A prophecy expressed frequently in engineering circles at the present day is that turbines actuated by hot gases, other than steam, will eventually come to the front as prime movers.
— A Scientific Investigation Into the Possibilities of Gas-Turbines, RM Nielsen, 1904
It was only a matter time before the Brayton-cycle gas turbine design fulfilled its potential via advances made in materials, coatings, and the 3D aero design of axial compressors.
— Gas Turbines for Electric Power Generation, Gulen, 2019
In the last newsletter we looked at the history of fracking technology in the US. With fracking, energy companies unlocked enormous amounts of natural gas in previously inaccessible shale deposits. Since the fracking revolution of the early 2000s, annual natural gas production in the US has doubled.
But an abundant supply of natural gas is only part of the story of the shale energy revolution. As drillers were refining their shale gas fracking techniques, utility companies were building enormous numbers of natural gas-burning power plants. Between 1990 and 2005, the US built about 260 gigawatts of natural gas power plants, and today natural gas supplies roughly 40% of US electricity, about twice as much as the next largest source.1 It’s somewhat unfortunate that natural gas plants are carbon emitting, as that dulls enthusiasm for a very impressive feat of infrastructure construction.

These gas power plants were overwhelmingly gas turbines, either on their own or in “combined cycle” plants, where hot exhaust from a gas turbine is used to heat water and drive a steam turbine. Today, gas turbine and combined cycle plants make up 86% of natural gas power plant capacity, with the balance being conventional steam turbine plants that use natural gas as a fuel.
Both gas and steam turbines work on similar principles. In a steam turbine, water is pumped through a boiler to become steam, and is then sent through a turbine, a series of rotors with airfoils mounted around the edge. As the steam flows through the turbine, the rotors spin, converting the heat energy of the steam into mechanical energy (which is then converted to electrical energy by a generator). In a gas turbine, air is pressurized by a compressor, and then sent to a combustion chamber, where it's mixed with fuel and burned. The hot gasses from combustion then drive the turbine rotors directly, rather than being used to heat up water.
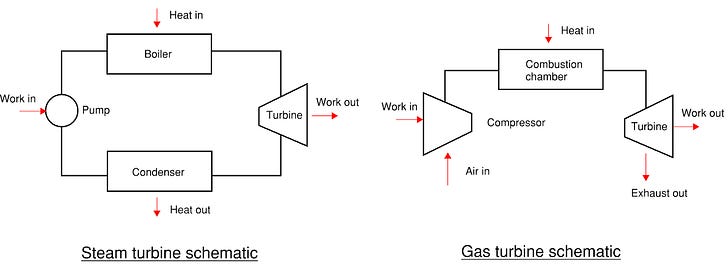
Though they work on similar principles, gas turbines took much longer to deploy than steam turbines. Both were first developed in the late 19th and early 20th centuries. But while the steam turbine was widely used to generate electric power by the 1910s, gas turbines weren’t used in appreciable numbers for electricity generation until the 1960s, and weren’t widely deployed until the late 1980s.
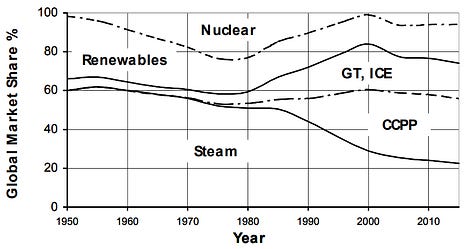
Why did the gas turbine come so much later than the steam turbine? And why did it eventually conquer the electric power industry? Let’s take a look.
Origins of the gas and steam turbine
The idea of using the force of steam to generate rotational energy dates back to Hero of Alexandria, but the invention of the modern steam turbine is generally credited to Charles Parsons, who in 1884 built a 7.5 kilowatt turbine connected to a dynamo that was used to generate power for electric lighting on ships. Over the next five years Parsons built more than 300 steam turbines for shipboard use, and in 1890 built the first steam-turbine powered central electric power station. The steam turbine was smaller, more efficient, less noisy, and could be built much larger than the reciprocating engines then used to generate electric power, and by the early 1900s power companies began to widely adopt steam turbines. By the 1920s Parsons was building enormous, 50,000 kilowatt (or 50 megawatt) steam turbines for central station use, and steam turbines were built by every major manufacturer in America.
As more steam turbines were being built in the early 20th century, engineers also experimented with gas turbines. Because a gas turbine could use burning gasses directly instead of using them to heat up water first, it was theoretically simpler than a steam turbine. A gas turbine could omit heat exchangers, boilers, cooling towers, and all the other steam-handling equipment that a steam turbine required. This made a gas turbine a compelling proposition, if it could be made to work. In his 1939 retrospective on the early history of gas turbines, Adolf Meyer described them as “the long cherished dream of engineers,” and that “hardly any other kind of machine has received more attention from inventors, skilled and otherwise.” By 1900, there had been hundreds of proposals to build a gas turbine.
As with the steam turbine, the basic ideas behind the gas turbine preceded its construction by many years. Smoke jacks, which used rising smoke and hot air to rotate a fan which turned a spit, date to the 1400s, and in 1791 John Barber patented the design for a gas turbine (though it was never built). But modern gas turbines weren’t built until the early 1900s. In 1903, Rene Armengaud and Charles Lemale built a gas turbine in Paris that successfully generated 220 kilowatts of work. In 1904, F. Stolze built a “hot air engine” in Berlin, which used compressed air that had been heated in a furnace to drive a turbine. And between 1903 and 1907, extensive experiments on gas turbines were performed at General Electric by Sanford Moss (who would spend the rest of his career developing turbochargers for aircraft engines).
But these early attempts to build a gas turbine all ended in failure. Stolze’s turbine failed to generate enough work to even run the air compressor. Armengaud and Lemale’s turbine fared better, but it was “woefully inefficient,” with a thermal efficiency of just 2-3%, about one-eighth the efficiency of piston engines at the time. GE’s experiments yielded similar results.
