The lithium-ion battery is, obviously, an extremely important technology. It helped make portable electronics possible, from laptops to smartphones to drones. It’s literally powering the transition to electric vehicles, and it’s increasingly finding a role in grid-scale energy storage, enabling more construction of intermittent renewables and helping with electric power decarbonization.
But to get there, the lithium-ion battery took a long, winding road. It took decades of research, performed around the world, before a practical lithium-ion battery was possible. And then, not unlike solar PV, it took many more years of marching down the learning curve before it could find its place in electric vehicles and large-scale energy storage. Since the early ‘90s, the cost of a lithium-ion battery has fallen by more than 97% per kilowatt-hour, which has finally allowed electric vehicles to approach cost-parity with gasoline-powered cars.
It’s perhaps more appropriate to think of the lithium-ion battery not as a single invention, but as a slow, steady accumulation of many inventions that were needed to both make a battery practical and to unlock its full potential.
Origins
The origins of the lithium-ion battery can be traced back to the 1960s, when researchers at Ford’s scientific lab were developing a sodium-sulfur battery for a potential electric car. The battery used a novel mechanism: while typically batteries used two solid electrodes (a positive cathode and a negative anode) immersed in a liquid electrolyte, Ford’s sodium-sulfur battery used two liquid electrodes (liquid sodium and liquid sulfur) separated by a solid electrolyte of beta alumina. By some unknown mechanism, sodium ions (atoms which have gained or lost electrons and thus have a negative or positive charge) were being transported rapidly through the solid beta alumina, making the battery function.
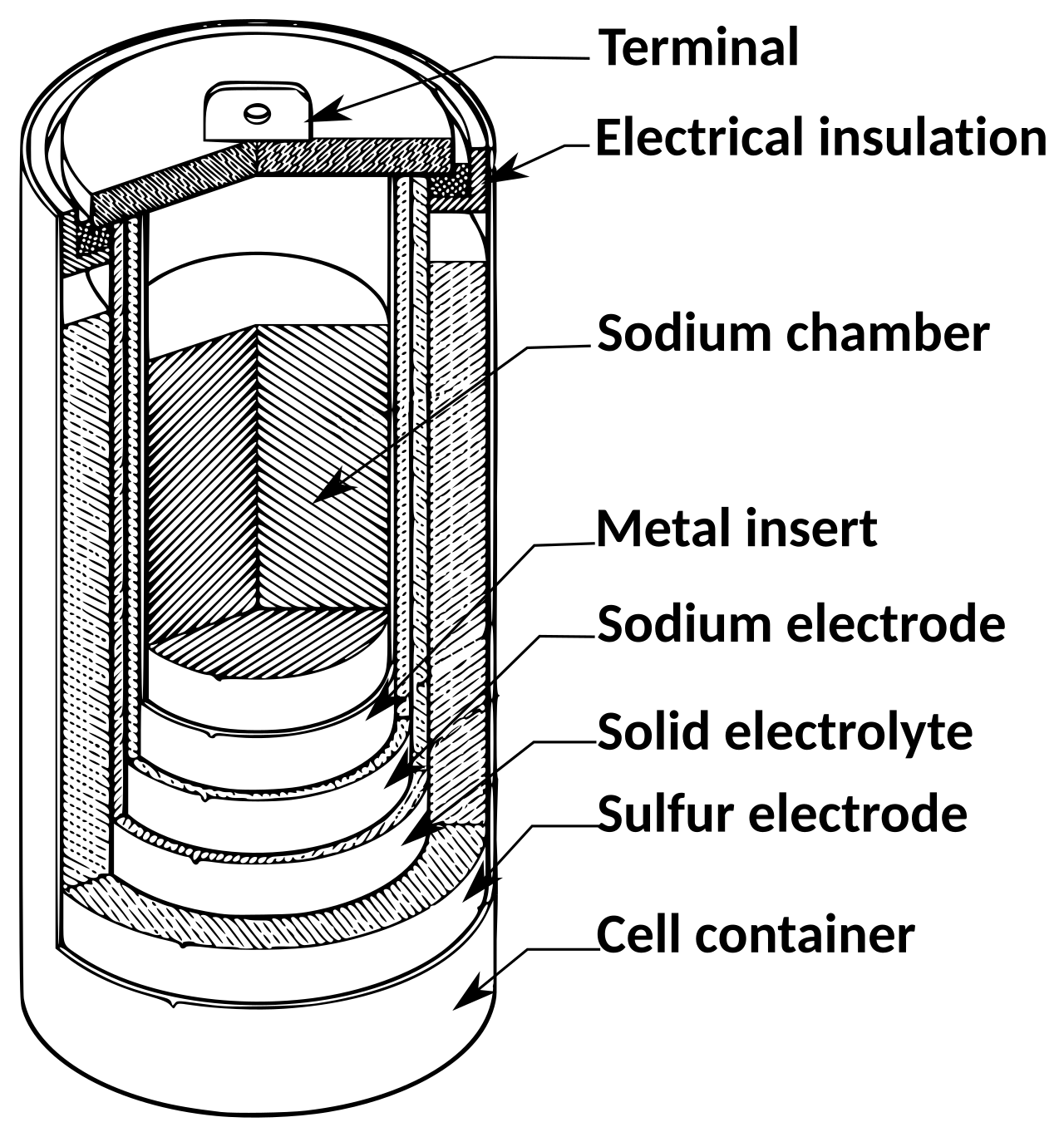
At Stanford in 1970, researcher M. Stanley Whittingham was tasked with studying this phenomenon, called fast ion transport, to discover how ions could move so rapidly through a solid material. To do this, he built his own battery, which used a solid beta-alumina electrolyte between two electrodes of tungsten oxide. Whittingham discovered that not only were ions moving quickly through the solid electrolyte, but they were rapidly moving in and out of tungsten electrodes. The ions were intercalating: inserting and removing themselves between the solid layers of the electrode material. Intercalation wasn’t an unknown chemical phenomenon, but Whittingham’s experiment marked the first time it had ever been used in a battery.
