at least two generations.
And my experience both training and using ML/DL-based systems is that they're certainly neat but not hard to back into an inappropriate use case- like any piece of software. When I checked in occasionally for writing help to generate a punchy line, the results were...fine, but I wandered off because because writing is conveying particularities inside my head that the machine isn't privy to (and it isn't that good). I suppose it could write customer service boilerplate- but the competition there is the templates everyone mostly uses already. I've flicked on assorted copilots while coding, and it's pretty nice- but the entire story of programming from machine code on has been about generating more standardized instructions with less typing- this is continuity again. And as a search add-on? It's notably, actively bad.
And then we have welding- a task where most of the volume of the task done in the world happens under repeatable controlled conditions, and so it was mostly but absolutely not completely, handed to machines- over the course of a century, with booms and busts tethered to bigger economic forces, and slowed by the fact that the next weird edge case that breaks the extant version of a technology is always much closer than you'd like to think.