These early failures can be traced to low operating temperatures and inefficiencies in the various turbine components, particularly the compressor. Early engineers couldn’t build a compressor that was efficient enough, or a turbine that could run hot enough, to produce useful amounts of work.
But early steam turbines worked on similar principles as the gas turbine, and were subject to the same limitations. Yet while early 20th century gas turbines struggled to produce any useful work at all, steam turbines proved to be far more efficient than existing reciprocating engines, and quickly took over the electric power industry.
To understand why the steam turbine was initially so much more successful than the gas turbine, we need to learn a little bit more about how a turbine works.
Heat engine thermodynamics
The steam turbine and gas turbine are both heat engines: they take in heat energy, convert some portion of it into mechanical energy, and exhaust the remaining heat into the surrounding environment.
To understand how this actually happens, let’s look at the Carnot cycle, a theoretical model of an “ideal” heat engine. Consider a gas-filled cylinder with a piston in it, which can be connected to either a heat source (TH) or a heat sink (TL). The cycle starts with the piston near the end of the cylinder, and the temperature of the gas is the same as the heat source.
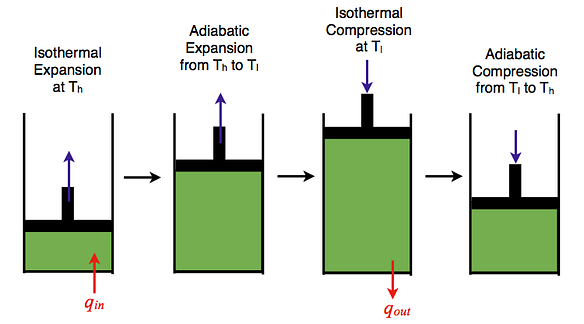
In step 1 of the cycle, the cylinder is connected to TH, allowing heat to enter, and the piston is retracted, expanding the volume of the gas. Ordinarily this would result in the temperature of the gas decreasing, but in this theoretical case each infinitesimal increase in volume is balanced by an infinitesimal addition of heat energy from TH, and temperature stays constant as the gas expands.
In step 2, the connection to the heat source is severed, but the gas continues to expand, lowering the temperature until it reaches the temperature of the heat sink.
Step 3 is a reverse of step 1. The gas is connected to the heat sink and the piston compresses the gas. Each infinitesimal decrease in volume is balanced by a transfer of heat energy to the heat sink, keeping the temperature constant as the gas is compressed. And step 4 is a reverse of step 2. The link to the heat sink is severed and the piston continues to compress, decreasing the volume of the gas and raising its temperature to the temperature of the heat source. The cylinder is now in the same state it was at the beginning, and the cycle repeats.
One way of understanding the Carnot cycle is with a temperature-entropy plot, or T-S plot, where entropy (S) is equal to heat energy (Q) divided by the temperature (T).
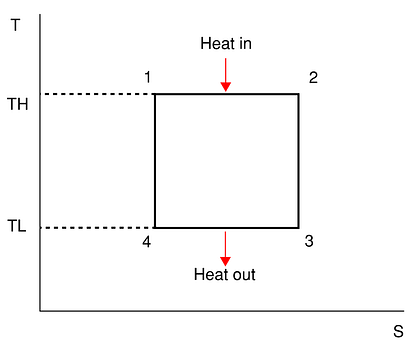
Starting from point 1, the cycle first increases the entropy of the gas at constant temperature (since heat energy gets added), then decreases the temperature of the gas without changing its entropy (since no heat energy is added or lost), then decreases the entropy of the gas at constant temperature (exhausting heat into the heat sink), and finally increases the temperature of the gas at constant entropy. On a T-S plot, the work done each time the cycle is completed is equal to the area enclosed by the cycle. The greater the temperature of your heat source or the lower temperature of your heat sink, the larger the area of the cycle and the greater the work done.
A key aspect of the Carnot cycle, and any heat engine, is that only a portion of the heat energy absorbed in step 1 gets converted to mechanical energy. The rest gets dumped into the heat sink. The fraction of heat energy that is converted into mechanical energy is the thermal efficiency of an engine, and is equal to the area enclosed by the cycle divided by the entire area beneath step 1 of the cycle. This works out to 1 - TL / TH, one minus the temperature of the heat sink, divided by the temperature of the heat source. The higher the temperature of the source, or the lower the temperature of the sink, the more thermally efficient the engine is.2
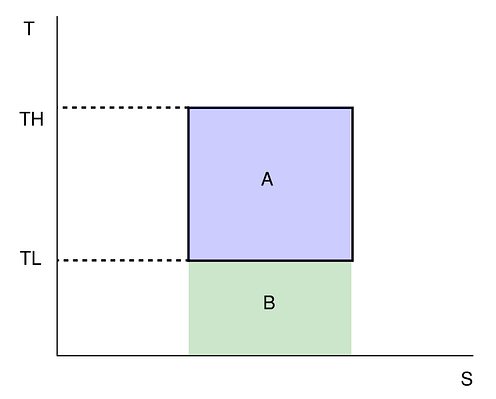
The Carnot cycle is a useful theoretical model of an ideal heat engine, but in real life it's impractical to add and remove heat from a gas without raising or lowering its temperature. To understand the behavior of actual engines that can be built in the real world, we want to use a cycle based on how the engine actually functions. Gas turbines can be modeled by the Brayton cycle. The Brayton cycle is similar to the Carnot cycle, except that the temperature of the gas rises and falls when heat energy is added/removed. (As we can see, this makes the Brayton cycle less thermally efficient than the Carnot cycle.)