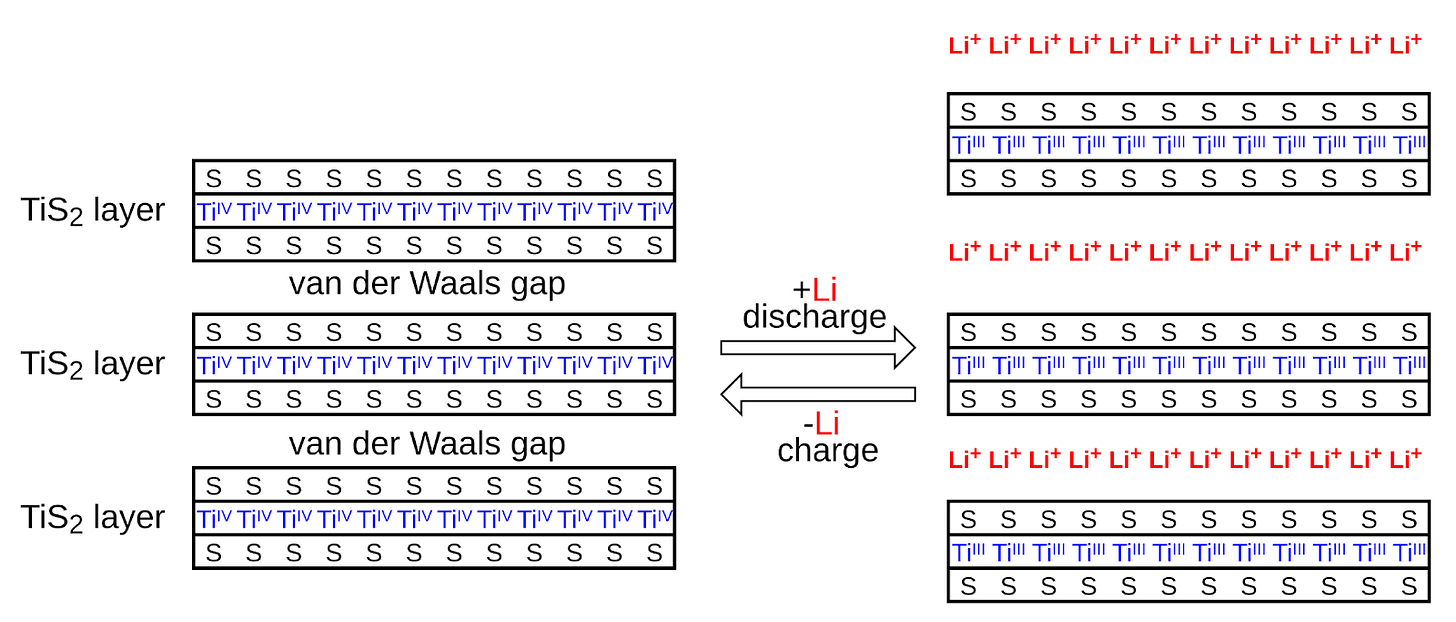
In 1972, Whittingham moved from Stanford to Exxon research. Exxon was concerned that oil supply might peak in the next few decades, and was funding research on a wide variety of alternative energy technologies that might replace it. Whittingham joined Exxon to research superconductivity, and began studying a compound called tantalum disulfide, which becomes a superconductor a few degrees above absolute zero. While injecting potassium ions into the compound, he noticed he was getting high-energy reactions, and speculated that the material could be used to store energy. He and his team began to look for other compounds, eventually choosing titanium. Within a few months, Whittingham’s team built a battery with a titanium disulfide cathode and a potassium anode. After potassium proved hazardous, they switched the potassium for lithium.
Whittingham’s battery used metallic lithium for the anode, and lithium salts within the liquid electrolyte to facilitate ion transport. When the battery discharged, positively-charged lithium ions would migrate from the metallic lithium anode through a non-conductive separator, and intercalate themselves between layers of titanium disulfide at the cathode. Because the lithium ions were positively charged, electrons would also need to flow from the anode to the cathode to balance the charge. Since they couldn’t flow through the non-conductive separator, they would be forced along a conductive pathway connecting the anode and the cathode, doing work in the process.
