Materials make up a substantial fraction of the costs of new construction. When we previously looked at a collection of 40 different construction tasks, on average materials made up 62% of the cost of the task. And for an average new house, materials make up roughly 50% of direct costs (excluding things like profit, marketing, development costs, etc).
Because such a large portion of construction costs come from materials, an obvious cost reduction strategy is to find a way to use fewer materials (and, to a lesser extent, use lighter materials instead of heavier ones).1 This is a popular topic for researchers studying new building technologies (though they often focus more on reducing embodied carbon than on costs per se), but you also see it crop up in the commercial world as well.
The main problem with this strategy is that because it's so obvious, the low-hanging fruit in material reduction has already been picked. Modern structures are fairly light and efficient, and while it's often possible to cut even more material out of them, it's seldom an easy win without tradeoffs.
A brief overview of structural efficiency
The various components of a building need enough strength to support the loading on them (including the weight of people, furniture, and the building itself, wind blowing against the building, etc.) and to transfer those forces into the foundation. Structural elements, such as the beams and columns that hold up the floors of a building, require this strength, and so do non-structural elements, such as windows that need to withstand wind and transfer that load into the rest of the building
There are, broadly, three types of forces that need to be considered. Axial forces act along the length of a structural element, like a column holding up a large load. Shear forces act perpendicular to the length of a structural element. And bending forces are forces that are trying to bend a structural element.2 Often, a loading can produce multiple kinds of forces. For instance, a beam supported at each end with a continuous load along its length will have both shear forces and bending forces.
In addition to resisting these loads, building elements also need to resist deflections. A beam might have enough strength to support a heavy load, but if it sags significantly when loaded, that can still cause problems, such as water pooling up in the center or brittle finishes that crack when the beam shifts.
Of these various forces, bending forces and deflections are often the major drivers of the size of structural elements, because of how quickly they increase. For a beam, maximum shear is proportional to the length of the beam, while maximum bending is proportional to the length squared, and deflection is proportional to length to the 4th power. Doubling the length of a beam thus increases bending forces by a factor of 4 and deflections by a factor of 16.
The easiest way to increase bending and deflection resistance is to make a structural element deeper. Bending resistance is proportional to depth squared, and deflection resistance is proportional to depth to the third. A building element can thus better resist bending and deflection purely by being made deeper, even without adding more material. More generally, a structural element will best resist bending and deflection if the material in it is put as close to the outside edges as possible.
This leads to things like steel I-beams (today more properly called wide flange sections or W-sections), which puts most of the beam's mass on the two flanges at the top and bottom of the beam. It also leads to trusses, which are essentially a beam with a solid top and bottom “chord” where most of the interior has been cut away.

