In the late 1940s and early 1950s, a revolution took place in American military aircraft design. The invention of the jet engine made it possible for aircraft to fly far higher and faster than ever before. While the fastest propeller-driven aircraft of World War II topped out at slightly less than 500 miles per hour in level flight, jet-powered aircraft in the mid-1950s were flying at over 1,300 miles per hour, twice the speed of sound, with even faster aircraft on the horizon. Achieving this level of performance required not only powerful jet engines, but a whole host of new aircraft technologies: materials like inconel and titanium, and manufacturing methods that could produce far stronger and lighter aircraft parts.
One promising technological advance was to use large forged or extruded parts. Forging is a manufacturing method that shapes metal by applying pressure, usually by hammering it or squeezing it with large presses. Extruding is a similar process that shapes metal by squeezing it through an opening of the proper shape. At the time, both forging and extrusion were used to produce aircraft parts, but parts were limited in size and needed to be stitched together with hundreds or thousands of fasteners. By using very large forgings and extrusions to replace many smaller parts, components could be thinner, lighter, and stronger. Aerodynamic surfaces could be smoothed, and seals could be tightened. And by eliminating so many individual parts (along with the time and effort to attach them together), large forgings and extrusions could potentially reduce the time and cost required to build an aircraft. While there were a variety of different methods for making very large parts, such as casting and machining from plate or billet, forging and extrusion had several distinct advantages.
…Machining from plate or billet requires tremendous machines and many machine-hours. A part machined from plate or billet is not as consistent in its mechanical properties as a part forged or extruded to finished or nearly finished dimensions. Mechanical properties in the center of thick plate or billet are questionable. Forgings have the added advantage of variable grain direction which generally can be tailored to the stress patterns of a specific design. The large percentage of stock going into chips [in machining] is unfavorable. Casting materials do not have sufficiently high physical properties, nor have casting techniques developed to the point where efficient metal distribution and thin sections can be obtained. – Symposium on Heavy Presses
But the size of forgings or extrusions was limited by the size of the presses used to make them. Very large forgings or extrusions would require building presses of unprecedented size. Machines would need to be ten stories tall and capable of exerting hundreds of millions of pounds of force.
In the 1950s, the Department of Defense undertook a program to build such presses. Known as the Heavy Press Program, it funded the construction of four large forging presses and six extrusion presses. Upon completion, the largest of them were the largest presses in the world.
The program was an enormous success. Not only did the large parts produced by the presses greatly reduce the cost and increase the performance of military aircraft, but the presses proved useful for making parts for things like helicopters, submarines, spacecraft, and commercial jets. Within roughly a decade the presses had returned more than double their investment in reduced manufacturing costs, and they continued to produce complex, high quality forged and extruded parts over the subsequent decades. Six of the ten presses are still operational today.
Origins of the heavy press program
The origins of the Heavy Press Program can be traced to Germany in the 1920s. As a condition of the Treaty of Versailles, Germany was forced to give up many of its western iron-producing regions, creating a chronic shortage of iron and steel. This drove Germany to make greater use of other metals, like magnesium and aluminum. Germany was the first country to produce magnesium on a commercial scale, starting in the 1880s, and it was an early leader in the development and use of high-strength aluminum alloys.
It was found that while aluminum and magnesium responded poorly to being shaped by hammering (they tended to shatter, particularly magnesium), good results could be achieved by squeezing them in hydraulic presses. As a result, Germany built a series of increasingly large presses in the years following WWI to make large forgings and extrusions from magnesium and aluminum. For forgings, it built a 7,000-ton press, followed by three 16,500-ton presses, followed by a 33,000 ton press, with plans for an even larger 55,000 ton press. Progress in extrusion presses was similar: by the end of WWII, Germany had four 12,000-ton extrusion presses in various stages of completion, and a 25,000-ton press on the drawing board. (“tons” refers to the pressure capacity of a press, not its weight. So a 7,000-ton press is capable of exerting 7,000 tons of force.)