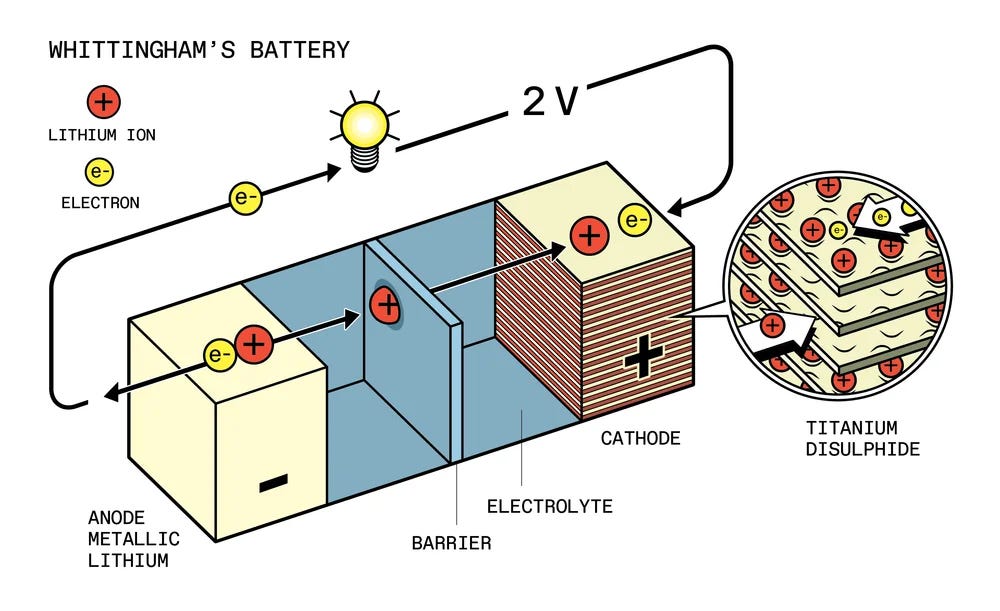
Whittingham’s battery, the first battery to use intercalating lithium ions, had several attractive features. Not only was it rechargeable, but it was far more powerful than existing rechargeable batteries. Existing nickel cadmium batteries could produce on the order of 1.3 volts, but Whittingham’s titanium disulfide battery could produce around 2.4 volts. (The battery’s high voltage was in part due to lithium’s very low electrode potential, which made it an excellent choice for an anode.) It was also able to store a large amount of energy in a comparatively small amount of material, with a theoretical energy density of 480 watt-hours per kilogram, more than twice as high as the theoretical capacity of nickel-cadmium (though actually achievable values were expected to be much lower).
Whittingham’s battery was not much more than a collection of chemicals in glass beakers, but before long Exxon had three research teams working on turning it into an actual product. One major effort was to reduce the battery’s risk of fire. Lithium is highly reactive (it reacts violently with, among other things, water) and in a battery it had a tendency to grow dendrites or whiskers, which if they crossed through the separator between the anode and the cathode could cause the battery to rapidly discharge and start a fire. (Firefighters allegedly visited the labs where the batteries were being developed on multiple occasions.) Exxon ultimately used an anode that was only two-thirds lithium, with aluminum making up the balance, to try and reduce dendrite growth and fire risk. By 1977, Exxon had developed a small titanium-disulfide “button cell," and had acquired a customer, Swiss watch company Ebauches. But ultimately Exxon deemed the battery business too small, and the technology too far from practical. A pure lithium anode would quickly grow dendrites through the separator and cause a catastrophic short circuit, and a lithium-aluminum anode had an unacceptably low cycle life. By the early 1980s Exxon had licensed the titanium disulfide battery to several other companies (none of which were successful with it), dismantled its battery group, and left the battery business.
Exxon demonstrated that a rechargeable, lithium-based intercalating battery was technically possible, but the technology needed to make it practical only came together bit by bit. The next major advance came from Oxford in 1979, in the lab of John Goodenough. Goodenough was studying battery chemistry, and trying to develop a better cathode for a lithium-based battery. After a year of studying different compounds, Goodenough and his research staff eventually came up with two possible cathode materials, nickel oxide and cobalt oxide, that would allow lithium ions to insert and remove themselves while causing minimal damage to the material (though eventually nickel oxide would prove to be too unstable to be practical). When tested in a battery, these cathode materials yielded a voltage of around 4 volts, far higher than the 2.4 volts of the titanium disulfide battery. The voltage was high enough, in fact, that it could be sacrificed in order to substitute the highly reactive lithium metal anode with a different, safer material.
At the time, Oxford had no interest in intellectual property, and so Goodenough turned to the UK’s Atomic Energy Research Establishment to get the new cathode patented. As part of the deal, Goodenough and his researchers relinquished their rights to any royalties. Later these royalties would be worth tens of millions of dollars.
Goodenough’s lithium cobalt oxide cathode was quickly followed by another cathode, developed by an associate of his, Michael Thackeray. Thackeray was a South African battery researcher who, eager to work with Goodenough, had joined Goodenough’s lab as a postdoc in 1980. Shortly after arriving at Oxford, Thackeray demonstrated that lithium could intercalate itself into iron oxide. This was notable because iron oxide had a spinel crystalline structure, which initially did not appear to be a promising structure to store lithium ions. Based on the results, Goodenough suggested experimenting with manganese, another spinel structure material which would likely produce a higher voltage if used as a cathode. These experiments were successful, and by 1983 Thackeray was building batteries with lithium manganese oxide cathodes.
There were now two possible cathodes for a practical lithium-ion battery: Goodenough’s lithium cobalt oxide (LCO) and Thackeray’s lithium manganese oxide (LMO). But a material that could replace the hazardous lithium metal in a battery’s anode was still needed. One possibility was to substitute it with another intercalating compound. This concept, of two intercalating compounds that ions would move back and forth between, was proposed in 1978 by French researcher Michel Armand as a “rocking chair battery,” but would only start to come together four years later, at Asahi Chemical in Japan.