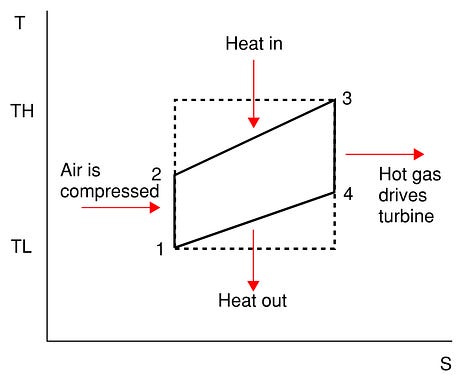
In the Brayton cycle, air is first compressed, increasing its temperature and pressure and decreasing its volume. This air is then fed into a combustion chamber where it's mixed with fuel and burned, adding heat energy to it and increasing its temperature further, but keeping its pressure constant. The hot exhaust from the combustion chamber is then fed through a turbine, which lowers the temperature and pressure of the gas as heat energy is extracted and turned into mechanical energy. This hot gas is then either cooled down and sent back to the compressor (in a ‘closed cycle’ turbine), or vented into the atmosphere (in an ‘open cycle’ turbine). As with the Carnot cycle, we have four steps: compression, heat addition, expansion, and heat removal.3
A steam turbine is modeled by a slightly different cycle, called the Rankine cycle. In the Rankine cycle, liquid water is pumped into a boiler, where heat energy is added and the water turns to steam. The steam is sent through a turbine where it expands, lowering its temperature and pressure as heat energy is extracted. The steam is then condensed back into liquid water in a condenser, dumping its remaining heat energy, and is sent back to the pump to repeat the cycle.
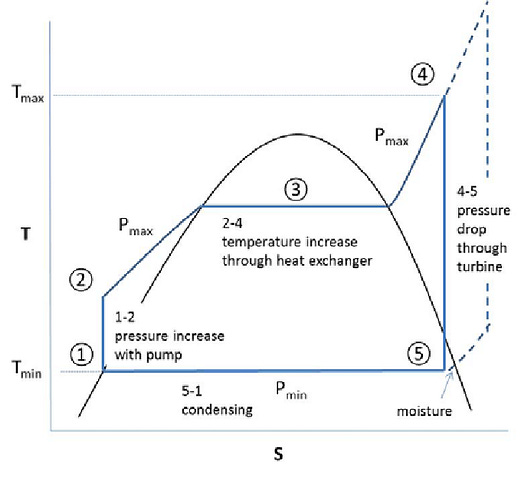
We once again see the same four steps of compression (via pump), heat addition, expansion and heat removal, though the nature of the working fluid means they look slightly different than in a Brayton cycle. Specifically: when water is being transformed from liquid to gas, heat is added/removed without an increase in temperature, yielding straight horizontal lines on the temperature-entropy diagram.
In both the Brayton and the Rankine cycle, the compressor in step 1 is driven by the turbine, and the net output of the engine will be the work done by the turbine minus the work required to run the compressor. The fraction of the turbine’s work required to run the compressor is known as the “back work ratio.”
In a Rankine cycle, the back work ratio will be very low, on the order of 1% or less. In a Brayton cycle on the other hand, the back work ratio will be very high. Driving the compressor might take 50% or more of the work done by the turbine.
The difference in back work ratios is due to differences in the working fluid. In a Rankine cycle, the compression step takes place with a liquid, whereas a Brayton cycle is compressing a gas. It takes much more work to increase the pressure of a gas than it does a liquid.4
“Ideal” Rankine and Brayton cycles assume that the compressors and turbine components have 100% “isentropic” efficiency: that they can perfectly convert heat energy into mechanical energy (or vice versa) without any increase in entropy. And with a perfectly efficient compressor, this high back work ratio is not an issue. The energy used to drive the compressor will all be converted to energy in the air that's being compressed, which will then be recaptured by the turbine. But real components are never 100% efficient. Some fraction of the energy fed into them will be “lost” as friction, vibration, and so on. And the higher the back work ratio — the more energy the turbine must supply to the compressor — the greater the losses from component inefficiencies. If my compressor is 90% efficient, that 10% loss means much less on a pump that requires 1% of the turbine’s work than an air compressor that requires 50% of the turbine’s work.
Thus, Brayton cycle engines, with high back work ratios, are much more sensitive to compressor and turbine inefficiencies, particularly compressor inefficiencies, than Rankine cycle engines are.
(It’s worth emphasizing the two different concepts of efficiency we’re talking about here. Thermal efficiency is the fraction of input heat that's converted into mechanical energy by the engine. Isentropic efficiency is a measure of how much of the input energy to a compressor/turbine is lost to things like friction, turbulence, and other entropy-increasing effects. Thermal efficiency is what we ultimately care about, because that determines how much useful work we get from a given quantity of fuel. Isentropic efficiency of the engine components will affect how thermally efficient our engine is.)
Consider, for instance, a Brayton cycle gas turbine and a Rankine cycle steam turbine operating over the same temperature range, a low of 300 Kelvin (about 80 degrees Fahrenheit) and a high of 900 Kelvin. If both use perfectly efficient turbines and compressors (ie: transfer all input energy to/from the working fluid with no losses to things like friction), they will operate at very similar thermal efficiencies: 43.6% for the gas turbine and 41.9% for the steam turbine. But as the isentropic efficiency of the components decreases, the thermal efficiency of the gas turbine falls much faster than the steam turbine. With a compressor and turbine that are each 75% efficient (combined 56% isentropic efficiency), the net work done by the gas turbine falls to zero, while the steam turbine is still doing useful work at 31% thermal efficiency.

In the early 20th century, manufacturing technology and understanding of compressor behavior wasn’t advanced enough to produce efficient compressors and turbines. In his 1939 paper on early gas turbines, Meyer noted that early turbine builders would have struggled to build compressors even 70% efficient. When Frank Whittle designed an 80% efficient compressor in developing the gas turbine-based jet engine in the 1930s, it was a major advance over existing compressors.
Because of the difficulties in building very efficient compressors, people also looked for ways to build gas turbines that didn’t require them. The Holzwarth “explosion” turbine, for instance, was a gas turbine first built in 1908 that pressurized gas by exploding fuel in a combustion chamber, rather than by using a compressor. Holzwarth’s turbine worked, and they were built in small numbers through the 1930s, but they were mechanically complex and extremely inefficient compared to other types of engines, and the design was never widely adopted.