The U.S. became aware of Germany’s large press capabilities as early as 1942, when inspection of the wreckage of German aircraft revealed forgings far larger than anything the U.S. could produce. The U.S. responded by starting work on a large, 18,000 ton forging press at the Wyman-Gordon plant in Massachusetts, but it wouldn’t be completed until 1946.
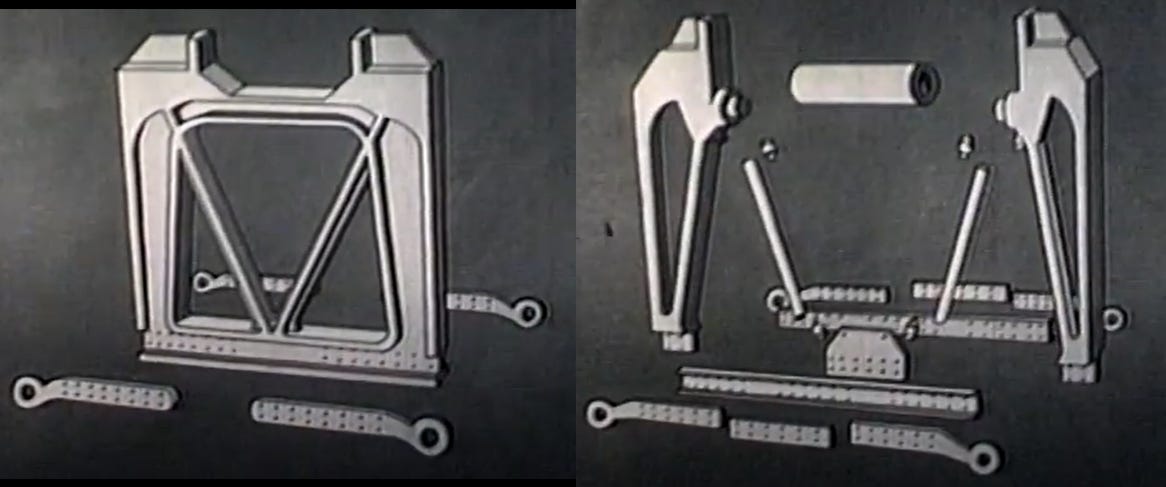
Following Germany’s surrender, the U.S. and the Soviet Union divided up its large press capabilities as well as its rocket scientists. The U.S. dismantled four German presses and had them shipped back to the states, while the Soviet Union secured the 33,000-ton press, the designs for the 55,000-ton press, and a number of German metallurgical experts.
By the late 1940s, a confluence of factors was pushing the U.S. towards building its own series of large presses. Rapidly improving aircraft performance was creating a need for lighter, stronger aircraft parts. The Germans had shown what could be achieved by using very large aircraft forgings and extrusions, and the U.S. had several years of experience from operating its own 18,000-ton press. The Soviet Union had taken the largest of the German presses and was presumably building more of its own, creating the risk that the U.S. might fall behind in aircraft manufacturing capabilities.
The Air Force studied seventeen different aircraft then under production, surveyed several different aircraft manufacturers, and concluded there were large potential benefits from building very large presses for forgings and extrusions. In 1950, the Department of Defense initiated a program to build 17 large presses: 9 die-forging (where hot metal was squeezed into a mold) and 8 extrusion. The expected cost, including presses and necessary supporting facilities, was $389 million. This was later cut down to 10 presses: 4 extrusion and 6 forging (in addition to the 18,000-ton Wyman-Gordon and the four presses taken from Germany), which would ultimately cost $239 million ($2.8 billion in 2024 dollars).
The program would be funded by the Department of Defense and managed by the Air Force, but the presses themselves would be leased to and operated by private industry (a choice that was controversial at the time). In return for very attractive lease rates, the companies would be responsible for any costs associated with maintaining and operating them, and the government would receive 4 to 5% of the revenue made from their operation.
This arrangement required some degree of selling on the part of the government. Private industry had to be convinced to participate, and that the presses would be sources of revenue and not simply a constant drain due to maintenance costs. Aircraft designers likewise had to be convinced that the presses would be available, and to design parts to take advantage of them. (Historically, aircraft designers had been reluctant to design parts that could only be made in a limited number of facilities.)