At Asahi, Akira Yoshino was researching a novel polymer anode that could intercalate lithium ions, polyacetylene. When searching for a cathode material to pair it with, Yoshino came across Goodenough’s research on the cobalt oxide cathode. Pairing it with a polyacetylene anode, Yoshino and his team created a battery that could be charged and discharged, and operated at four volts. But while the new battery was promising, polyacetylene had a major drawback: it was very bulky, making it less than ideal for batteries in the portable electronics that Japanese manufacturers were beginning to produce. Some Asahi researchers thus began to look around for another possible anode, and soon homed in on carbon. Carbon had been known to intercalate lithium ions as early as 1955, and graphite had been suggested as a battery anode material by Michel Armand in the 1970s. In 1985 Asahi researchers successfully intercalated lithium ions into thin “whiskers” of carbon. While this worked, carbon whiskers were incredibly expensive and difficult to procure, so researchers looked for alternative carbon materials, examining more than 100 before ultimately deciding on a soft carbon derived from petroleum coke. In 1986 Asashi had a small batch of the first test batteries manufactured using the new chemistry by Battery Engineering in the US.
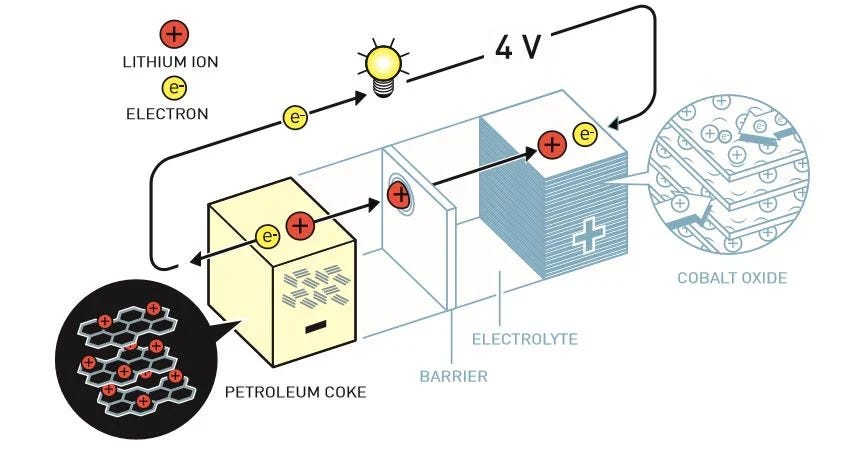
While Asahi was developing its battery, a research team at Sony was also exploring new battery chemistries. Sony was releasing a steady stream of portable electronics — the walkman in 1979, the first consumer camcorder in 1983, and the first portable CD player in 1984—and better batteries were needed to power them. In 1987, Asahi Chemical showed its prototype lithium-ion battery to Sony, and the two companies made tentative plans for a joint battery venture. But even as these negotiations were going on, Sony began to work on its own version of a lithium-ion battery (not unlike Apple starting work on its own GUI-based operating system after seeing a demonstration of Xerox’s). But while Asahi’s battery efforts had been tentative and timid, Sony pursued the technology vigorously: Sony assigned six different teams the task of studying different lithium chemistries in the hopes that at least one of them would come up with a compelling one, and quickly converged on a very similar chemistry to Asahi’s: a cobalt oxide cathode and a soft carbon anode made from coke.
Over the next several years, Sony steadily, methodically, turned this chemistry into a practical battery. It figured out how to make the cathode materials in large volumes, and how best to heat treat the coke. It worked with suppliers to develop other key parts of the battery like the separator and the conductive electrolyte. Batteries began to roll off the assembly line in 1991, and by the end of the year Sony had produced more than 100,000. The next year, it would make more than a million. Asahi would shortly follow up with its own lithium-ion battery in partnership with Toshiba, and within a few years there were a half-dozen Japanese manufacturers competing for the market.
Lithium rides the learning curve
But the invention and development of the lithium-ion battery is only half the story. Not unlike the solar photovoltaic cell, the lithium-ion battery was a novel energy technology that was incredibly expensive in terms of cost per unit of energy delivered. Its high energy density made it useful for many applications like portable electronics, but its full potential wouldn’t be unlocked until it could fall down the learning curve, and get orders of magnitude less expensive.
Lithium-ion’s progress along the learning curve encompasses several different types of improvements. One major one has been continued improvements to the battery chemistry. Sony’s first lithium-ion battery used a soft carbon anode made from coke, and a lithium cobalt oxide cathode, but it soon replaced soft carbon with hard carbon, which could store more lithium ions between the layers. Hard carbon increased the energy density of the battery by about 50%. Hard carbon was then replaced by graphite, which allowed another 25% increase in energy density. Switching to graphite required finding a new electrolyte that wouldn’t produce undesirable “side reactions” with the graphite. This was eventually discovered by accident by Moli Energy in the form of ethylene carbonate, which reacts with graphite to form a passive solid electrolyte interphase (SEI) layer over the anode. The SEI layer blocks the flow of electrons and protects the anode from further reaction with the electrolyte, while allowing ions to flow through it. Graphite remains the primary anode material for lithium-ion batteries today, but manufacturers have gradually begun to add small amounts of silicon to it to further increase its performance.
