A recent viral tweet by Micah Springut, founder of stone-carving startup Monumental Labs, argued that it will be cheaper to build buildings with stone than with steel or concrete within the next 10 years.
Stone has of course been used for thousands of years as a construction material, and is still used today for things like building cladding. For instance, the Empire State Building is clad in limestone. But for the load-bearing structure that holds the building up, stone has been almost entirely replaced by modern materials like concrete, steel and dimensional/engineered lumber.
Why should we expect stone to get cheaper than concrete or steel? The basic argument is that stone is expensive primarily because of the high cost of finishing it: it requires skilled masons to carve quarried stone into the proper shape, which is time-consuming and labor-intensive. As automation gets better, these costs will fall, making stone construction substantially cheaper than it is now. Springut’s company, Monumental, makes robotically-carved stone statues, and he thinks incredibly cheap automated stoneworking is near.
Most folks in the building industry will immediately roll their eyes at this claim, but there are actually some good reasons to believe that stone might be cheaper than concrete or steel if labor costs fall enough. Stone has an arguably simpler supply chain than concrete or steel, and it can potentially eliminate certain on-site construction tasks.
But it’s far from obvious that these advantages would be enough to overcome the benefits of concrete or steel, or the many disadvantages of working with stone. Even if stone construction were cheaper in some theoretical sense (which I highly doubt), practical concerns like needing to change building codes, develop supply chains, and train workers in the system would likely prevent stone from being cheaper in the next decade.
The case for stone
As building materials, concrete, stone, and steel all start out at the same place: rock dug out of the ground. For concrete and steel, turning this rock into a finished material means sending it through a long, multistep process that requires an enormous amount of expensive equipment and consumes a great deal of energy. With concrete, rock is crushed into small pieces called coarse aggregate, and other rock (specifically limestone) is crushed into a fine powder and heated in a kiln to turn it into cement.1 The cement and coarse aggregate will be mixed with water and sand, along with other chemicals called admixtures, to form concrete.
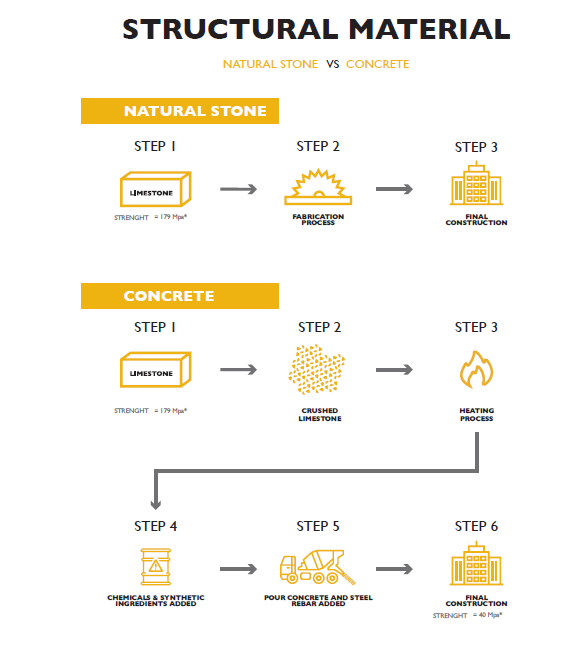
The steel production process is even more involved. It starts with iron ore that's dug out of the ground.2 Because most iron ore today is low-grade ore with a relatively small proportion of iron, the ore must then be sent to a beneficiation process to raise its iron content, which might involve crushing the iron ore, heating it, and compressing it into pellets. The beneficiated ore is then sent to a blast furnace which turns the pellets into liquid pig iron, and a basic oxygen furnace which turns the pig iron into steel. The steel will then be sent to rolling mills to turn it into finished products: beams, plates, rebar, steel sheet, and so on.
The process for producing finished stone, on the other hand, is simpler. Rock is simply quarried out of the ground, carved into the proper shape, and then sent to the jobsite. And not only is the production process for stone much simpler, but stone can simplify the construction process as well. Because stone already has an attractive and durable surface finish, you can eliminate some finishing tasks, like exterior cladding, drywall, and painting. Stone is also stronger than concrete, and so a stone structural element could theoretically be smaller and lighter than a concrete one. Like concrete, stone is weak in tension, but this can be addressed by using post-tensioning: running a steel cable through the stone and tensioning it. This would allow stone to be used not only for compression elements such as columns, but also for spanning elements like beams and slabs.
