Long-term, I’m optimistic about robots and automation solving construction’s stagnant cost and productivity problem. Even if nothing else works, if you can build a cheap machine capable of doing everything a human can do, that would greatly reduce labor costs, which are a large fraction of the total cost of putting up a building. This level of automation would probably reduce the cost of producing construction materials as well.
But it’s hard to tell how far we are from this sort of technology. There’s been some impressive-looking progress in things like Tesla’s Optimus robot and Agility’s Digit, but if you look inside nearly any heavily automated factory (including Tesla's) you won’t see humanoid robots. Instead, you’ll find robotic arms that don’t, on their surface, seem all that different from the robotic arms of the 1970s.
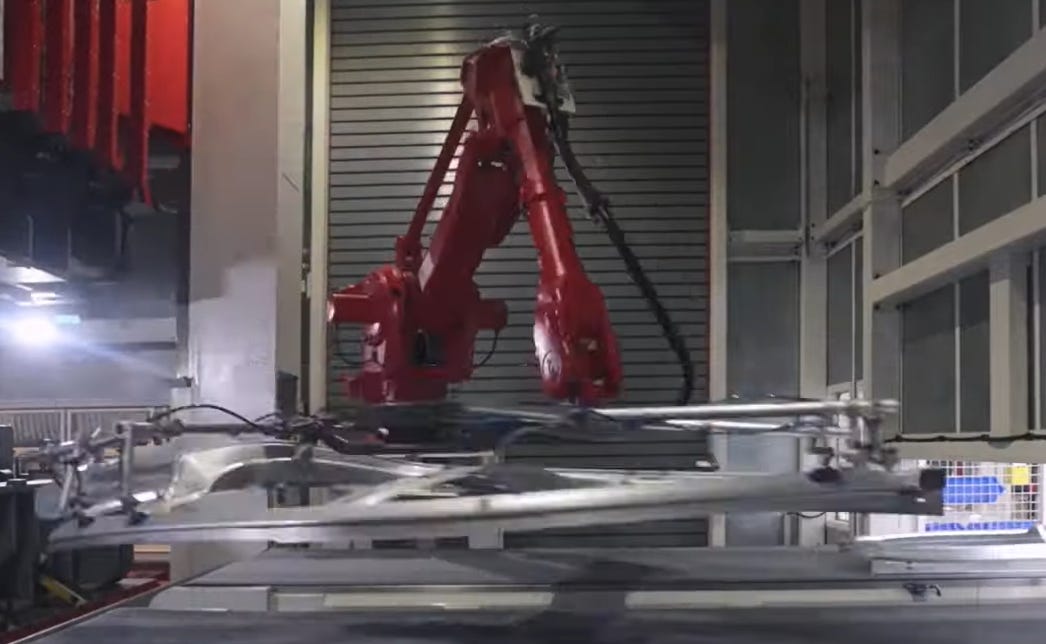
But of course, just because they look similar doesn’t mean that there haven’t been important advances. What do we know about progress in industrial robots? How have they gotten better since they were first deployed in the 1960s? Let’s take a look.
Industrial robot cost
Robots, separated from the software and sensors that give them perception and intelligence, aren’t terribly complex (conceptually at least). They’re a collection of control systems, motors, and gearboxes mounted to lever arms that make it possible to move things around in particular ways in 3D space. They can have different end effectors mounted to them for tasks like grasping, welding, or painting. One possible axis of improvement for robotic hardware is cost: if robots get cheaper over time, it becomes possible to cost-effectively use them in more locations.
Data from the International Federation of Robotics suggests that the average cost of a robot has declined significantly over time, falling 80% just between 1995 and 2017. But using IFR data is tricky. Most of its cost data isn’t quality-adjusted, and doesn’t take into account differences in robot capabilities, like payload capacity, speed, or repeatability. If customers are shifting their behavior to buy fewer large robots and more small robots (as IFR suggests that they are), this would cause a decline in average unit costs of robots, without any individual robot getting cheaper. The IFR did give quality-adjusted data between 1990 and 2005 (between which the costs of robots fell by 83% in quality-adjusted terms), but this is a fairly narrow window of time, and it's an abstract measure that doesn’t tell us what's going on with individual robots. Can we do better?