There have been similar improvements in the cathode material. The high cost of cobalt spurred a search for alternative cathodes made from cheaper materials, and in 1997 John Goodenough discovered another battery cathode made from iron phosphate, with assistance from Michel Armand who suggested a carbon coating for the material that would make it more conductive. While lithium iron phosphate (LFP) did not have the energy density of a cobalt cathode, its materials, iron and phosphorus, were far cheaper. LFP batteries also proved to be very stable, making them less of a fire risk, and they could last for a very large number of charge and discharge cycles. These advantages have made LFP batteries an increasingly attractive choice for electric vehicles, despite their lower energy density.
Around the same time, Michael Thackeray, who had moved to Argonne National Labs in the US, developed another new cathode, made from nickel, manganese, and cobalt (NMC). Thackeray’s NMC cathode was initially only a slight improvement over a cobalt cathode in terms of energy density, but it eliminated a large amount of expensive cobalt. Since then, NMC cathodes have continued to improve. Thackeray’s first NMC cathode used roughly equal proportions of nickel oxide, manganese oxide, and cobalt oxide (known as NMC111, for a 1/1/1 proportion of each), but more recent formulations have used much higher nickel fractions, such as NMC 811 (80% nickel, 10% manganese, 10% cobalt) and NMC 955 (90% nickel, 5% manganese, 5% cobalt), which offer even higher energy density and even smaller amounts of costly cobalt.
NMC was followed by another nickel-based cathode (the origins of which are somewhat unclear), nickel cobalt aluminum (NCA). NCA would be used for Tesla’s first Model S in 2011, and has very high energy density, but it has since lost ground to other battery chemistries.
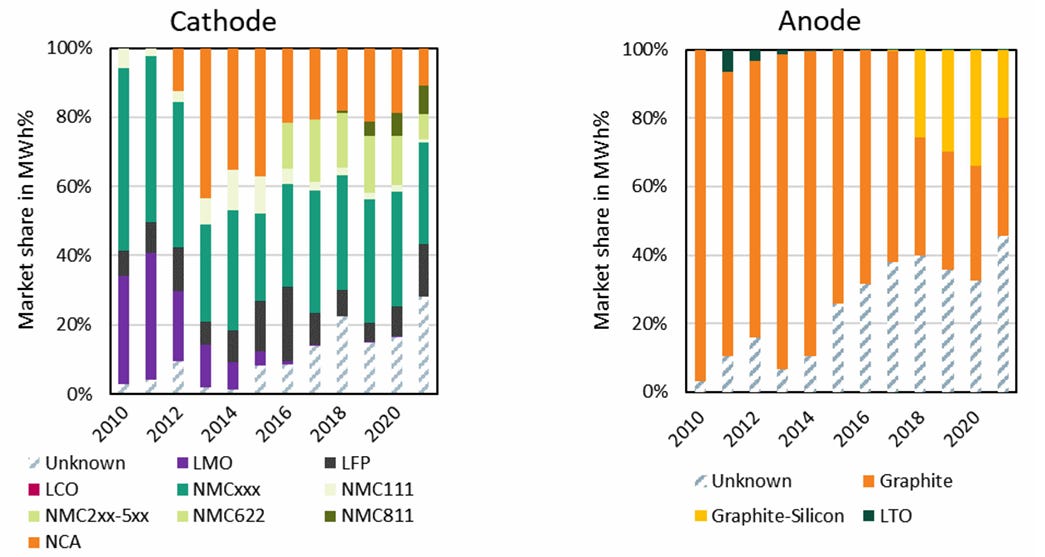
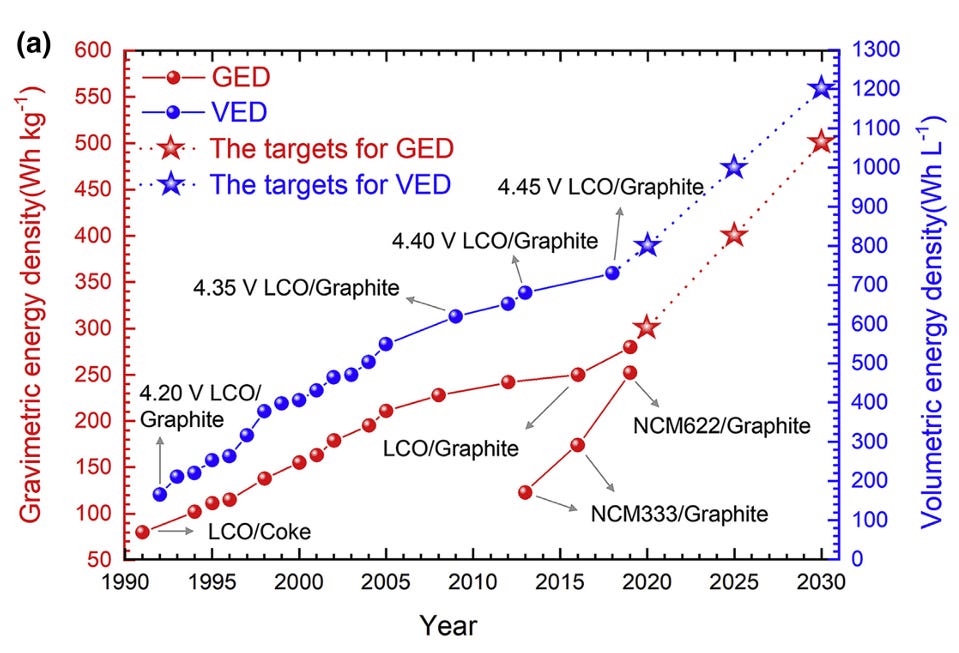
In addition to the anode and the cathode material, there have also been improvements to the electrolyte solution that conducts the lithium ions. An electrolyte typically consists primarily of a solvent (like ethylene carbonate) and a lithium salt (like lithium hexafluoride, or LiF6), but manufacturers have also experimented with a variety of additives to help improve electrolyte performance. Electrolyte formulations are closely guarded by battery manufacturers, who often consider it their “secret sauce”. Tesla executives apparently call electrolyte additives “magic pixie dust” because of the huge impact they have on battery performance.