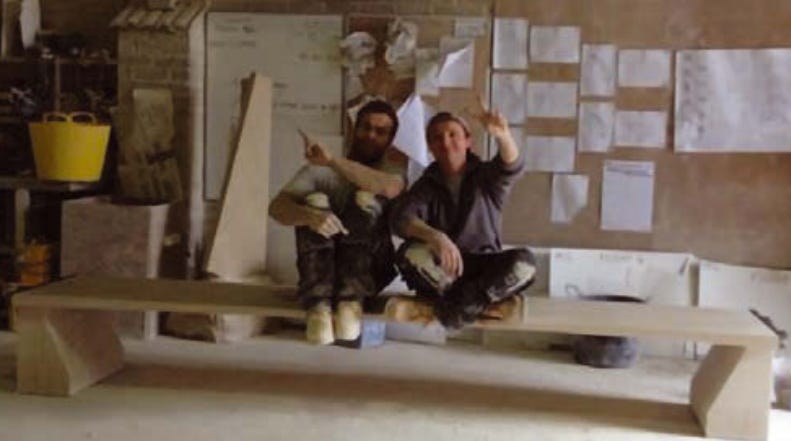
Not only does stone have a simpler production process, but it’s far less energy intensive to produce. Heating cement in a kiln and melting down iron ore both require large amounts of energy: around 20-30% of the cost of concrete, and 20-40% of the cost of steel, goes to the energy required to produce it.3 Stone, on the other hand, doesn’t have these heating steps, and will naturally consume less energy.
According to stone proponents, these various advantages make stone inherently superior to concrete and steel. It’s only the high labor costs of working with the material that has prevented stone from being used widely. A small but vocal group of architects and engineers is advocating for the return to stone construction, though their arguments are more focused on the carbon benefits of stone — stone’s simpler and less energy-intensive supply chain means that it theoretically has much lower embodied carbon than concrete or steel. One of them, Webb Yates, has even produced a conceptual design for a 30-story stone skyscraper.
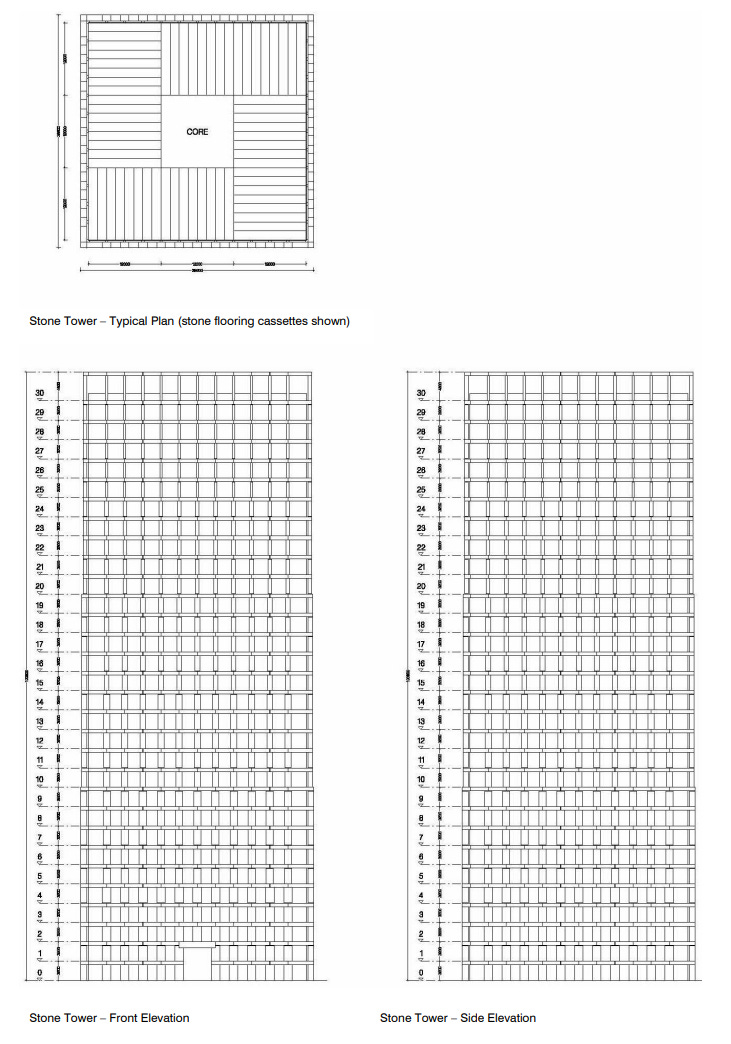
At the moment, this advocacy is mostly theoretical. Stone is commonly used for cladding, and is occasionally used as a masonry alternative (such as in Kenya, or by this Texas homebuilder, or simply for stone walls), but it’s hard to find even a single example of it being used as the primary structural material, including spanning members, in a modern commercial building. Even buildings feted for their use of structural stone, such as Clerkenwell Close or this French housing project, seem to limit the stone use to the facade, with more conventional structural materials such as steel and concrete for the interior structure. Webb Yates seems to mostly use stone for stairs inside of luxurious London homes. But a small but vocal group of architects and engineers can be surprisingly influential (such advocacy has helped drive the advance of mass timber), and it’s not impossible that stone could make a comeback, especially if automation makes using it much cheaper.