Inefficient compressors and turbines also affect gas turbine thermal efficiency in another way, via temperature. In an ideal Brayton cycle with no compressor or turbine losses, the thermal efficiency of the engine is a function of the pressure ratio: the post-compression pressure divided by the pre-compression pressure.5 The higher the pressure ratio, the greater the thermal efficiency of the engine. Modern land-based gas turbines typically have pressure ratios ranging from 8 to 20.
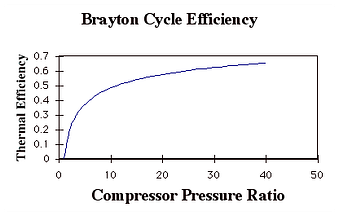
We can see why this is by looking at the T-S diagram. As we increase the pressure ratio, the temperature of the compressed gas increases, and the area enclosed by the cycle increases relative to the amount of heat dumped back into the environment.
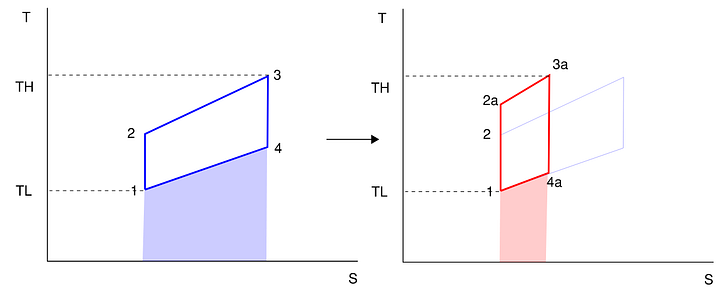
Thus, in an ideal Brayton cycle, we can increase the thermal efficiency by raising the pressure ratio, without needing to increase the operating temperature of the engine. Conversely, in an ideal Brayton cycle raising the operating temperature without increasing the pressure ratio won’t substantially increase thermal efficiency.
However, in real engines with compressor and turbine inefficiencies, this changes. We can once again see why by looking at the T-S diagram. While the theoretical Brayton cycle has vertical lines at the compression/expansion steps (indicating these do not increase entropy, ie: are reversible), in real engines these steps will have losses that increase entropy (ie: the lines are slanted). Once this is taken into account, raising the pressure ratio while keeping the operating temperature constant can decrease thermal efficiency.
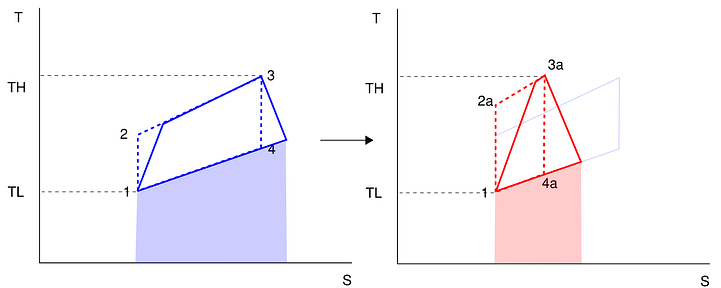
But we can overcome this problem by raising the operating temperature of our turbine, which lets us make use of higher pressure ratios even with efficiency losses in our components. For a Brayton cycle engine with less than perfectly efficient components, using a higher pressure ratio, and getting a higher thermal efficiency, requires running it at a higher temperature.
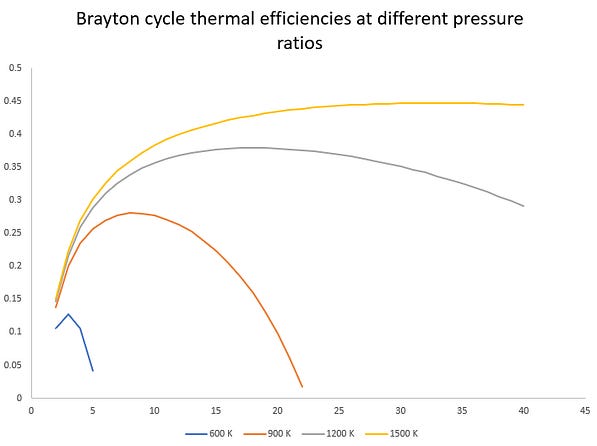
Raising the operating temperature of a gas turbine also has other benefits. It increases the amount of work done in a single cycle, which means you can get more work from the same amount of equipment. And it raises the temperature of the exhaust, which means any process that recaptures that heat, such as a steam turbine in a combined cycle plant, also gets more efficient.
Thus, achieving high thermal efficiencies in real world gas turbines means raising their operating temperature as high as possible. And while generating high temperatures is straightforward (the gas in a turbine burns at over 2000 degrees Kelvin), building turbine components, especially turbine blades, that can withstand high temperatures is much more difficult. In the early 20th century, turbine blades couldn’t withstand operating temperatures of more than about 1000 degrees Fahrenheit (~810 degrees Kelvin), which kept thermal efficiencies low.
Thus, in the early 20th century, the technology didn’t exist to build a gas turbine that could do useful amounts of work. Gas turbines, if they worked at all, were far less efficient than other sorts of engines. And because of their sensitivity to operating temperature and component efficiencies, gas turbines would lag behind steam turbines in thermal efficiency for most of the 20th century, and it was steam turbines that would dominate the electric power industry.
Slow and steady progress
By the 1930s, research on airfoils and the aerodynamics of moving air was being used to design more efficient turbines and compressors, which made it possible to build a gas turbine that did useful amounts of work. Velox boilers were built, using a gas turbine to force large amounts of hot air through a steam boiler (increasing the heat transfer rate and thus getting more work from a given amount of equipment).6 Gas turbines also started to be used in petroleum refining for blowing large amounts of air in Houdry catalytic cracking units.

But by far the most successful application of the gas turbine in the 1930s was in the jet engine, which was simultaneously developed by Frank Whittle in Britain and Hans von Ohain in Germany. Both Whittle’s and von Ohain’s engines first ran in 1937, and by the early 1940s several jet-powered aircraft were in operation.