In addition to chemistry improvements, there have also been substantial improvements in making batteries more materially efficient. A battery cell consists of a series of layers (current collector, anode, separator, cathode, current collector) stacked on top of each other and rolled or folded up, and over time many of those layers have gotten thinner. Copper current collectors, for instance, have over 20 years shrunk from around 20 to 6 microns thick. Similarly, separators have steadily gotten thinner.
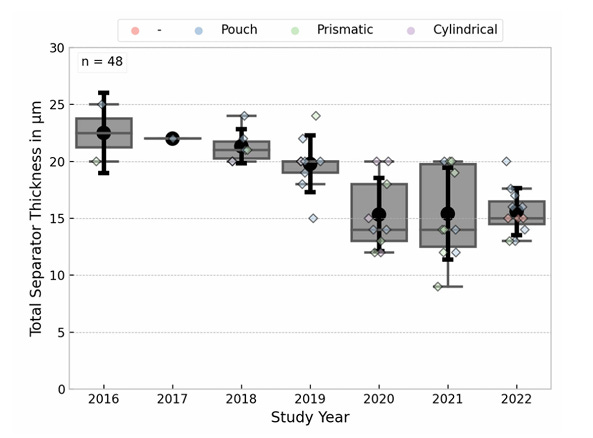
More generally, there have been steady efforts to make the active, electricity-generating part of the battery a large fraction of the overall weight. Electric vehicle battery packs have historically been made from thousands of small individual cells, with the cells bundled into modules and the modules bundled into entire packs. But there have recently been efforts to eliminate the separate modules (and the additional material they require) and simply go directly from cells to packs. Over the last four years the adoption of “cell to pack” has caused the price of EV battery packs to fall by roughly 15%.
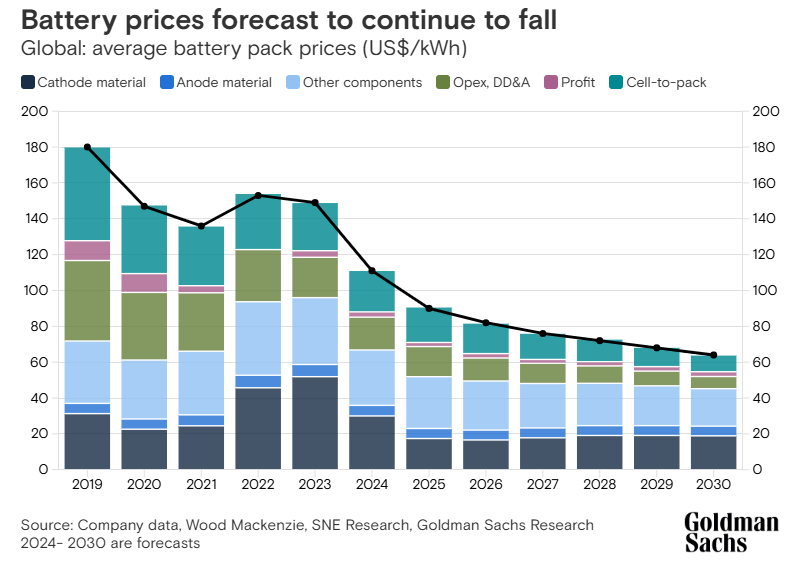
Effort has also gone into making individual cells bigger, to take advantage of surface-area-to-volume effects: all else being equal, a cell that's twice as large will require less than twice as much material to enclose it. These sorts of scaling efforts have been somewhat limited historically, due to (as far as I can tell) some combination of the economies of scale achieved by producing huge numbers of small battery cells, and the fact that reducing the risk of thermal runaway pushed towards using many smaller cells instead of a few large ones in electric vehicles. But there nevertheless seems to be movement in this direction, partially due to the adoption of more stable LFP chemistries: for the last several years Tesla has been working on delivering a much larger cylindrical cell, the 4680, and BYD recently introduced its very large “blade” LFP battery.1
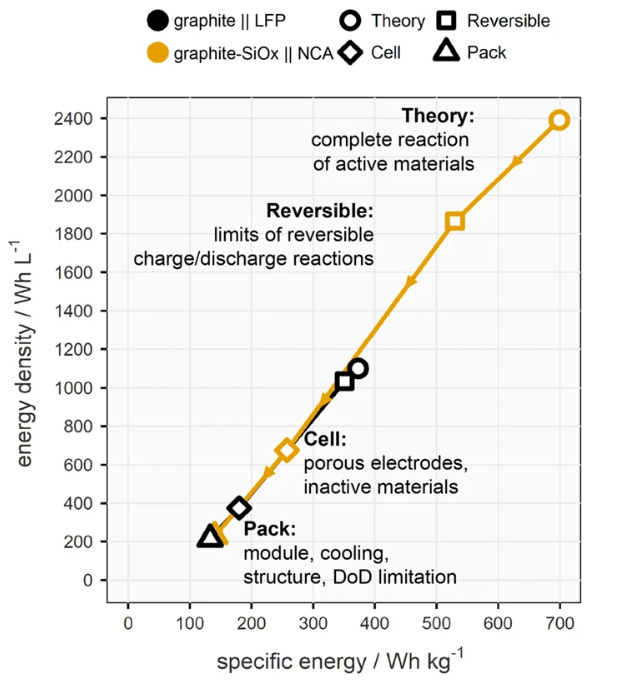
You can see the trends in battery improvement on a small scale in the evolution of Tesla’s 4680 lithium-ion battery. Between the first-generation batteries produced in 2022, and the second-generation batteries currently being produced, the thickness of the battery casing shrunk significantly (going from 0.6mm to 0.4mm on the sides), the chemistry changed from NMC811 to NMC955, and the anode and cathode both got thinner (by 10 microns and 30 microns, respectively). These and other improvements increased the energy density of the battery by roughly 11%, and have helped to drive down costs.