Structural elements are designed to be as materially efficient as possible, and have been for many decades. Wood trusses (made up of conventional lumber stitched together with steel plates) and wood I-joists (made up of engineered lumber top and bottom chords with a center “web” of oriented strand board, or OSB) are standard for residential construction in the US. Steel W-sections and steel joists (basically trusses) are standard for commercial construction. For even lighter steel construction, there is light gauge steel framing, which consists of very thin sheets of steel bent into structurally efficient shapes. There are also things like insulated metal panels, which are in some ways the platonic ideal of an efficient structural element: a thin sheet of steel on the top and bottom, separated by a layer of insulation. (The wood version of insulated metal panels, SIPS, never quite caught on in the US, though not for lack of trying.)
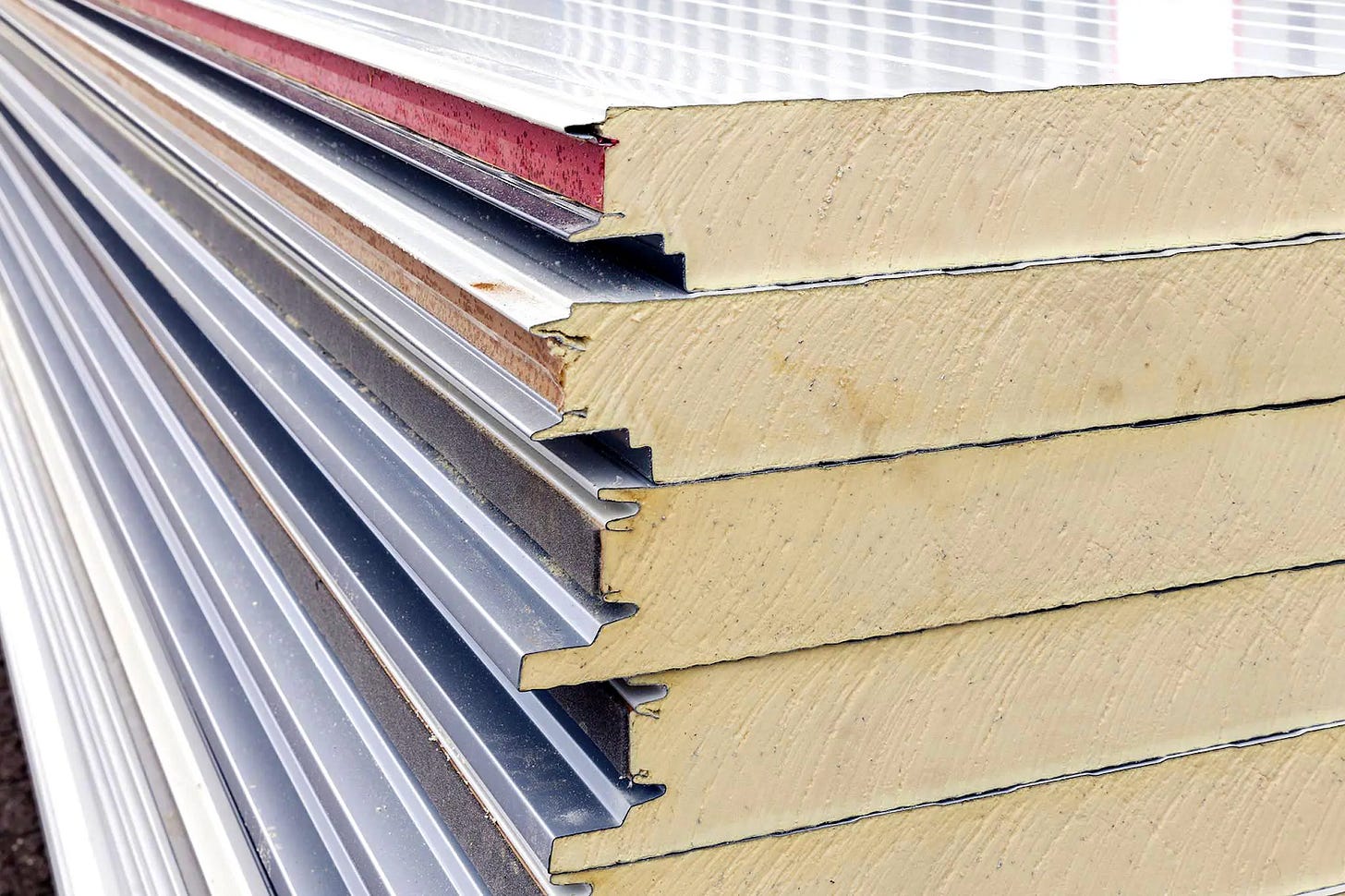
Even heavy, cheap materials like concrete are used in materially efficient ways. For concrete floors, a common construction method is to pour concrete over a ribbed metal deck. The ribs give the steel the strength to support the concrete while it's wet (eliminating the need for additional shoring), and give the whole assembly greater depth, increasing bending resistance and placing the steel at the outer edge where it's most useful. There are also things like hollowcore slabs (concrete slabs manufactured with voids in the middle), and concrete blocks (which are hollow in the middle, though many of the voids will have reinforcement placed in them and be grouted solid). And of course, there have been many attempts to find ways to further cut material out of concrete construction going back decades.
Minimizing the amount of material in the structure of a building is one of the main jobs of structural engineers, and they have many tools to help them do this. Software packages like RAM can calculate all the forces on a structure and choose the lightest beams and columns that will resist them. In very tall buildings, engineers will shrink the columns higher up the building as the forces to be resisted are lower.
We see a tendency towards reduced material in architectural elements as well, with hollow wooden doors replacing solid doors, and thin engineered wood floors replacing thicker solid sawn boards.
The challenge of further material reduction
This is not to say that buildings are as efficient as they can possibly be, and no more material reduction is possible. But as builders, architects and engineers have always focused on cutting material out of a building, the material that's left generally isn’t easily removed. Even material that may not be required structurally is often hard to remove for practical reasons.
Consider, for instance, the typical steel W-section, which has a solid top and bottom flange and a solid web of steel all along its length. You might look at this and think, “Maybe in some cases we could cut out some of the material from that solid web. After all, trusses can support loads with most of that center material carved away.” And in fact, you’d be correct: often the web material in a W-section isn’t strictly required structurally, especially for long-spanning beams. Indeed, there’s an entire type of beam that tries to take advantage of this called a castellated beam, which is made by cutting a normal W-section apart and stitching it back together with holes in the middle.
But in practice, it's rare to see castellated beams used. Empirically, the added costs of designing and fabricating them, and the additional coordination and scheduling requirements seldom seem to be worth the material savings. In most cases, it's far simpler (and less likely to cause a catastrophic coordination failure) to use standard, off-the-shelf W-sections and steel joists than to mess around with castellation.