The case against stone
However, I think most of these pro-stone arguments are much weaker than they seem, and I would be very surprised if stone made a comeback as a structural material.
First, let’s consider the issue of supply chains. Stone’s shorter, simpler production process is a real advantage that could, theoretically, lower costs. Removing steps from a production process is one of the main mechanisms at work in Lean Methods (industrial improvement methods which aim to eliminate wasteful operations in a process), and Design for Manufacturing and Assembly (which aims to design products so they’re easy and inexpensive to produce). It’s also one of Elon Musk’s five rules for manufacturing improvement. I’ve also argued previously that the extra, expensive process steps in mass timber manufacturing are part of what makes it inherently more expensive than light-framed wood construction. All else being equal, fewer process steps means lower costs.
But often all else is not equal. While cutting out steps for a particular process will reduce its costs, one must be very careful when comparing two very different processes and assuming the one with fewer steps will be cheaper. In particular, this sort of analysis ignores the enormous potential benefits of economies of scale. In large, high-volume processes, “extra” process steps are often very, very inexpensive in unit-cost terms. It’s often worth it to use a longer, more involved process, if doing so lets you take greater advantage of economies of scale.4
We saw this sort of mechanism at work with semiconductor manufacturing. As time has gone on and Moore’s Law has advanced, producing semiconductor devices has required more and more process steps, and more and more expensive fabrication facilities. However, as this was happening, the cost of semiconductors fell: shrinking component size and larger silicon wafers meant that more components could be produced at a time, more than offsetting the added production costs.5
More generally, people tend to have poor intuitions about how expensive large-volume processes are in unit terms, and how little an extra step adds to the cost of something. Environmentally-minded folks often desperately want to believe long global supply chains are inefficient, especially those that seem to add thousands of miles of unnecessary transport, but a cost breakdown shows these steps are actually incredibly inexpensive.
For instance, cotton grown in the U.S. might get shipped to Bangladesh to be turned into a T-shirt, only to be shipped BACK to the U.S. to be sold: what could be more wasteful! But looking at a breakdown of the costs of a T-shirt, shipping and logistics is a tiny proportion of the manufacturing costs, which itself is a small fraction of the retail price of the shirt. For an $8 dollar T-shirt, transporting it from Bangladesh to the U.S. or to Europe costs just a few pennies. Similarly, it requires an enormous global supply chain with (plausibly) thousands of process steps to produce a McDonald’s cheeseburger, but that cheeseburger still only costs $2.59. If you have a Doordash driver bring it to you, that single trip of a few miles will be more expensive than every other part of the process combined.
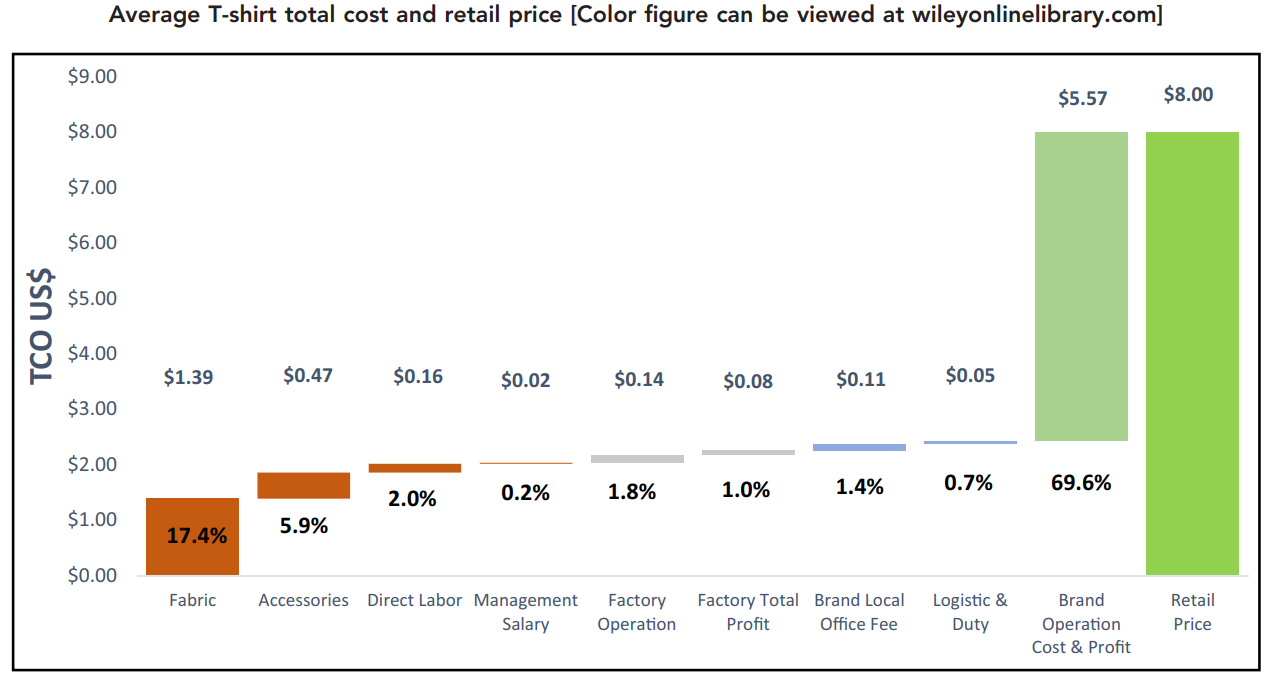
To return to construction, the long and involved production processes for steel and concrete may appear ripe to be disrupted by stone’s simpler process, but steel and concrete are produced in high-volume processes that can achieve significant economies of scale. Materials are handled with continuous process machinery or with bulk processing methods such as blasting, both of which can achieve very low unit costs. It’s not obvious to me whether such economies of scale are possible with stone, even if you could significantly automate much of its production. I can imagine that stone would need to be carefully worked piece by piece, and wouldn’t be as amenable to bulk or continuous processing manufacturing methods used for steel and concrete. It’s notable that right now in the US, even bulk, unfinished fieldstone is several times more expensive on a unit basis than concrete is. It’s possible that very good automation could close this gap, but there’s reason to be skeptical.