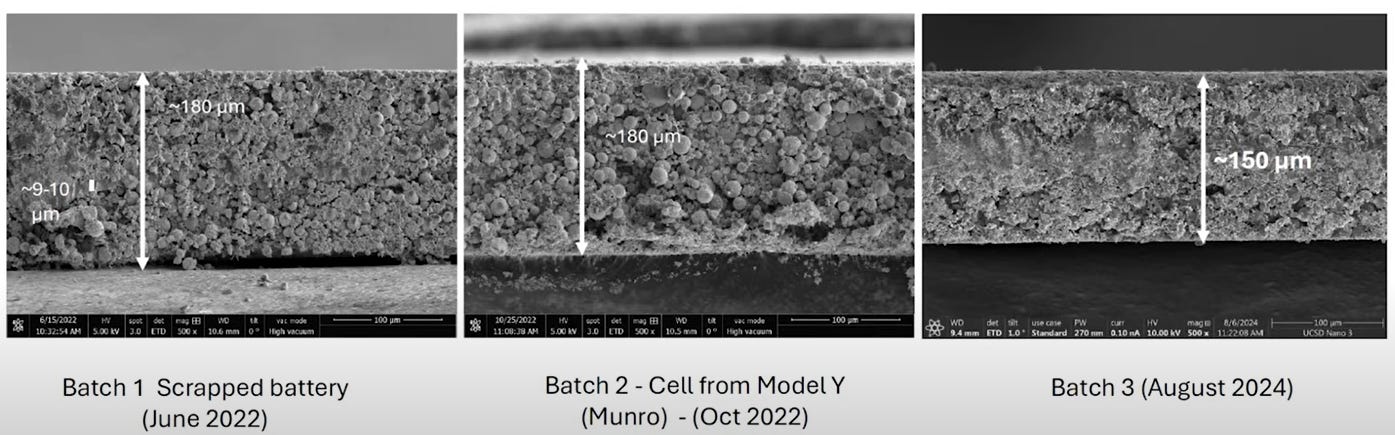
In addition to improvements to the batteries themselves, there have been significant manufacturing improvements. Supply chains have gotten more robust, and production machinery has gotten far faster and higher volume. The speed of electrode coating machines (which spread the anode and cathode material over large sheets of foil) increased by nearly a factor of 10, reducing the amount of capital required per unit output by roughly 90%. In 2019 the author of “Lithium Ion Battery Chemistries” noted that double-sided electrode coating machines, which can add two layers of material simultaneously, might be developed in the future. Now those machines seem to have arrived. Stacking machines that install the separator between the anode and the cathode have also gotten faster.
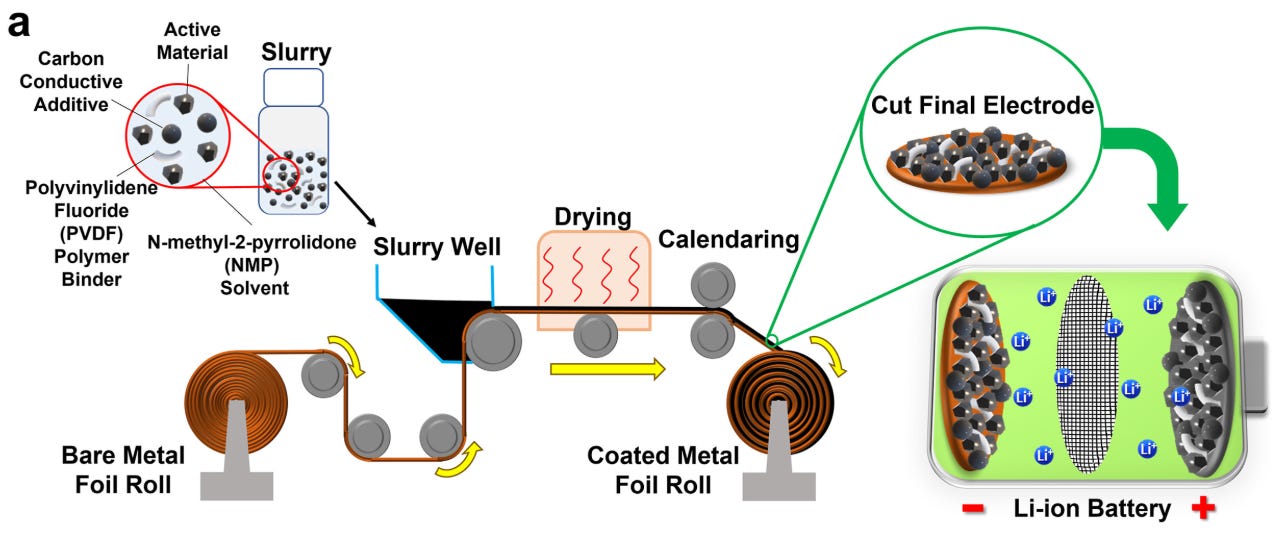
Machines have also gotten much larger, producing wider sheets of material. And manufacturers have looked for ways to cut material not only out of the battery itself, but the process for producing it. Traditionally manufacturing electrodes has required mixing the anode or cathode material together with a solvent to form a slurry, spreading that slurry onto sheets of foil, and then evaporating that solvent in large dryers. But Tesla has been attempting to master a “dry” process that can lay down electrode material without requiring a solvent at all, which (supposedly) can reduce electrode manufacturing costs by 50%.