The heavy presses
Construction on the presses began in 1952 and was a monumental undertaking. The largest, the 50,000-ton forging presses, were behemoths: each was the size of a ten-story building, and could exert enough force to lift an entire battleship. The 35,000-ton forging presses weren’t much smaller. Even the 12,000-ton extrusion presses were 120 feet long, with parts twice as tall as a man, and more than twice the capacity of the previous largest American extrusion presses.
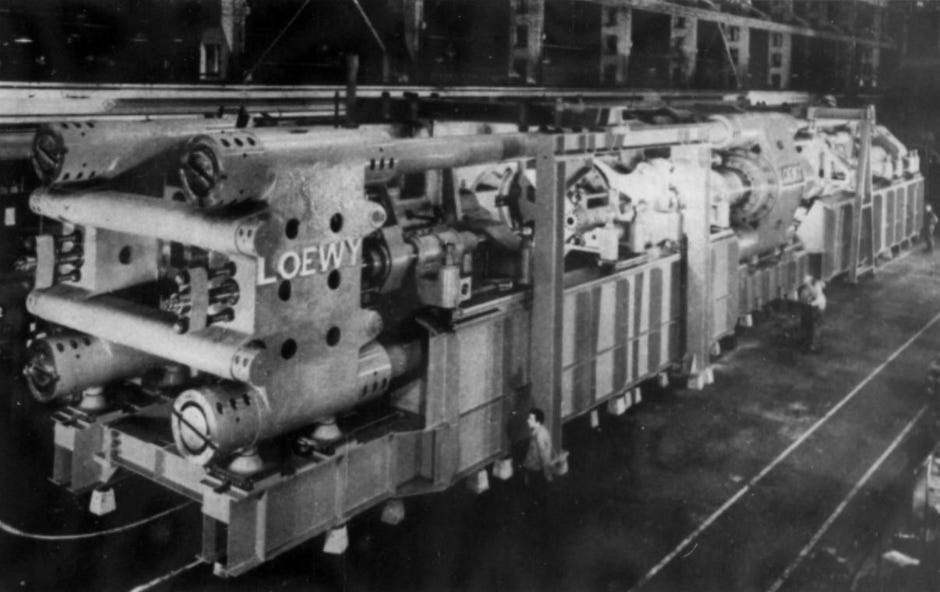

Most of the forging presses themselves would be underground, and required a 100-foot deep hole lined with concrete walls 13 feet thick. The forging and extrusion presses alike were made up of massive iron and steel components that were some of the largest metal parts ever produced: 200-ton cross beams, 90-ton cylinder supports, 145-ton tie rods. The parts were so large that special manufacturing and transportation methods were devised to handle them. Special furnaces needed to be built to fabricate the 108-foot tie rods for the forging presses, and multiple cranes were needed to move them. Some press components exceeded the weight limit for what a single rail car could support, and so were carried by multiple rail cars at once. Parts were produced by American fabricators like Bethlehem Steel, but also came from all over the world: England, Scotland, France, and Japan.