These early gas turbines were less thermally efficient than other sorts of engines, but they had other features that nevertheless made them useful for certain applications. Velox boilers and Houdry units took advantage of the ability of a gas turbine to blow large volumes of hot air (the fact that gas turbines could actually generate positive amounts of work in Houdry units turned out to be an unexpected bonus). Jet engines didn’t have the aerodynamic limitations of propeller-based engines, making it possible to achieve much higher altitudes and aircraft speeds.
As jet engines powered aircraft, they were also generating electricity for the first time. The first gas turbine-based power plant in the world was built at Neuchâtel in Switzerland in 1939 by the Brown Boveri Company, which had invented the Velox boiler and built many Houdry unit turbines. Brown Boveri would go on to build 10 more gas turbine power plants over the next 6 years. The first gas turbine power plant in the US was built by GE in Oklahoma City in 1949.7 It used a turbine that had been originally designed to power a locomotive, and was based on the designs of the aircraft jet engines GE built during the war.
These first gas turbine power plants were inexpensive to build and ran reliably but were far less efficient than steam turbine plants. The Belle Isle plant operated at a thermal efficiency of around 17%, compared to the 30% or more that was achievable in steam turbines. The gas turbine was considered “the weak sister” of the steam turbine. The few gas turbine plants were mostly used for things like peak-loading or standby operation, where fuel use was less of a concern. Natural gas did become increasingly popular for electric power generation following WWII, but it was almost entirely used in conventional steam turbine plants. By 1962, worldwide electric generation capacity of gas turbines was just 4 gigawatts, roughly the equivalent of 10 large steam turbines.
But outside of the electricity sector, the gas turbine was finding more success. Hundreds of gas turbines found their way into industrial uses such as burning blast furnace gas in steel plants, pressurizing natural gas pipelines, and powering locomotives.
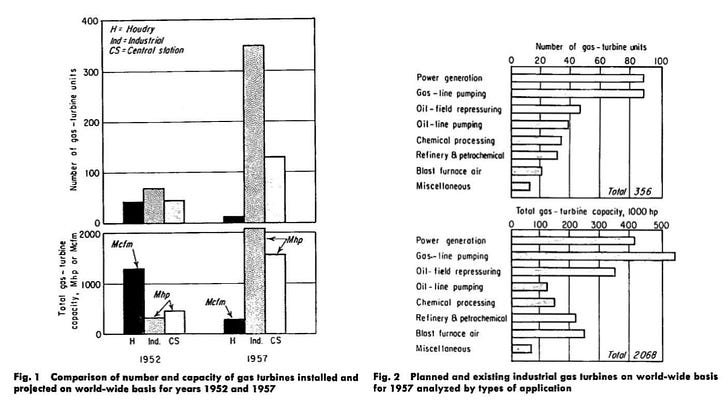
Gas turbines also began to be applied to ship propulsion, particularly for naval vessels where the high power-to-weight ratio of gas turbines allowed for faster speeds.
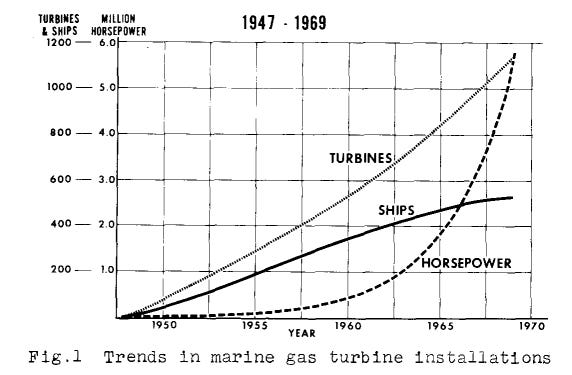
But the most important use of gas turbines continued to be the jet engine. By the end of the 1950s hundreds of thousands of jet engines had been built, and the jet engine was “almost universal in combat aircraft” and widely used by commercial airliners. To push the boundaries of jet engine performance, engine builders developed new high temperature “superalloys,” and techniques like vacuum induction melting and vacuum arc remelting to manufacture them. These developments raised the temperature turbine blades would withstand by nearly 100 degrees Kelvin. These alloys, and other jet engine technology, would then filter down into industrial gas turbines.
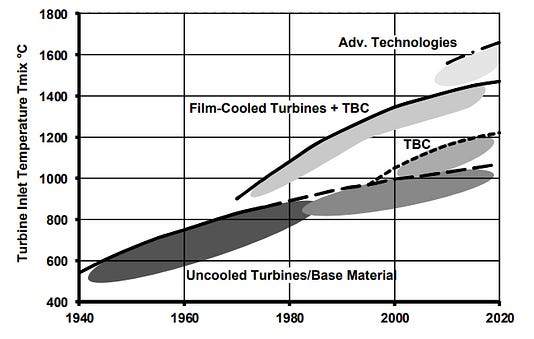
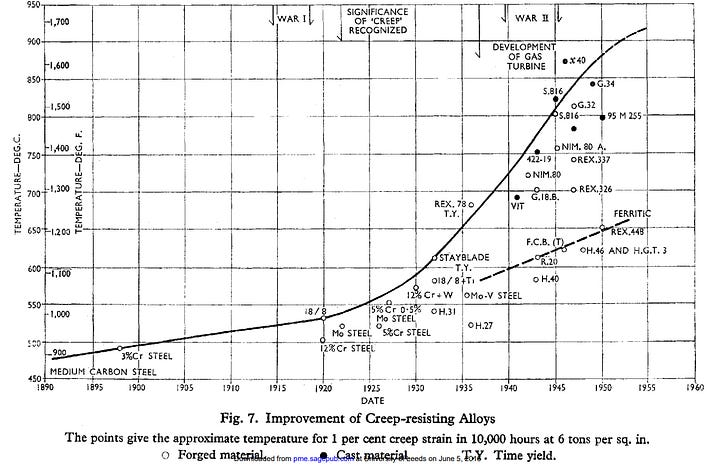
By the mid-1960s, increased turbine operating temperatures and pressure ratios had raised the thermal efficiency of simple gas turbines to 20-25%. And gas turbine plants were getting cheaper to build. Between the mid-1950s and the mid-1960s, the capital cost of a gas turbine plant fell by nearly 50%, below that of a coal-fired steam turbine. The comparatively small size of a gas turbine also made it possible to build “package” plants, which could be quickly assembled on-site from large, prefabricated components. Gas turbines were still uncompetitive with steam turbines once the costs of fuel were taken into account, but the gap was closing.