The most straightforward way to do this is to look at the cost of some individual robots, and compare them to costs of robots with similar capabilities in the past. For current robot costs I wasn’t able to find an enormous amount of data, but ABB lists starting prices for many of its robots on its online store, and this motion control supplier gives some rough prices for FANUC robots (if someone has more robot cost data, I’d be very interested).
We then need some method of comparing the costs of different robots with different capabilities. One easy way is with robot size: the greater the reach of a robot, and the more weight it can move, the more expensive it will be. We can create a simple size index that's just the maximum reach of a robot times its maximum payload. This index turns out to give a fairly strong correlation (which gets even higher if we remove the outlier of the large FANUC robot): greater reach and payload have a fairly close relationship to increased cost. (Reach and payload capacity are also two of the four measures that IFR used for its quality-adjusted robot unit cost when it was giving this information, the other two measures being speed and repetition accuracy.)
Comparing robots purely by size is of course a large simplification. Even restricting ourselves to looking just at the base hardware (ignoring things like sensors, effectors, and software that have a major impact on robotic capabilities), there are many relevant robotic performance considerations beyond reach and payload. For one, robots of the same size can have very different movement capabilities. This dataset includes both 6-axis robotic arms and simpler 4-axis SCARA robots that have much more limited motion capabilities (though interestingly, removing the SCARA robots doesn’t change the correlation much). Other relevant performance considerations are speed and repeatability: moving faster, and being able to reliably move to the same spot every time are more difficult and expensive than moving slowly and imprecisely. And though I’ve excluded them in this dataset, there are also things like cobots, which have more sensors (and are thus more expensive) but allow people to safely work around them. We could try to use a more complete index that includes some of these (which is what IFR does), but this gets complex and isn’t straightforward (and empirically, adding accuracy to the index made the correlations worse). Instead, we’ll simply keep these other performance considerations in mind as we go.
Based on this data, today a robot with a reach of 1 meter and a payload capacity of 10 kg costs in the neighborhood of $50,000 (this is just the hardware, not including other components of a robot system like end effectors, control units, and software, which all in might triple the cost of the base robot). How does this compare to historical costs?
Let’s start by looking at robots from the 1980s. This 1984 issue of Robotics Age gives cost and performance data for several industrial robots available at the time. Here’s how these costs, adjusted to 2023 dollars, stack up against modern costs.1
A few things jump out. First, robots in 2023 are generally much cheaper than robots in 1984. Our 1-meter, 10 kg payload robot would cost two to three times as much in 1984, even before considering other performance improvements like higher repeatability.
Second, there’s a much lower correlation between robot size and cost in 1984 than there is in 2023. In 1984, there’s a very large variation in cost for robots of a given size: our 1-meter, 10 kg robot seems like it could cost anywhere from $100,000 to almost $250,000. And small robots seem to cost almost as much as large robots: a robot with a 10 cm reach and a 1kg capacity might cost nearly as much as a robot with a 2 meter reach and a 50 kg capacity.
One possible explanation is different levels of repeatability, but this doesn’t seem to be the case. The small Unimate PUMA 500 (payload of 2.5 kg and a reach of just under a meter) has a similar repeatability as the much larger Sterling Detroit Robotarm (payload of 68 kg and a reach of 3 meters), but actually costs more. Another possible explanation is the greater variety of manufacturers in the 1984 data (vs just 2 in the 2023 data), but this lack of correlation remains even if we restrict 1984 to just the two most numerous manufacturers (Unimation and Yasakawa).
The most likely answer is simply the large variety of different robotic architectures available in 1984, which had widely varying costs. At the time, robotic technology was still in flux, and the Robotics Age list has robots with several types of power systems (hydraulic, electric, and pneumatic), different path-tracking capabilities (point to point, continuous, or something in between), and different component arrangements for achieving 3 dimensional motion. The Unimate PUMA was a somewhat complex multi-axis robot arm not unlike modern robot arms, while the Sterling Detroit Robotarm was, as far as I can tell, a much simpler gantry system. Today, industrial robots have converged upon a few basic architectures (in addition to 6-axis robot arms and SCARA robots, there are delta robots, as well as cobot-versions of some of these), and offerings between major manufacturers are similar.