Similarly, because columns are often governed by buckling failures, the most materially efficient column would be a tapered column that was larger in the center than on the ends. But this would be more expensive to fabricate (since it could no longer use a continuous process that produced a uniform section), and likely be somewhat awkward to use, since you’d no longer have continuous vertical surfaces to attach things to. The “most efficient” shape is rarely if ever used.3
Likewise, we’ve previously talked about advanced framing (sometimes called optimal value engineering), a method of light framed wood design that uses less lumber by arranging structural elements to streamline load paths and minimize redundancy. Though this seems like an easy win (estimates range from 10-25% reduction in framing material costs, and potentially even larger labor savings), empirically builders seem reluctant to take it, due to the added coordination difficulties and design effort, and the potential downside if the carpenters make a mistake.4 A slightly misplaced floor joist that can be easily accommodated by normal framing could cause a serious issue in advanced framing were it not caught and repaired.
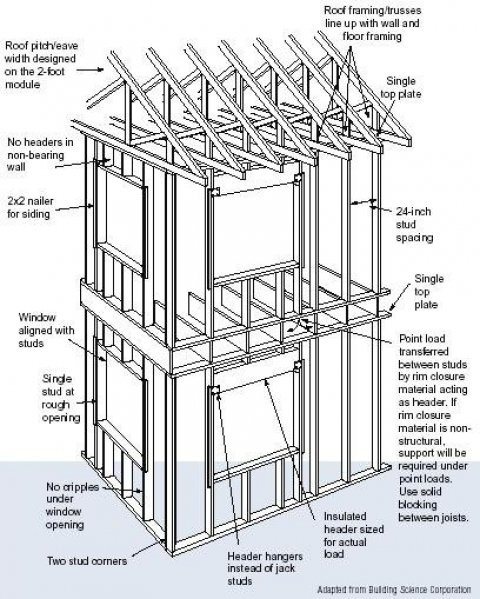
A similar tradeoff exists with other technologies that could potentially cut material out of a building. This research effort, for instance, made the rounds a few years ago as a way to dramatically reduce the amount of material in a concrete floor by automatically assembling a sort of two-way tied arch. But not only would this complex method of construction almost certainly add design and fabrication expense, it requires much deeper floors than would otherwise be required, which would add both height and cost to the building. In general, developers prefer their floors to be a) as thin as possible and b) as simple to build as possible, which is why concrete construction has converged on building methods like post-tensioned slabs, and has eschewed methods like voided slabs or waffle slabs that might use less material but add depth and construction complexity.
In other cases, the limitations on material reduction have more to do with building form. Most buildings, for instance, are rectangles that contain a series of rectangular rooms, because of the many benefits of this sort of arrangement. A rectangular room is easy to use (since you can push furniture flush against the walls), easy to build, packs tightly together against other rectangular rooms, and so on. Technically circle or sphere-shaped buildings would be more materially efficient (requiring less material to enclose a given amount of space), but while in some cases you see this (such as with pressurized storage tanks or the brief fad of octagonal houses in the 19th century), in general the material savings is not worth the added construction complexity, cost, and loss of convenience.
With architectural elements, we see the same general phenomenon, where further material reductions come with performance tradeoffs. In general, thick, heavy materials feel better than lighter, flimsy materials, and all else being equal people prefer the former to the latter. This is one of the reasons that drywall substitutes like vinyl on gypsum have had limited appeal, and why people still want tiled bathrooms even though fiberglass or acrylic are probably superior from a pure performance perspective.
The idea of reducing building costs by using fewer materials has motivated builders, architects, and engineers since essentially forever. Because of this, I’m generally somewhat bearish on the possibility of cutting costs by developing new, more materially efficient building technologies. In many cases we already have more materially efficient systems waiting in the wings that aren’t used because of the various costs, complexities and risks they introduce. I don’t think there’s zero opportunity here, but the material that’s currently used in a building is generally going to be very hard to remove, and removing it will come with a lot of tradeoffs.
Lighter materials are in some cases cheaper, and often require less effort to install (since they’re easier to move around, require less equipment, etc.), but there’s not a straightforward “lighter = cheaper” relationship. Many heavy materials are cheap, such as concrete, and many light ones are expensive, such as titanium or aluminum.
There are also torsion forces, but these are typically less of a consideration.
You do see tapered, non-uniform columns in metal buildings, however, though they usually have a vertical surface on one side.
Another important consideration is resistance to infrequent environmental effects. While a very light material might perform the same as a heavy-duty one 99% of the time, it might fail in the 1% case, or in black-swan-like scenarios.
Some of the high tech construction techniques replace materials with complexity. You wonder how long such buildings would last if they were to suffer damage or deterioration i.e., could they be repaired or refurbished and if not do they need to be torn down. A simple example are UPVC windows commonly used in the UK to replace wood often sold as needing no maintenance. True they don’t rot, but they certainly do deteriorate and have a fixed life. A carefully maintained quality wooden framed window may not perform so well thermally but could last over 100 years. There are plenty of buildings in the UK built 600 years ago and which are still reparable using simple methods and with care could last another 400years. Low tech construction techniques may use more materials, but if the building lasted 1000 years, less materials would be used than with high tech buildings if they have to be replaced 10 times in the same period .. and this doesn’t even account for the high complexity/high energy supply chain that accompanies high tech construction.