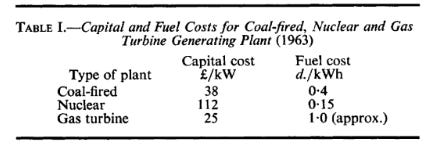
The first big break for gas turbine electric power came following the 1965 Northeast Blackout, which left 30 million people without power for hours in the Northeast US and Canada. Because starting and running a power plant requires a significant amount of electrical power, bringing a plant back online in a wide-scale power outage (known as a “black start”) is difficult. But gas turbines need comparatively little power to get started, making them useful for restoring a grid from black-start conditions. A gas turbine in New York was successfully used to restart the grid following the blackout, and almost overnight utilities ordered gas turbines by the hundreds to improve grid reliability. Between 1963 and 1975, gas turbine power plant capacity in the US increased by a factor of 70. Many of these turbines were essentially jet engines (aka “aeroderivative” turbines) redesigned to generate electric power.
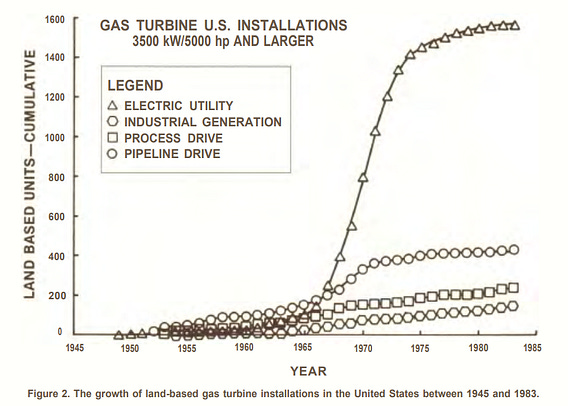
As gas turbines were built in large numbers for electric power generation, they got larger. By the early 1970s, turbine unit sizes approached 100 megawatts, up from 20 to 30 megawatts 10 years earlier. This also increased thermal efficiency due to geometric scaling effects.
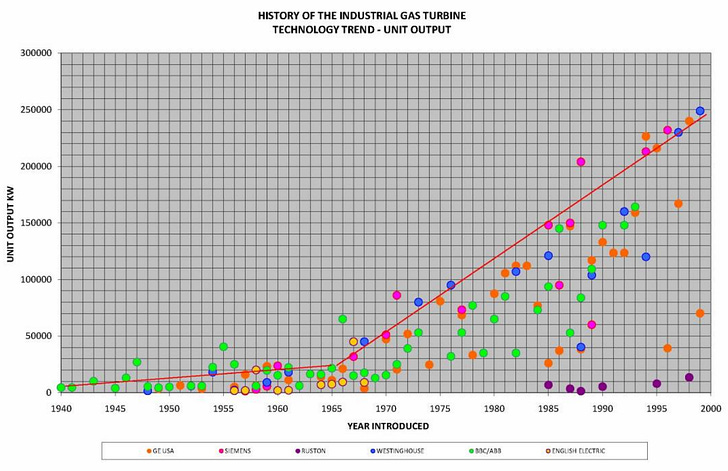
Turbine operating temperatures also continued to increase, thanks to the development of things like air-cooled turbine blades, another technology developed for jet engines that was then adopted by industrial turbines.
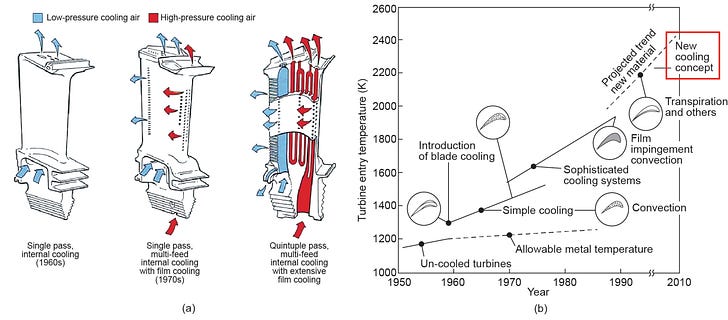
Gas turbine thermal efficiencies came closer and closer to steam turbine efficiencies, which had stopped improving in the late 1960s, and the capital cost of gas turbine plants continued to fall. Efficiencies could be pushed even further by recapturing the exhaust heat from the turbine in a combined cycle plant. By the early 1970s combined cycle plants were more efficient than steam turbines alone, and major turbine manufacturers like GE, Westinghouse, and Alstrom were all developing their own combined cycle technology that replaced boilers with heat recovery steam generators.

But the Oil Embargo of 1973 caused natural gas prices to skyrocket, and the 1978 Fuel Use Act prevented the construction of new natural gas power plants. As if this weren’t enough, the rapid scale-up of gas turbines and the addition of complex heat recovery equipment caused reliability issues, giving gas turbines a reputation for being high maintenance. In the late 1970s, the bottom fell out of the utility gas turbine industry. Between 1975 and 1985 no net gas turbine generation capacity was added in the US. The market became so dire that some manufacturers considered exiting the business.

But gas turbine technology continued to advance, mostly thanks to the aerospace industry. The military continued its interest in pushing the bounds of jet engine performance, and the rising cost of aviation fuel incentivized developing more efficient jet engines. Single crystal turbine blades, which eliminated grain boundaries in turbine blade metal and allowed for even higher turbine temperatures, first appeared in military aircraft in the 1970s, and by the 1990s had made their way into industrial gas turbines. Thermal barrier coatings were developed, insulating the turbine blades using a thin layer of ceramic. Blade cooling was improved with film cooling, which created a thin film of protective cooling air over the turbine blades. The operating temperature of turbines continued to rise.