These and other manufacturing improvements have allowed battery factories to greatly increase their production volume and take advantage of economies of scale. Factory-level production volumes increased from on the order of a few tenths of a gigawatt-hour per year to tens of gigawatt-hours today. A modern battery factory will be enormously expensive due to the scale involved: this planned battery factory in Virginia will cost $1.4 billion, and it only produces battery separators. This scale creates a virtuous cycle: the larger the market for batteries, the greater the opportunities and rewards from finding technical improvements, which reduces costs and drives further increases in market size.
Conclusion
One notable thing about the evolution of the lithium-ion battery is how hard it is to predict the trajectory of research, and how important it is to allow researchers the flexibility to pursue what they feel is promising. Whittingham stumbled across an intercalation-based battery when researching fast-ion transport through a solid electrolyte, an entirely different phenomenon. And his invention of the first lithium-ion battery cathodes was the result of a serendipitous discovery during work on superconductors. Thackeray discovered the manganese oxide cathode at Oxford, where he only was because his employer, South Africa’s Council for Scientific and Industrial Research (CSIR), paid for a year’s sabbatical so he could pursue the battery ideas he found promising. (CSIR was developing an entirely different, zeolite-based battery that Thackeray thought little of.) Early research on a graphite-based anode, performed by Rachid Yazami, was originally aimed at discovering a graphite-based cathode, not an anode, and Akira Yoshino’s battery efforts at Asahi Chemical were pursued in spite of the fact that company thought very little of the battery market, and only bore fruit because the company didn’t actively try and stop him. Likewise, the discovery of ethylene carbonate as an electrolyte that would allow graphite to be used as an anode was an accidental discovery by Moli Energy.
This sort of trajectory, of course, makes it hard to capture the value of research, or to have anything like a reliable, predictable path by which scientific research gets turned into marketable products. Exxon’s efforts to develop a practical rechargeable battery ultimately failed, though its research would spawn a successful battery in the fullness of time, and Goodenough signed away the rights to his cathode patent because it didn’t appear especially valuable at the time. And while science is often conceived as a sort of straight path that leads from basic research, to applied research, to invention and product development, real paths are often much more circuitous. Charles Murray notes this in “The Long Hard Road," a history of the lithium-ion battery and the electric car:
…There hadn’t been a linear progression from fundamental research to applied research to engineering. Ford Motor had given birth to the idea of fast ion transport in what could best be described as applied research. Then the idea had zigzagged back and forth between fundamental and applied research, from Ford to Stanford to Exxon to Oxford to France and elsewhere, before finally reaching Japan. Thus, it wasn’t a case of pure R&D; it was R&D&R&D&R&D. There was nothing linear about it.
Even the extensive applied research needed to put the pieces together and take the battery over the finish line doesn’t appear to have created much of a lasting advantage for the companies that did it (possibly because the key components had been patented by others and were available to license). Shortly after releasing its first lithium-ion battery as a product, Sony found itself in a cutthroat competition with many other Japanese battery manufacturers. And while it spent the next several years advancing the technology (going from soft carbon to hard carbon to graphite anodes), Sony nevertheless still divested its battery division in 2016, a few years before the market for electric vehicles began to take off. Today the largest Japanese manufacturer of batteries appears to be Panasonic, and its Chinese and (to a lesser extent) Korean manufacturers that have conquered the EV battery industry.
The lithium-ion battery thus both shows why unrestricted research and novel technological development is so valuable, and why, in practice, companies might not be especially enthusiastic about funding it.
Thanks to Austin Vernon for reading a draft of this, all errors are my own.
The 4680 doesn’t currently use an LFP chemistry, though there’s speculation that it might in the future.
This is a great article on one of the most important technological innovations of the last 50 years.
Your conclusions are particularly strong. The old Silicon Valley mantra about “First Mover Advantage” is clearly not the rule. In fact, I would argue that it is the exception.
Plus the relationship between Basic Science and launching a viable product is much more complex than most people realize.
I assume the subtext is the bankruptcy of Northvolt?