To get a better sense of whether concrete is fundamentally more expensive than stone if labor costs drop, we can look at another pair of building materials: dimensional lumber and oriented strand board (OSB). Dimensional lumber is like stone in some ways: wood gets cut from its origin material (tree trunks) into the proper shape, and is used directly. While most dimensional lumber is produced in high-volume lumber mills, it’s possible to produce it using simpler, small-scale portable sawmills.
OSB, on the other hand, is more like concrete. Instead of using the lumber directly, wood is instead chopped up into tiny pieces, then glued back together using resins and extruded into sheets. Like concrete, making OSB requires large, expensive process machinery. Critically, both dimensional lumber and OSB use highly automated manufacturing processes, eliminating the question of whether one is more expensive because it hasn’t been automated yet.
But despite the complexity and overhead of the OSB manufacturing process, it's still incredibly inexpensive. On a board-foot basis (a board-foot is a 12-inch by 12-inch by 1-inch square of wood), OSB is cheaper than almost every type of dimensional lumber, sometimes dramatically so. Depending on when and how it was done, this estimate might change (my 2024 Construction Estimator has OSB coming out more expensive), but it illustrates the basic point: large-scale production operations can produce things very cheaply, even if the equipment and number of process steps required seem like they should be expensive.
This leads us to another fact of manufacturing that I think is often not appreciated: not all automation is created equal. Two highly automated processes can differ dramatically in how expensive they are. CNC machining and 3D printing, for instance, are much more expensive than injection molding for large-volume production, despite the fact that all three processes are highly automated. A key question for stone advocates is not whether finishing stone can be automated (it obviously can), or whether that will reduce costs (it obviously will), but what sort of scale effects are possible.
Aside from questions of material production cost, there are many drawbacks to using stone as a structural material. The OSB and dimensional lumber comparison points us to one, that of verifying mechanical properties. Highly processed materials like steel, concrete, and engineered lumber tend to have fairly uniform and predictable mechanical properties, as individual variation in the raw material tends to average out when it's chopped up and reformed from many tiny pieces.
But when using a natural material directly, this is no longer true. Defects or impurities in the material may greatly compromise its strength or other mechanical properties. With dimensional lumber, determining capacity requires visually inspecting or mechanically testing each individual piece of lumber, and these estimates must be very conservative due to their fundamental imprecision. Right now, determining structural stone’s mechanical properties requires mechanically testing many individual samples and performing a complex statistical analysis to determine what a safe capacity is, taking into account that a stone block may have hidden flaws and weaknesses that reduce its capacity. An article on structural stone’s mechanical properties spends a third of its pages talking about what statistical distribution is best to use (it recommends a Weibull distribution). The upshot to this is that the design strength of stone (what you could rely on the material achieving) would be much less than its theoretical maximum strength, reducing or even eliminating its strength advantage over concrete.