The gas turbine turnaround
By the late 1980s, the tide was turning for the gas turbine. Environmental laws that regulated the emissions of coal power plants greatly increased the cost of coal-generated electricity, and public opposition made it difficult to build new hydroelectric power plants. Nuclear power, which had held so much promise in the 1960s, had steadily increased in cost, and also faced significant public opposition following the accidents at 3 Mile Island and Chernobyl. Renewables such as wind and solar were gaining in popularity, but without government subsidies they remained far more expensive than existing sources of energy. The time was ripe for an alternative method of electricity generation.
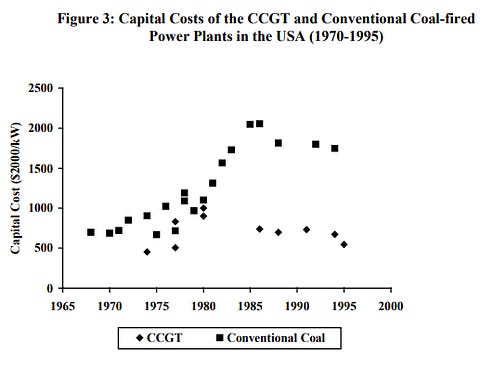
The gas turbine was well-positioned to fill the gap that had emerged. Natural gas prices had fallen nearly 40% from their peak in the early 1980s, and the Fuel Use Act that prevented gas turbine plant construction was repealed in 1987. The Public Utility Regulatory Policies Act (PURPA), passed in 1978 as part of the National Energy Act, forced utility companies to buy power from anyone who built a plant and connected it to the grid (for certain types of power plant). One of the technologies allowed by PURPA was cogeneration, plants that produced both electric power and heat. Combined cycle gas turbines qualified, and they were quickly adopted by independent power producers. Because gas turbines had relatively low capital costs and could be built quickly, they had low financing costs, making them attractive to private builders. By 1992, gas turbines were generating 44% of the electricity provided by non-utility companies in the US.
Independent power producers were a small fraction of overall electricity production in the early 1990s, but PURPA was followed by wide-scale electricity deregulation in the late 1990s and early 2000s. Suddenly, anyone could build a power plant of any size and fuel, and connect it to the grid.
The result was an explosion in gas turbine construction. Between 1986 and 2001, the number of simple gas turbine plants in the US increased 3x, and the number of combined cycle plants increased 10x. Gas turbine plants became so dominant that “virtually no other type of power plant was built” (Blanchard 2021). This sudden spike proved to be a temporary bubble, but combined cycle plants continued to be popular after it popped. In 1989, natural gas provided less than 10% of US electricity. Today, it's nearly 40%.
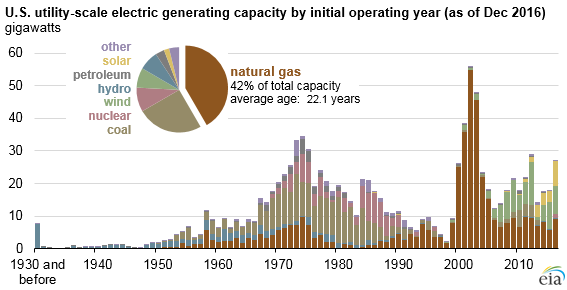
As the combined cycle gas turbine became widely adopted, its efficiency improved. Operating temperatures, pressure ratios, and unit size all continued to increase. Air cooling of turbine blades was replaced by steam cooling, where steam from the steam-turbine cycle is used to cool the turbine blades and guide vanes. In the early 1980s, gas turbine “technology factors” (the ratio of actual gas turbine performance to ideal Brayton cycle performance) were slightly above 60%. By 2000, it was approaching 80%, and simple cycle gas turbines (ie: non-combined cycle) had finally passed steam turbines in efficiency.
As more experience was gained building combined cycle plants, capital costs continued to fall. During the 1990s combined cycle gas turbines had a learning rate – the amount that costs fall for every cumulative doubling of installed capacity – of roughly 25%, higher than the learning rate of solar photovoltaics (though this hasn’t been sustained).
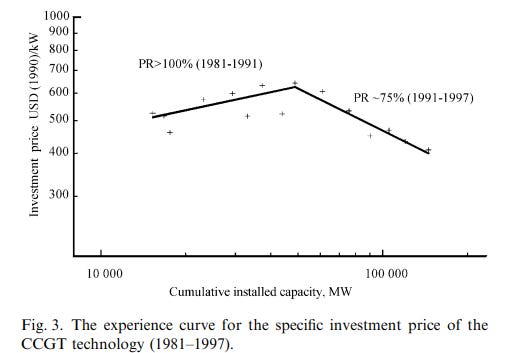
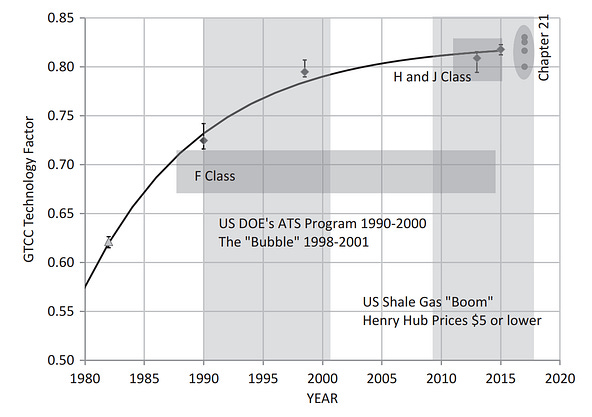

Thanks to continued advances in turbine technology, a utility gas turbine can operate at a turbine temperature of nearly 2000 degrees Kelvin, and a pressure ratio of more than 20, with compressor and turbine mechanical efficiencies exceeding 90%. A simple gas turbine can have a thermal efficiency above 40%, with a combined cycle plant having a thermal efficiency of 60%.