To look back even further at robot costs, we can use this 1972 Industrial Robot Survey, which gives prices and performance for dozens of different robots available for sale in 1972. This was just a few years after the introduction of the first industrial robot, Unimate, in 1961. Here’s the graph of robot size vs cost with 1972 robot costs added, adjusted to 2023 dollars.
There’s a few interesting things here. For one, we see a somewhat better correlation between size and cost in 1972 than in 1984, even though the 1972 series has many more manufacturers (the 1984 data just has 7 manufacturers, where the 1972 data has a few dozen) and similar variety in robotic architectures. There’s still a lot of variation, however. Our 1-meter reach, 10kg payload robot seems like it might cost anywhere between $50,000 and $200,000 in inflation-adjusted dollars.
For another, robot costs seem to have risen between 1972 and 1984, rather than fallen. In 1972, our 1-meter, 10kg robot arm would cost roughly 2/3rds what it did in 1984 in inflation adjusted dollars. Looking only at size, the cheapest 1972 robots are about the same cost as the 2023 robots.
Of course, size isn’t everything, and we see substantial improvements when looking at other performance metrics like repeatability. Here’s repeatability vs size for robots in 1972, 1984 and 2023.
Interestingly, the 1984 robots are not that much more repeatable than the 1972 robots. Our 1-meter reach, 10kg payload robot would on average have a repeatability of around 1 mm in both years (with a lot of variation, as some 1984 robots could evidently achieve 0.1mm of repeatability). But since then, there’s been a huge improvement. Our 2023 1-meter reach, 10kg payload robot will have a repeatability closer to 0.01 or 0.02 millimeters, or 50 to 100 times more precise than the robots in the 70s and 80s.
And while we don’t have good data to track it, there have been other improvements in robotic motion since the 70s and 80s, such as path control. Through the 1980s, robots still often relied on point to point movement, where virtually all modern robots are capable of reliably tracing smooth, continuous paths (the spec sheets for modern robots, in fact, all give “path repeatability” values in addition to “position repeatability”).
So, overall, robots have fallen substantially in cost since the 1980s, while simultaneously getting more precise. A robot with a 1-meter reach and 10 kg payload capacity would cost anywhere from 2 to 3 times as much in the 1980s as it does today, even before considering the rise of cheap Chinese robot arms, which seem poised to make prices fall even more. And the modern industrial robot is roughly 100 times more accurate, and far more capable at smooth, continuous motion, than robots in the past.
We’ve also seen an evolution towards a somewhat standard architecture for robots (what we might call a few “dominant designs”). Early on, there was a wide variety of different types of robots that used different power systems, different control systems, different types of 3D motion, and so on. Modern industrial robots, by contrast, are overwhelmingly robotic arms with 6 axes of motion (though 5 and 7 axes also seem to be common), SCARA robots with 4 axes of motion, or delta robots. These all use electric drives and servo motors for smooth, precise and repeatable motion.
Thanks to David Nichols of Loupe for reading a draft of this. All errors are my own.
Note, there is some inconsistency in the way a robot’s reach is measured. Some sources measure reach as the maximum point that the maximum point a robot can reach from the center of the robot. Other sources measure reach as the maximum range of the robot: the farthest point it can reach minus the closest point it can reach (since robots often can’t reach places very close to their bodies). In general, it looks like the 2022 reach values are the pure maximum, and older values are the reach range, but it’s not always easy to tell (the Robotics Age article doesn’t specify, for instance). I’ve opted to use the values given without making adjustments, but some quick estimates (scaling maximum reach down by 30% or so to make it comparable to maximum range) suggests it won’t change conclusions terribly much. But a deeper, more quantitative analysis would have to correct for this.
From what I've read, one of the areas of advancement has also been better control over acceleration, with "soft" starts and stops at the end of motion. This would reduce wear and tear and power consumption, and allow for faster motion, since the peak speed in the middle of motion can be higher without damaging things. Older control systems didn't have this capability to the same degree.
People interested in this may want to head to the Automate Conference in Chicago this May.
https://www.automateshow.com/press-releases/automate-is-officially-annual-next-stop-chicago-2024