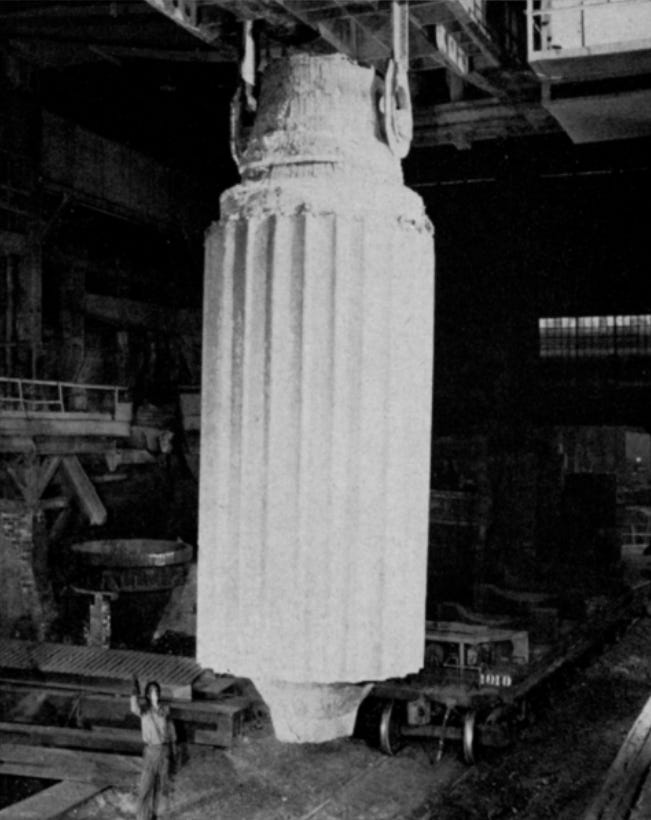
The huge presses required equally huge supporting infrastructure. Hydraulic systems for the presses required water tanks thousands of gallons in size, and complex pumping systems that could pressurize water up to 7000 psi. Huge new furnaces had to be built, along with new, larger tools like saws and stretching devices. Mills had to figure out how to produce larger ingots of metals like aluminum to feed the large presses. At Alcoa, an entire 500,000 square foot factory was built in Cleveland to accommodate the 50,000- and 35,000-ton forging presses being installed.
By 1954 the first heavy presses were operational, and by 1956 they had all been completed. The presses quickly proved their worth, greatly reducing aircraft part counts and manufacturing costs. In one case, four forgings replaced a collection of 272 individual parts held together by 2,700 rivets. In another case, nine large extrusions replaced 81 smaller parts and eliminated more than 9,000 fasteners, reducing part cost by 30% and weight by 6%. And the new presses were also faster, further increasing production efficiencies.

The presses eliminated machining time as well as parts and fasteners. Typically, a forging or extrusion didn’t come out of a press perfectly accurate, which required machining to carve the part down to its final dimensions. Likewise, very large parts had often needed to be cut down from large pieces of plate or billet. While machining wasn’t totally eliminated by the heavy presses, their ability to produce thin and complex parts near in size to the final shape required meant that machining time was greatly reduced. In one case, a part that started weighing 1,600 pounds and had more than 1,200 pounds removed by machining, at a cost of $18,000, was replaced by a part that started at just 321 pounds and required $500 worth of machining. Another part went from needing 23 pounds of material removed to just 2 pounds removed.
These savings had a significant effect on the total cost of aircraft being produced. Savings on the Convair F-102A were estimated to be $20,000, around 1.6% of the cost of the aircraft. The savings on a heavy bomber was estimated to be even greater, around 5-10% of its total cost; savings on the B-52 alone were estimated to be greater than the entire cost of the Heavy Press Program. By the 1960s, the heavy presses had saved the government an estimated $500 million in reduced manufacturing costs.
And it wasn’t just aircraft that were able to take advantage of the new press capabilities; parts from the presses were used in ballistic missiles, nuclear submarines, and armored vehicles for the Army. The presses were used to forge the beryllium heat shield on the Mercury space capsule, and the huge aluminum “anchors” that attached the Saturn V rocket to the launch pad. In 1956, the presses were first used to produce parts for commercial aircraft, and by the 1960s this was common — a 4,000-pound titanium beam made on the heavy presses to support the landing gear on the Boeing 747 was the largest titanium forging that had ever been produced.
Partly this broad range of uses for the heavy presses came from expanding the range of materials used in them. Originally the presses were designed to make parts from aluminum and magnesium, but by the 1960s they were not only pressing aluminum and magnesium but steel, titanium, nickel, copper, columbium, beryllium, and a variety of other metals.
The heavy presses have been described as “the most rapid and far reaching advance in metal processing in industrial history,” as well as the biggest leap for aircraft manufacturing in industry history. By the early 2000s, parts from the heavy presses were in every U.S. military aircraft in service, and every airplane built by Airbus and Boeing. The two 50,000-ton forging presses remained the largest closed-die forging presses in the U.S. until 2018, when they were surpassed by an even larger 60,000-ton press.