Lessons from the gas turbine
It's worth comparing the development of gas turbines for electricity generation to another important energy technology, solar PV. In both cases, the basic technology first appeared in the late 19th/early 20th century and first became practical in the mid-20th century. Armengaud and Lemale built their turbine in 1903, but it wasn’t until the 1930s that turbines were built that could do appreciable amounts of work. Likewise, the first solar PV cell was built in 1881 by Charles Fritts, but it wasn’t until the silicon PV cell was invented in the 1950s that solar PV became more than a curiosity.
Both technologies were initially expensive compared to other methods of electricity generation, but had other benefits that made them useful in certain niches. Because solar PV could provide electricity without fuel, it proved to be an ideal way to power satellites. For gas turbines, their combination of small size, low capital cost, quick startup time, high power to weight ratio, and ability to blow large volumes of heated air made them useful for certain industrial tasks, as well as for transportation (jet aircraft, marine engines, locomotives). In each case, these initial use cases enabled the technology to continuously improve via small, incremental improvements over many decades, gradually getting cheaper until it was competitive with utility-scale electricity generation.
(This is schematically similar to Clay Christensen's theory of disruptive innovation, in the sense that both technologies started out worse than some existing solution but excelled for certain use cases, which enabled them to develop until they were superior to the existing solution. One major difference with gas turbines is that many of the players that developed them, such as GE, Brown Boveri, Westinghouse, and Mitsubishi, also had, and have, successful steam turbine businesses. So gas turbines aren’t a case of an incumbent being disrupted by some new player that uses different technology.)
With solar PV, the technology was pushed forward by a long series of government subsidies and other funding programs: military funding for satellite solar PV in the 1950s, DOE funding for cost-per-watt reductions in the 1970s, Japan's rooftop program, Germany's feed-in tariff, renewable portfolio standards and tax credits, and so on. This funded the continuing development of the technology over the decades it took to achieve cost parity with other methods of electricity generation (One way of looking at the enormous cost declines of solar PV is how incredibly terrible it was for most of its life as a method of electricity generation.)
Gas turbines had many fewer direct subsidies. The major US one was the Advanced Turbine Systems program, a DOE program to fund the development of gas turbine technologies, which can be credited for things like closed loop steam cooling and the adoption of single crystal turbine blades. But it’s unclear whether this program simply substituted for industry research and development that would have taken place anyway. In fact, some of the most important developments for gas turbines, such as repealing the fuel use act and electricity deregulation, were about the government stepping back and letting the market take a greater role.
However, gas turbines saw an enormous amount of indirect subsidies, in the form of government funding for jet engine development. Ever since Frank Whittle developed the first jet engine in the 1930s, jet engine development has extensively relied on military and other government funding. The military funded many early jet engine development projects, as well as research into things like improved turbine blade materials. Technology developed for aircraft and jet engines, such as airfoil-shaped turbine blades, superalloys, special ceramic coatings, and single crystal turbine blades, has eventually made its way into industrial gas turbines. Jet engine development has proved so crucial to the advancement of industrial gas turbines that the gas turbine companies that don't have a jet engine business (and many, like GE and Mitsubishi, do) have partnered with jet engine developers to keep their products competitive.
We in fact see something similar with solar PV, where it was able to piggyback on improvements in semiconductor technology for most of its early existence.
This then points to a fundamental challenge of technology development. Technology improves in incremental steps over many decades (or centuries). There needs to be some way to fund that development over that period of time. In many cases, the market can address this, but if the technology is competing with an existing, superior solution, this is more challenging, even if the long-term prospects of the technology are brighter.
Thanks to Austin Vernon, Nick McCleery, Ben Reinhardt and homerificus for reading drafts of this. All errors are my own.
By comparison, France’s much-vaunted nuclear power construction spree accounted for roughly 60 gigawatts of capacity between 1975 and 1990, and China built about 400 gigawatts of solar PV capacity between 2007 and 2022, though today China is building about 100 gigawatts of solar a year.
This is why Rankine cycle turbines today exhaust into a vacuum to allow very low temperature condensation of steam.
Though in the Brayton cycle, the heat addition/removal takes place at constant pressure, where they don’t in the Carnot cycle.
This is due to how compressible the two fluids are. Liquid water is relatively incompressible, whereas a gas can be compressed. Because the gas will undergo significant volume change, this requires more work.
More specifically, thermal efficiency is a function of the pressure ratio and the specific heat ratio, if we simplify and assume that specific heat doesn’t change with temperature.
Velox boilers originally used Holzwarth-type explosion turbines, but were later replaced with more “conventional” gas turbines. Early on the compressors required more energy than the turbine could supply, but as turbine designs improved they became net energy producing. See Seippel 1953.
Japan also got its first gas-turbine based powerplant in 1949.
That was a marvellously lucid explanation of the history of the gas turbine, pitched just right for the interested lay-person. Thank you!
Brian: you, Ed Conway with "Material World", and the Works In Progress crew (and perhaps Bent Flyvbjerg too,) between you all, seem to be recapitulating and expanding on the work of Vaclav Smil, in a far more readable way. I have a copy of his "Energy in Nature and Society", and between the typos and the lack of firm editing for readability, it's a bit of a slog.
Don't take that as belittling what you are doing: it's vitally important to clearly explain the facts of life and how we got to where we are today. Smil has done that for a few academically-oriented people; you all are doing it for everyone else. Thanks again.
Excellent article and as another commenter noted, perfectly pitched for the knowledgeable layman.
In 1982 as Engineering Manager of Alcon's Puerto Rico plant I negotiated and signed the contract with O'Brian Energy. O'brien was to build, own and operate a cogeneration plant on our site to. Provide electricity and chilled water.
This led to a kerfuffle with the PR Power Authority trying to block it.
That eventually led to FERC ruling in favor of alcon/o'brien and mandating utilities nationwide to permit 3rd party owned cogeneration
You are welcome.