Another major drawback of stone compared to concrete and steel is that the latter two materials can be worked in a flowable state. For concrete, this is done at the jobsite or the factory (pouring liquid concrete into forms and letting it cure), while for steel this takes place at the mill (heating up steel and then squeezing it into different shapes via hot rolling, or simply bending it cold using cold-forming). This makes it possible to relatively easily form concrete and steel into a variety of efficient structural shapes (shapes with low weight but high moment of inertia). With concrete, this also makes it possible to have thin, continuous concrete slabs (commonly used for high-rise construction), and to cast in any connectors or inserts that are required.
Stone, on the other hand, can’t be handled in a flowable state. Making it into an efficient structural shape would be much more involved (lots of cutting would be required), as would installing any connectors or post-tensioning cable (the latter would require drilling very long, straight holes). The sort of thin, continuous slabs that are standard in commercial buildings wouldn’t be possible with stone, requiring things like post-tensioned single-span stone slabs (a reasonable option) or strange, corner-supported stone squares. Stone advocates might argue that stone doesn’t require the formwork that concrete does, but setting up formwork is the exact sort of process likely to be made cheaper by the rising tide of improved automation.
Even if these concerns could be addressed, getting to this point would be a long and arduous journey, and would almost certainly take longer than a decade. Getting a novel building system adopted (and structural stone is “novel” in modern construction despite its long historic use) requires an enormous amount of effort sustained over years to move the wheels of the various bureaucracies. A novel building system needs a building code pathway that makes it possible to use it, and building officials willing to sign off on projects that use it. It needs a robust supply chain to supply parts and materials, and designers who know how to arrange a building to best take advantage of it, and construction workers who know how to work with it on-site.
This all takes time to put in place. Mass timber advocates have been pushing for its adoption in the U.S. for over a decade at this point, and had European and Canadian movements to build off of, and it’s still an extremely niche material in the US. And without robust supply chains and expertise at using systems, building systems tend to remain more expensive, even if they're cheaper in some theoretical sense. Stone has nowhere near the advocacy that mass timber has, which would greatly limit its progress even in the absence of any other issues.
To sum up: there’s a few reasons to believe that stone construction could theoretically be cheaper than concrete or steel, based on the fact that stone could have simpler supply chains and construction process, and be less energy intensive to produce. And there's a small group of architects and engineers (most of whom are talking their own book) advocating for the material. But the theoretical lower cost of stone is partly based on intuitions that don't take into account economies of scale, which can make added process steps and long supply chains surprisingly inexpensive. Highly processed materials like OSB can be as cheap or cheaper than “raw” ones like dimensional lumber, and it's not clear if structural stone could be produced as cheaply as concrete or steel, even if automation greatly improved.
Even if stone became cost competitive as a raw material, there would still be practical problems that would make it less attractive than steel or concrete. And the nature of material adoption would mean that even if it was cheaper at maturity, the path to get there would be long and burdensome, even if the will existed to push it forward. Right now, in the U.S., it doesn’t.
Some aggregate, such as sand and some gravel, can also be excavated directly from the earth.
In the US, most steel today is actually recycled steel made in electric arc furnaces, but around the world most new steel starts as iron ore.
This site gives the energy embodiment in concrete as 2778 MJ per cubic meter. Converting that to cubic yards, and to kilowatt hours, and then using the average cost of industrial electricity in the US (about 8 cents per kilowatt hour) yields about $80 dollars, vs $300-$350 dollars for a yard of concrete per RSMeans.
Incidentally, inability to appreciate the benefits of economies of scale is a major weakness of many Lean Methods advocates.
In the last 10 years or so, this has become less true, leading some to declare that Moore’s Law is dead in economic terms.
Well argued article, especially like the focus on economies of scale, perhaps the least understood driver of economic growth but probably one of the most major factors.
Less ambitious use of stone might be to replace bricks, we use a lot of bricks in house construction in UK. Manufacturing bricks is fairly energy intensive so maybe automation could shift the balance between the ease of handling clay vs cost of cutting raw stone? Potentially early adaptors who just prefer the finish of stone could drive this even at higher costs.
The "case against stone" as a replacement for concrete and steel is so clear it never went to trial. A subtractive process from an irregular material (particularly with the density and hardness of stone) will never be a cost effective alternative to consistent, moldable and formed parts. But isn't reducing the cost of bespoke stone parts enough of a triumph on its own without making this crazy claim? Cool tech!