Conclusion
The Heavy Press Program is a classic example of military technological spillovers, and the potential returns from government investment in technological capabilities. The heavy presses were built specifically for military purposes — making lighter and stronger parts for supersonic aircraft — but once they were built, they proved useful for all sorts of other things, from spacecraft to power systems to commercial aircraft. The U.S. has accrued the benefits of the presses for 70 years and counting, and at least part of America’s success in commercial aircraft manufacturing can be attributed to their existence. Some have gone so far as to say that the entire modern American aerospace industry owes its existence to the heavy presses.
The Heavy Press Program also shows the importance of manufacturing improvements for technological progress. The sorts of design for manufacturing optimizations that the presses made possible — replacing a large number of parts and fasteners with a smaller number of larger components, reducing machining time — not only reduce manufacturing costs, but they changed the economic calculus as to what sorts of technologies are commercially viable, and thus get further developed. The heavy presses made it possible to build strong, precise, lightweight aircraft components more cheaply than other manufacturing methods, making things feasible that otherwise might not have been. An official Air Force statement from 1964 states that “to catalogue the significant accomplishments of the heavy press program is almost to relate the history of our modern advanced aircraft,” and credits it for making things like aircraft wet wings (where the wing of the airplane holds the fuel) inexpensive enough to be viable.1
We can see a modern, obvious parallel between the Air Force Heavy Press Program and Tesla, which has created a similar revolution in car manufacturing by using large aluminum castings to replace dozens or hundreds of smaller parts. Like the Heavy Press, using large castings required building new, larger capacity machinery, in the form of “Giga-casting” machines of unprecedented size. Tesla was the first car manufacturer to adopt large castings, but the savings were so significant — an estimated 20 to 40% reduction in the cost of portions of the car body — that they’re being adopted by many other car manufacturers, particularly Chinese ones. Large, complex castings have been described as a key tool for not only reducing cost but also good EV charging performance.
The experience of Tesla with large castings suggests that there’s still opportunities available to push technology forward by making large, complex parts in a single step. Even with large presses, we may not have exhausted the possibilities. The largest closed-die forging presses have now reached 80,000 tons (in China, naturally), but as early as the 1950s experts were speculating that presses of up to 200,000 tons might be useful for aircraft manufacturing. Experience developing the SR-71 led Kelly Johnson to believe that the U.S. needed even larger, 250,000-ton presses, and in the 1980s the Army studied whether presses of up to 200,000 tons might be useful. But no such presses were ever built, either in the U.S. or elsewhere.
And in fact, recent experience suggests the U.S. might no longer be willing or able to take advantage of this type of opportunity. Much of the experience in building machinery of this magnitude has been lost, or has migrated elsewhere. The original heavy presses were built by American companies like Loewy Hydropress and Mesta, but when the 50,000-ton Alcoa press was refurbished in the early 2000s, the parts came from German company SMS, the same company that built the 60,000-ton forging press. And while American car manufacturers are using large Giga-casting machines in their manufacturing operations, those machines themselves are overwhelmingly built by Chinese or Chinese-owned companies like IDRA.
Technological progress means building things that have never been built before, which often means pushing the boundaries of manufacturing technology forward. Fail to do this, and you risk being outcompeted by people who do.
Making aircraft out of aluminum at all was only possible because of the invention of the Hall-Heroult process, which drastically lowered the cost of producing aluminum.
Great article. Thanks.
How about a follow-up about the methods used in the actual Pressing or Extruding process?
The Press needs something to give the part a desired shape. I'm assuming some kind of strong/hard pattern/plate above and below the material to be pressed. What are they made of? How long do they last? How are they made? Is the forming done as a single slow procedure or multiple strikes? I've seen videos of steel railway wheels being forged from rectangular blocks... How is this different?
In Extrusions, how do they get the hollow centers from solid material? How is butted tubing made?
This is a wonderful article. I had no idea that these very heavy presses needed such government support, and it's rather depressing that further progress in this important field of manufacturing will be, in practice, made by the Chinese.
I think most of us think of manufacturing as a boring, low-tech field with doesn't require much R&D, and certainly doesn't require programs to be sponsored by the government. How wrong we are.